이번에는 저번에 이어 윤곽 가공경로 공구항목 파라미터값에 대하여 알아보겠습니다.
② 공구
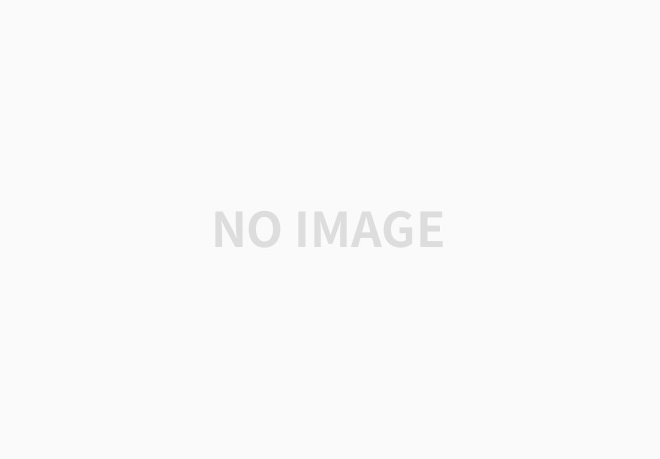
㉤ 공구지름 / 코너반경
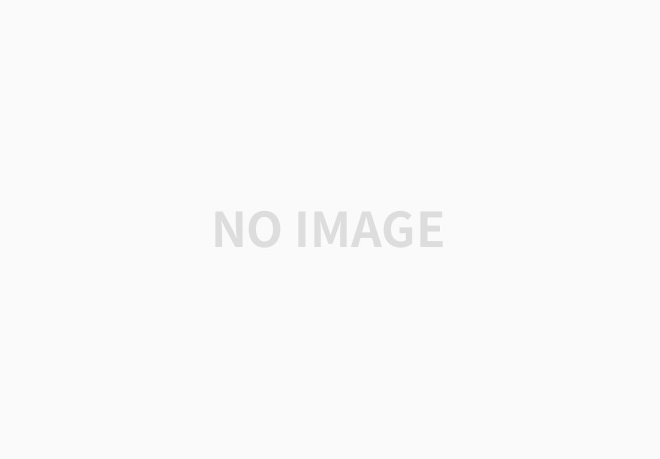
현재 선택한 공구의 지름과 코너반경(불노우즈)의 값을 표시합니다.
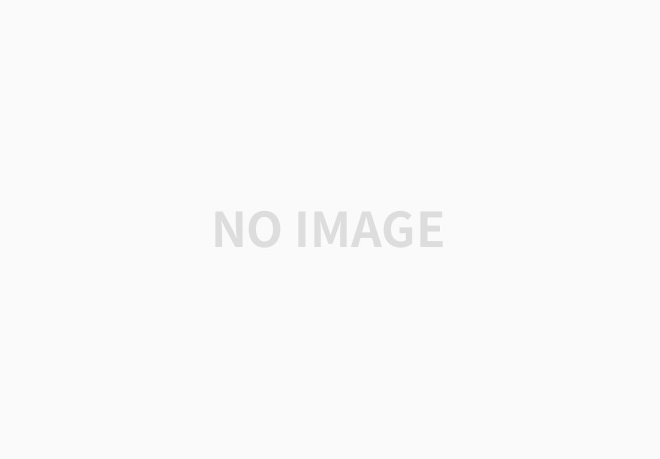
* 이때 주의 사항이 현재 화면상태에서 공구지름 / 코너반경 값을 변경하시면 아래와 같이 경고메시지가 나오면서 해당 공구의 제원이 변경됩니다.
