자 이번에는 드릴 사이클 과정 (G73 , G83)에서 대하여 알아보겠습니다.
신규 장비 을 안착하고 나서 처음 드릴링 가공을 시작합니다.
*예제로(이해를 돕기 위하여)
칩 브레이크(G73) 작업 중 팩(PEEK) 값을 5.0mm 입력(마스터캠상) 하고 가공을 시작하였는데 깊이 5.0mm 가공 후 순간 살짝 움찔하고는 다음 가공 깊이로 들어갑니다.
처음 의도하는 바는 5.0mm 가공하고 1.0mm 도피하고 다시 다음 가공 깊이 까지 진행하길 원하었는데 신규 장비 라 그런지 드릴링 (G73)이 생각대로 되질 않습니다.
먼저 칩 브레이크 (G73) 고정 사이클에 대하여 알아보겠습니다.
고속 심고 드릴 사이클 (칩 브레이크/깊은 홀 가공용) 등으로 불려지며 간헐적 팩 작동으로 가공 시간 단축에 유리 한 드릴 사이클입니다.
* 다만 절삭유 공급(드릴 끝단까지 공급) 이 중요하며 주로 주축 절삭유 공급 이 가능 한 장비와 주축 절삭유 지원 공구 사용 시 유리합니다.
* 일반 형태(하이스 재질) 드릴 경우 가공 깊이 5D 이상(공구경 대비 5배) 경우 칩배출의 문제가 되는 드릴 끝단 위치 칩 배출이 안 되는 문제 가 있으므로 주의 바랍니다.
G코드 적용 은 다음과 같습니다.

* X, Y 값은 드릴 가공 위치 값 , Z값은 드릴 가공 깊이 값
Q값은 팩(도피) 하는 간격 깊이 값(증분)
R값은 팩(도피) 작업 시 최종 후퇴하는 복귀 지점 높이 값 (G99 경우 최종 적용)
F값은 드릴 가공 피드 값
그럼 드릴 사이클 이 작동하는 동작을 알아보겠습니다.
예: G73 G90 G98 Z-50.0 R4.0 Q5.0을 지령합니다.
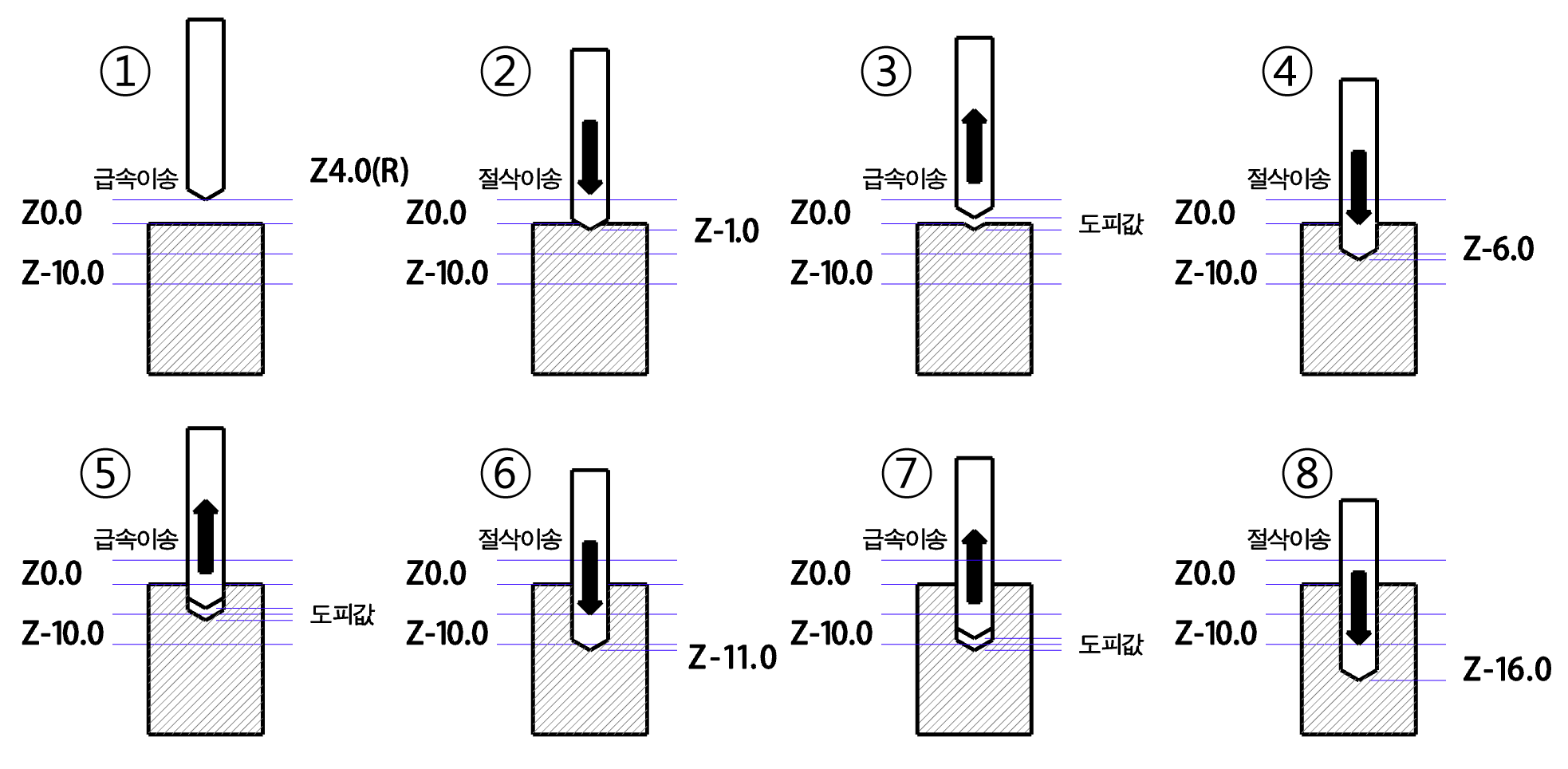
위의 이미지 을 참고하면. ① R값 지점(Z4.0)까지 급속 이송
② Z-1.0까지 절삭 이송 (Q값 (5.0) 적용)(+4.0 - 5.0(Q) = -1.0)
③ 도피 값만큼 급속 이송으로 도피
④ Z-6.0까지 절삭 이송 (Q값 (5.0) 적용)
⑤ 도피 값만큼 급속 이송으로 도피
⑥ Z-11.0까지 절삭 이송 (Q값 (5.0) 적용)
⑦ 도피 값만큼 급속 이송으로 도피
⑧ Z-16.0까지 절삭 이송 (Q값 (5.0) 적용)
이러한 형식으로 G73 칩 브레이크 드릴 가공이 이루어지는데 신규 장비 을 써보니 칩 브레이크 가공 시 Q값 위치마다 살짝 움찍 하더니 그냥 G81처럼 가공합니다. 이것은 마스터캠 드릴 가공 파라미터 에서 설정할 수 없고 , G73 칩 브레이크 도피량 은 머시닝 자체 설정 파라미터에서 지정하게 되어 있습니다.
* 보통의 경우 이 파라미터는 0.1mm로 입력되어 있습니다. 이것을 재설정해 보이겠습니다.
우선 장비 매뉴얼을 찾아보았습니다.
G73 고정드릴 사이클 관련 파라미터는 5114번입니다.
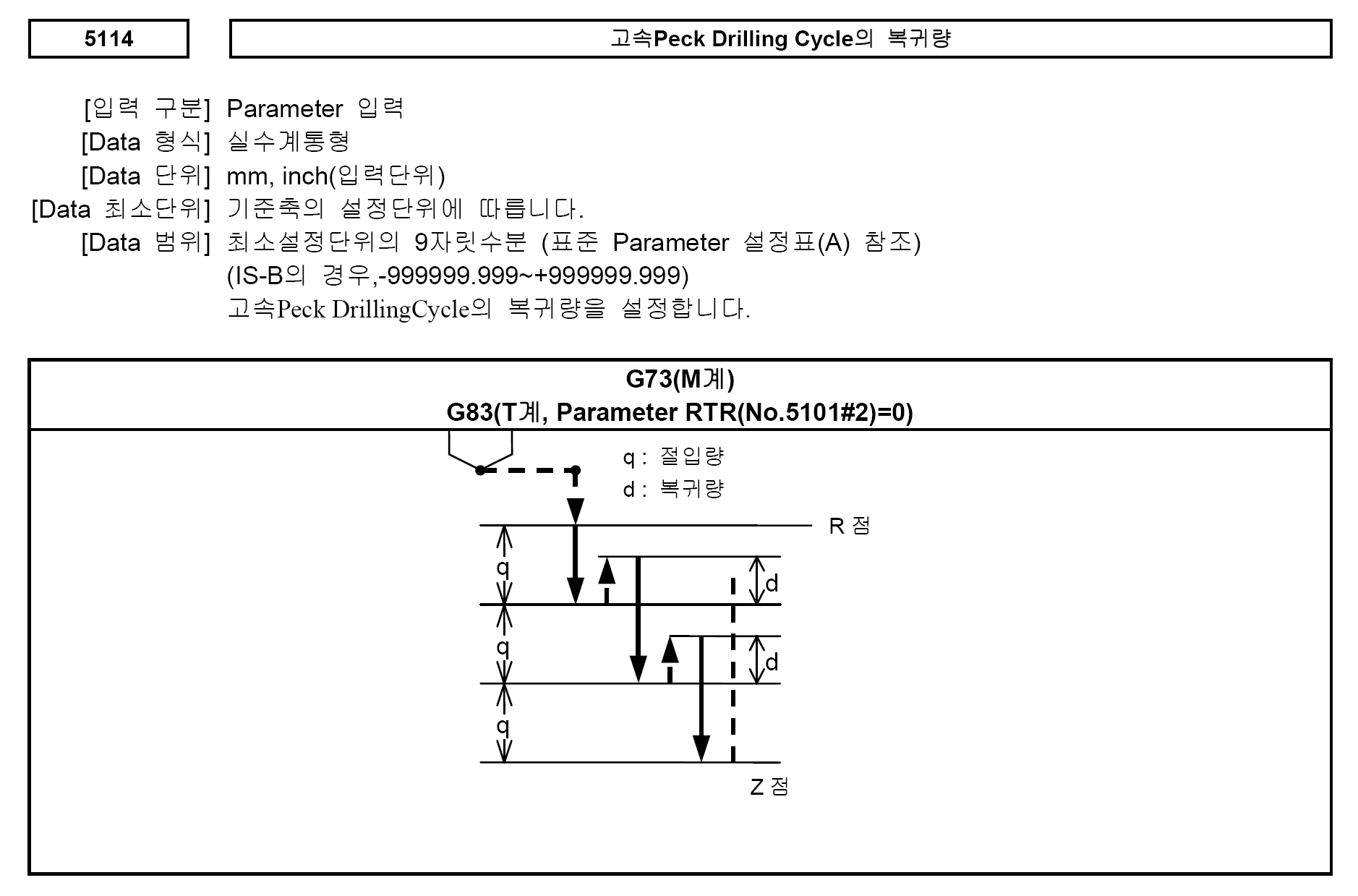
즉 위 도표의 도피 값 (d)을 입력해주는 것입니다.
