일 | 월 | 화 | 수 | 목 | 금 | 토 |
---|---|---|---|---|---|---|
1 | 2 | 3 | 4 | |||
5 | 6 | 7 | 8 | 9 | 10 | 11 |
12 | 13 | 14 | 15 | 16 | 17 | 18 |
19 | 20 | 21 | 22 | 23 | 24 | 25 |
26 | 27 | 28 | 29 | 30 | 31 |
- 회전 최소/최대
- 회전수 파라미터
- 틸팅인덱스
- 선형배열
- CHAIN OPTION
- 윤곽가공 탭
- 진입/복귀
- 2D가공경로
- i/o채널
- 윤곽가공경로
- 머신 시뮬레이션
- 절삭파라미터
- 체인 옵션
- 윤곽가공
- 최소 회전수
- 곡면 고속가공경로
- 포스트수정
- 마스터캠
- 정도레벨
- 5축 시뮬
- 스핀들 파라미터
- 체인옵션
- Weterline
- 평면관리자
- 대기툴
- 윤곽가공 파라미터
- 부가축가공
- 마스터캠 모의가공
- 머시닝
- 멀티포스트
- Today
- Total
언젠가 반드시 모모가
스레드 밀 (THREAD MILL : 미터식) 설정법 (웹버전) 본문
스레드밀(THREAD:나사) 사용법을 알아봅니다.
먼저 사용 공구 들을 알아봅니다.
① M6 멀티 타입(1나사산) : 소구경 (M1~M6 :피치 1.0mm 이하) 비철 위주
② M8 멀티 타입(2 나사산) : 중구경 (M1 ~ M12 : 피치 2.0mm 이하) 다용도로 사용 난삭재 가능
③ M8 드릴 타입(다중나사) : 중~대구경 (M1.4 ~ M14 : 피치 2.0mm 이하) 비철 위주 , 면취 겸용
④ 범용 나사산 바이트 사용 (나사산 인서트 타입) 대구경 나사 홀 가공시 다용도 난삭재 가능
* 공구 형태 나 규격 들 은 임의로 보시고 작업시 해당 공구 규격을 준수 하십시오.
공구 규격
1. 소구경 M6 스레드밀 사용법
① 나사밀 공구 설정
각 해당 하는 나사밀 사용 공구 을 실제 공구(예시로는 툴렉스:toolrex)에 맞게 설정하셔야 합니다.
1. 나사밀 공구 사용
① 나사밀가공에서 새 공구 생성을 클릭 합니다.
② 공구 생성에서 나사밀나사밀을 선택 합니다.
③ 나사밀 정의 을 입력 합니다.
ⓐ 미터나사 이므로 Metric Metric로 정의합니다..
ⓑ 해당 나사 피치 입력 (M6 이므로 피치 1.0(P))
ⓒ 나사밀 칼 날 외경입니다. (나사 기초홀 규격 규격보다 작아야 진입 이 가능합니다.).)
여기서 는 4.0mm (D1) 중요!!
ⓓ 전체 길이 공구 의 전장 길이입니다..
(60.0mm (L))
ⓔ 절삭 길이는 절삭 날 높이 (피치)을 입력하셔야 합니다.
(주의 사항으로 피치와 동일하게 입력하셔야 합니다.)
ⓕ 홀더 길이 공구 날목 부분 길이 (?) 공구 유효장유효장으로서 가공 가능 한 깊이 (나사 홀 깊이)라고생각하시면 됩니다.
(모의 가공시 적용)
ⓖ 위 공구 날목 부분 직경으로 입력하시면 됩니다.
(잘 모르시면 ⓒ 직경에서 피치 을 빼고 좀 더 작게 입력하시면 됩니다.) (모의 가공시 적용)
ⓗ 나사밀 공구 샹크 부분 직경입니다. (D)
ⓘ 나사밀 공구 발목 부분 과 샹크 부분 연결 각도입니다. (15°~30°) (모의 가공시 적용)
* 모의 가공 적용 항목 은 실제 가공 시 가공 파라미터파라미터에 영향 주지 않고 모의 가공 이 적용됩니다.
2. 사용자 정의 공구 사용
① 먼저 생성할 공구 을 별도 의 레벨에 공구 단면을 생성 합니다. (레벨:11)
주의 사항
1. 해당 레벨 에는 공구 단면만 있어야 합니다.
