이번에 알아볼 것은 보링바 활용 법입니다..
주로 30ø 이상 홀 가공 시 기초 홀 가공 후 홀 확대 또는 홀 내면 의 조도(품질)&치수 향상을 목적으로 작업합니다..
주로 내경 홀 가공을 원칙으로으로 하나 변칙적으로으로 외경 홀(?) 작업 도 가능 하나 이는 논외로 하겠습니다.
먼저 처음 접 하시는 분 위주로 설명 하겠습니다.
보링 바는 구조 상 일반 절삭 공구처럼 지정 된 공구경 은 없고 가공 가능한 규격 범위 가 있습니다.
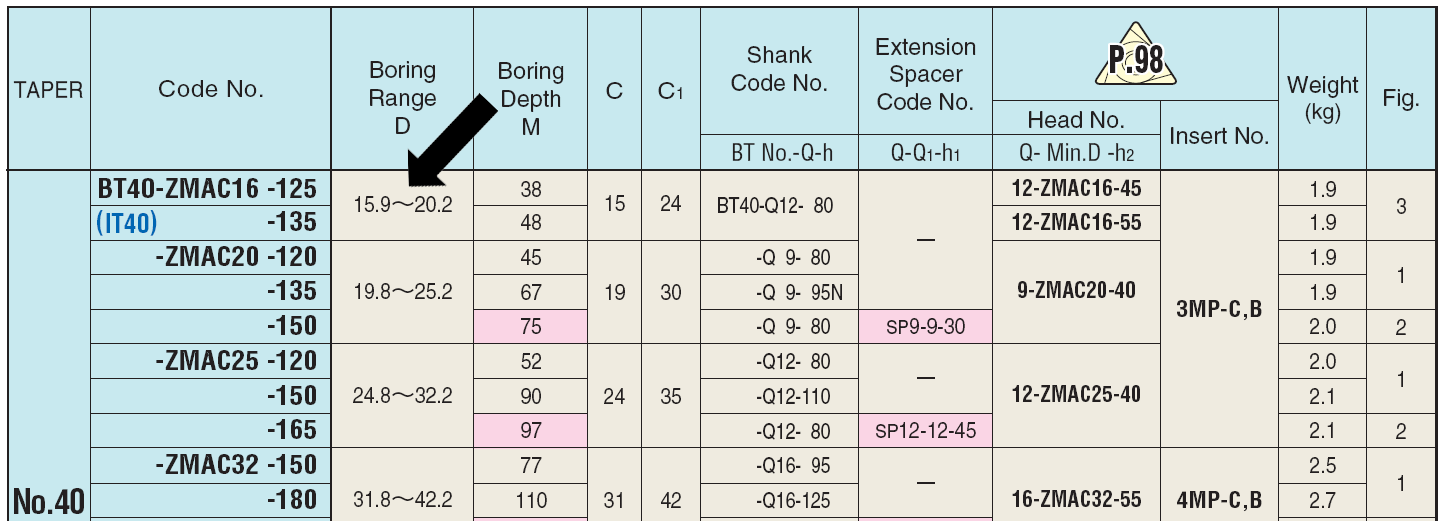
* 닛켄(NIKKEN) ZMAC ARBOR 형 자료입니다..
우선 닛켄 ZMAC 25 – 150 모델을 기준으로 설명합니다..
먼저 해야 할 일 이 해당 홀 작업 규격에 맞게 보링바 규격 세팅 을 하여야 합니다.
우선 가공 은 소재 알루미늄,, 홀 규격 은 32ø(+0.02)32 ø(+0.02)로 설정합니다..
* 주로 64ø미만을 마이크로 보링 바로 칭 합니다.
* 보링바보링바는 아바 일체형 , 밀링척 부착형 , 헤드 교체형 , 보링바 교체형 등 여러 가지 가 있습니다.
* 가공 시 선행 기초 홀 가공 이 되어 있어야 합니다.
* 주로 기초 홀은 드릴, 유드릴유드릴을 사용 합니다.
* 원칙 적으로 관통 홀 가공을 기본이며비관통 (막힌) 홀 가공 도 가능 하나 조금 단속(칩( 배출, 홀바닥 가공 여부 등 ) )을 고려하여야 합니다.
- 마이크로 보링 바 세팅-
1. 머시닝 센터 공구 부착
우선 해당 마이크로 보링 바 을 머시닝 주축 척 에 부착합니다..
1. 빠른 세팅 방법 ( 간단히 일회성 가공 경우)
간단하게 빨리 세팅하고1차 가공 후 다시 한번 규격을 확인 조절 후 재 가공 하는 경우에 해당됩니다.
보링바 규격 세팅 이 사실 현재 규격을 알고 그것을 기준으로 원하는 규격으로 미세하게 세팅하는 것이라 사실 방법 상 차이는 없습니다.
범용 밀링밀링에서 는 버니어버니어로 만 측정해서 하는 경우 도 있습니다.
(물론 홀 규격 측정 도 버니어버니어로 측정 합니다. 다만 버니어 내경 홀 측정 이 좀 믿음이 부족하여.)
최소 간단하게 하는 법 (측정 공구 가 버니어 밖에 없는 환경 기준)
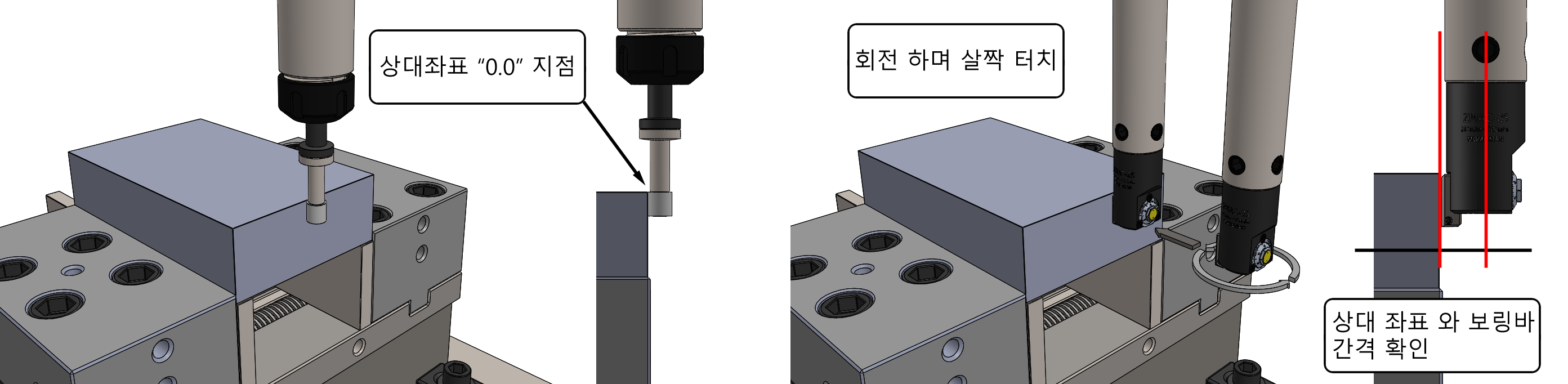
위 와 같이 먼저 면 이 깨끗한 잔재 을 놓고 아쿠센터 등 의 기구로 잔재 측면을 상대 좌표 “0” 으로 세팅 후 보링바 을 천천히 회전시켜 가면 서 잔재에 접촉하여 이때 둘 사이의 떨어진 간격을 상대 좌표 을 대조 하여 가며 측정한 후한후 실제 원하는 보링 치수 을 보링바 규격 조절 하는 기능을 이용 하여 조절합니다.
이후 일차 가공 후 (가능한 마이너스 가 나오도록) 가공 홀 측정 후 다시 치수 을 보정 하여 보링 가공을 마감 하는 방법 을사용 합니다.
* 단 이 방법 은 어느 정도 경험 이 있어야 할 수 있으나 처음 경험 상 연습 하며 하시기 에는 적당 한 방법입니다..
이 외 에도 더 간단하게 (사실 은 도구 가 없어서…) 하는 방법 은 범용 밀링 하시는 분 들 이 버니어만으로측정하여 하는 방법 도 있습니다.
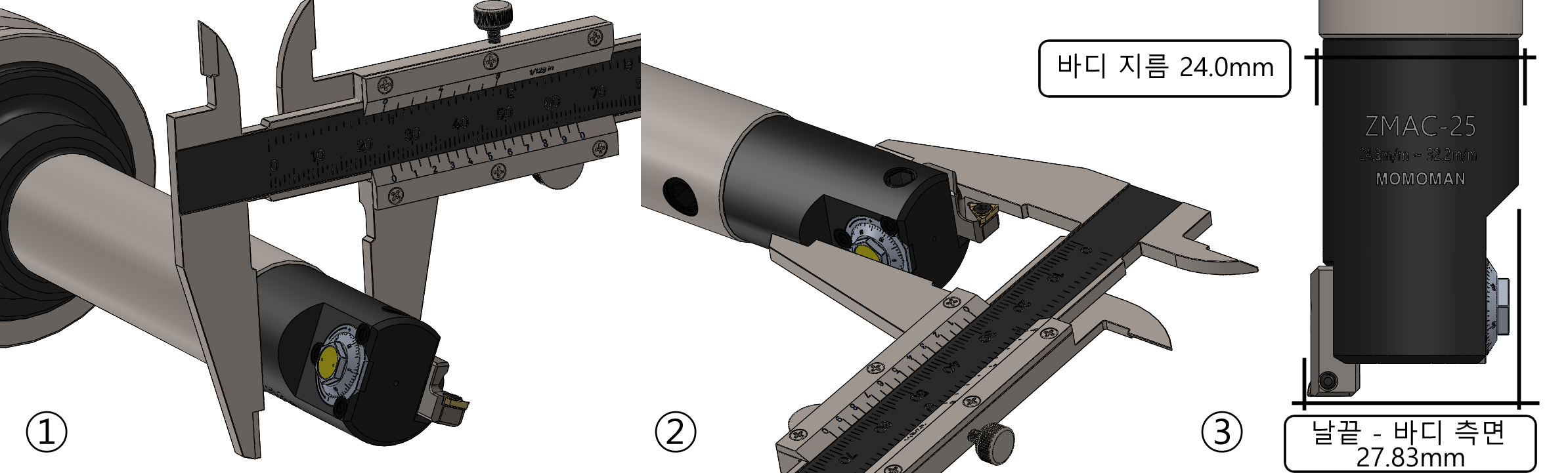
① : 버니어로보링바 하부 바디 구경을 측정 24mm
② : 버니어버니어로 인서트 날 끝에서 보링바 바디 끝을 측정 27.83mm
③ : 계산 27.83 – 24 = 날끝 돌출 길이 3.83 x 2(양쪽) = 7.66 + 바디 지름 24 = 31.66mm
이후 원하는 치수 32mm 이므로 보링바보링바의 치수 조절 기능을 이용 하여 31.66 + 0.34 = 32mm로 하여 1차 가공 후 홀 지름측정 하여 재 가공 합니다.
간단하면서 좀 더 정밀하게 하는 방법 (하이트 프리셋 사용)
이 는 많은 분 들 이 알고 계시는 방법입니다..
① 먼저 바이스바이스에 하이트 프리셋을 눕혀 살짝 고정합니다..
* 이때 절대로 하이트 프리셋을 물려서 바이스 을 잠그시면 안 됩니다. (하이트 프리셋 변형)
부드러운 소재 (MC , 장갑 등)을) 물려서 밀리지 않을 정도만 살짝 손으로 조이시기 바랍니다.