이제 조작반의 설정으로 들어갑니다.
먼저 조작반의 MDI 상태에서 OFS/SET 버턴을 눌러 설정 화면으로 들어갑니다.
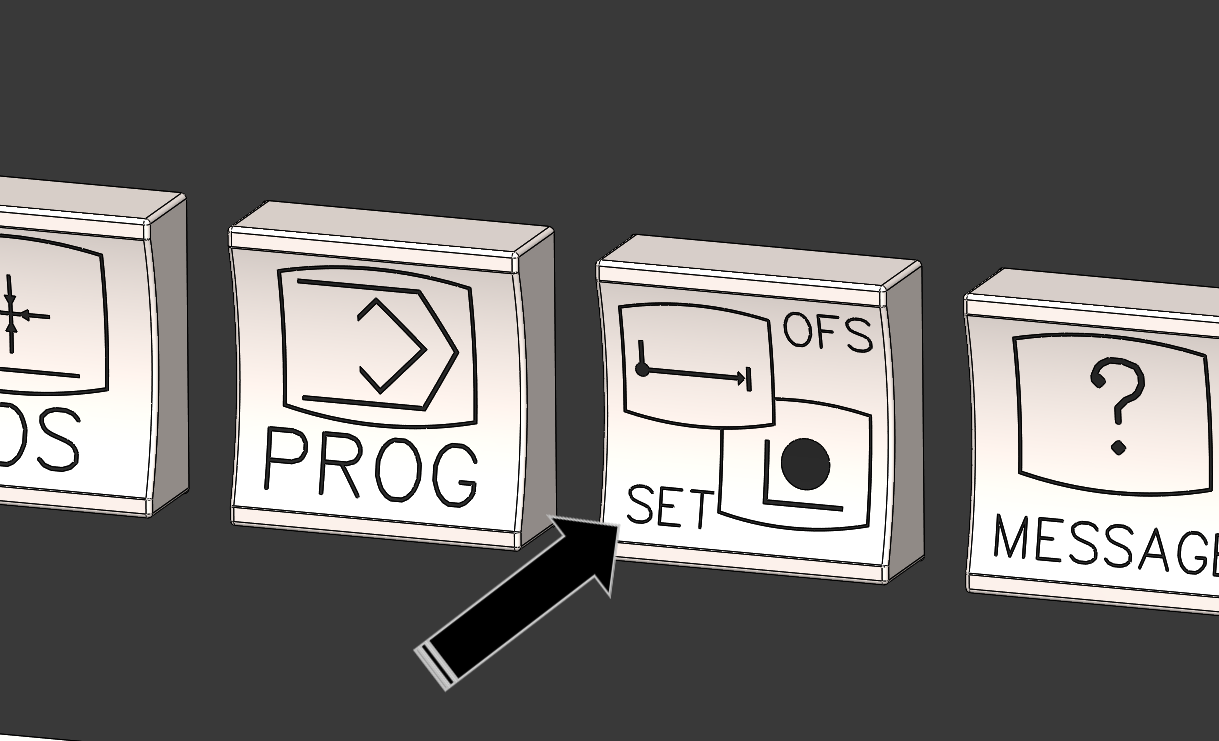
그리고 설정 소프트 키 을 눌러 설정 화면으로 들어갑니다.
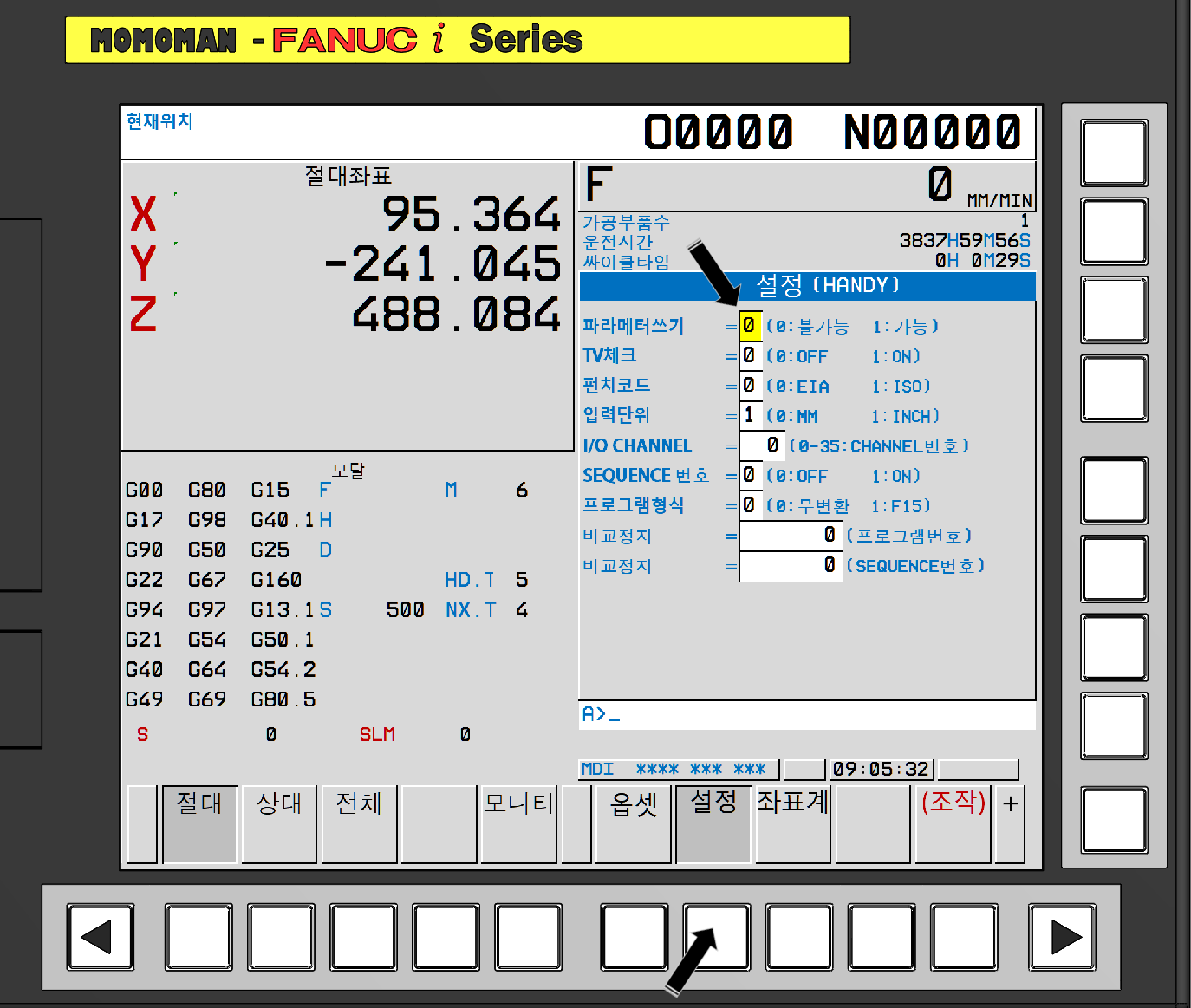
그리고 파라미터 쓰기 입력 칸 에 "0"으로 되어 있는 것 을 "1"로 입력합니다.
(키보드 "1" 누르고 입력 소프트 키 누름) or (하단부 "ON : 1" 소프트 키 누름)
* 파라미터 쓰기 입력 칸 값을 변경 하면 장비에서 알람 발생 하지만 현재로는 무시하셔도 됩니다.
다시 파라미터 쓰기 값 을 "0"으로 변경하고 리셋(RESET) 키 을 눌러 해제 가능합니다.

이후 조작반의 SYSTEM 버턴을 눌러 파라미터 설정 화면으로 들어갑니다.