2. 공구 단면 은 원점 기준 우측 상단에 위치하여야 합니다.
(공구 끝단 이 원점에 위치)
3. 공구의 단면 선 (중심축) 은 그리지 않고 공구 단면은 이어져 있는 한개 의 라인으로 이루워져야 합니다.
공구 단면 이외에 다른 객체는 있으면 안 됩니다..
(치수, 표기, 기호 등 불가)
4. 선의 굵기,, 색상 은 무방 합니다. (문자 불가)
② 나사밀가공에서 새 공구 생성을 클릭 합니다.
③ 공구 생성에서사용자 공구 을 선택 합니다.
④ 사용자 공구 정의 중 을 “레벨에서 가져오기 및 사용자 저의 형상에 링크“ 항목을 클릭 합니다.
⑤ 선택 레벨에서 처음 정의 한 공구 레벨 “11”을 클릭해 줍니다.
⑥ 사용자 공구 정의 을 입력 합니다.
ⓐ 절삭 지름 나사밀 날 직경을 입력 합니다. (중요)
ⓑ 절삭 길이 나사밀 피치 을 입력 해주세요. (중요)
나머지 부분 은 적당히 입력해주셔도 됩니다.
(공구 단면 형태 규격 이 우선시됩니다.).)
3. 나사밀 캠 작업
① 밀링 가공경로 – 원호 가공경로 – 나사밀나사밀을 선택 합니다.
ⓐ 드릴 점 선택 하기 (여기 에는 3가지 방법 이 있습니다. 사실 다 같은 것이지만))
1. 가공 홀 중심 점 그리기로 생성된 점 선택 ( 점 선택)
2. 탭 기초 홀 구경 선택 (5.1Ø)
3. 탭 규격 홀 구경 선택 (6.0Ø) * 도형요소로 선택
② 나사밀가공에서 해당 공구 을 선택 하고 절삭 파라미터 을 선택 합니다.
ⓐ 나사 공구 이의 수 : 공구의 날 수 을 의미하며 여기서 는 11 날 이므로 “1” “1”을 입력합니다..
ⓑ 나사 피치 : 해당 나사 피치 을 입력 합니다.
여기서 는 M6 : “1.0”을 입력합니다..
ⓒ 나사 시작 각도 : 홀 에 진입하는 공구의 진입 하는 방향을 각도로 지시 하는 것입니다..
* 적용 은 CW 기준 90° 방향 이 “0”이고반시계 방향 으로 돌아갑니다.
(다줄 나사 가공시 필히 확인하고 작업하세요.)
ⓓ 허용치(오버컷) : 나사밀 공구 가공 값(?) 또는 피치 값이라고 도 할 수 있는 수치입니다..
예시 을 들면 나사밀 체인 시.
1. 중심점 점체인 경우
이경우 가공 홀 직경을 지정 하지 않았으므로 중간의 나사 지름 (M6 = 6.0) 입력하면 해당 공구 을 6.0Ø 을 기준으로 윤곽 가공 도는 것처럼 이송 합니다.
그럼 여기서는 허용치(오버컷) 은 가공 여유처럼 작동 합니다.
* 그러므로 중심점 기준 체인 작업 하셨으면 허용치는“0” 으로 두고 나사지름을 해당 규격 대로 입력 하시면 됩니다.
2. 나사 드릴 기초홀 체인 경우
여기서는 M6 이므로 기초홀 이 5.1 Ø입니다.이것을 기준으로 체인을 걸으셨으면 6.0 Ø-5.1 Ø=0.9mm 0.9를 허용치에 입력하시면 됩니다. (0.9/2=0.45가 아닙니다.)
그러면 진입 후 M6=6.0 홀 에 따라 공구가 이송됩니다..
* 이때 점체인 과 다르게 중간의 나사 지름을 입력 할 필요 가 없습니다. (비활성화)
3. 나사 홀 체인 경우
6.0 Ø0.0 이 됩니다.
* 이때 점체인 과 다르게 중간의 나사 지름을 입력 할 필요 가 없습니다. (비활성화)
ⓔ 경사 각도 : 나사산의 경사 각도 을 지정 하는 칸입니다..
