이번에는 볼엔드밀로 경사면등 3D 가공 시 필히 생각하게 되는 절삭간격(?)에 대하여 설명해 보겠습니다.
우선 공구 절삭간격(피치 : Pitch) 간 무엇이냐 하면 공구 간 간격(가공경로 간 현재경로에서 다음경로 진행 시 서로 떨어져 있는 공구축과 공구축 의 간격입니다.
주로 3D가공(경사면이나 곡률이 있는 곡면등 : 등고선 또는 스컬릅 가공경로등...) 시 적용해야 할(값을 입력해야 할) 값입니다.
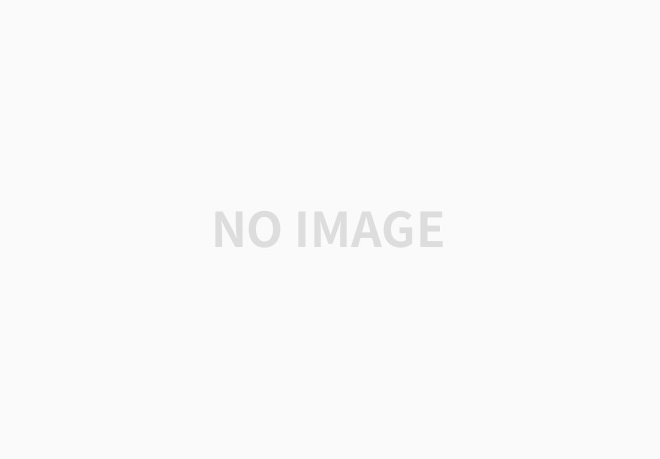
이것을 보통 거의 전설이나 감. 또는 전 작업자의 결괏값, 또 검색을 통한 추정 등으로 작업하는 경우가 대부분입니다.
그러나 문제가 가끔 이 제품은 조도가 좋아야 한다라던가 조도규제가 있다던가 또는 전에 10 Ø볼엔드밀 를 쓰다가 이번에 6 Ø볼엔드밀로 변경하여 사용해야 하는데 그전 값을 그대로 적용해도 되는 것인지... 볼엔드밀이 없어 볼노즈 엔드밀로 사용하여야 하는 그럼 어떻게 하나 여러 가지 걱정이 생깁니다.
그래서 어떠한 기준이 있어야 하겠다는 생각이 듭니다.
그 기준을 알아보고 그 적용 방법을 알아보겠습니다.
우선 커습(Cusp)이라는 것이 있습니다.
용어적 의미는 볼엔드밀 한정 일정가공면에 접하여 공구 가공면(경로) 간 거리차로 인하여 파도 모양의 미절삭 부분 발생형태를 커습(CUSP)라고 합니다.
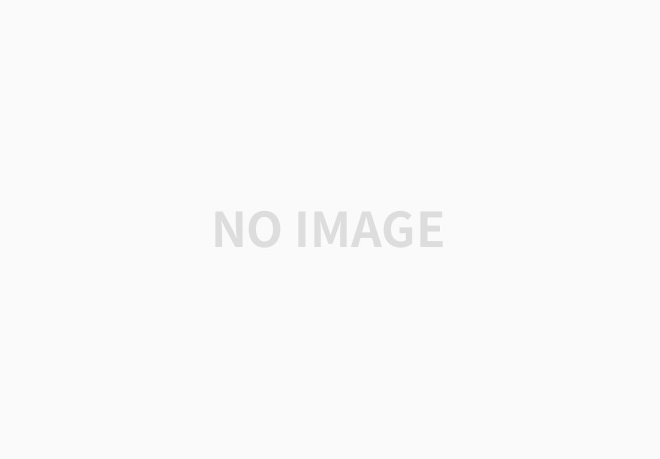
여기서 우리가 중요하게 볼 점은 저 커습 형태의 높이 (볼엔드밀 가공면 바닥에서 미절삭된 파도모양의 높이)입니다.
왜냐하면 그 커습 높이를 기준으로 하여 그 가공면의 조도(거칠기) 상정 기준이 됩니다.
이 커습값 구하는 공식은 아래와 같습니다.