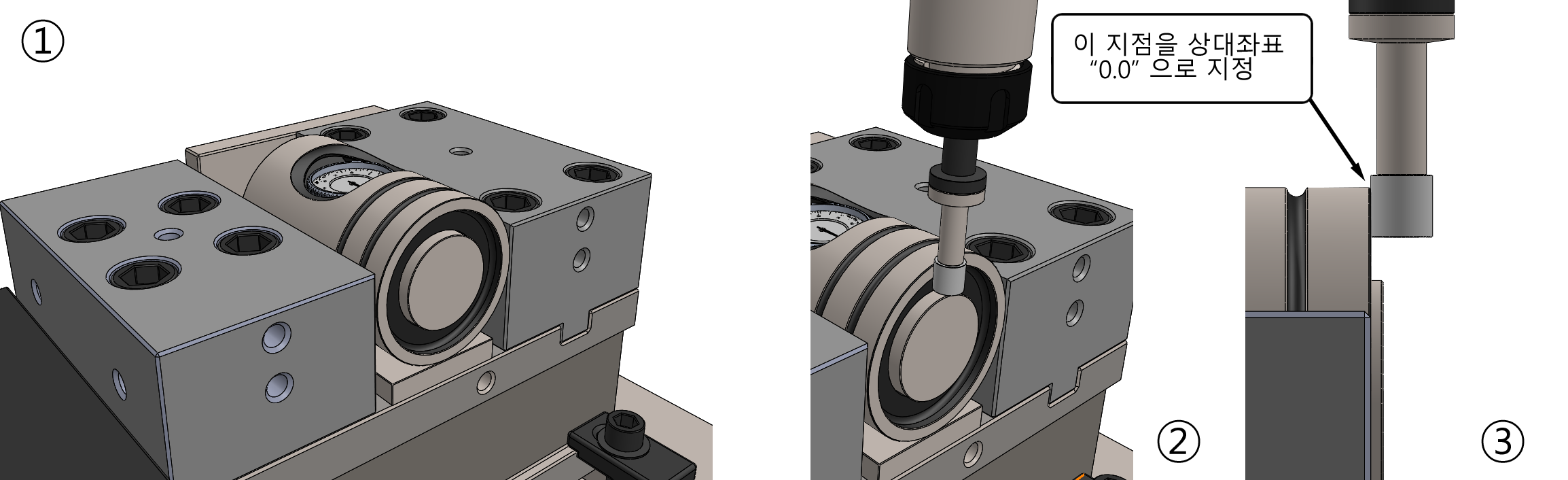
② 아쿠센터 을 호출 하여 하이트 프리셋 상부 테두리 (H:100 지점)을 터치합니다..
③ 이후 POS POS에서 이 지점을 상대 좌표에서“0” 으로 설정합니다..
④ 해당 마이크로 보링바 을 호출 합니다.
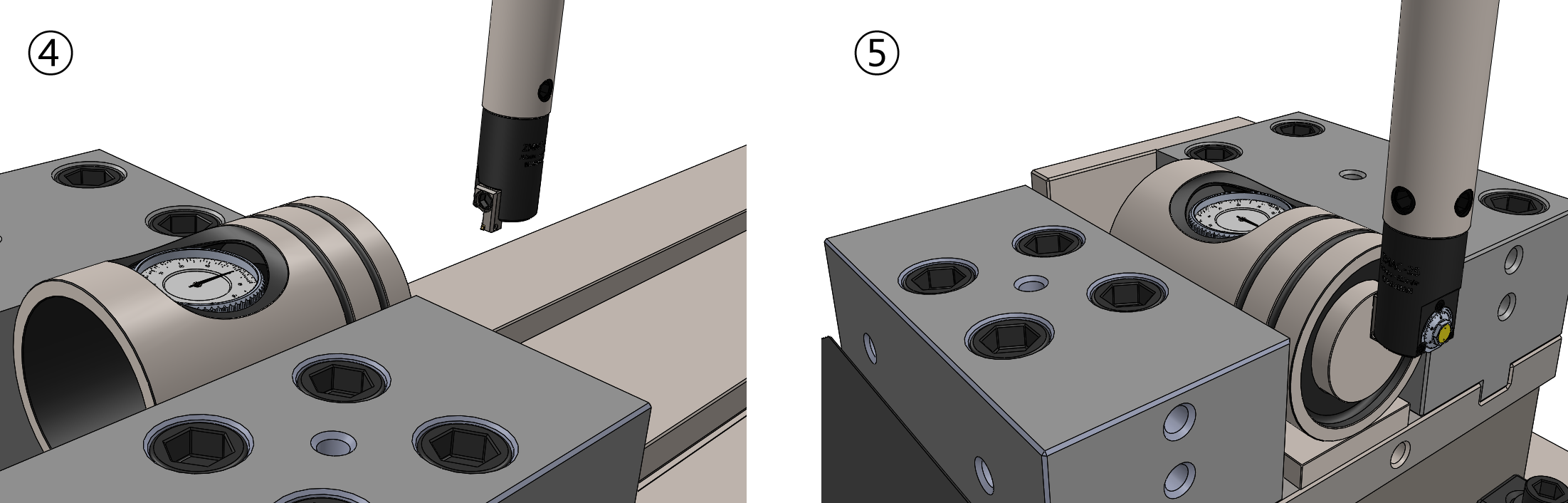
⑤ 보링바의 인서트 끝 쪽 을 하이트 프리셋 측정 방향으로 하여 근접시킵니다..
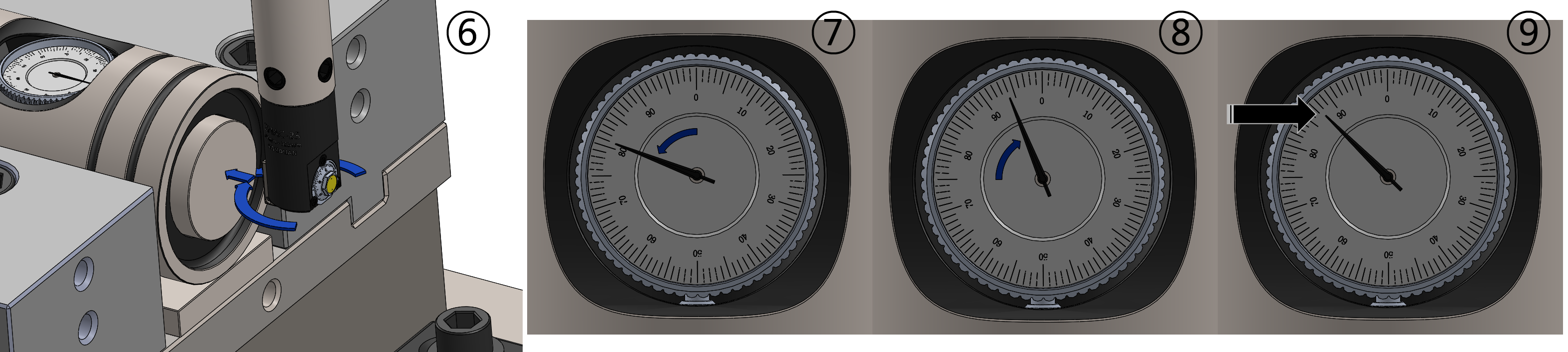
⑥ 보링바 을 손으로 돌리면서 인서트 날 끝 부분을 하이트 프리셋에 접촉하면서 최 상위 점 을 찾습니다.
(하이트 프리셋과 인서트 날끝 이 직각을 유지 되는 점을 찾는 것입니다,, 이때 게이지 의 눈금 이 꼭 “0” 이어야 할 필요가 없습니다.)
⑦⑧⑨ 손으로 돌리면 서 인서트 날 끝을 찾습니다. (눈금 이 -81 ~ -94 이므로 중심 점 은 87.5)
중심점을 찾았으면 중심점(87.5) 지점에서 움직움직이지 말고 핸들모드 (X축만)을 이용하여 하이트 프리셋 눈금 을 “0” 으로 조절합니다..
⑩ 이후 조작판 모니터상 의 상대 좌표 을 확인 한 후 그 상대좌표 값(X축) 이 현재 보링바의 반경 값입니다. (예: 15.83 이 나오면 보링바 지름 은 31.66mm입니다.)
*지금 까지 설명 한 방식 은 ±0.05mm 정도 오차 가 있을 수 있으므로 간단한 것 또는 규격 보다 조도가 더 중요하던가 하는 경우가 아니면 권장하지는 않습니다.
간혹 가다 특이 한 상황 (측정 기구 등 이 없는 경우)에) 제한적으로 사용하시기 바랍니다.
보통 추천 하는 방법입니다..
다이얼 게이지 을 활용 하는 방법
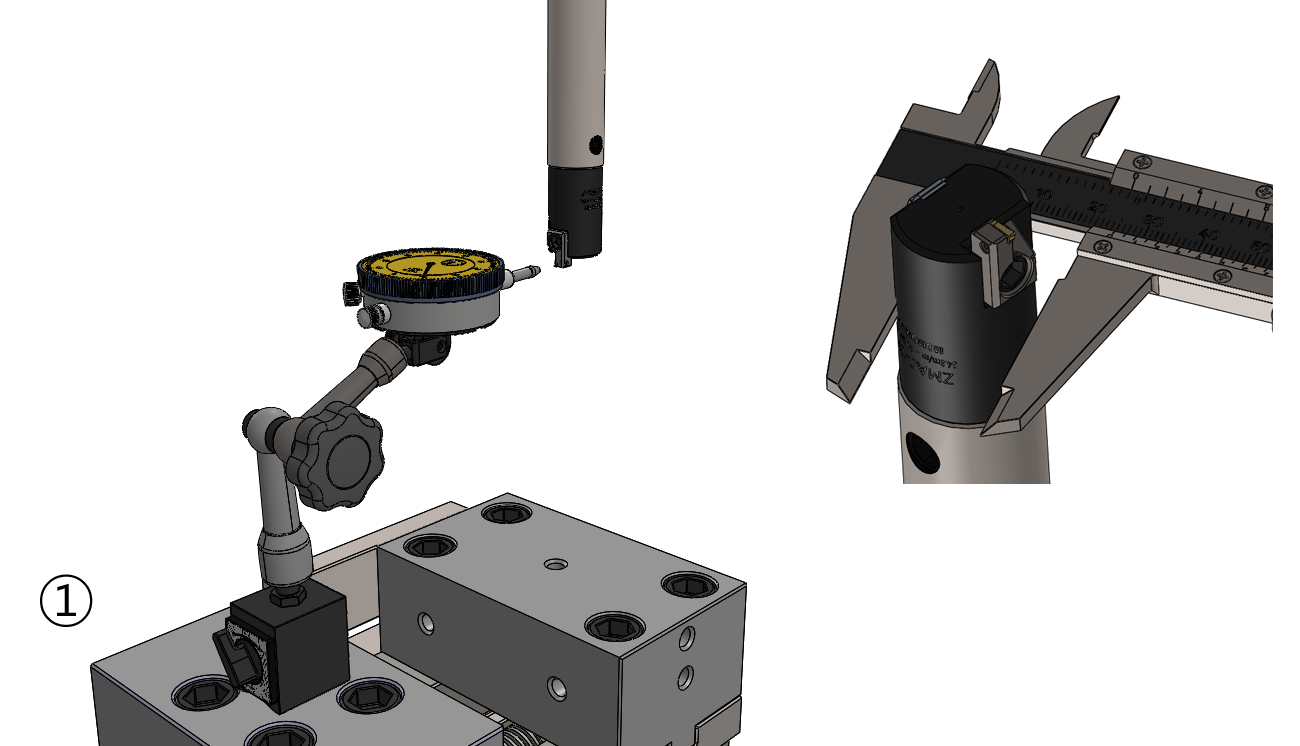
① 먼저 다이얼 게이지 을 마그넥틱 베이스 로 하여 적당한 장소에 부착해 놓고 보링바 을 호출 합니다.
(선행 작업으로 앞으로 측정할 부위 (보링바 바디 깨끗한 부분)을) 먼저 버니어 나 다른 측정 기구로 해당 기준 부위 지름 값을 먼저 알아 둡니다. 예: 24.02mm)
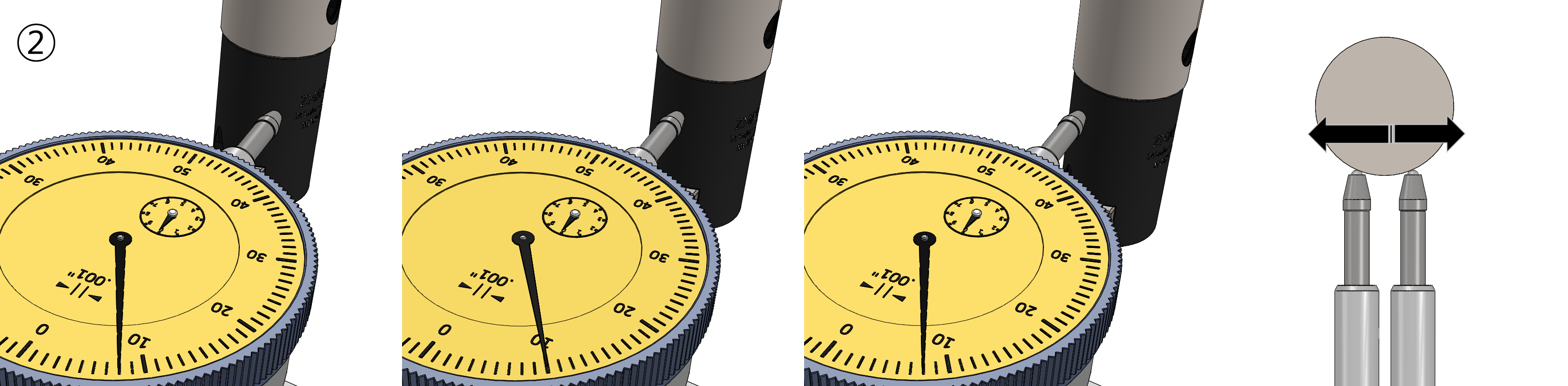
② 선행 측정 한 부위 을 다이얼 게이지에 접촉한 후 머시닝 핸들 모드로 좌우로 이동 해 보면서 바디 원통형 최상단 (원통형 중심)을) 구합니다. (다이얼 게이지는 고정 상태입니다.).)