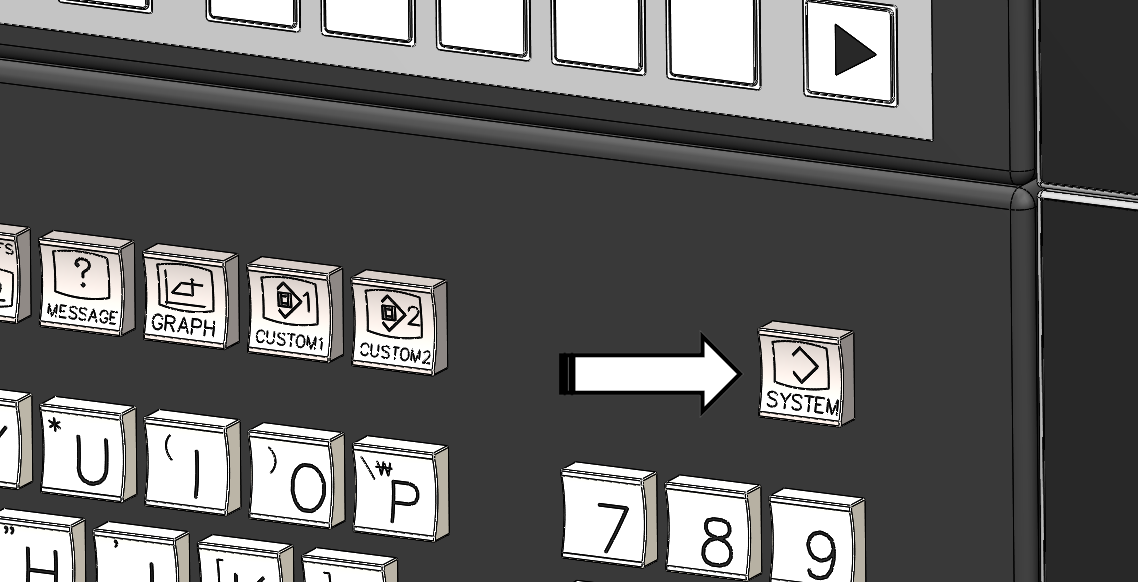
이후 5114번 대 파라미터 설정 화면을 찾아갑니다.
방법 은 조작반 키보드의 상하 화살표 또는 페이지 업다운 버턴을 눌러 해당 번호 파라미터로 가거나 해당 파라미터 번호 을 입력 후 "NO검색" 소프트 키 을 눌러 해당 번호 파라미터 설정 화면으로 갑니다.
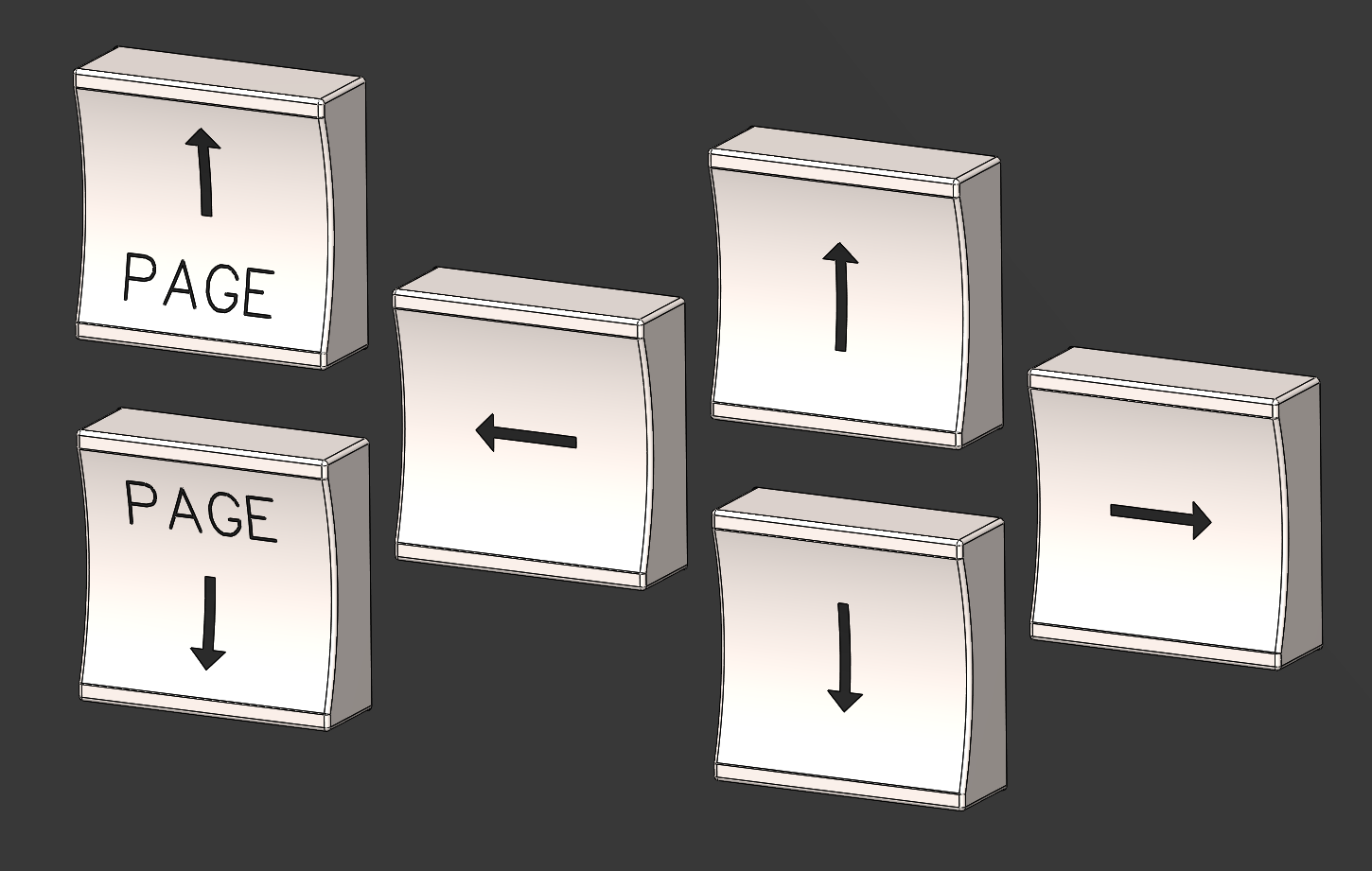
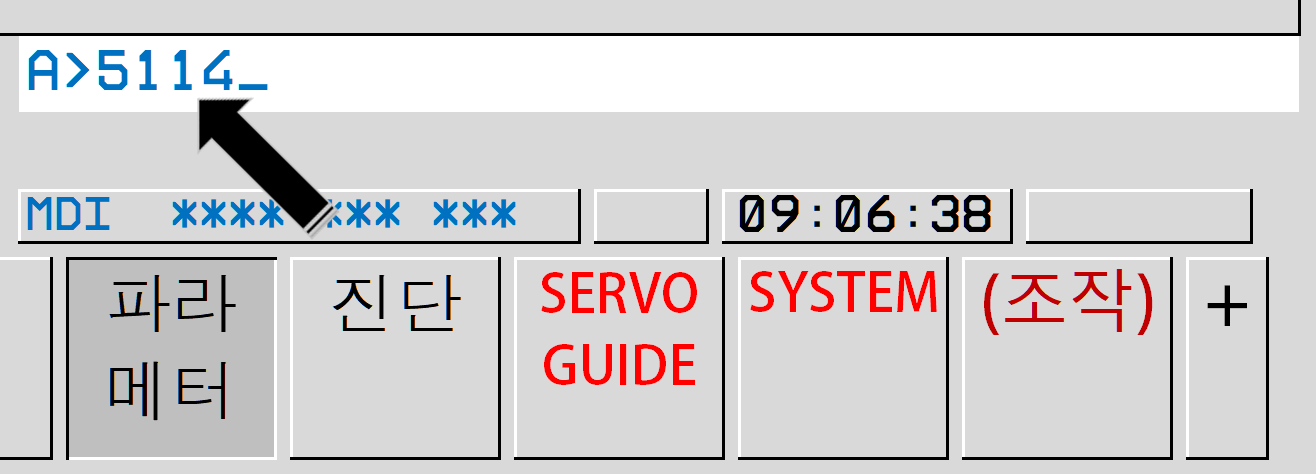
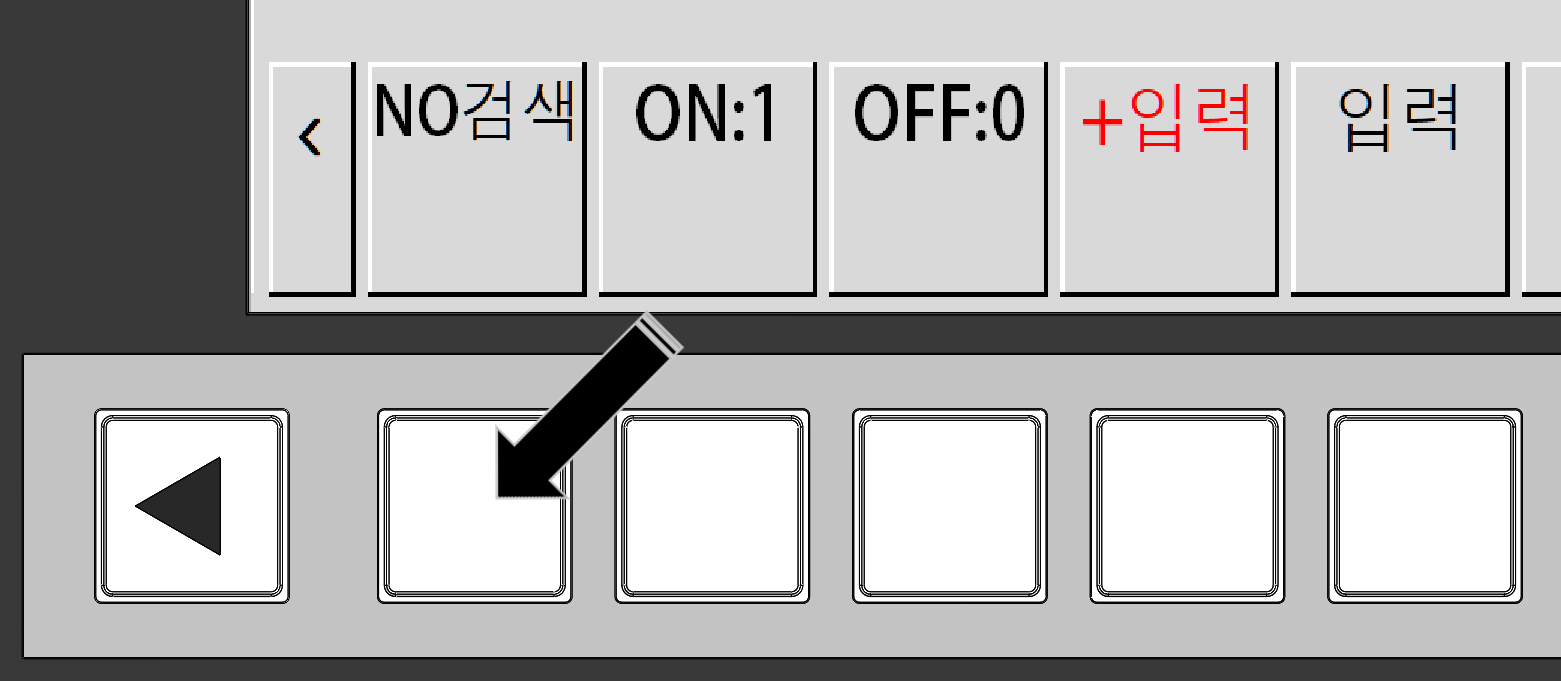
그럼 해당 5114 파라미터 설정 화면으로 왔습니다.