커습량(mm)
P = 공구 간 간격 피치(Pitch)
R = 볼엔드밀 공구 R값
최대커습량(Hmax) = P² / 8R
* 그냥 상식적으로만 알고 계시면 됩니다.
여기서 한번 거칠기 기호에 대하여 잠깐 알아봅니다.
거칠기 기호는 다음과 같습니다.
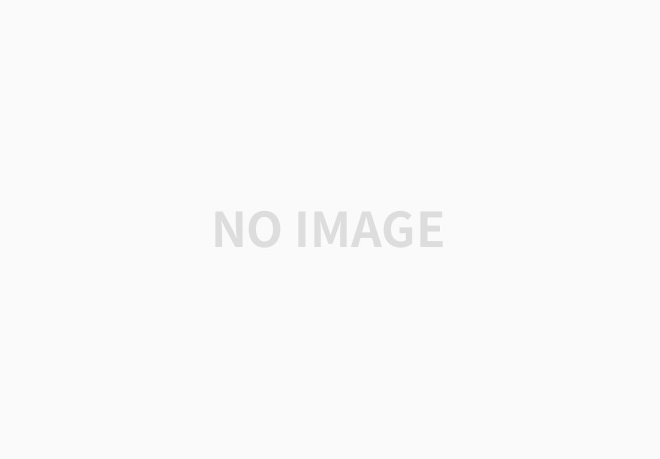
일단 이런 게 있다는 상식적으로만 보시면 되고 (나중에 참고할 일이 있으면 다시 자료를 찾아보면 됩니다.)
우선 이러한 거칠기 측정은 해당 가공면의 커습의 높이값의 평균, 최댓값 표시입니다.
이러한 커습값 측정기 중에서 제일 간단하면서 직관적인 것이 촉침식 측정기입니다.
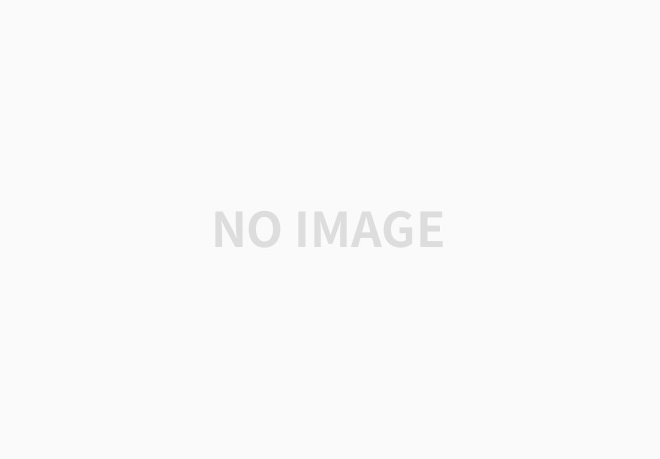
저렇게 가공면(측정할)에 초침을 접촉 후 뒤로 이동하면서 (마치 골짜기 따라 초침이 위아래로 움직이는) 거습량를 측정하여 표면 거칠기 값을 산출합니다.
단순히 얘기하면 표면 거칠기 값 단위는
Ra = 측정면 커습 높낮이 중간값 (단 기준은 가공면과 평행 유지)
Rmax = 측정면 커습량 최댓값
Rz = 측정면 커습값 10점 기준 평균값
우리가 여기서 중요시 볼 점은 Ra 값입니다.
이후 얘기 할 커습값은 여기 Ra 값을 기준하며 단위는 천분의 1mm입니다.
* 즉 위 Ra 값에 1/1000 = 0.8Ra 이면 0.0008mm입니다.
* 이것은 아래에서 다시 핵심 애기에서 다시 나오므로 기억은 해두세요... (중요!!)
이것을 좀 더 시각적으로 알아보기 좋게 얘기를 하면 표면 거칠기 시편(표준면)(Surface Roughness Scale) 이 있습니다.
여기 시편 사진을 보면 각 표면 거칠기 기호에 따른 표준 거칠기 샘플 표준면이 있습니다.