여기서는 미터식 일반 나사 산이라 각도는 “0” “0”을 입력하셔야 합니다.
ⓕ 콘트롤러컨트롤러로 공구 보정 : 다른 윤곽 가공 의 공구 보정과 동일 합니다.
보통 컴퓨터로 놓고 (공차 조절 : 허용치 값) 쓰거나 중복 보정으로(머시닝 보정 값) 하여 초품 가공 후 실 가공 을 하십니다.
공차 시 중복보정 사용 권합니다.
* 진입/복귀에서 다시 애기 드리지만 중복 보정 시 진입시 경로중 직선 구간 이 필요합니다..
(이것은 수기로 (G41,42 사용)작성해보신 분은 이해 가실 것입니다.
보정 이 들어가는 데 진입 초기에 경로 중 직선 구간 이 있어야 보정 이 가능합니다.)(중요)
ⓖ 현재 가공하려는할려는 나사 가 외경(숫) 나사 인가 내경(암) 나사 인가 지정 합니다.
ⓗ 나사 진행 방향 이 오른손 나사,, 왼손 나사 을 지정 합니다.
ⓘ 나사밀 가공 방향 이 하부에서 상부로 진행하는 것(하향절삭) 인지 상부에서 하부로 진행 하는 것 (상향절삭)을 지정합니다..
보통 하부에서 상부로 가공 하는 것을 권하나 막힌 홀 경우 칩 배출 문제 을 고려 하셔야 합니다.
관통 홀 경우는 하부에서 상부로 가는 것 을 권합니다.
ⓙ 경우에 따라 원호코드 IJK 가 적용 되지 못하는 기종 경우 점 테이터 형태로 NC코드 출력 시 적용합니다.
③ 나사밀 절삭 파라미터 – 리드인/아웃에서 공구 진입 복귀 을 설정 합니다.
ⓐ 진입/복귀 원호 Z 높이
윤곽 가공에서 공구 이송 높이 와 같은 의미입니다.
ⓑ 진입/복귀 직선 길이
진입/복귀 시 법선 형태 설정 ⓓ 을 체크 시 적용되는 길이입니다..
목적 은 공구 보정(중복보정) 시 보정 값이 적용되도록 살짝 (0.1~0.2) 직선 경로 가 형성 됩니다.
ⓒ 원호 중심점 위치에서 시작
나사밀 가공 시작 시 원호 중심에서 가공 시작 합니다. (중요!!)
* 만일 법선 형태 진입 체크 시 법선 진입 가능 한 위치에서 진입 하여 나사밀 가공 시작 시 홀 중심 점으로 이동 후 나사밀 가공 시작 합니다.
(이 경우 주의 사항 이 원호 중심점에서 시작 체크 하고 법선 형태 진입을 같이 체크하면 공구 가 법선 형태 진입 이 가능 한 위치(진입/복귀 법선 길이 지정 한 만큼)에서) 진입 후 가공 이 시작됩니다.) (주의 필요!!)
ⓓ 법선형태 진입/복귀
위에서 설명 한 대로 법선 진입 (직선 경로) 적용 여부 지정입니다..
ⓔ 상단 / 하단 으로 헬리컬 진입/복귀 적용
가공 경로 의 처음과 끝 (상단/하단) 이 피치에 의한 헬리컬 (나사산 모양) 대로 진입/복귀하냐 아니면 진입/복귀 시 마치 일반 2d 윤곽 가공 처리 Z값 변동 없이 (평면 이송) 하는 것 을 말합니다.
* 보통 둘 다 체크해주셔야 합니다. (잘못되면 실물 나사 조립 시 진입 이 안됩니다.)
④ 절삭 파라미터 – 측면 가공
이 항목 은 황삭 가공 옵션으로 보시면 되고 보통의 경우 비철 계열 은 11회로 가공 (피치 1.0 이하) 하고 피치 가 크거나 철 계열 소재는2회 정도 가공 합니다.
옆의 옵션 처럼 하면 0.45(0.9) 가공 에서 0.1을 남기고 1회 가공하고 이후 0.1 0.1을 마저 1회 가공 총 2회 가공 을 합니다.
⑤ 링크 파라미터
나사밀의.
주의 사항으로 진입/복귀 헬리컬 적용시 막힌 홀 은 저 깊이만큼 나사산 이 생성되지 않습니다.