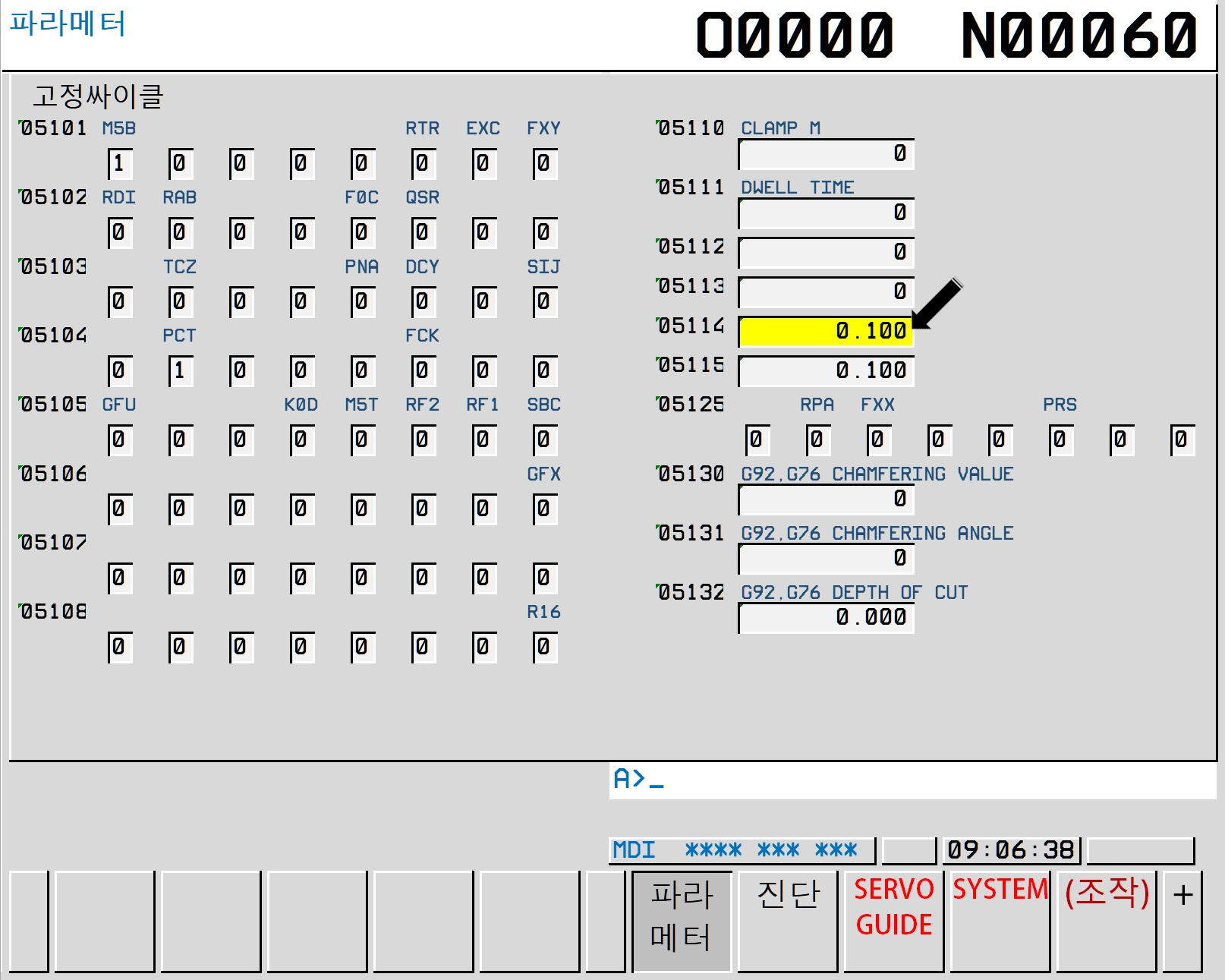
위 화면처럼 해당 5114번 파라미터에 (기본값 :"0.1mm) 각자 사용자 작업 환경에 맞는 도피 값을 넣어 주시면 됩니다.
그리고 다시 역순으로 파라미터 쓰기 칸으로 돌아와서 파라미터 쓰기를 "0"을 입력한 후 알람 해제 을 위하여 리셋(RESET) 키 을 눌러 주시면 됩니다.
그러면 다음 가공(G73 드릴 사이클) 작업 시 Q값에 위하여 가공 후 위에 입력한 값만큼 급속 이송으로 도피 후 다시 다음 Q값까지 드릴 가공 이 이루어집니다.
* 가공 시간 단축을 위하여 작은 값을 넣어야 하지만 간혹 가공 깊이 가 깊은 경우 드릴 끝단의 칩이 배출 이 잘 안 되는 경우 입력 값을 조금 키워주면 칩 배출 시간을 벌어 (물론 절삭유 공급 이 더 중요합니다.) 가공에 도움 이 됩니다.
이번에는 G83 팩 드릴 사이클의 장비 파라미터 값을 알아보겠습니다.
자 이제 칩브레이크 드릴 가공을 마치고 이번에는 팩 드릴 (G83) 드릴 가공을 시작해 봅니다.
*예제로(이해를 돕기 위하여)
마스터캠 에서 팩 드릴 가공을 선택한 후 Q값을 5.0mm 주고 NC 코드 을 출력해 보았습니다.
그리고 실가공에 들어가면 또 뭔가 의아감 이 있어 보입니다.
즉 절삭 이송 으로 가공 깊이 까지 절삭 후 다시 리턴 지점(R점)까지 도피하여 다시 급속 이송으로 다음 가공 깊이 (Q값에 의하여) 내려가는 데 왠지 드릴 이 꾹 드리 박는 듯한 느낌의 가공이 진행되는 느낌입니다.
(드릴 끝단 이 바로 급속 으로 찍는 듯한 느낌) (그래서 드릴 끝단 마모 가 심한 경우 스틸 소재 시)
드릴 사이클 상으로는 이상 없는 움직임이지만 뭔가 개선이 필요해 보입니다.
G코드 적용 은 다음과 같습니다.

* X, Y 값은 드릴 가공 위치 값 , Z값은 드릴 가공 깊이 값
Q값은 리턴점(R점)에서 증분 되는 가공 단계 별 깊이 값(증분)
R값은 리턴점(R점)에서 다음 가공 시작 깊이 (Q값 시작점 , 전 가공 깊이)에 도착 전 급속 이송에서 절삭 이송으로 전 환하는 길이 의 값 (가공 시작 위치 전 절삭 이송 으로 전환하는 위치 값)
F값은 드릴 가공 피드 값
그럼 드릴 사이클 이 작동하는 동작을 알아보겠습니다.
예: G83 G90 G98 Z-50.0 R4.0 Q5.0을 지령합니다.