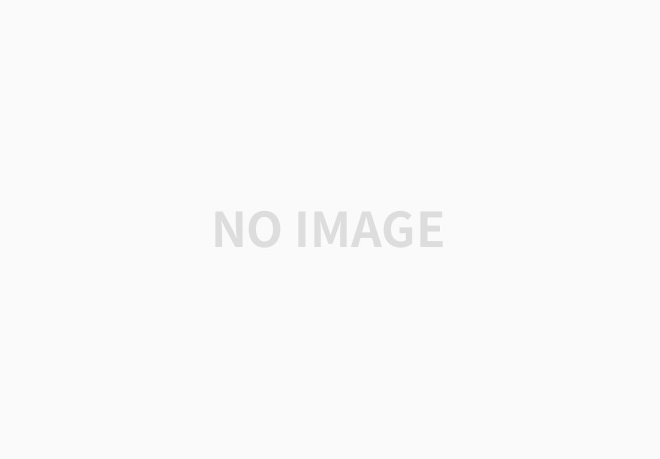
다만 해당 공구명은 기준 변경 전 공구명이 그대로 적용되므로 차후 작업실수가 있을수 있으므로 이러한 루트로 변경하는것은 지향 하시기 바랍니다.
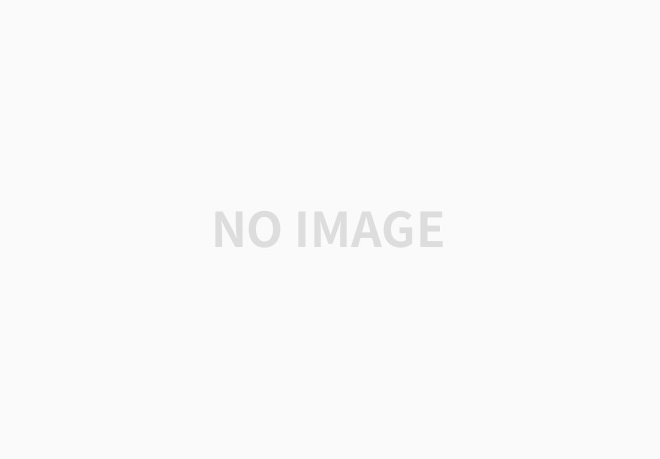
* 위 이미지처럼 해당 가공경로 절삭파라미터에서도 수정이 안되고 아래 가공경로 관리자창 경로표시에도 변경 전 공구명이 기재되며 차후 가공데이터(G코드) 출력시에도 변경전 공구명이 기재됩니다.
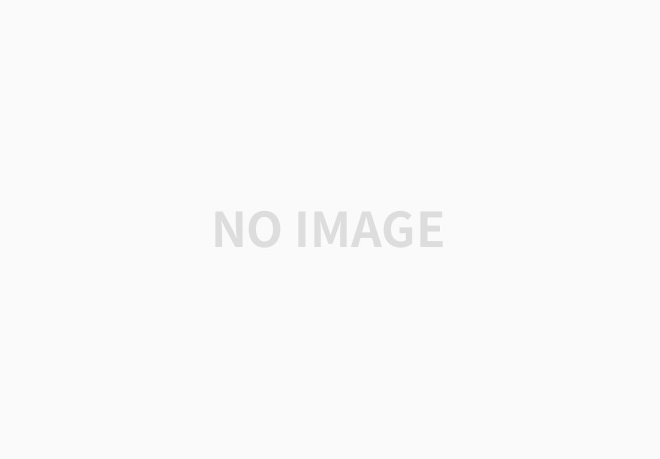
그리고 여기서 위 표시된 경고 메시지에 대하여 알아보겠습니다.