(불완전 나사산 같은)
그러므로 일반 탭 가공처럼 약간 의 가공 깊이 연장 이 필요합니다..
모의 가공 결과
주의 사항으로 위 모의 가공 결과 도 보이지만 막힌 홀 경우 하부에 불완전 나사 부분 이 존재합니다..
옆 그림과 같이 링크 파라미터 가공 깊이(화살표)까지 내리더라도 리드인/아웃에서 하단으로헬리컬 진입/복귀 설정 체크로 살짝 피치 높이만큼헬리컬 이송 후 실 가공 이 들어가므로 만일 정확한 탭 깊이 을 원하시면 피치만큼 더 가공 깊이 을 내리시고 (정확히는 나사밀 날끝 바닥 면 이 있으므로 그만큼 (피치/2) 만큼 깊이 가 필요 하므로 드릴 기초홀 가공 시 고려하셔야 하며 만일 막힌 홀 평바닥에나사밀 작업시좀 더 계산 이 필요합니다..
(해당 공구 규규격에 적합하게))
2. 외경(숫) 나사 가공 법
① 외경 나사산 경우 내경 나사산 의 반대로 하신다고 생각하시면 간단합니다..
다만 나사 홀 중심점 체인(?) 은 적용 안되고 나사산 내경 골 구경 (M6 은 5.0(4.9)) 을 체인 걸으시면 됩니다.
② 원호 가공 경로 – 나사밀나사밀을 선택 한후 도형 요소 을 선택 후 해당 나사 내경을 선택 합니다.
* 내경 나사밀나사밀과 같은 내용은 생략하겠습니다..
③ 나사밀 공구 설정 후 절삭 파라미터 을 클릭 합니다.
ⓐ 외경 나사 을 선택 합니다.
* 외경 나사 을 선택 하면 나사 지름 항목 이 불활성화됩니다..
ⓑ 가공 방향을 위에서 아래로 선택 합니다.
* 외경 나사 가공 경우 내경나사와 반대로 위에서 아래 가 하향 가공 이 됩니다.
④ 그 외 파라미터 을 설정 하시면 다음과 같이 가공 경로 가 생성 됩니다.
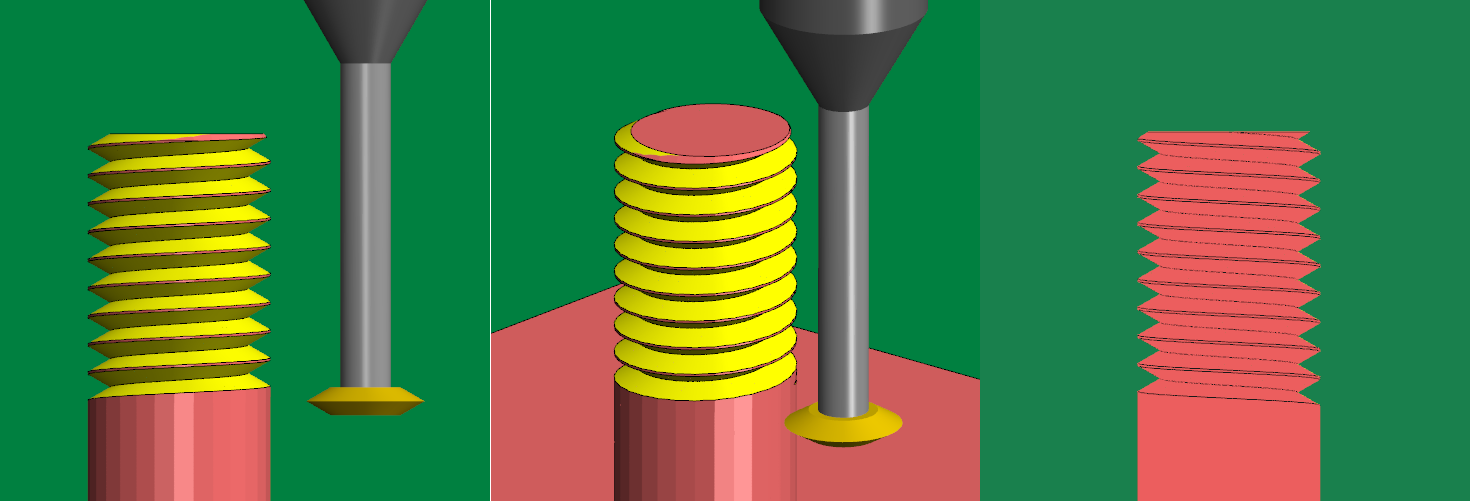
원칙 적으로는M6 피치 1.0 나사산 골 직경 = 5.0 이므로 5.0Ø 원호 기준 이 되어야 하는데 이론적으로 생각하면 1대 1규격 가공 이되므로 만일 공차 가 중요하지 않으면 외경 나사 경우 좀 더 작은 내경 나사 골 (M6 = 4.9)을 기준 하여 작업하시는 것 을 권합니다.