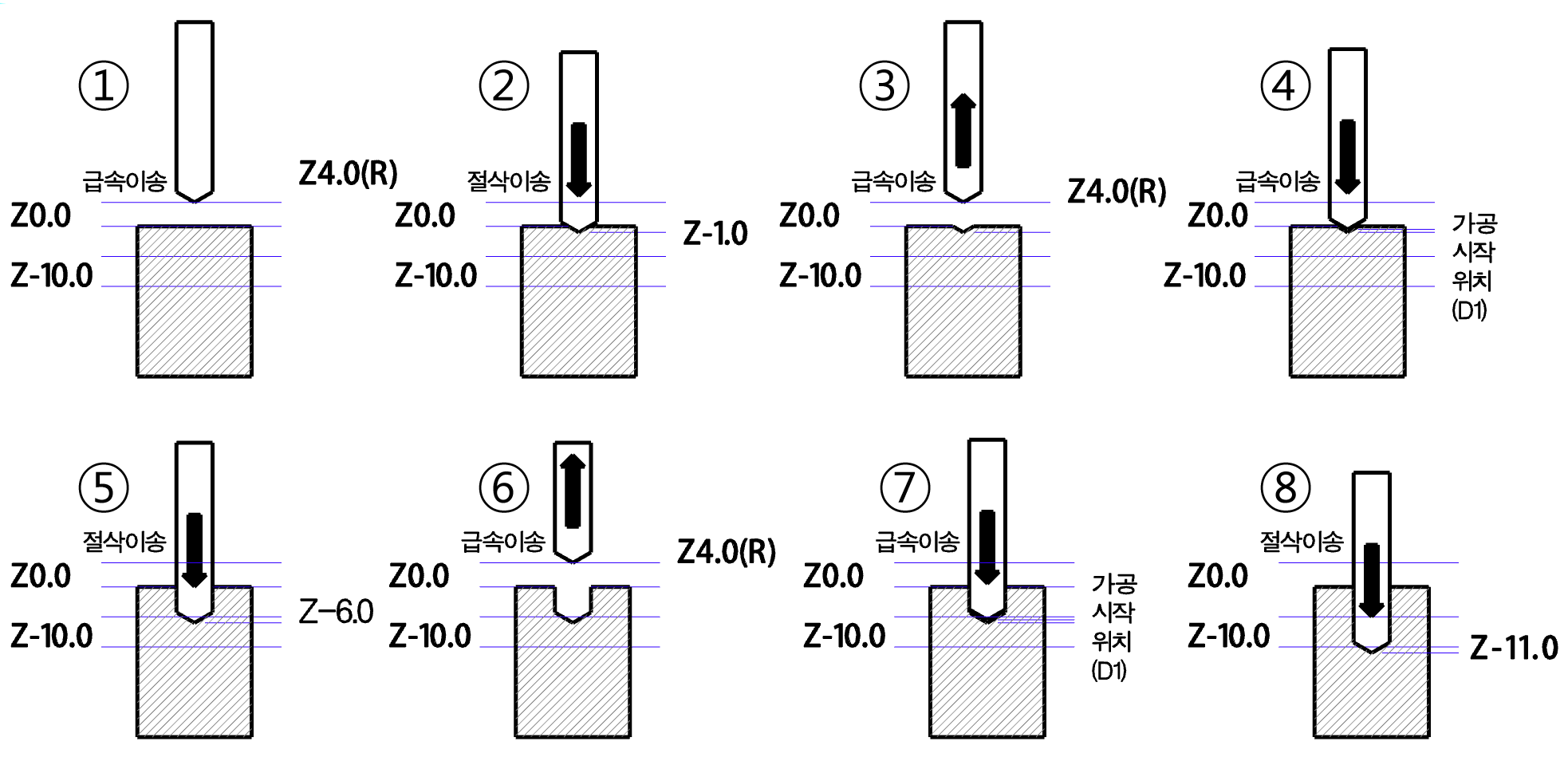
위의 이미지 을 참고하면.
① R값 지점(Z4.0)까지 급속 이송
② Z-1.0까지 절삭 이송 (Q값 (5.0) 적용)(+4.0 - 5.0(Q) = -1.0)
③ 리턴점(R점:Z+4.0)까지 급속 이송으로 도피
④ (Z-1.0 - 가공 시작 위치(D1)) 까지 급속 이송 (만일 가공시작 위치 (D1값: 장비 파라미터 값) 이 0.1mm 이면 Z +0.9mm)
⑤ Z-0.9에서 Z-6.0까지 절삭 이송(Q값 적용)
⑥ 리턴점(R점:Z+4.0)까지 급속 이송으로 도피
⑦ (Z-6.0 - 가공 시작 위치(D1)) 까지 급속 이송 (만일 가공시작 위치 (D1값: 장비 파라미터 값) 이 0.1mm 이면 Z +5.9mm)
⑧ Z-5.9에서 Z-11.0까지 절삭 이송(Q값 적용)
여기서 중요시 볼 것이 한번 절삭 이송 이후 리턴점(R점)까지 급속 이송한 후 다시 급속 이송으로 다음 가공 지점 까지 급속이송 으로 왔다가 가공 위치 에서 절삭 이송 으로 전환되는데 바로 급속이송 에서 절삭이송 으로 가공 전환 시 공구 파손 의 우려가 있어 가공 시작 직전 약간 의 여유값 을 두고 급속 이송 에서 절삭 이송 으로 전환 되는 길이 값이 (D1) 장비 파라미터에서 설정해주어야 하는 값입니다.
그러므로 만일 드릴 작업 시 드릴 끝단이 자주 파손되는 형태 이시면 이 D1값을 한번 조절하여 칩배출할 시간을 좀 더 주며 급격한 공구와 소재의 충돌을 피할 수 있습니다.
* 다만 이 값을 너무 크게 하시면 가공 시간 이 늘어날 가능성이 당연히 있으나 큰 변화는 없으니 한번 살펴보시기 바랍니다.
이것은 마스터캠 드릴 가공 파리 미터에서 설정할 수 없고 , G78 팩 틈새 값 은 머시닝 자체 설정 파라미터에서 지정하게 되어 있습니다.
* 보통의 경우 이 파라미터는 0.1mm로 입력되어 있습니다.
이것을 재설정해 보이겠습니다.
우선 장비 매뉴얼을 찾아보았습니다.
G83 고정드릴 사이클 관련 파라미터는 5115번입니다.
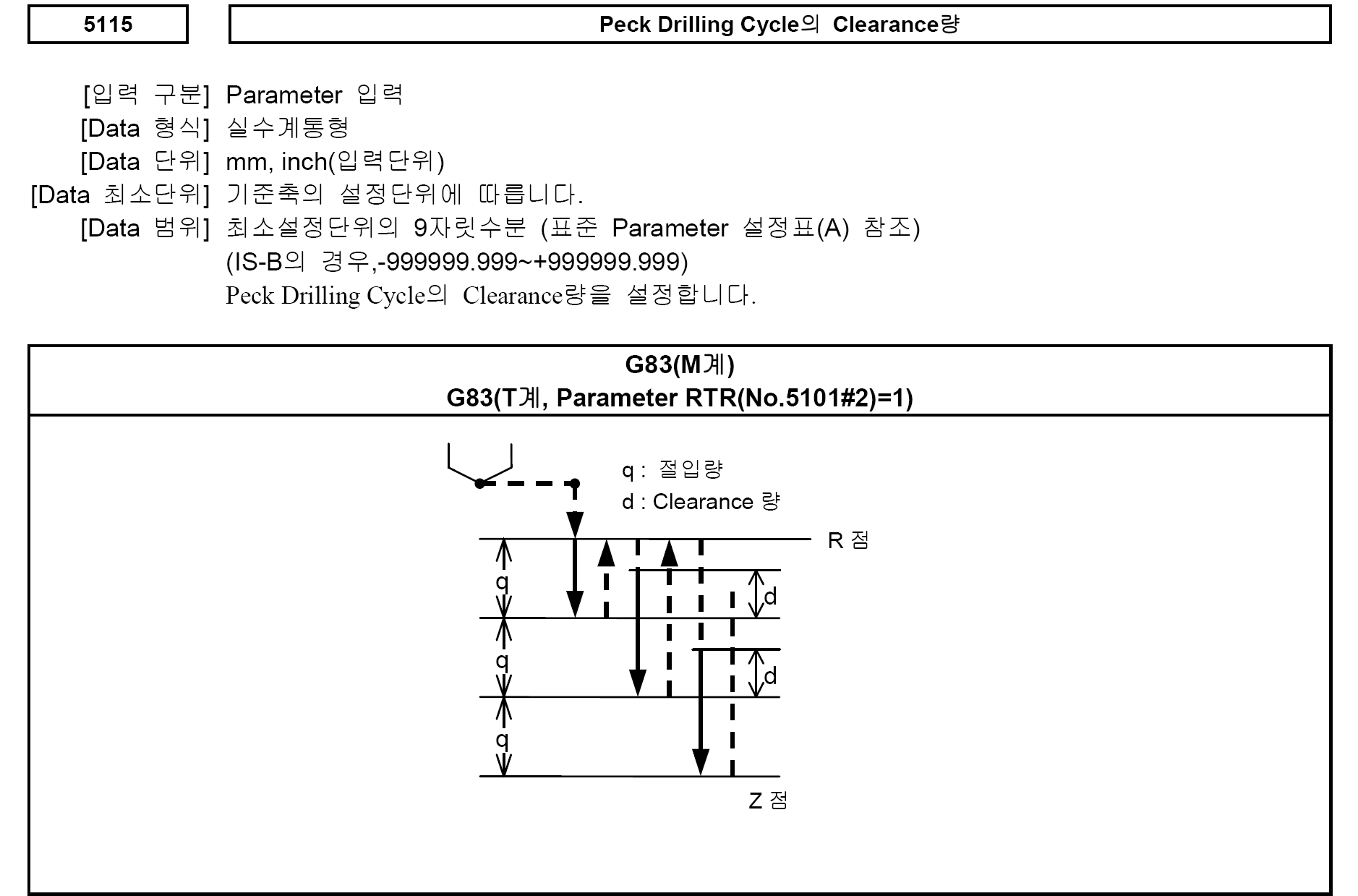
즉 위 도표의 틈새 값 (d)을 입력해주는 것입니다.
이제 조작반의 설정으로 들어갑니다.
먼저 조작반의 MDI 상태에서 OFS/SET 버턴을 눌러 설정 화면으로 들어갑니다.
이후 파라미터 설정 화면으로 들어가는 것은 전과 동일 하니 바로 파라미터 설정으로 들어갑니다.