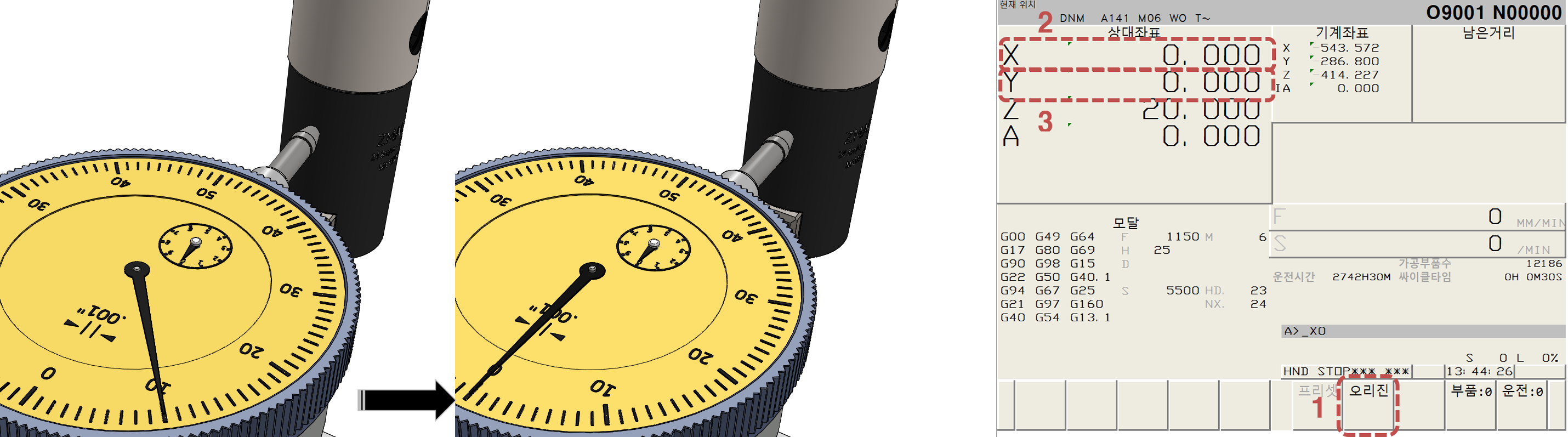
③ 중심점을 구한 후 X축 은 POSPOS의 상대 좌표 “0” 으로 고정 후 Y축 만 이동하여 다이얼 게이지 의 눈금 을 “0” 으로 조절합니다..
이때 움직이지 말고 POS의Y축 도 상대좌표 “0” 으로 고정합니다..
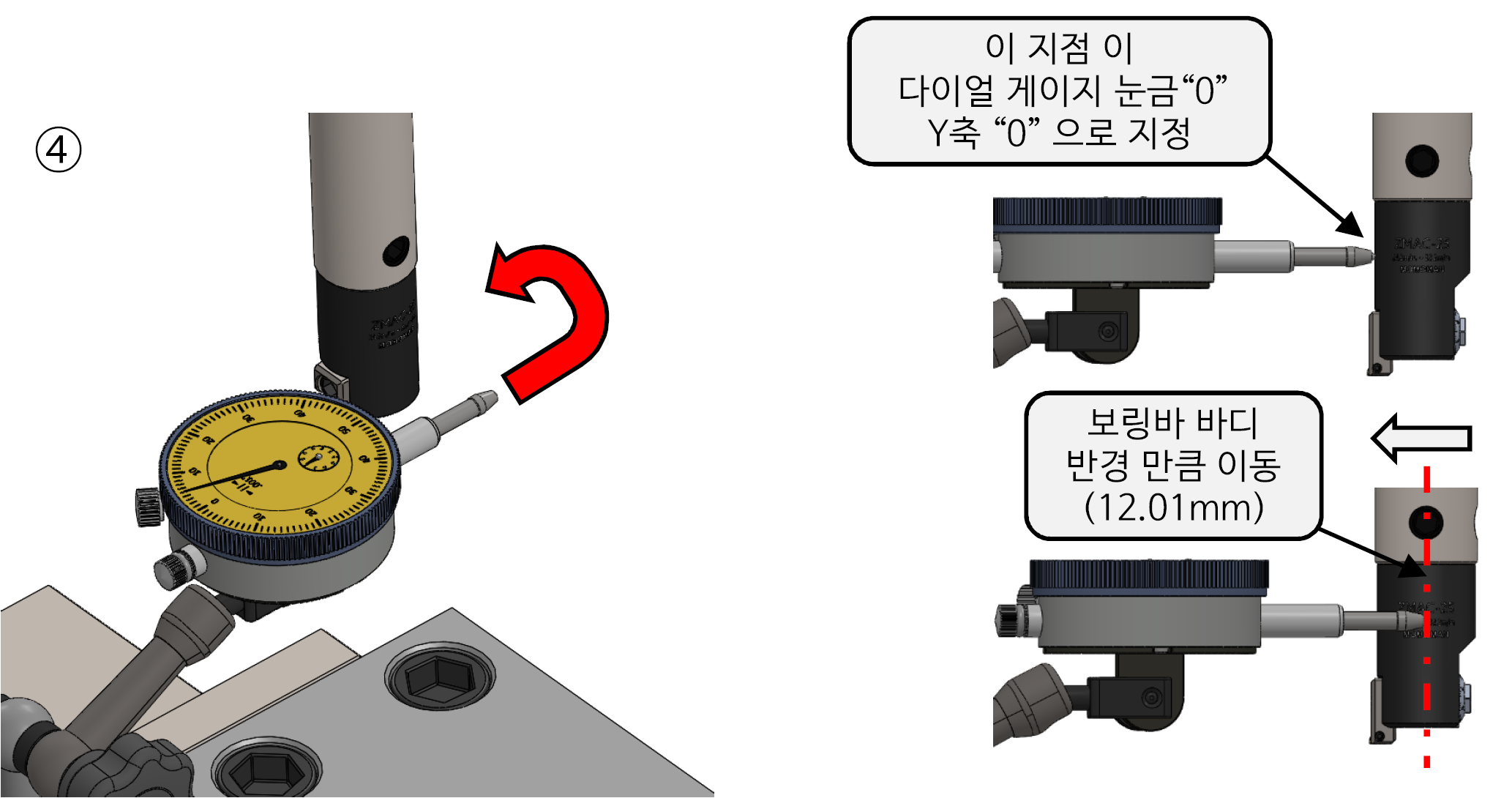
④ 이 후 보링바 을 핸들 모드로 좌우 한쪽으로 이동시켜 앞에서 측정 한 보링바 바디 직경(24.02)의 반경 (12.01) 만큼 앞으로 이동시킨 후 다시 POS POS에서 상대 좌표 Y축 을 “0” 으로 설정합니다..
(이렇게 하면은 아까 다이얼 게이지 눈금 “0” 이 위치 한 지점에보링바중심축 을 일치 하기 위한 작업입니다.)
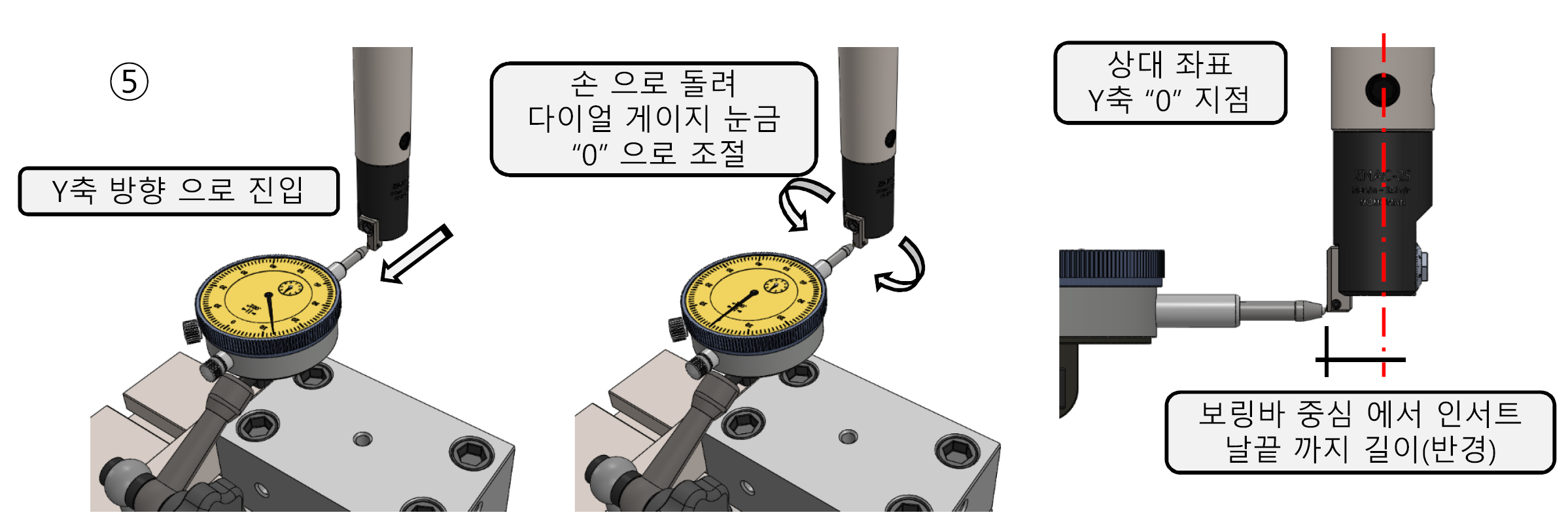
⑤ 이후 다시 보링바 을 핸들모드로X축 “0” 으로 이동한 후 Y축 방향으로 천천히 진입해 줍니다.
이윽고 다이얼 게이지 눈금 이 “0” 지점에 오면 보링바 을 손으로 살살 돌려서 역시 같은 요령으로 으로 Y축 최상지점을 찾아 주세요 (손으로 돌리는것 과 핸드 모드로Y축 이동 이 병행됩니다.).)
이후 잠시 움직이지 말고 머시닝 모니터상 의 상대 좌표 (Y축)을 보면 출력된 수치 가 현재 보링바 보링바의 반경 사이즈로 보시면 됩니다.
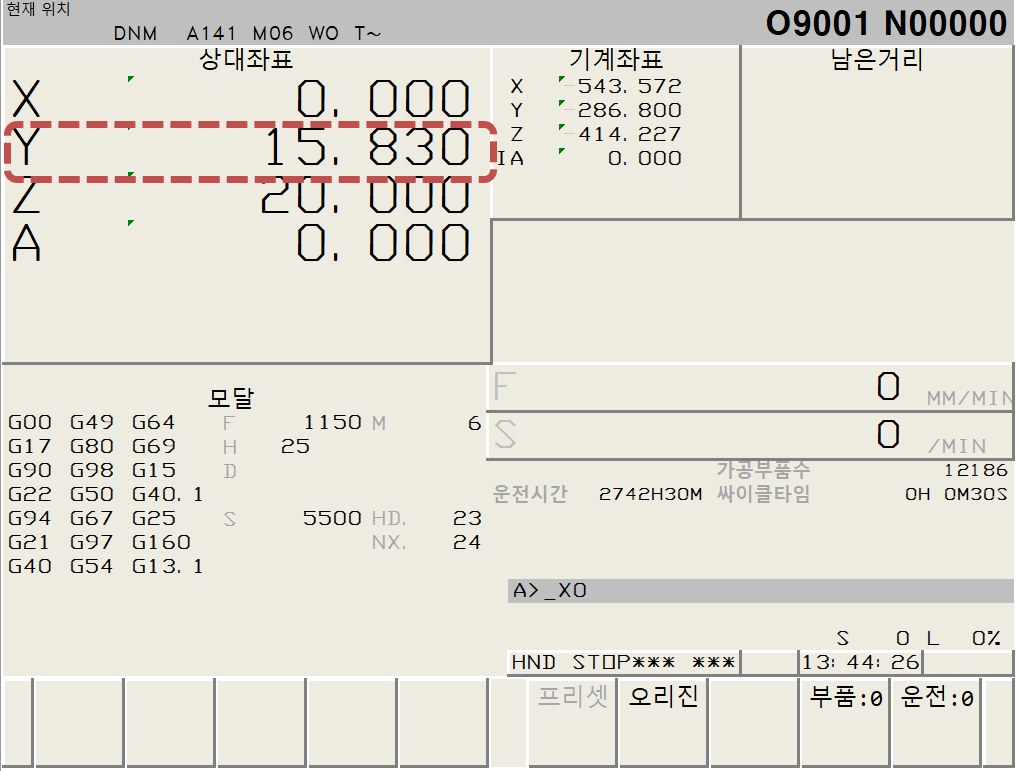
* 현재 상대 좌표 가 15.83 이므로 현재 보링바보링바의 가공 규격은 31.66mm입니다.
