이번에 는 회전 지그(ROTARY JIG)를 사용하여 대량 가공 하는 것에 대한 방법을 알아보겠습니다..
지그 형식 은 위 같이 한 면에 3개, 4면 12개 순차 가공 방식입니다..
실 가공과 다소 차이 가 있으니 유념하여 개념만 받아 드리시 길 바랍니다.
또한 이러한 것 구축하는 방법 자체 가 많아 여러 가지 을 구현 하느라 다소 복잡합니다..
또한 기계 특성이나 가공물의 성격, CAM 작성법,작성법, 해당 포스트 의 차이 등으로 실 G코드 출력 이
차이 가 있으므로 이렇게 하는구나 정도로 받아 주시기 바랍니다.
1. 지그 제작
우선 해당 가공 물을 고정할 지그를 가공합니다..
소재는 미리 선반 물로 96 ø 길이 285mm 285mm로 후반 30mm 정도 인덱스 연동척연동척에 고정할 부분은 만들어 줍니다.
우선 소재 을 인덱스에 고정한 후 왼쪽 부분을 원점으로으로 하여 세팅 을 해 놓습니다.
소재 원점 은 작업좌표 G54, G56, G57, G58을 사용할 것이므로할것 미리 워크 좌표계에 XYZXYZ 좌표 값 입력하고 AA 축 만 G54=-0˚, G56=-90˚, G57=-180˚, G58=-270˚ 을 입력 해 둡니다.
이후 지그 모델링에서 가공 체인으로 사용할 선을 그리기-커브-커브끝단기능으로 생성하여 투영이동으로 선을.
이후 선을 체인 걸기 쉽게 정리 후 보기 좋게 배치합니다..
우선 위 와 같이 정리 후 지그 모델링 한 면을 기준 잡아 (솔리드면) 작업 평면을 설정하여 줍니다.
여기서 한번 다시 생각하셔야 하셔야 합니다.
이 가공 을 하는 방법 은 여러 가지 가 있습니다. (중간에 생각났습니다.).)
3. 1개 작업 좌표 설정 후 4개 작업 평면 설정 한 후 각각 의 가공 정의 을 작업 평면에 배치하여 가공하는 방법 (각각의 면당 "1,2,3,4차” 가공 등 을 작업 할 수 있음)
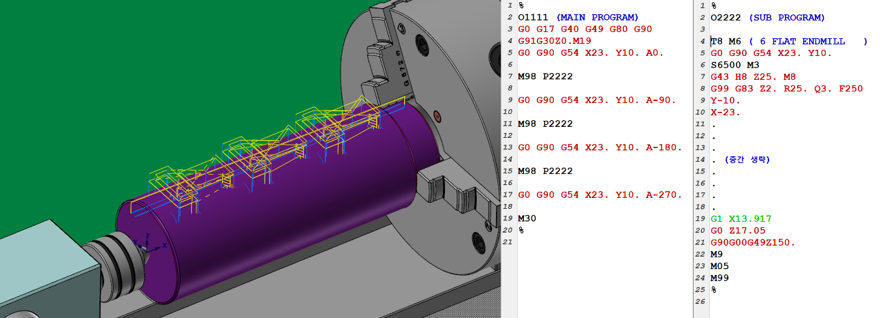
2. 작업 좌표 설정 후 작업 평면 설정 하여 선형 배열로 회전 배열 하기.
위에서 설명한 것 과 동일 하게 우선 소재 인덱스 고정 후 소재 원점 설정 (G54,56,57,58) 합니다.
원점 설정 은 다음과 같이 합니다.
위 그림과 같이 보통 소재 중심점을 원점으로 설정하는데 여기서는 작업 평면을 사용하므로 위 파란 면을 작업 평면 설정 하여 절삭 파라미터 을 지정 합니다.
그러므로 머시닝 작업 좌표 입력 시 G54 G54에 X, Y X, Y는 소재 앞부분 좌표를 사용하고 Z Z는 소재 중심점에서 39 mm 만 큼 올린 높이 을 “0” 으로 설정되도록 입력합니다.
부가축 (A) (A)는 우선 G54 = 0˚, G56=-90˚, G57=-180˚, G58=-270˚입력하였습니다.
위 와 같이 머시닝 작업 좌표에 입력합니다. (좌표 값이나 AA 축 부호는 임의 적인 값입니다.)
그런 다음 CAM 프로그램에서 미리 설정한 작업평면 (G54-WORK) (G54-WORK)을 재료 상단 “0” 으로 하여 가공 설정을 해줍니다..
이후 해당 설정을 기준 하여 모의 가공 을 해줍니다.
모의 가공 결과 문제점 이 없으면 이 을 토대로 회전 선형 배열을 설정해줍니다..
위 같이 첫 번째 선형배열 은 첫 G54 평면 가공 물을 패턴 이동 두 점 간 배열 한 것입니다.
G54 평면 가공물 패턴 이동 용 선형 배열 G56.57.58 용 회전 선형 배열
이후 경로 확인도 하고 심코에서 도 확인 해 봅니다. (심코가 설정 문제 인지 작업평면 (부가축 적용)이 적용 이 안되네요….)
이후 모의 가공 을 해보고 확인합니다.
* 실제 가공 시 에는 조금 다를 수 있습니다.
이 방법 은 특별 한 방법 이 아니고 이 앞에 여러 가공 방식에 쓰인 바로 그 방법입니다.
각 4면에 할당 한 면에 작업 평면을 작성하고 그 평면에 가공 정의 을 하는 방법으로 2번2 방식과 거의 차이 없는 방법입니다. ( 사실 이점 이 없습니다.)