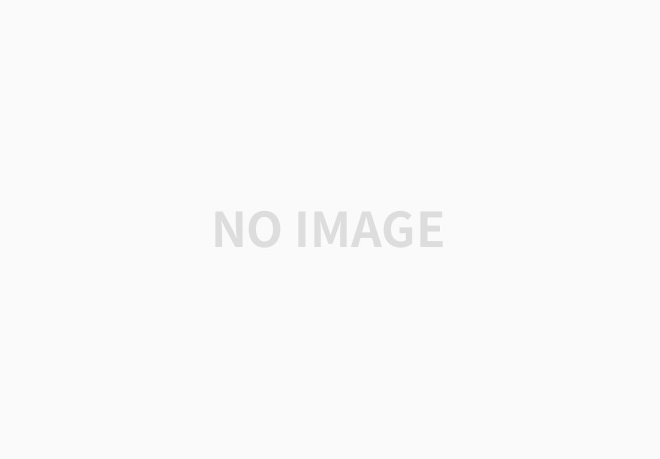
- 어셈블리가 사용된 모든 작업과 어셈블리 업데이트
해당 공구가 적용된 모든 가공정의와 해당 공구 어셈블리 내용을 변경합니다.
* 이경우 해당 공구가 적용된 가공정의를 재생성하셔야 합니다.
* 또한 해당 공구가 공구목록에 있는 공구이고 계속 그 변경사항으로 적용하시려면 해당 공구목록에도 해당 공구를 저장하셔야 합니다.
- 새 어셈블리 생성
해당 공구와 동일한 어셈블리가 생성((동일 공구번호, 이름, 절삭조건이 적용) 변경된 공구 제원값만 변경)합니다.
* 이경우 변경한 해당공구와 동일한 조건에서 변경값만 적용된 공구가 하나 생성됩니다.
* 이 생성된 공구는 해당 가공정의에 적용되지 않습니다.
- 어셈블리 변경을 취소
해당 변경사항을 취소하고 해당 공구의 입력된 값은 원래대로 복원됩니다.
* 해당 변경사항이 취소되고 공구 제원은 원래대로 돌아갑니다.
* 이러한 문제가 있어 해당 절삭 파라미터창에 공구 지름/반경값을 변경하는 것은 지향하고 해당 공구목록에서 공구수정 기능으로 해당 공구 변경값을 적용하는 것을 권장합니다.
㉥ 공구이름 / 공구 적용번호
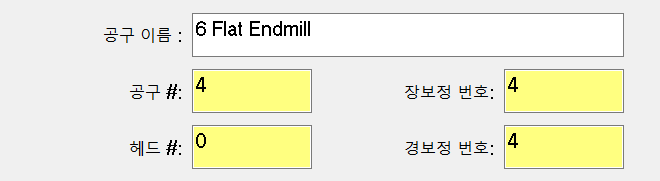
해당 공구의 이름 표시와 해당 공구 적용번호 (장보정 번호 / 경보정 번호), 해당 스핀들 헤드 번호(다축 헤드 장비경우)를 표시합니다.
* 공구 이름은 여기서 변경 시 해당 공구 전체에 동일하게 적용됩니다. (공구목록 제외)
* 공구 적용번호 또한 해당 값을 변경하면 해당 공구 전체에 동일하게 적용되며 공구 번호(공구 #)변경 시 장/경 보정번호도 동일하게 변경되지만 만일 장/경 보정번호를 변경시 해당 값만 변경됩니다.
이것은 공구번호 적용상 당연한 것이지만(동일한 공구번호에서 서로 다른 장/경 보정번호를 적용 가능합니다.)

* 위처럼 공구번호 #12 적용, 장보정 번호는 #11, 경보정 번호는 #10 적용할 수 있습니다. (해당 가공경로만 적용가능)
㉦ 절삭공구 절삭조건값 입력칸
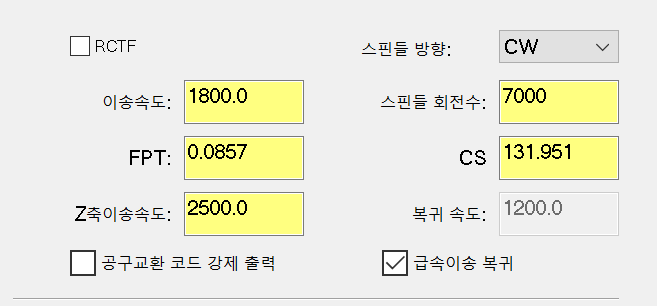
해당 절삭공구의 절삭조건값(이송피드 / 주축 회전수)과 이송 시 필요한 사항을 선택합니다.