* 자료사진 찾기 어려워서 화질 상태가 불량합니다.
이러한 표준면를 참조하여 이러한 표면 거칠기는 거칠기 어느 값을 가진다는 것을 시각적 , 촉각적으로 확인할 수 있습니다.
*어떻게 얘기하면 예를 들어 작업지시가 표면 거칠기 (▽▽▽)(Ra 0.8a) 기준으로 작업하라고 하면 그 시편 표면을 만지며 작업자가 가공한 가공면과 비교(?) 하면서 작업하라는....... 설마 따라 하지는 않겠지요?)
자 다시 마스터캠으로 넘어가면
표면거칠기 단위(R)가 무엇이냐면 위에서 얘기 한 듯이 커습(CUSP)은 볼엔드밀로 가공하여 공구경로 간 미절삭된 부분의 높이를 얘기하는 것입니다.

그래서 어려운 공식은 넘어가고 작업 도면을 보니 이렇게 거칠기 표시가 되어 있습니다.

*전부 값은 동일한 거칠기 값입니다. (예제로)
해당 가공면은 10 Ø 볼엔드밀로 가공한다 할 경우 그럼 절삭간격은 얼마로 해야 저러한 거칠기 정도를 만족할만한 가공면이 나오는지 가 중요 포인트입니다.
그래서 우선 도면 표기 보면 (▽▽▽), (y값), (0.8a), (N6) 등으로 명기되어 있습니다.
그럼 우선 거칠기 값이 0.8a = 0.8㎛ = 0.0008mm이라고 볼 수 있습니다.
여기서 커습 계산기라는 프로그램을 동원합니다.
마캠뽀개기 네이버카페에서 구할 수 있는 커습 프로그램입니다.
사용법은 간단하게 말씀드리면
우선 작업자가 알고 싶은 것은 가공경로의 절삭간격이고 지정된 거칠기 값(Ra = 커습값 = 0.8 = 0.0008mm)을 알고 있습니다.
그럼 다음과 같이 값을 입력합니다.

① 해당 가공공구(볼엔드밀) 직경(D) 값을 넣습니다. (예제는 10.0)
② 해당 가공면의 각도(°) 값을 넣습니다.(평면의 경우는 0° 입력)(예제는 0°)
③ 해당 커습값(Ra : 단위가 마이크로미터(㎛) 이므로 표기된 값에서 천분의 일 를 하셔야 합니다. 0.8Ra = 0.0008 입력) (예제는 0.0008)
* 해당 값을 입력하면 자동적으로 피치값(절삭간격) 이 나옵니다.

예제에서는 절삭간격이 0.1789 가 나옵니다. 대략 0.17mm 정도 입력하시면 됩니다.
만일 반대로 이미 지정된 절삭 간격값이 있는데 그 커습값(가공 후 나올 거칠기 정도 값) 이 알고 싶으면 동일하게 ①②값을 입력하고 ④절삭간격을 입력하여 나온 값을 보면 현재 가공면의 거칠기값 정도를 알 수 있습니다.

그러면 현재 12 Ø 볼엔드밀로 평면 가공면을 절삭간격 0.2mm로 하면 거칠기 값 Ra0.8 이 니온다는것을 알 수 있습니다.
이러한 값을 왜 공구경이 큰 볼엔드밀을 적용하면 조도가(동일한 절삭간격 적용 시) 좋아진다는 것을 이해하실 수 있을 것입니다.
그런데 이러한 평평한 면은 이해되는데 곡률이 있는 가공면은 어떻게 하나요? 하는 의문이 있습니다.
먼저 등고선 값이 가공면의 곡률에 관계없이 Z값 간격에 따라 절삭간격(피치값) 이 변화하는 가공경로는 제외 합니다.

* 이러한 이유로 조도를 중요시할 경우 면방향 또는 스컬릅 가공경로 같이 절삭간격(피치값) 이 일정하게 유지가능한 가공경로를 사용하시는 것을 권유합니다.

위와 같이 일정한 절삭간격이 유지....(실제로는 살짝 변동이 있습니다.) 할 수 있는 경우 각 가공면의 곡률 을 정의 할수 없으므로 보통의 경우 모델링 형태에 따라 경사를 준 커습값을 주거나 모든 가공면이 평면이다라는 전제하에 (투영이동 반대로 생각..) 커습값을 적용하시면 됩니다.
'마스터캠 2021 기능 교육 자료(초안) > 마스터캠 2021 활용 소소한 팁' 카테고리의 다른 글
마스터캠 2021 활용한 소소한 팁-4-2 (각인 공정 관련 매크로 관련하여) (0) | 2023.08.09 |
---|---|
마스터캠 2021 활용한 소소한 팁-7 (NC 파일이름 변경 관련하여) (0) | 2023.07.29 |
마스터캠 2021 활용한 소소한 팁-5 (곡면 등고선가공중 필렛(?)부분 가공경로 생성(쉘로우 가공경로 추가)에 관하여) (1) | 2023.07.21 |
마스터캠 2021 활용한 소소한 팁-4 (각인 공정 관련 매크로 관련하여) (0) | 2023.07.15 |
마스터캠 2021 활용한 소소한 팁-3 (곡면가공중 평면부 가공경로 생성에 관하여) (6) | 2023.07.14 |