사실 실제 가공 여러 번 해보고 데이터 정리 해보시면 어느 정도 가공 여유 값이 나온다고 생각합니다.
2. 나사산 2 나사밀 공구 사용.
나사산 이 여러 개 있는 공구 사용 시 고려 사항 은 크게 없습니다.
다만 여러 개 의 나사산 이 동시에 가공 이 진행되므로 가공 부하 문제로황삭사용을 고려 하셔야 합니다.
또는 절삭 피드조절을 통한 적절한 절삭 조건을 설정 하십시오.
① 나사산 2 나사밀 공구 사용
나사밀 절삭 파라미터파라미터에서 나사산 수 만 해당 수만큼 입력하시면 됩니다. (예시는 2개)
우선 나사밀 공구 설정 을 합니다.
ⓐ 피치 : 해당 공구 피치 을 입력 합니다. (M8=1.25)
ⓑ 외부직경 : 나사밀 날 직경을 입력 해주세요.
ⓒ 절삭 길이 : 피치 x 날수 (1.25 x 2 = 2.5)을 입력합니다..
나머지 사양 은 해당 공구에 맞게 설정해줍니다.
만일 해당 공구 형태 을 잘 아시면 단면 작성 하여 사용자 공구로 사용 하셔도 됩니다.
② 나사밀나사밀의 절삭 파라미터 을 클릭 합니다.
ⓐ 나사 공구 이의 수 : 해당 나사밀 공구 의 나사산 수 을 입력 합니다.
(예시는 2개)
ⓑ 나사 피치 : 해당 나사밀 공구 의 나사 피치 을 입력 합니다.
(예시는 M8=1.25)
③ 나머지 파라미터파라미터는 앞과 동일 하게 진행합니다..
그럼 생성된툴패스 을 살펴보겠습니다..
뭔가 툴 패스 가 나사산 11개와 많이 틀려 보입니다.
이 상태에서 모의 가공을 실행 합니다.
모의 가공 되는 것 을 보면 한 싸이클사이클에 나사산 수량만큼(피치 X 나사산 수량) 가공하고 다시 복귀(제자리에서)후 나사산 수량만큼 올라가서 다시 가공하고 단계 별로 올라갑니다..
이번에는 외경 나사 을 적용해 보았습니다.
이와 같이 외경나사 도 나사산 수만큼 단계별로 가공하며 진행합니다..
특이점 은 마치 윤곽 과정 의 공구 유지 을 체크 안하는것처럼 공구 가 나사산 수량만큼 가공하고 안전 높이 까지 복귀 후 다시 내려가서 가공합니다. (안전 높이 체크 여부와 관계없이..)
이점 유의 하시어 작업하십시오.
*이 때문 인지 이런 나사산 22개짜리 공구 도 그냥 나사산 11개로 공구 설정 하여 작업하시는 분들 도계십니다.
(이 공구 복귀 때문 인지 모르겠지만…)
*또 이러한 나사산 두, 세 개짜리 공구 중 나사산 날 이 황삭,정삭 구분 하는 것 이 있습니다.
이러한 경우 나사산 1개로 작업하여 두개두 개의 나사산 이 전부 (정삭 나사산 이 다 가공 이송되도록) 가공) 깊이 을 조절 하셔야 합니다.
3. 나사산 다수 의 나사밀 공구 사용 (헬리컬 or 드릴 타입)
드릴 타입 의 나사밀 공구 같은 경우 저도 본적 이 없고 그 가공 방법에 대한 자료 도 없어 해당 캠 상 에서 할 수 있는 방법을 찾아서 하는 것이라 실제 가공과 차이 가 있을 수 있습니다.