RCFT(Radial chip thinning factor / 절삭 시 방사되는 절삭칩의 두께(칩의 양)에 대한 제어 방식)
이 기능은 특정 공구(ISCAR HEM) 적용 시 활성화되는 기능으로 공구 절삭량(스텝 값이 아닙니다)을 일정한 비율로 유지하기 위한 공구 이송피드와 회전을 제어하는 기능으로 일반적으로는 적용되지 않습니다.
* 즉 해당 공구가 항상 일정한 량의 절삭칩을 절삭하기 위한 공구 절삭조건을 제어합니다. (작업자가 지정한 스텝값을 유지하면서)
스핀들 방향
해당 공구(주축 스핀들)의 회전방향을 정의합니다.
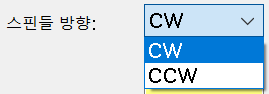
CW : 시계 방향(정방향) M3
CCW : 시계 반대방향 (역방향) M4
이송속도 (FEED : 분당 밀리미터단위 이동거리 / 1분 동안 이송되는 밀리미터 거리)
여기서 이송속도는 절삭이송(G01) 지령 시 각축의 이송속도를 말합니다.
* 보통의 경우(초기값) 공구 생성 시 절삭조건에 대한 값을 지정하지 않으면 마스터캠 해당공구 정삭 기본값(거의 하이스 소재 공구에 준하는)이 입력되며 대부분 미리 정의된 공구목록의 해당 공구 절삭조건 값이 해당 공구 선택 시 자동적으로 입력됩니다.
(머신정의 속성의 공구 설정의 이송속도 적용방법에서 공구 파라미터 적용 시 상황입니다.)
* 이 이송속도는 FPT 또는 CS값을 수정 시 해당 절삭공식에 따라 자동 변경됩니다.
* 이송속도 단위는 MM/MIN입니다.
스핀들 회전수 (Spindle speed : RPM : 분당 회전수 / 1분당 회전하는 횟수)
주축 스핀들의 회전수(RPM)를 입력합니다.
* 보통의 경우(초기값) 공구 생성 시 절삭조건에 대한 값을 지정하지 않으면 마스터캠 해당 공구 정삭 기본값(거의 하이스 소재 공구에 준하는)이 입력되며 대부분 미리 정의된 공구목록의 해당 공구 절삭조건 값이 해당 공구 선택 시 자동적으로 입력됩니다.
(머신정의 속성의 공구 설정의 이송속도 적용방법에서 공구 파라미터 적용 시 상황입니다.)
* 이 회전수는 CS값만 수정 시 해당 절삭공식에 따라 자동 변경됩니다.
FPT : (FEED PER TOOTH AND SURFACE FEET PER MINUTE : 공구 날다 이송속도 & 분당 공구면 피트단위 이동속도)
FPT는 공구 날다 이송속도(fz)로 보시면 됩니다.
* 이 값은 이송속도와 주축 회전수에 연관됩니다.(서로 값이 변경 시 연관되어 변경됩니다.)
* 해당 공구 절삭조건 값 중 fz 값이 있으면 여기에 입력하셔도 무방 합니다.
* 이때 주의 사항이 fz값은 해당 공구 날수에 좌우되므로 해당 공구의 기타 속성 마무리 항목의 절삭날수 값에 연관되므로 만일 FPT값 입력 시 해당 공구 절삭날수도 입력하셔야 정확한 절삭조건 적용이 가능합니다.