그런데 현재 가공 홀 규격 은 32 ø(+0.02)이고1차 가공은 31.9ø 31.9 ø로 가공 할 예정입니다..
지금 측정 한 보링바 규격 은 31.66 이므로 원하는 규격에서 0.24(0.12) 0.24(0.12)가 부족하므로 이 을 보정 해 주어야 합니다.
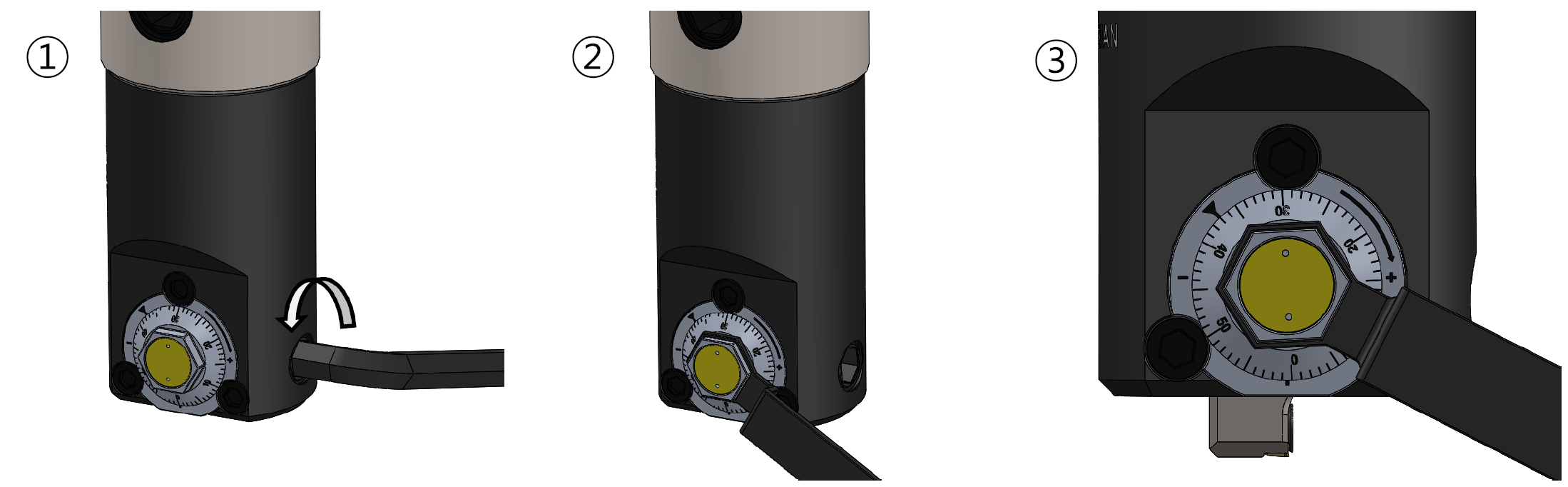
① 먼저 DIMMATER 고정 볼트 을 시계 반대 방향으로 돌려 풀어 줍니다. 살살..
②그 후 전용 공구로DIMMATER 조절 볼트 을 잡고 원하는 치수만큼 돌려 보정합니다..
③ 여기서는 각 눈금 단위 가 0.01mm 0.01mm이고 현재 +0.12 만큼 보정해야 하니 시계 방향으로 현재의 눈금을 기준 하여 12 만큼 돌려줍니다..
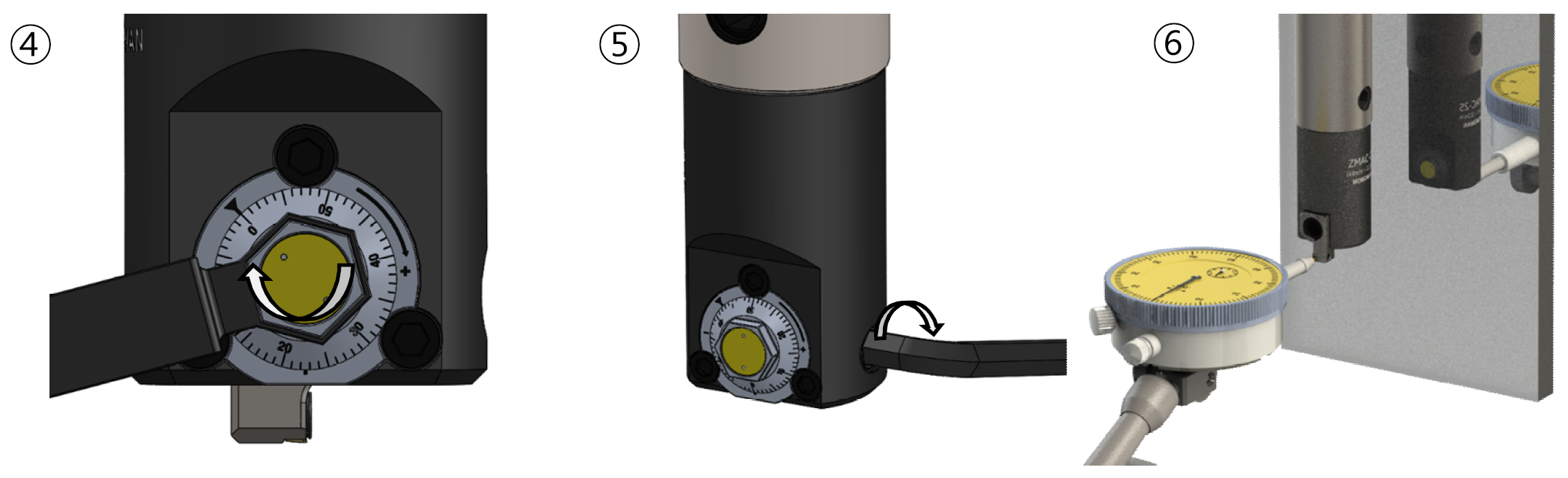
④⑤ 원하는 치수만큼 조절하여 돌려준 후 다시 DIMMATER 고정 볼트 을 시계방향으로 돌려 조여 줍니다.
⑥ 이후 마지막으로 다시 한번 다이얼 게이지에 접촉하여 POS POS의 상대 좌표 을 다시 확인하여 보링바 규격을 확정 합니다.
이후 다시 작업 단속 을 하여야 하니 공구에 현재 측정 한 공구 경 값을 적어 놓거나 어느 관리 문서에 기입한 후 다음 작업 준비 을 합니다.
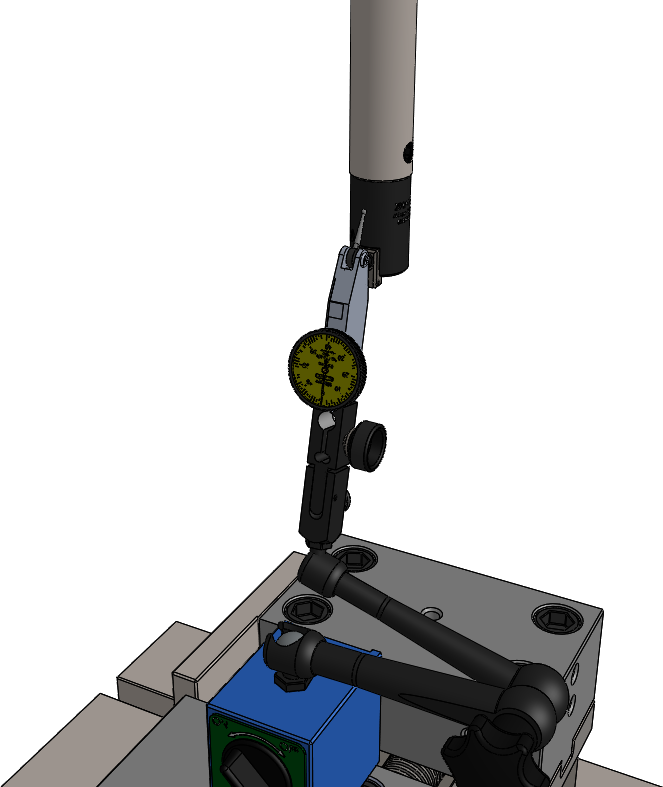
황삭 용 보링바 세팅 방법
여러 가지 이유 가 있겠지만 만일 대략 60ø 이상 홀 보링 을 하여야 할 경우 이 규격에 준 하는 드릴이나IC드릴(유드릴) 등 공구로1차로 황삭 하기 어려운 상황 일수 있습니다.
그러므로 1차로 드릴 이나 IC드릴 공구 로 1차 홀 황삭 (2차 황삭 보링 가공 이 가능할 정도의 규격)을) 하고 2차 황삭 용 보링 공구로황삭 을 하고 나서 3차로정삭 보링 하는 경우가 있습니다.
그래서 황삭 용 보링 공구 세팅 하는 법 을 보겠습니다.
( 기본적으로 가공 인서트 가 양쪽에 있는 경우 을 황삭 보링바보링바라고 칭 합니다.)
일단 황삭용 보링 공구는황삭 가공 이므로 약간 의 가공 여유(높은 정밀도가 필요 없는)를) 가지므로 어느 정도 여유 을 가지고 세팅합니다..
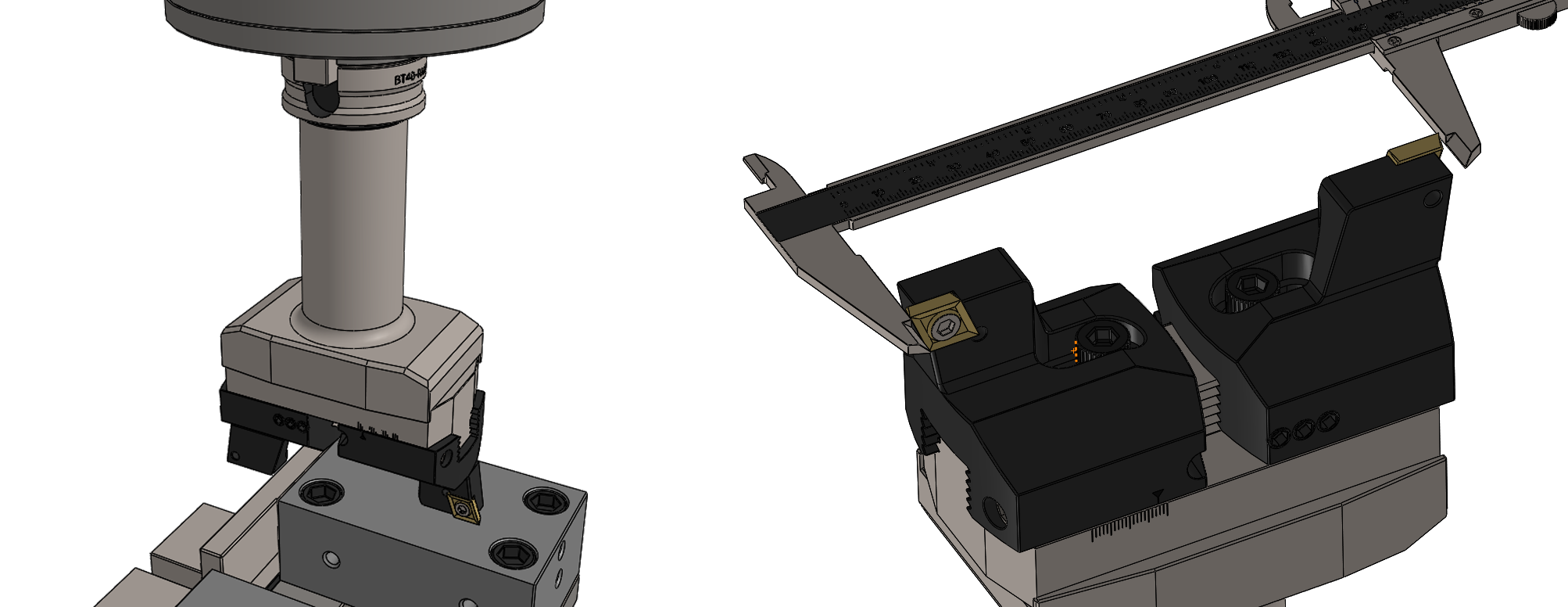
먼저 해당 황삭 보링 공구 을 호출 한 후 공구 을 어느 기구 을 이용 하여 뒤집어 고정한 후 버니어 같은 측정 기구로 양쪽의 인서트 끝날 거리 을 측정 합니다.