단지 이러한 경우 어떻게 하나에 대하여 조금 이나마 도움 이 되지 않는가 하여 설명하겠습니다..
* 공구의 특이 사항을 예시 하기 위하여 가공 자체 을 드릴 타입 (한 개 공구로드릴링,탭 가공 을 하는 것으로 설정하였습니다.).)
① 관통 홀 나사밀 가공 방법
우선 공구 설정 을 합니다.
해당 공구 단면을 작성 하신 후 사용자 공구로 지정 하여 작성하시면 되는데 주의 사항 은 나사밀 가공 이 핵심 이므로 공구 절삭 지름을 해당 나사산 날 직경을 입력 하셔야 합니다.
* 날끝 부분 은 당연히 6.8 Ø(드릴 기초홀) 입니다.
② 맨 처음 드릴 작업을 작성 해 줍니다.
일반 드릴 가공과 같이 생각하여 작업해 주시면 됩니다.
다만 드릴 가공 후 면취작업을 병행 하여 가공할 예정 이므로 가공 깊이 을 면취 구간 까지 내려 오서야 합니다.
* 단 가공 소재 두께,, 공구 절삭 가능 길이,, 면취부 규격 등 을 고려 하셔야 합니다.
(특히 막힌 홀 경우 필수)
* 우선 예시는 두께 10.0mm 소재에 관통하는 것으로 설정하였습니다..
공구 규격을 보면.
그림과 같이 상부 면취 부 끝 점까지 높이 가 14.95mm 이므로 8 Ø 0.2C = 4.2 + 14.95 = 19.15mm까지 공구 을 내립니다.
③ 드릴 싸이 클 이 끝나면 통상드릴 가공과 같이 R점 복귀합니다..
(칩 배출 문제로 R점 복귀 을 추천 합니다. 만일 복귀하지 않고 드릴 가공 후 바로 나사밀 가공 을 원하시면 드릴 사이클을커스텀 하시거나 수기로G1 방식으로 내리시고 나사밀 가공 으로 들어기야 합니다. 나사밀 가공 나사 깊이 치수 을 참조하여 작성하셔야 합니다.)
그럼 나사밀가공을 클릭 합니다.
ⓐ 해당 공구 의 나사산 수량을 입력 합니다.
* 이때 해당 공구는 가공 하고자 하는 규격(진입부 나사산 + 소재 두께 + 상부 여유 나사산 : 1.25 + 10.0 + 1.25 = 12.5 이상) 이 되어야 합니다.
이 경우 나사산 가공 길이 가 15.5mm 15.5mm이라 무방 합니다.
또한 드릴 타입 나사밀 공구 경우에 해당합니다..
(원스텝으로)
ⓑ 해당 공구 나사 피치 을 입력 합니다.
ⓒ 콘트롤러로 공구 보정
이것은 컴퓨터 또는 중복 보정 중 선택하시면 됩니다.
ⓓ 가공 방향 – 아래에서 위로
드릴 타입 특성상 공구 을 아래로 (드릴 날 부분을 통과 하여야 하므로) 내려서 가공합니다.
④ 리드인 / 아웃
ⓐ 원호중심점 위치에서 시작
공구 가 계속 가공 나사 홀 내에 있으므로 급속 이송 시 홀 중심에 위치하도록 합니다. (중요!!)
ⓑ 법선 형태 진입/복귀
중복보정을 위하여 약간 의 법선 형태 진입 길이 을 입력 해주십시오.
* 화면상 에서는 비활성 되어 있는데 이경우 해당 캠 이 자동 계산 합니다.
(가공 경로 필히 확인 요!!) (만일 컴퓨터 조정 경우 의미 가 없습니다.)
ⓒ 상단/하단으로헬리컬 진입/복귀 적용
위 법선 형태 진입/복귀 경우와 반대로 항상 공구 이송 이 나사산 형태(헬리컬)로 이송하여야 하므로 체크해주셔야 합니다. (중요!!)
⑤ 측면 가공
가공하는 가공 깊이만큼 가공 부하 을 고려 하셔서 입력해 주시기 바랍니다.