다만 4면 중 1면에 1차 가공 2면에 2차 가공 … 등 작업 을 하시거나 사면이 동일한 하지만 제품 번호 또는 뭐 한 가지 추가한다 듯하던가 하는 경우에 사용하지 않을까 생각합니다.
* 사실 제대로 양산 체제 라면 4면에 1,2,3,4 차 가공을 적절히 분배하여 1회1 가공 시마다 완제품이 나오게 하는 것이 좋다고 생각합니다.
* 의외로 CAM 작업 시간 이 오래 걸리는 경향 이 있으므로 (연산 시간 과는 관계없이)) 잘 판단하여하시기.
2. 지그에 제품 가공 하기.
사실 방법 은 지그 가공과 동일합니다..
똑같이 머시닝 작업 좌표계에 각 면의 원점 입력 하고 소재 고정용 에지클램프 을 설치 합니다.
소재 원점은 지그 평행 이 중요하므로 인디게이트인디게이트 등 여러 가지 방법을 이용하여 각 면의 평행을 확인하시고 에지클램프 (협찬 : 상우정공 엣지 클램프 지지력 1.5t) 1.5t)을 설치합니다.
우선 지그 모델링을 불러드린 후 각각 의 작업 평면을 작성하여 각각 의 작업 평면에 소재 을 배치 합니다.
그리고 소재 을 공작물 모델 (공작물 설정 X) X)에서 지정해 줍니다.
1. 각 소재 위치에 솔리드솔리드로 소재 을 만들어 줍니다.
2. 가공 경로 – 공작물 모델을 선택
3. 공작물 이름 적어주고 초기 공작물 형태에서 모델 선택 후 해당 솔리드 을 선택 해줍니다.
4. 가공 경로 아이콘 부분 의 경로확인/모의가공조건을/ 선택
5. 경로확인/모의가공 조건 의 공작물 모델 의 해당 공작물모델 선택.
소재 가 잘 설정되면 해당 작업 가공물 의 도면 (체인용)을 작성해 주고 이 에 대한 CAM CAM을 작성합니다.니다.
해당 CAM 작업 은 대충 넘어가고 모의 가공까지 하여 가공의 이상 이 없는가 확인합니다..
자 이후 나머지 면 의 가공을 설정하여야 하므로 G54면 의 선형 배열을 다시 선형배열 하면서 작업 좌표만 G56 G56으로 출력합니다.
그런데 위 와 같이 선형 배열한 툴 패스 가 화면상으로는 G56 (-90˚)으로 보여주는 것이 아니라 G54 면에 그대로 출력되어 있습니다. (이 상태에서 G코드 출력 하면 G56 G56으로 출력됩니다.).)
그래서 모의 가공 상이나 뭔가 추구하고 싶은 분 은 다음과 같이 출력하시면 됩니다.
아까 와 똑같이 하시고 선형배열 이동 항목에서 하부 □평면에서 □평면으로으로 을 체크 하고 G54에서 G56으로(평면 전환)
이러한 절차 G54 가공 정의 – G56으로 전환하며 선형 배열(이동) – G56 선형배열을G57으로 전환하며 선형배열(이동) – G57 선형배열을 G58 G58으로 전환하여 선열배열(이동) 하여 마무리합니다.다.
사실 업무상으로 이렇게 하는 것이 별 의미는 없습니다.
나중에 타작업자가 작업 인계 시 좀 시각적이나 설명상 또는 교육적 목적 이외에는 시간 낭비 일수 있습니다.
모의 가공 결과 도 좋게 나왔습니다, 심코심코는 작업 평면 부가 축 미 지원으로 할 수 없습니다.
이렇게 해서 이러한 가공 에는 이런 식으로으로 진행하는구나 하고 참고로 보시고 실 가공 시는 각자 알고 있는 자신 있으신 방법으로으로 활용하여 가공 하시 길 바랍니다.
인덱스 (물론 5축 가공 은 더욱) 가공 은 사전 소재 설정이나 공구 충돌 같은 것은 충분히 검토하여 작업하셔야 하며 조품 작업 시는 실 가공 경로가 본인 이 설정한 데로 잘 움직이는 가 확인 하고 하셔야 만 합니다.
필히 모의 가공 경로 확인 통해서 하셔야 하며 포스트 지원 여부에 따라 실 G코드 출력이 많이 달라지니 G 코드 출력 후 심코 같은 툴 패스 체크용 프로그램을 통하여 확인하시기 바랍니다.
'마스터캠 관련 한 여러 이야기 > 마스터캠 을 활용한 인덱스 (부가축) 가공 캠 방법 에 관하여' 카테고리의 다른 글
인덱스(4축) 설치 후 CAM(가공경로) 음료수병 블로우 금형 형태에 관하여 (웹버전) (0) | 2023.03.01 |
---|---|
인덱스(4축) 설치 후 CAM(가공경로) 스크류형태 모프가공경로에 관하여 (웹버전) (0) | 2023.02.12 |
인덱스(4축) 설치 후 CAM(가공경로) 형상가공 (4면)형태 가공 에 관하여 (웹버전) (0) | 2023.01.21 |
인덱스(4축) 설치 후 CAM(가공경로) 생성된 곡면 형태 가공 에 관하여 (웹버전) (1) | 2023.01.21 |
인덱스(4축) 설치 후 CAM(가공경로) 생성 방식 생성된 체인(커브) & 바닥 곡면 형태 가공 에 관하여 (웹버전) (2) | 2023.01.20 |