측정 결과 가 141.04mm 141.04mm로 나옵니다.
황삭 가공 규격 이 145.00mm이라면145.00 – 141.04 = 3.96 / 2 = 1.98 (한쪽당) 이므로 이에
따라 보링바규격을 재 설정 합니다.
* 물론 상황에 따라 정삭 용 보링바보링바처럼 다이얼 게이지에 세팅하여 조절하는 방법 도 사용 합니다.
(사실 안전하게 할려면 이렇게 하여야 합니다.)
* 방법 자체는 해당 보링바 공구 특성에 따라 차이가 있습니다.
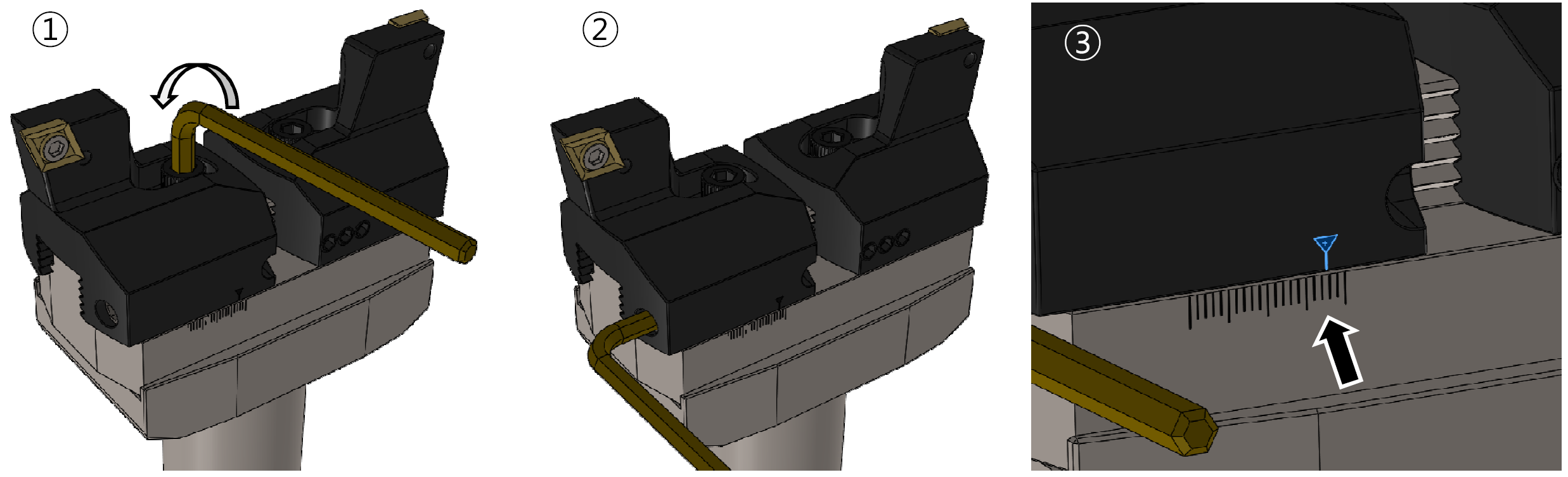
① 인서트 카트리지 고정 볼트 을 풀어 줍니다. (방향 은 일반 볼트와 동일합니다.).)
② 이후 카트리지 의 조절볼트 을 돌려 조절해 줍니다. (보통 조이면 규격 이 줄어들고 풀어주시면늘어납니다.
③ 카트리지 조절 규격 의 확인 은 유니트 의 보통 조절량 규격 눈금 이 각인되어 있습니다.
(보통 눈금 간격 이 1mm 단위입니다.)
(정삭용 보링바 와 틀리게 측정 한 값에 더하고 빼고가 아니고 옆에 각인된 눈금을보사고 해당 규격 으로 조절하셔야하셔야 합니다.
눈금 이 해당 공구 보링 규격 이므로 위 같은 경우 눈금 보시고 145 ø의 맞추어 조절한 후한후 다시 카트리지 고정 볼트 을 조여 주시고 반대쪽 카트리지 도 동일 하게 작업 합니다작업합니다.좌우 카트리지 의 조절 장치 가 서로 연동되지 않으니 각자 확인 하여 조절하셔야하셔야 합니다.)
위 와 같은 절차로황삭 보링바규격을 세팅 한 후 다시 측정하여 확인하시며 보통 가공 하시면 측정된 규격 보다 0.01~0.03mm 정도 마이너스로 가공 경우 가 많으니 이에 참조 바랍니다.
* 어디까지 나 황삭 공구 이므로 이 에 대한 공구 사용 검토가 필요합니다..
여기까지 세팅했을 때 잠시 가공 전 확인 하여야 할 사항 이 있습니다.
보통 황삭용 보링 가공 은 일반 IC드릴(유드릴)과G81 , G83 , G86 등으로 일반 드릴과 같이 가공 공정 을 진행 하므로 해당 사항 없습니다.
하지만 정삭 보링 가공 은 G76 정밀 보링 사이클을 진행 합니다.
보링 싸이클 은 정삭 이 완료된 이후 현재 보링 가공 작업 이 끝난 홀 면과 동일 한 위치에 있는 공구의 끝날을 지정 치수 (머시닝 파라미터(#5148) , G76 파라미터 Q값 등)으로이동후복귀하는 기능입니다.
* 황삭 보링 (G86) 가공 과정
G86 (일반 보링 사이클)은 일반 드릴 싸이클사이클과 틀림 점 이 가공 깊이 까지 가공 후 최종 가공 깊이 까지 도달 후 공구 회전 정지(M05) 후 그대로 급속 이송으로R점 까지 복귀하는 것입니다..
(중요한 점 이 가공 좌표(X, Y)는(X,Y) 변동 없고 회전 없이 R점 까지 급속 복귀 하는 것입니다.).)
G86 황삭 보링 가공 과정
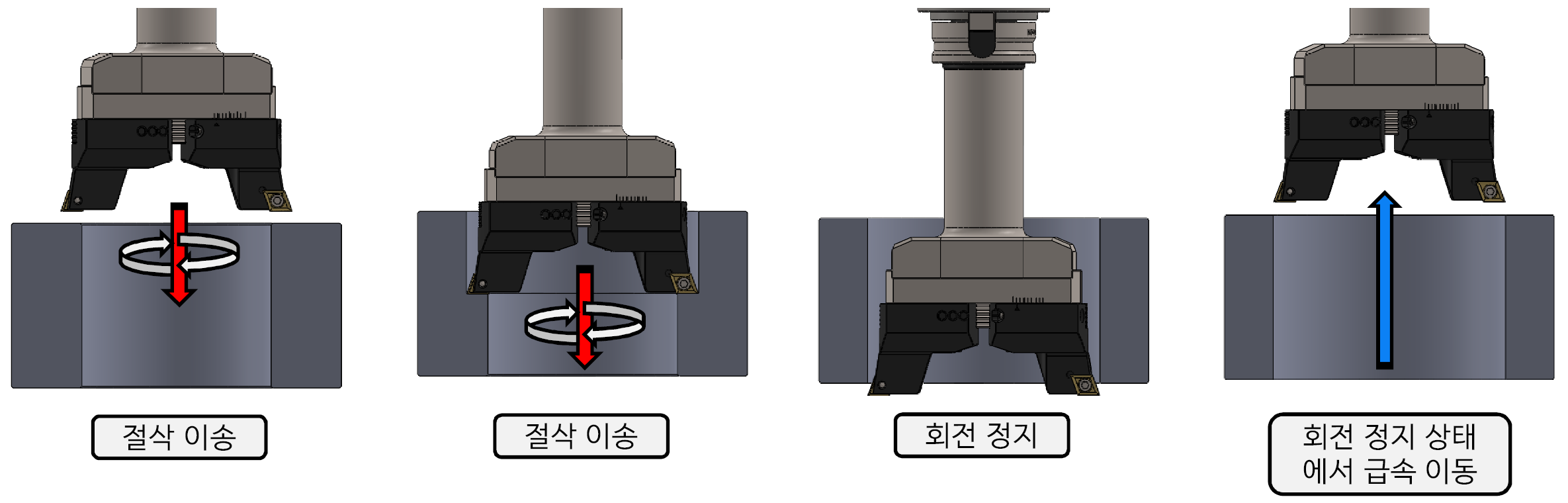
위 와 같이 공구 가 회전 정지 상태에서 급속 이송으로R점 복귀하므로 경우에 따라 가공 홀 면을공구 가 끌면서 올라가 홀 면에 자국 이 발생할 수 있습니다.
그러므로 정삭 가공 시 G76 (정밀 보링 사이클)을 사용하는 데 가공 과정 은 다음과 같습니다.
G76 정삭 보링 가공 과정
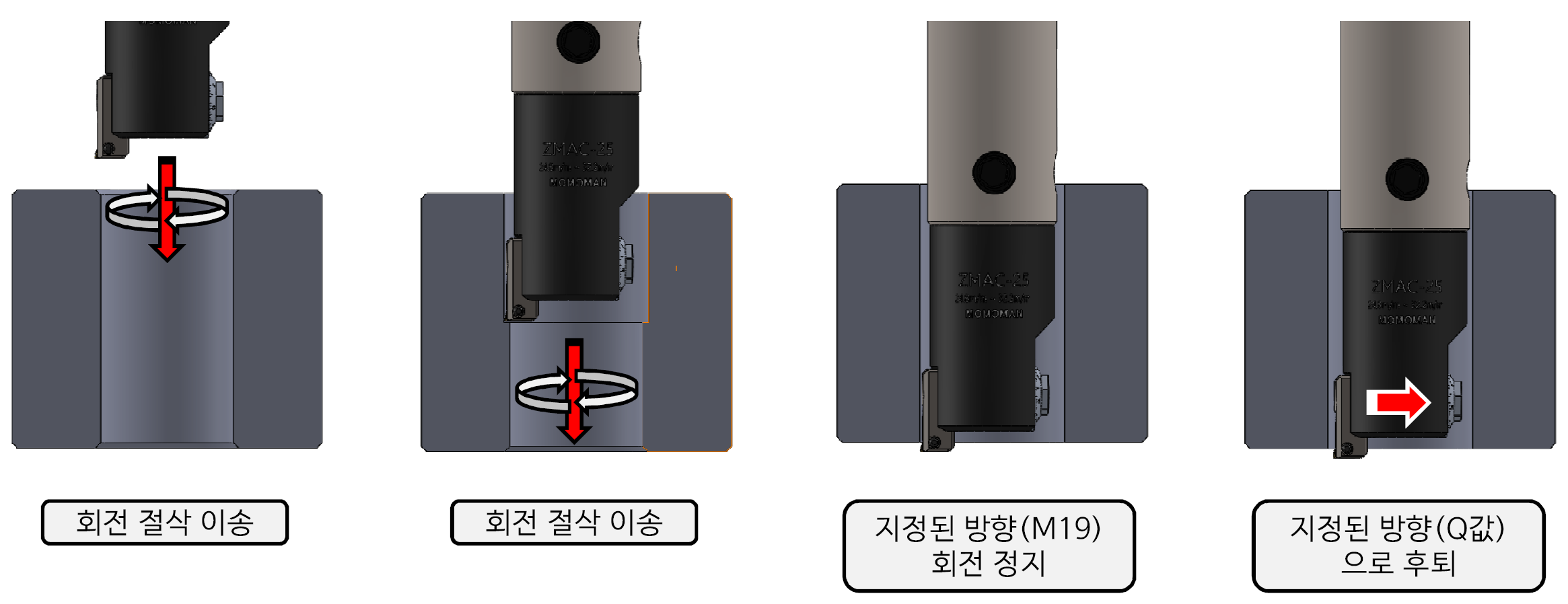
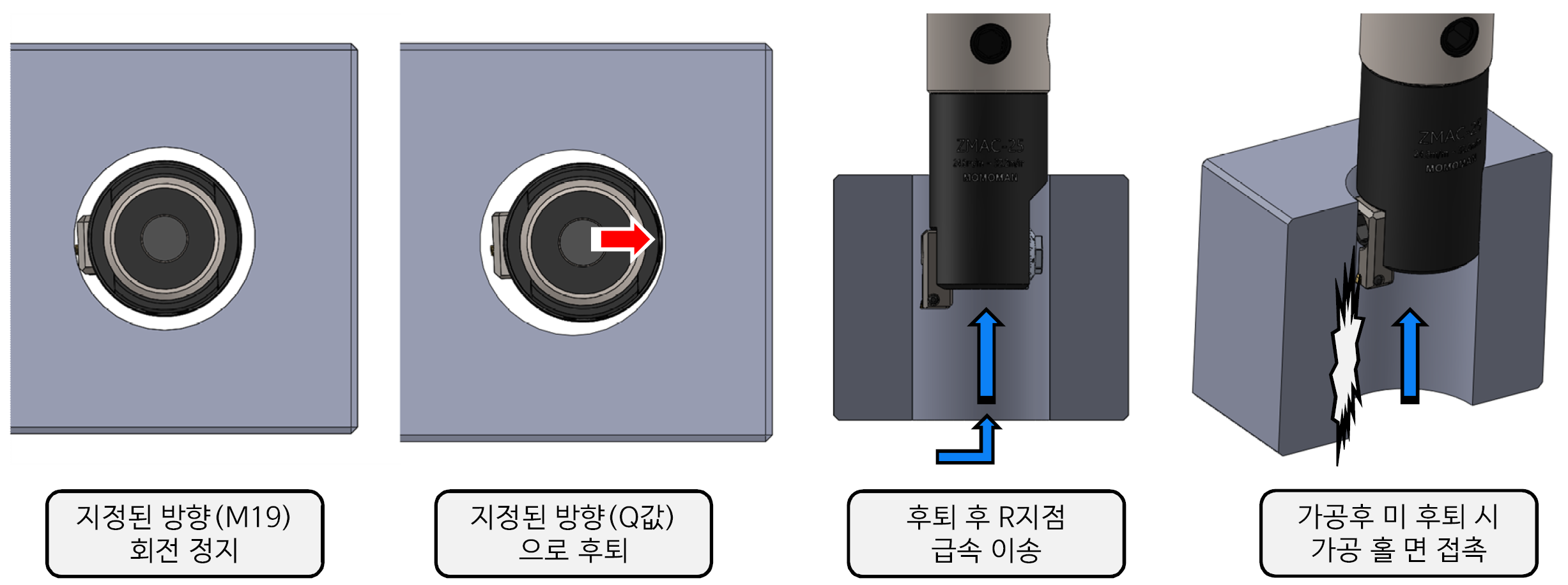
이와 같이 가공 완료 후 보링바 의 인서트 끝날 이 가공면가공면과 일치 하므로 급속 이송으로으로올라갈 때가공 면을 깍고올라갈 수 있습니다. (거의..)