위 와 같이 5115번대 파라미터 값이 G83 드릴 사이클 적용 시 절삭 이송 시작 위치 틈새 값입니다.
이 값을 조절하셔서 팩 드릴 가공 시 바로 급속 이송으로 이송된 드릴 이 바로 소재와 접촉하는 것 을 방지함과 동시에 절삭유 유입(드릴 끝단에) 시간을 벌기 위한 값입니다.
적당한 값을 입력하시고 다시 같은 요령으로 파라미터 설정 화면으로 돌아와서 파라미터 쓰기 비활성 화 하신 후 작업하시면 됩니다.
* 단 다른 드릴(T-DRILL , U-DRILL 등) 사용 시 적용 여부 을 생각하셔야 하며 만일 주축 절삭유 공급 환경 이시면 다소 값을 작게 잡으셔도 무방 합니다.
그럼 이번 에는 G84 탭 가공 사이클에 대하여 알아보겠습니다.
*예제로(이해를 돕기 위하여)
이번에는 탭 가공을 진행합니다.
가만히 탭 움직이는 것 을 살펴보니 사실 가공에는 아무런 문제 가 없는데 탭이 Q값만큼 가공 후 다시 리턴점(R점)까지 후퇴 후 다시 다음 가공 깊이 까지 가공하고 다시 리턴점(R점)까지 후퇴 후 다시 들어가고 을 반복합니다.
Q값이 작은 경우 자주 왕복을 하여 또 왠지 시간 낭비 요소 같아 보입니다.
그래서 이것도 마치 G84 + G73처럼 Q값만큼 가공 후 잠시 조금만 후퇴하고 다시 가공하면 안 되나 생각합니다.
G코드 적용 은 다음과 같습니다.
* X, Y 값은 드릴 가공 위치 값 , Z값은 드릴 가공 깊이 값
Q값은 리턴점(R점)에서 증분 되는 가공 단계 별 깊이 값(증분)
R값은 팩(도피) 작업 시 최종 후퇴하는 복귀 지점 높이 값 (G99 경우 최종 적용)
F값은 드릴 가공 피드 값
그럼 드릴 사이클 이 작동하는 동작을 알아보겠습니다.
예: G84 G90 G98 Z-8.0 R4.0 Q6.0을 지령합니다.
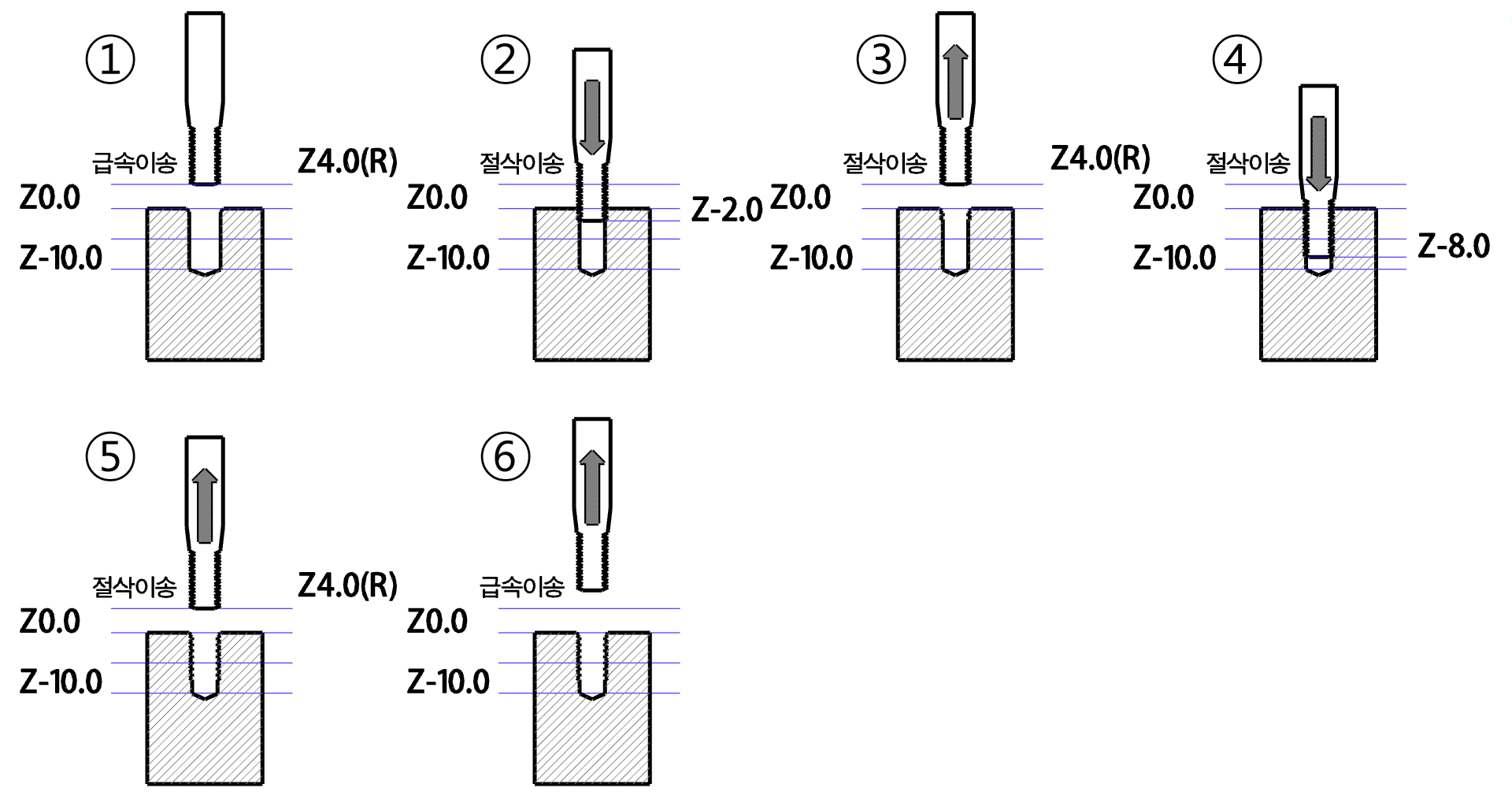
위의 이미지 을 참고하면.
① R값 지점(Z4.0)까지 급속 이송
② Z-2.0까지 절삭 이송 (Q값 (6.0) 적용)(+4.0 - 6.0(Q) = -2.0)
③ 리턴점(R점:Z+4.0)까지 절삭 이송으로 도피
④ Z-8.0까지 절삭 이송 (Q값 (6.0) 적용)
⑤ 리턴점(R점:Z+4.0) 까지 절삭 이송으로 도피
⑥ 급속 이송으로 안전 높이 까지 도피
위 와 같이 한번 Q값만큼 절삭 이송 하면 다시 리턴점(R점) 까지 절삭 이송 한 후 다시 절삭 이송 으로 Q값 만큼 절삭 이송을 반복하게 됩니다.
이것을 마치 G73처럼 전환할 수 있는지 장비 매뉴얼을 살펴봅니다.
매뉴얼 에는 5200번대 파라미터 을 수정하라고 되어 있습니다.
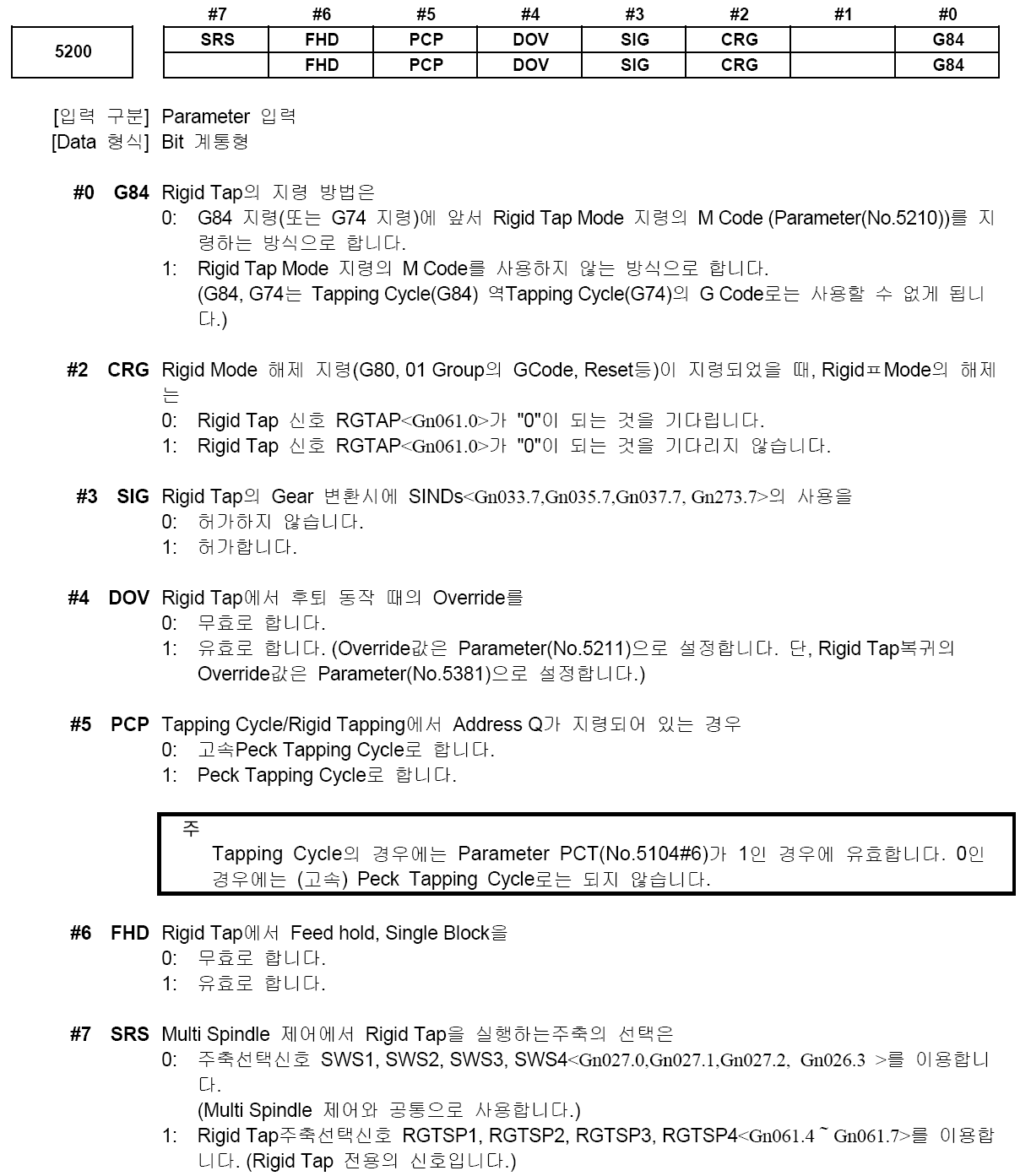
위 파라미터처럼 5200 번대 5번 입력 칸 (#5 PCP)을 설정하라고 되어 있습니다.