⑥ 링크 파라미터
여기서 주의 사항 이 실제 나사 가공 되는 것 은 공구드릴 날 (1.8mm) 부분 이 나사 피치 규격보다 많게 (피치 1.25 이므로 여기서는 1.5) 소재 두께 10.0 + 드릴날 1.8 + 피치 1.25 = 13.05인데 여유 잡아 가공 깊이 14.0 ⓐ으로 설정합니다..
그럼 나사 깊이 (소재 상단) 은 14.0 - (1.25*2) = 11.5로 입력 합니다.
(실제 1회전 시 1.25 피차 가 되나 확실한 가공을 위하여 2회전 실시합니다.) (주관적 의견)
소재 상단 가공 깊이 황삭 절삭 이송 홀 중심축가공 깊이 정삭 절삭 이송 홀 중심축소재 상단
도 착 Z -14.0 이송 Z -11.5 까 지 급속 이송 Z -14.0 이송 Z -11.5 까 지 급속 이송 급속 이송
위 와 같이 소재 을 관통 후(드릴 가공) 가공 깊이 Z -14.0 -14.0까지 내려 온후 Z -11.5까지헬리컬 나사밀나사밀가공을 진행 하며 정삭 가공 완료 후 홀 중심축 에서 상단으로 급속 이송 합니다.
⑦ 모의 가공 결과
해당 파라미터 을 고려 하여 모의 가공을 실시 하였습니다.
드릴링 준비 / 기초홀 과정 / 가공 깊이 이송 / 황삭 나사밀 가공 / 홀중심 정렬 / 정삭 나사밀 가공 / R점 급속복귀 / 단면 상세
또한 밑 드릴날 부분 이 나사산을 건드리지 않는지 확인하셔야 합니다.
⑧ 드릴 타입 막힌 홀 가공 경우
막힌 홀 경우 해당 캠 생성 방법은 큰 차이 가 없습니다.
다만 나사밀 가공 시 헬리컬 절삭 이송 이 되면 하부드릴 날 부분 이 절삭되므로 이에 대한 고려 및 협의가 필요합니다..
간혹 일정 완전 나사 길이가 필요한 경우 고려할 수 도 있다고 하나 권장 하는 방법 은 아닙니다.
⑨ 이외 헬리컬 타입 은 별도 드릴 공구로 기초 홀 작업 후 나사밀작업만 하시면 됩니다.
4. 나사 인서트 사용 바이트 공구 사용
방법 은 앞과 동일 합니다.
나사산 1개 한줄 나사 방식으로 하시면 되고 다줄나사는 그 나사 날 수량만큼 입력하여 작업하시면 됩니다.
다만 이러한 인서트 방식 은 보통 피치 별로 구분하여 사용하며 내외경 나사 용 이 따로 있습니다.
선반용 바이트 사용 시 회전 방향 도 다른 것 이 있다는 것 을 감안 하여 준비하셔야 합니다.
다만 이러한 나사밀공구는 좀 더 큰 규격에 사용합니다..
나사 피치만 맞고 기초홀규격에 맞게 진입/복귀가 가능하면 큰 홀 도 가공 이 가능합니다..
다만 단순한 조립용 나사산 가공 이 아니시면 적절하게 가공하고자 하는 나사 규격에 맞게 선택하여 작업하시면 됩니다.
* 참고 로 제이제이툴스 스레드밀 자료 같은데 각 나사홀 의 내외경 나사산 골 직경,, 기초홀 직경 이 잘 나와 있으므로 참고 바랍니다.
'마스터캠 관련 한 여러 이야기 > 마스터캠 활용 가공 방법' 카테고리의 다른 글
3축 바이스 에서 소재 각치기 (웹버전) (1) | 2023.01.01 |
---|---|
머시닝 공구 길이 보정 및 소재 원점 Z값 입력(웹버전) (3) | 2022.12.28 |
거르기 기능(Filtering and Tolerances) 설명 (웹버전) (3) | 2022.12.26 |
마스터캠 면취(모따기) 챔퍼(CHAMFER) 에 관하여 (3D 가공)-7 (0) | 2022.09.02 |
마스터캠 면취(모따기) 챔퍼(CHAMFER) 에 관하여 (2.5D 가공)-6 (0) | 2022.08.27 |