그러므로 G76 싸이클 사용 시 QQ값을 이용 하여 보링바 을 살짝 후퇴한 후 R점 급속 이송 하도록 해야 합니다.
이때 고려 사항 이 있습니다.
1. 가공 후 정지 방향 은 주축 오리엔털 (M19) 위치에 정지하여R점 복귀합니다..
2. 그러므로 처음 공구 부착 시 G76 QG76Q값에 의 한 후퇴 을 고려 하여 공구 을 부착 하여야 합니다.
3. 이 후퇴 값 은 기본적으로 머시닝파라미터(#5148)에 근거 한 G76 싸이클 QQ값에 좌우됩니다..
그러므로 위 보링바 공구경 (가공 지름)을) 확정하고 나서 이제 가공을 위 하여 공구 주축 부착시 공구 방향(인서트 끝)을정하 셔야 합니다.
우선 머시닝 파라미터 설정을 알아보겠습니다..
화낙 시스템 의 경우 #5148 에 기준 합니다.
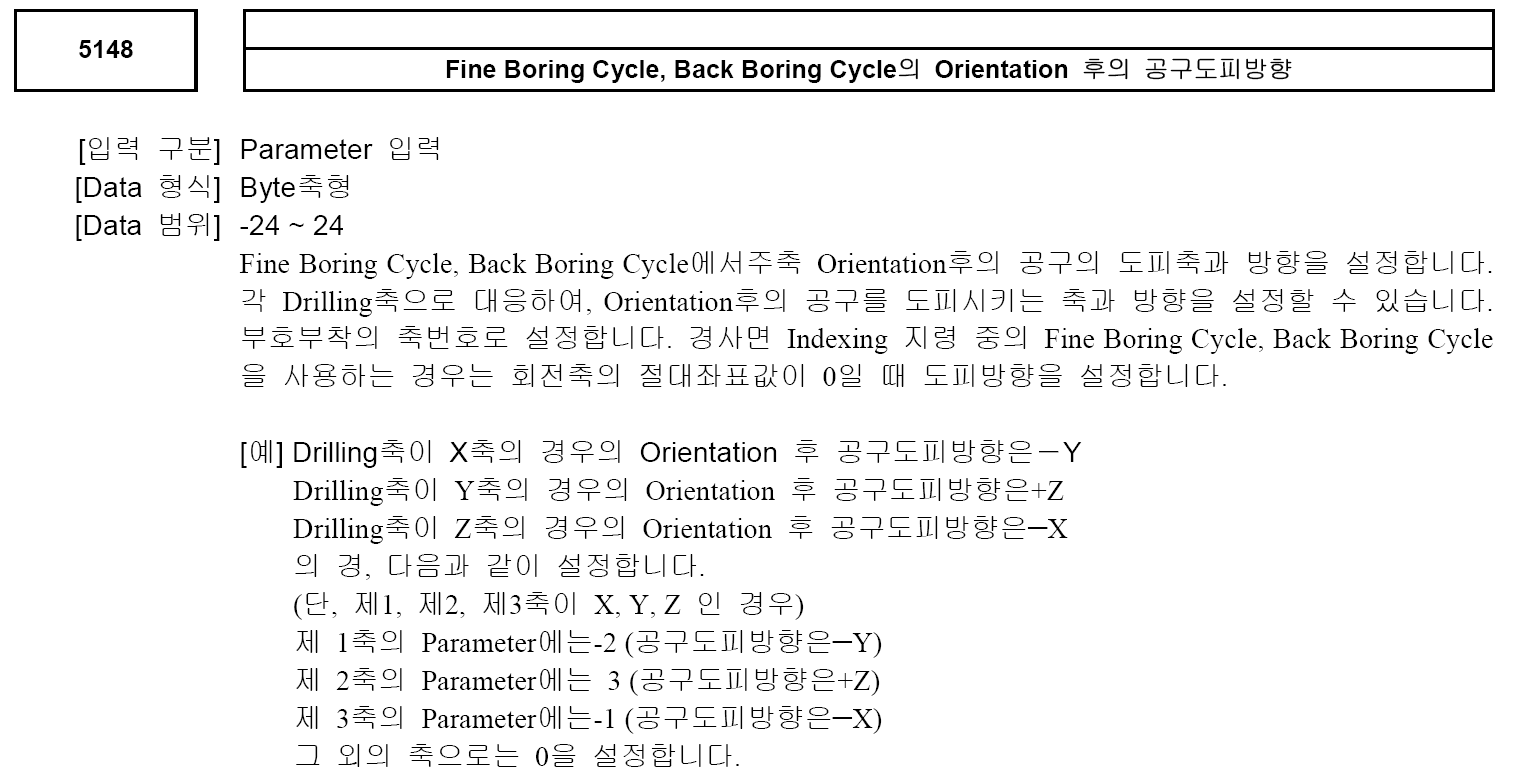
# 5148 파라미터 변수
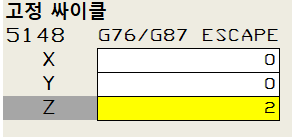
* 우선 #5148 #5148의 X,Y 축 변수 값은 “0” 으로 설정합니다..
이는 G18,G19 좌표계 용입니다. (도피 축 설정 : “0” 미설정)
Z 축-1 , 1 ,-2 , 2 네종류 가 있으며 각각 변수값 은 다음과같은 의미 을 말합니다.
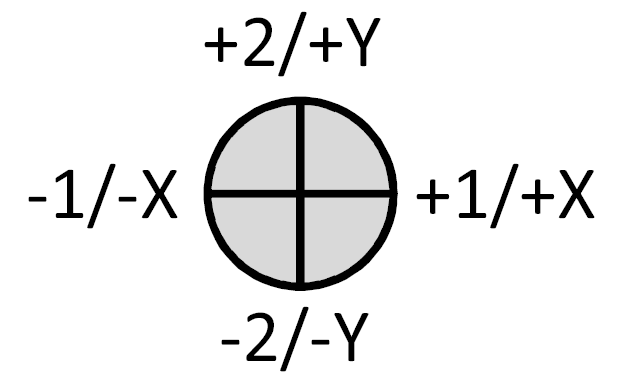
-1 = -X축 방향으로 QQ값만큼 도피 / 1 = +X축 방향으로 QQ값만큼 도피
-2 = -Y축 방향으로 QQ값만큼 도피 / 2 = +Y축 방향으로 QQ값만큼 도피
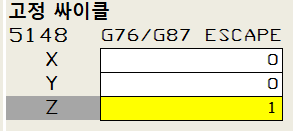
그러므로 작업자 가 보랑바세팅을 인서트 끝날을–X 방향 (CW 270˚)에 놓고 가공후 +X 방향으로 도피하여R점 급속 이송 할 계획이면 #5148 (Z) 설정 값을 “1” 로 입력하시면 됩니다.
* 만일 이것이 정상적으로 작동하지 않은 경우 파라미터 #5101 #5101을 확인해 보시길 바랍니다.
#5(RD2) #4(RD1) G17 G18 G19
“0” “0” “+X” “+Z” “+Y”
“0” “1” “-X” “-Z” “-Y”
“1” “0” “+Y” “+X” “+Z”
“1” “1” “-Y” “-X” “-Z”
* #5101 파라미터 가 G17 G17로 고정 되어 해당 변수 을 수정 못 하는 경우 도 있습니다. (기계 사양)
이러한 문제 때문에보링바 사용시 (아바 일체 형,, 밀링척 고정 형 등) 미리 M19 주축 오리엔털 기능 시 작업자 가 인지하는 방향으로 인서트 가 향 하도록 미리 세팅되어 있어야 합니다.
그러므로 맨 처음 시 보링바 사용 시 주축 부착 후 주축 오리엔탈 기능을 사용 하여 방향을 확인 하셔야 합니다.
1. 해당 공구 을 주축에 부착합니다..
2.MDI 모드에서 M19 M19을 지령합니다..
PROG - MDI - “M19” 키보드 입력 + EOB 입력 - INSERT 입력 - CYCLE START 입력
3. 주축 이 해당 오리엔탈 위치로 온것 을 확인 후 (보통 이 위치 가 공구 교환 위치입니다.) 보링바 보디 유니트 고정 무두볼트 을 풀거나 밀링척 부착형 은 척 고정을 살짝 풀어서 보링바 유니트가 돌아갈 정도만해두시고방향을 돌려서 다시 고정(흔들리지 않을 정도 만 고정하시고 나중에)
주축에서 공구 분리 후 다시 확실하게 조여 주시기 바랍니다. (주축 고정 상태에서 척 조작 불가!!)