즉 #5 PCP 값이 "1"인 경우 가공 후 (Q값 지정 시) 리턴점(R점)까지 후퇴 후 다음 가공 깊이 까지 절삭 이송되고 (PEEK TAPPING CYCLE) "0"인 경우 고속 PEEK TAPPING CYCLE로 (G73) 전환됩니다.
그럼 파라미터 설정으로 들어갑니다.
* 이동 절차는 전부 동일하므로 생략합니다.
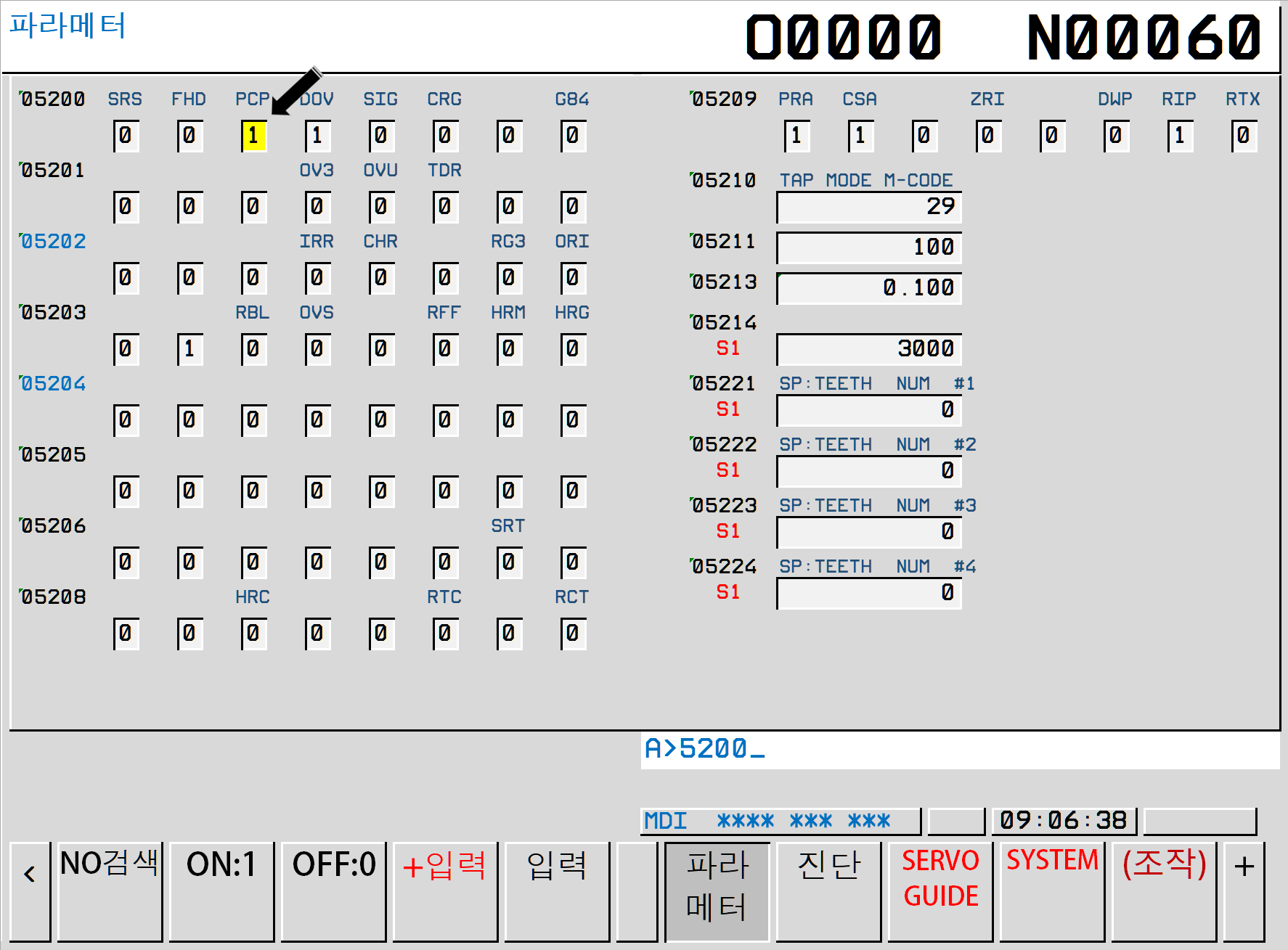
위 와 같이 보통의 경우 5200 #5 PCP 값이 "1"로 되어 있습니다.
이을 고속 PEEK TAPPING CYCLE로 전환하기 위하여 "0"으로 수정합니다.

이후 다시 같은 탭 가공 사이클을 작동시켜 봅니다.
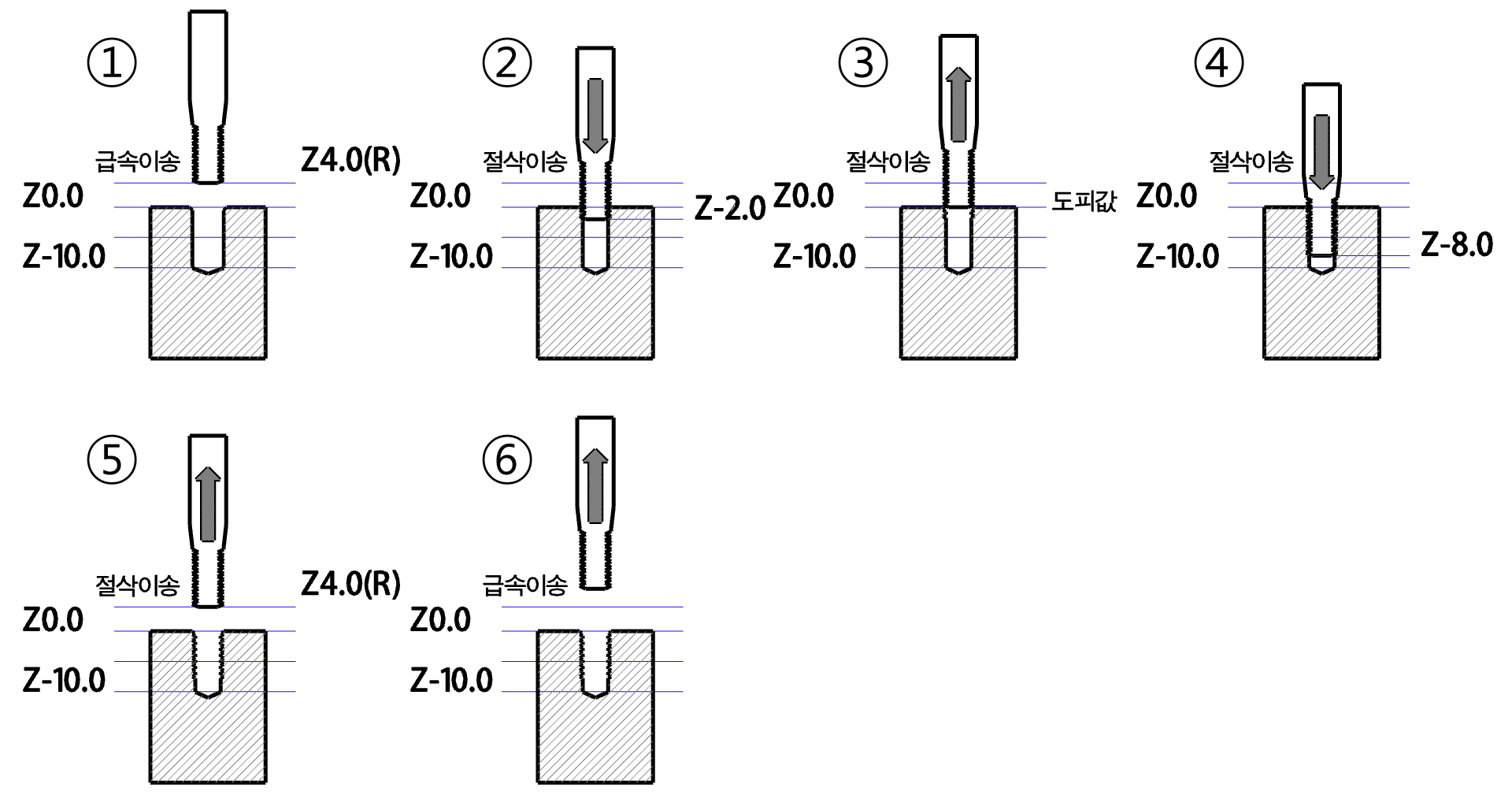
위의 이미지 을 참고하면.