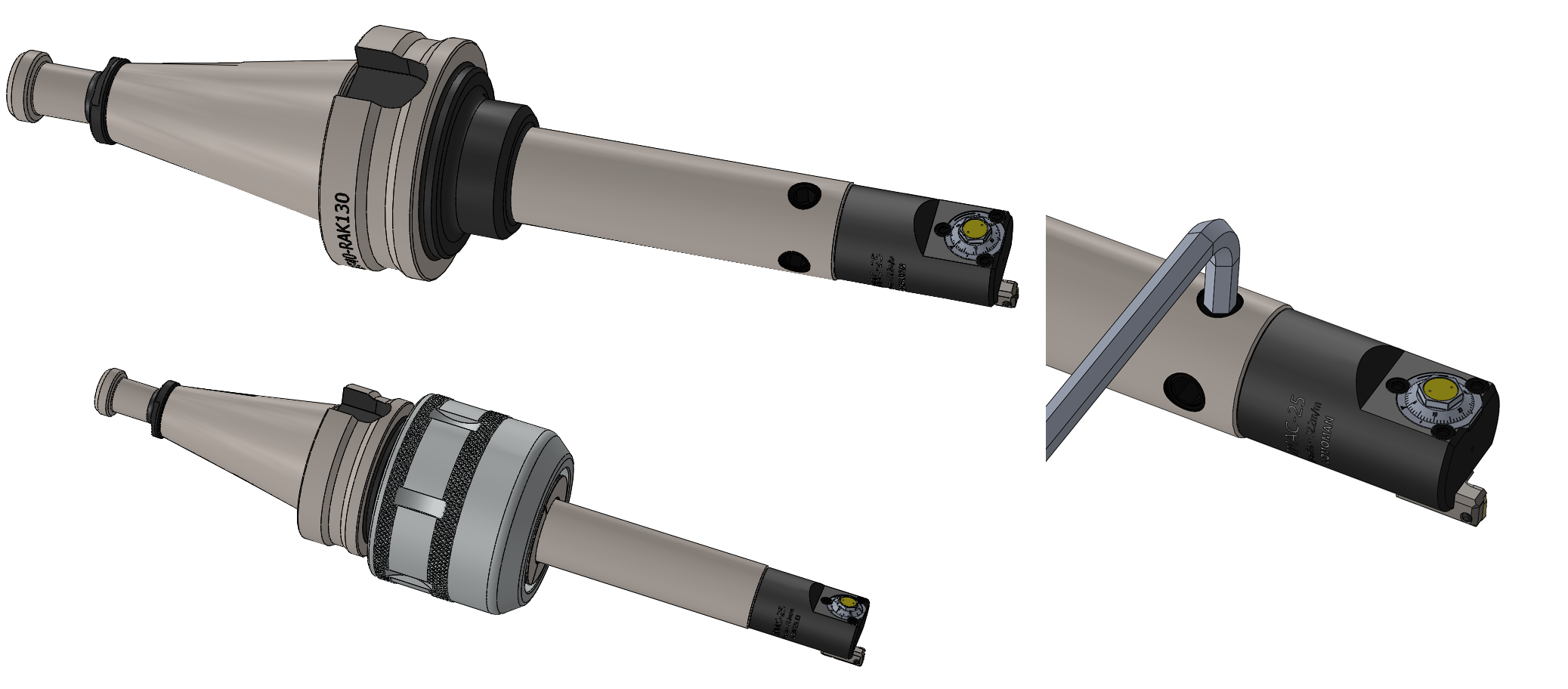
이제 실 가공시 G76 QG76Q값을 어느 정도 해야 하는지 알아보겠습니다.
* 실제 가공면가공면에서 살짝만 (0.1mm) 떨어져도 무방 하지만 마음 약한 분이 많아 계산해봅니다..
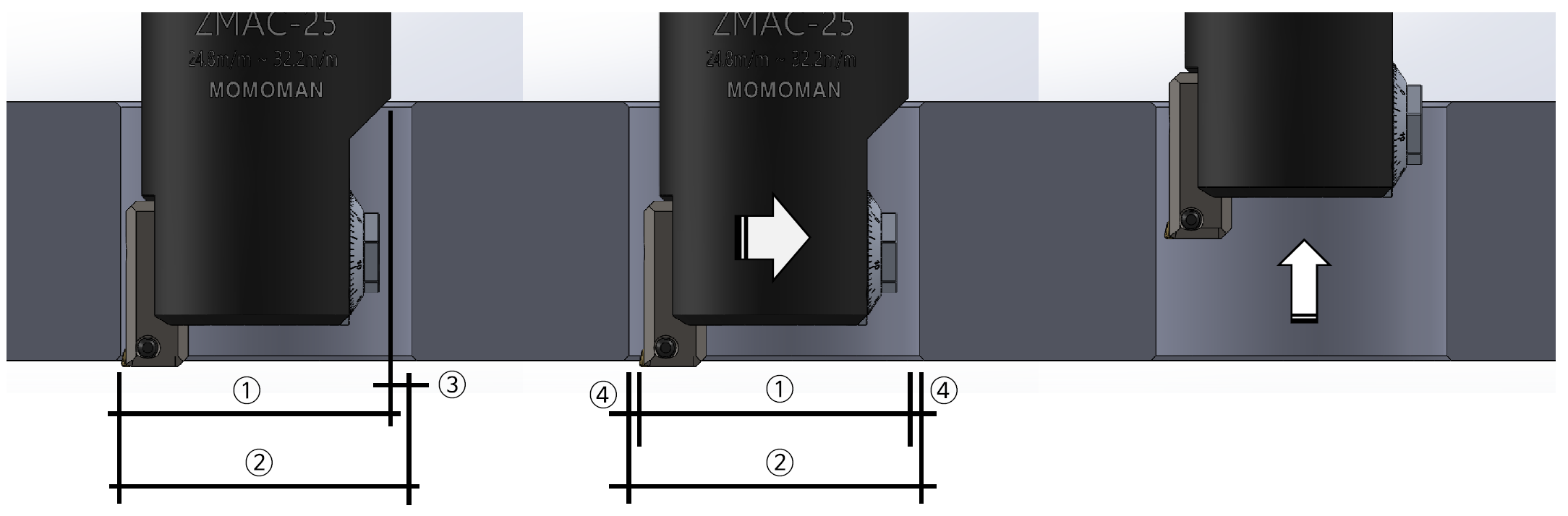
① 보링바바디에서 인서트 날끝 까지 규격 (예 : 25.95mm)
② 가공 홀 규격 28.0ø
③ 보링바 바디 한쪽에서 가공 면까지 틈새 (28.0 - 25.95=2.05) Q값 적용 가능 최대 값
④ Q값을 2.05/2=1.025 2.05/2=1.025을 적용 시 양쪽 틈새 의 규격
간단히 하여 가공 홀 규격에서 인서트 끝날에서 바디 한쪽끝한쪽 끝까지 규격을 뺀 나머지 을 다시 둘로 나뉜 수가Q값 도피 가능 최대 값이 됩니다. 그러므로 여기서 약간 정리하여(1.025 이면 대충 1로) 대입하여 입력하기도 하며 아니면 가공 면에서 살짝 떨어지기만 하면 되므로 0.1~0.5 정도 고정된 값을 입력 하기도 합니다.
예 : G98 G76 Z-22.0 R2.0 Q0.5 F20.0
가공된 홀 내경 측정 방법
이렇게 보링바 을 이용 하여 가공을1차 완료하고 공차 확인을 위 하여 측정 을 하여야 합니다.
이러한 측정 에는 여러 가지 방법 이 있지만 (보통 버니어캘리퍼 , 내경 마이크로미터,, 실린더 게이지 등) 여기서는 실린더 게이지와버니어 캘리퍼캘리퍼로 하는 법을 설명하겠습니다..
1. 실린더 게이지 (보어 게이지)
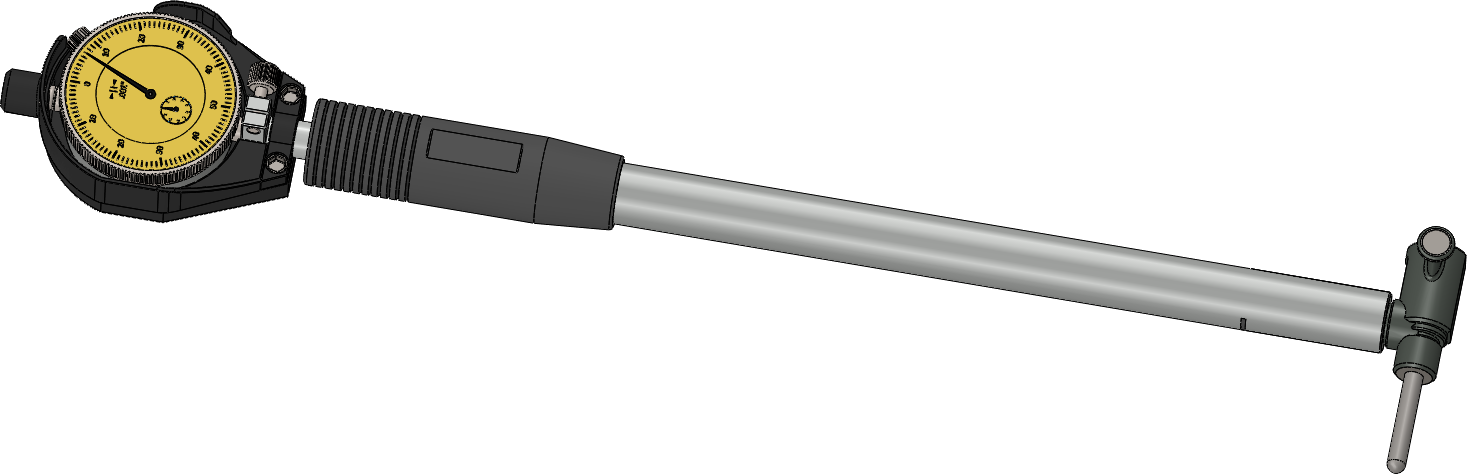
우선 해당 측정 규격(100 ø)에(100ø) 맞는 실린더 게이지 을 준비 합니다.
그리고 실린더 게이지 부품 중 측정하려는할려는 100ø 100 ø에 맞는 서브 앤빌앤빌을 준비 하여 실린더 게이지에 부착해둡니다.
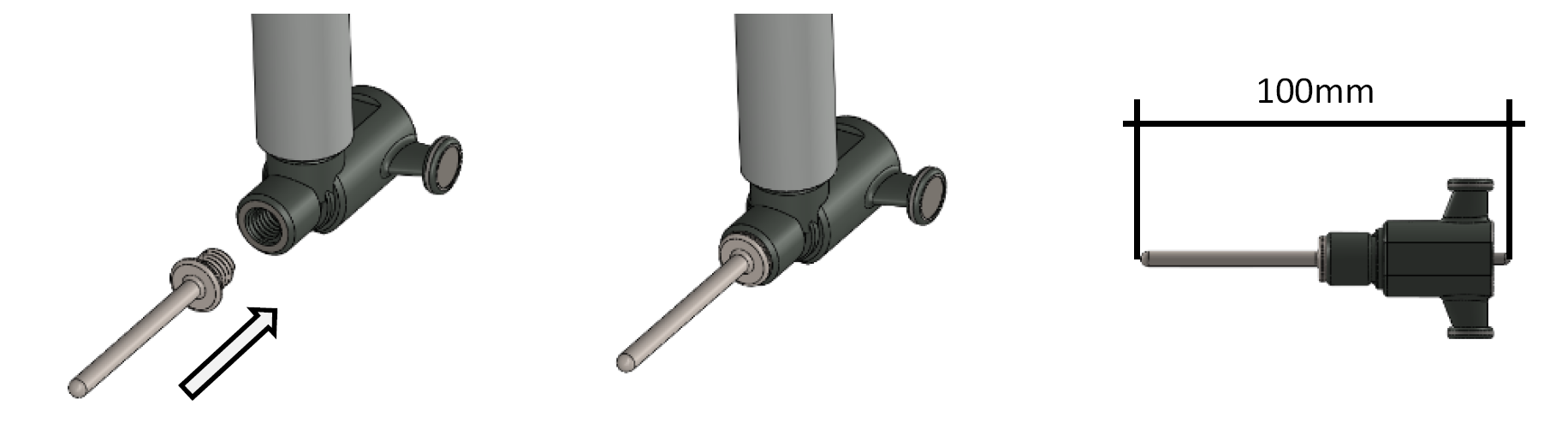
이후 미리 100mm에 맞추어 놓은 마이크로미터 을 준비 합니다.
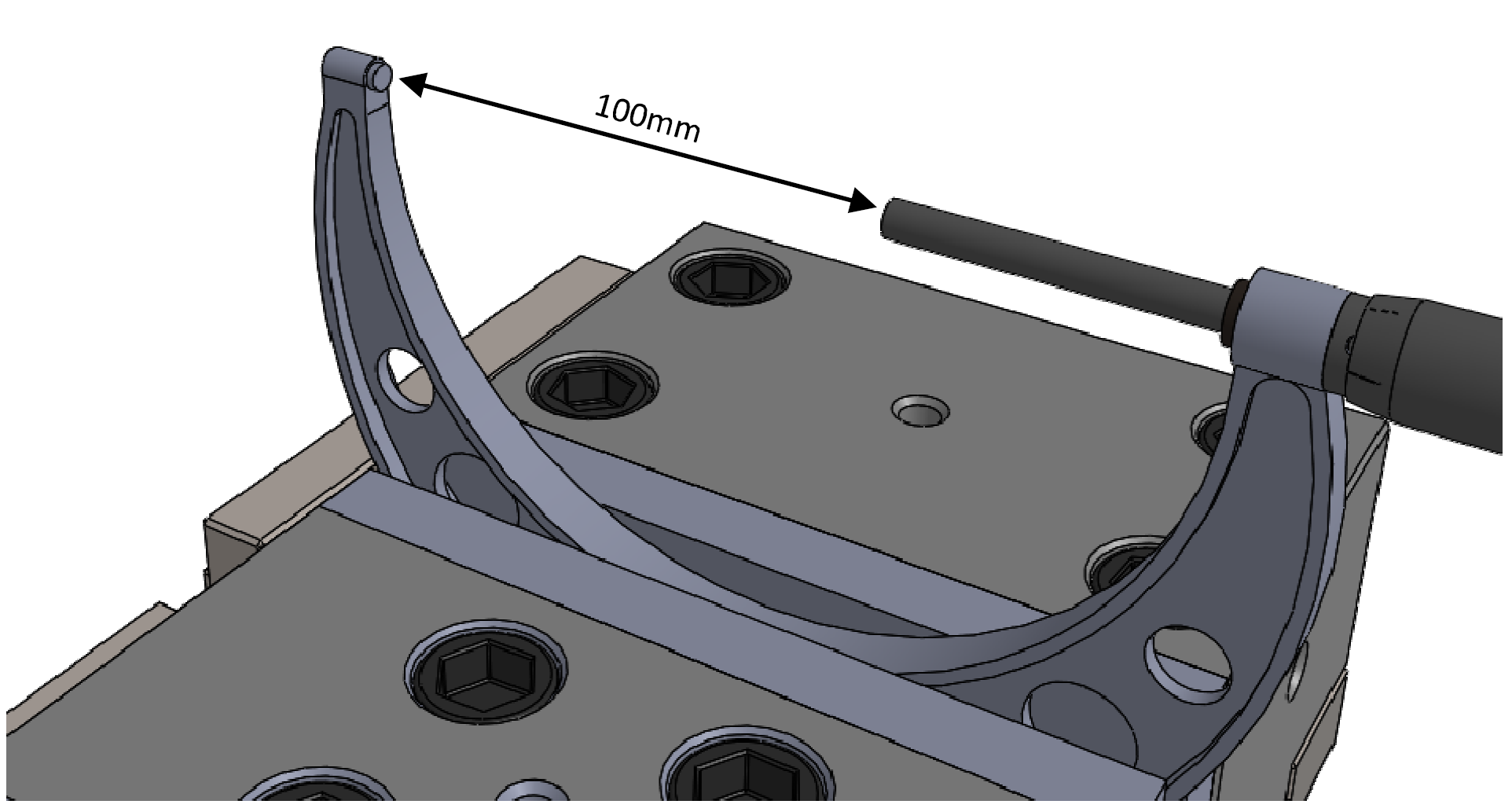
이렇게 마이크로미터 측정 규격 세팅 이 중요 하므로 미리 해당 규격 블록 게이지 을 준비 하여 측정 후 그 지점 을 오리진 하여 100mm 정하거나 아니면 마이크로 미터 을 끝까지 조여 측정면측정면까지 간 후 다시 100mm 다시 나와 100mm 지점에 정지하는 등 여러 가지 방법을 사용 하여 세팅해놓으시기해놓으시기 바랍니다.
그 후 이렇게 세팅된 마이크로미터 을 고정 할 수 있는 장소 (전용 고정대추천)이나 아니면 MC 나 기타 부드러운 고정 재 을 붙이고 바이스바이스에 살짝 고정한 후 실린더 게이지 을 접촉 합니다.
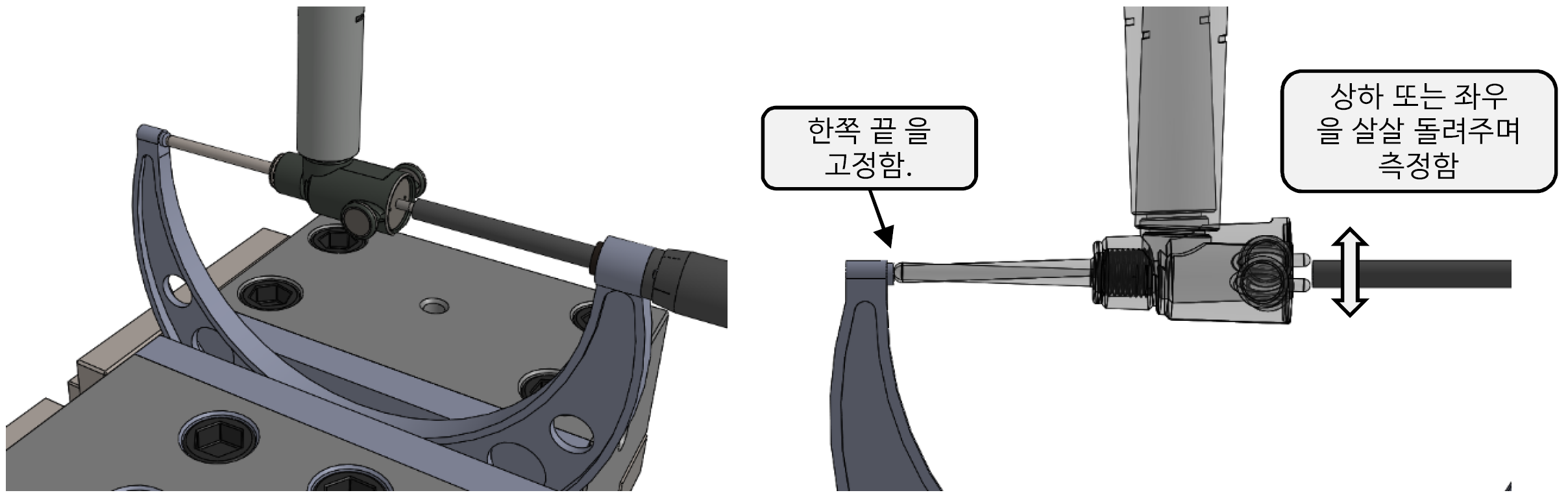
이때 실린더 게이지 눈금을 자세히 살펴보면 눈금 이동의 중간점 을 찾아 살펴보시기 바랍니다.
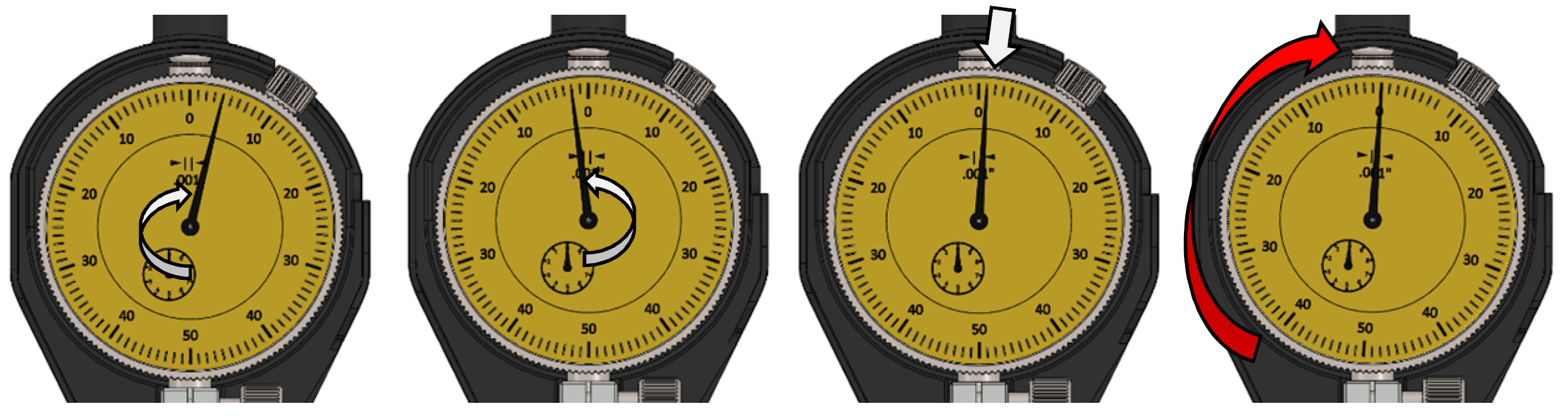
좌우(상하)로 흔들어 최고 점 과 최저 점을 찾아 중간 점 을 다이얼 게이지 눈금 “0” “0”에 맞춥니다.
(마지막 “0” 은 다이얼 게이지 외부 을 돌려 눈금을“0” 으로 돌립니다.)
여기까지 세팅하면 정확히 100mm 일때 게이지 눈금 이 “0” 이 되도록 세팅한 것입니다.
이후 이렇게 세팅된 실린더 게이지 을 활용 하여 보링 작업 이 끝난 홀의 내경을 측정 합니다.

위 그림과 같이 실린더 게이지 을 우선 측정자 가 있는 쪽 (움직이는 곳)을) 먼저 넣고 길이별 엔빌 을 살짝 누르면서 홀 안으로으로 넣어 주시기 바랍니다.
제대로 세팅하여 진입하면 자연스럽게 홀 가운데 쪽으로 이동합니다..
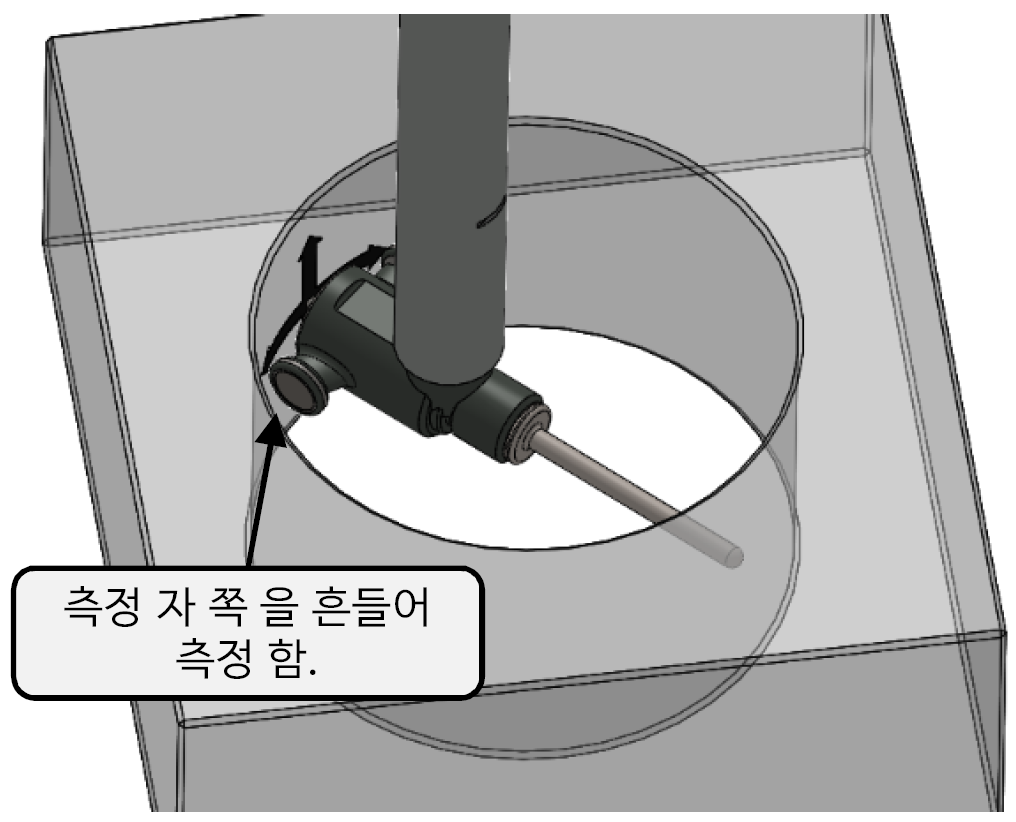
이후 측정자 쪽 을 축으로 삼아 엔빌 쪽을 살짝 흔들어서 역시 다이얼게이지 의 최상점최상점을 찾아 주시면 됩니다
그리고 그때 치수는 게이지 눈금을 그대로 읽으시면 됩니다.
* 이것은 조금만 실제 해보시면 터득 가능하십니다.
이러한 측정 방법으로으로 가공 완료 한 홀의 내경을 확인 한 후 재가공을 작업 하시면 됩니다.
'머시닝 관련 이야기' 카테고리의 다른 글
머시닝 센터 (MCT) 파워 바이스 세팅 방법 -1(웹버전) (2) | 2023.01.29 |
---|---|
머시닝 백 면취(BACK CHAMFER : 모따기) 설정법(웹버전) (2) | 2023.01.05 |
환봉 바이스 에서 사각 각치기 작업시 순서? (0) | 2022.06.08 |
머시닝 센터 (MCT) 백(BACK) 면취 방법 (0) | 2022.05.18 |
머시닝 센터 (MCT) 면판 을 이용한 플레이트 가공 방법-5 (0) | 2022.05.18 |