① R값 지점(Z4.0)까지 급속 이송
② Z-2.0까지 절삭 이송 (Q값 (6.0) 적용)(+4.0 - 6.0(Q) = -2.0)
③ 지정된 값만큼절삭 이송으로 도피 (5213 값)
④ Z-8.0까지 절삭 이송 (Q값 (6.0) 적용)
⑤ 리턴점(R점:Z+4.0) 까지 절삭 이송으로 도피
⑥ 급속 이송으로 안전 높이 까지 도피
처음과 달리 이번에는 Q값까지 절삭이송 후 도피값(여기서는 2.0mm) 만큼 절삭 이송한 후 다시 다음 Q값 까지 절삭 이송을 하는 것 을 반복합니다.
그러면 여기서 다시 드는 의문이 그럼 도피 값을 어디서 정하나요 하는 의문 이 생깁니다.
다시 장비 매뉴얼을 살펴보니 파라미터 5213 값이 고속 PEEK TAPPING CYCLE 적용시 도피 값 으로 적용 된다는 것을 알수 있습니다.
그래서 이것도 살펴봅니다.
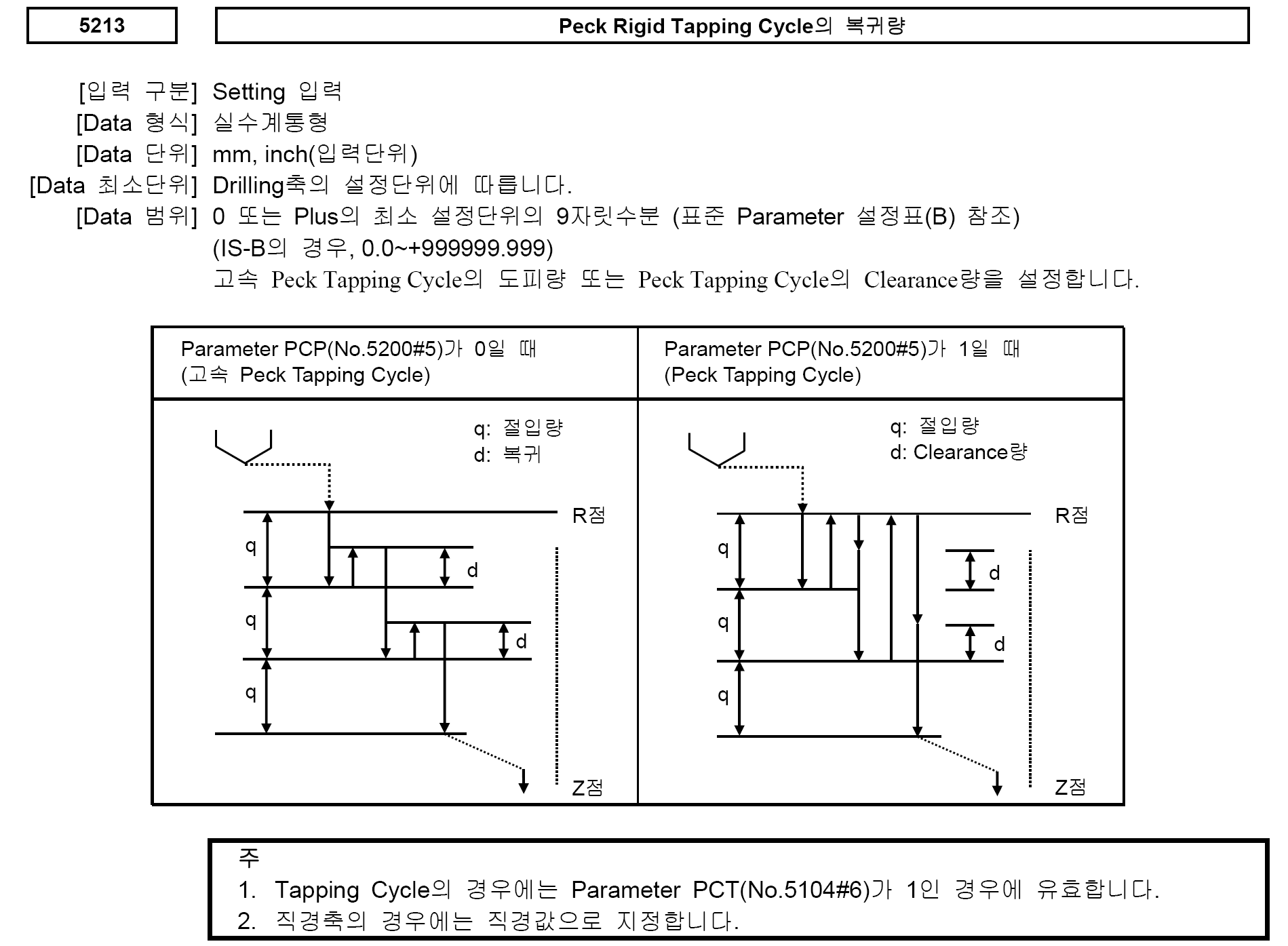
위 와 같이 고속PEEK TAPPING CYCLE 시만 적용됩니다.
그래서 다시 파라미터 설정 화면으로 들어갑니다. 중간 생략... 중간 생략...
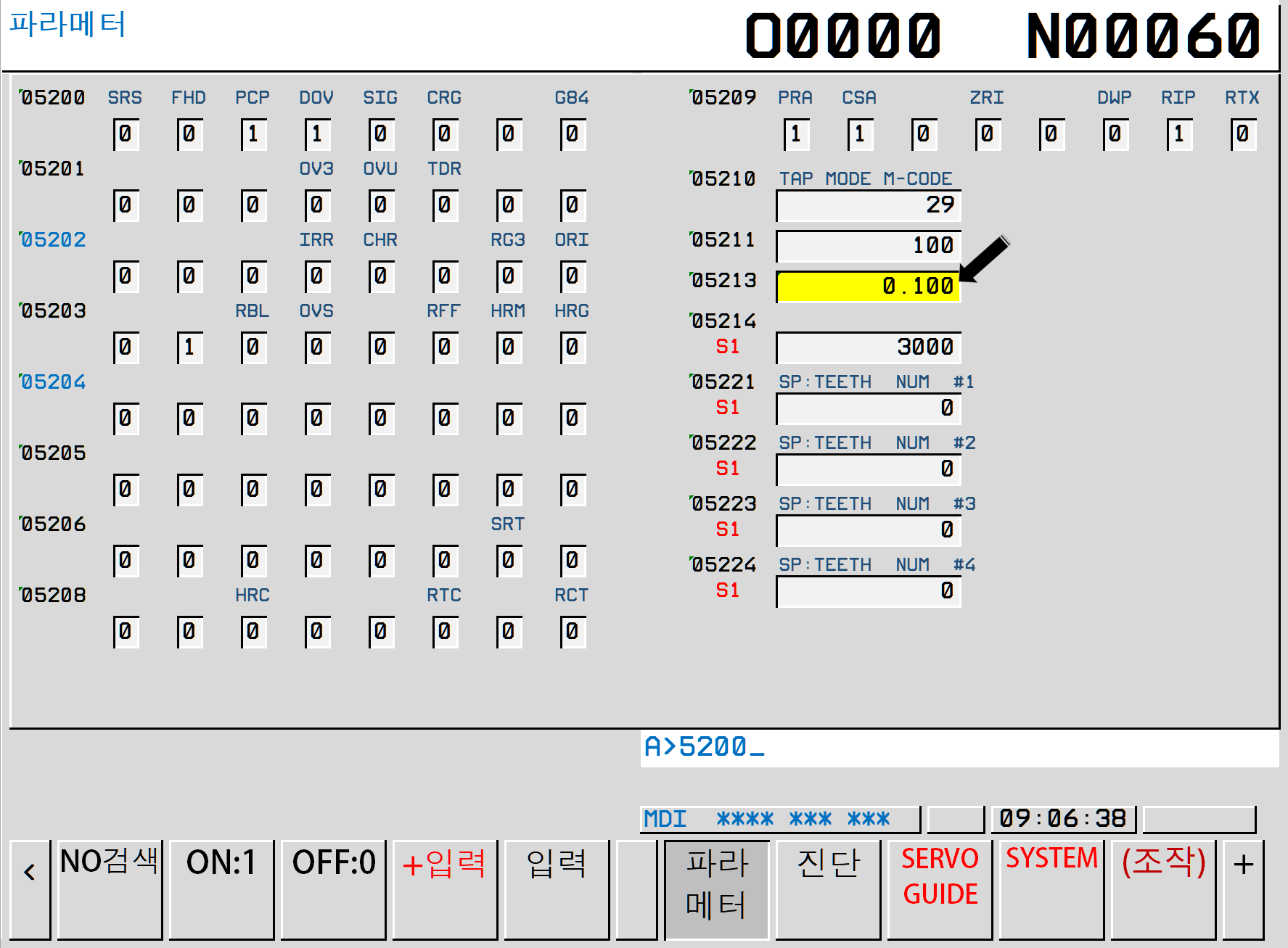
처음 값은 0.1mm로 되어 있어 너무 작은 것이 아닌가 하는 감 은 있습니다.
(이것은 작업자의 작업 환경에 따라 조절하여야 합니다.)
이 5213 입력 칸 에 작업자 가 원하는 도피량만큼 의 값을 입력하시면 됩니다.
* 이것 외도 몇 가지 더 탭 가공 관련 파라미터 가 있으나 그것 은 다음 기회에......
그럼....