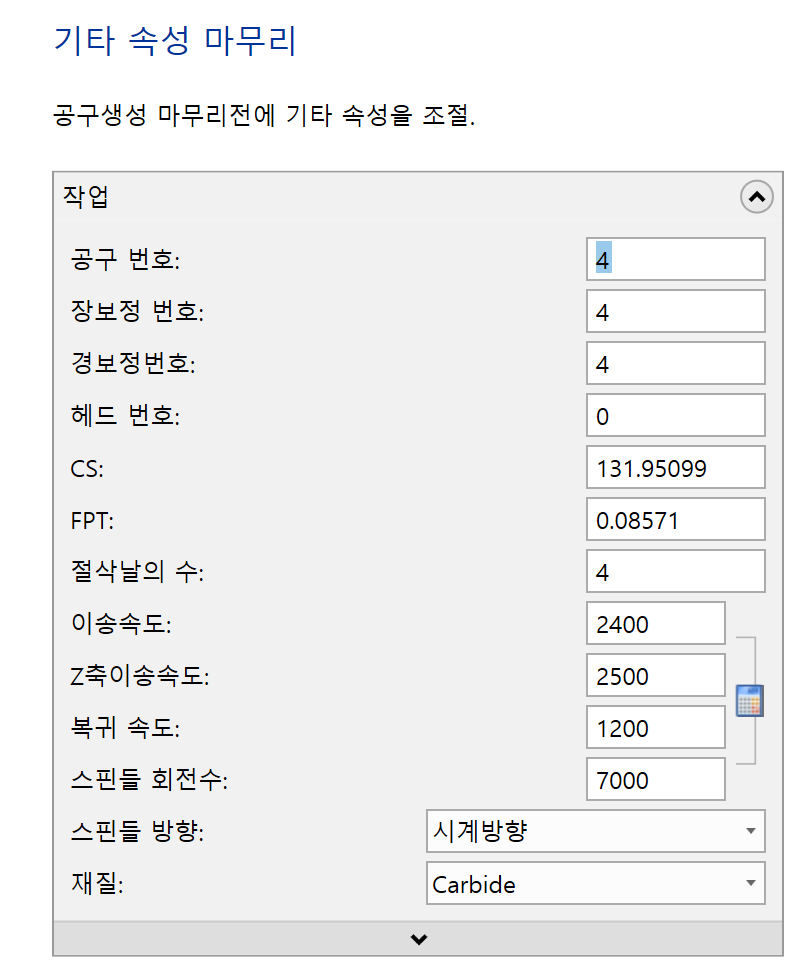
* 그러므로 가능한 공구 절삭조건 입력시 FPT와 CS 값 적용 시 해당 공구 기타 속성 마무리 항목에 입력하여 공구를 등록하여 사용하시는 것을 권유합니다.
CS : (CUTTING SPEED(미터단위) / SFM(인치단위) 절삭속도)
해당 공구의 절삭 속도(Vc)로 보시면 됩니다.
* CS값은 공구경, 회전수값에 연관됩니다.(서로 값이 변경 시 연관되어 변경됩니다.)
* 해당 공구 절삭조건 값 중 Vc 값이 있으면 여기에 입력하셔도 무방 합니다.
* 이때 주의 사항이 CS값은 해당 공구경에 좌우되므로 해당 공구 기타 속성 마무리 항목의 공구경에 연관되므로 만일 CS값 입력 시 해당 공구경 값에 주의(일치)하셔야 합니다.
요점
해당 공구 절삭조건 fz, CS 값을 알면 해당 공구의 속성에서 공구경과 날수량 값입력 시 그대로 해당 칸에 입력하면 해당 공구 절삭조건(FEED & RPM) 값이 자동 연산되어 입력됩니다.
* 자세한 것은 별도로 절삭조건 값 입력 편에서 설명합니다.
Z 축 이송속도 : (Z축 방향 절삭이송(G01)의 속도)
Z축 이송속도는 기본적으로 윤곽경로 링크 파라미터에서 진입높이에서 가공깊이까지 절삭이송(G01)하는 구간에 적용되는 이송속도를 입력합니다.
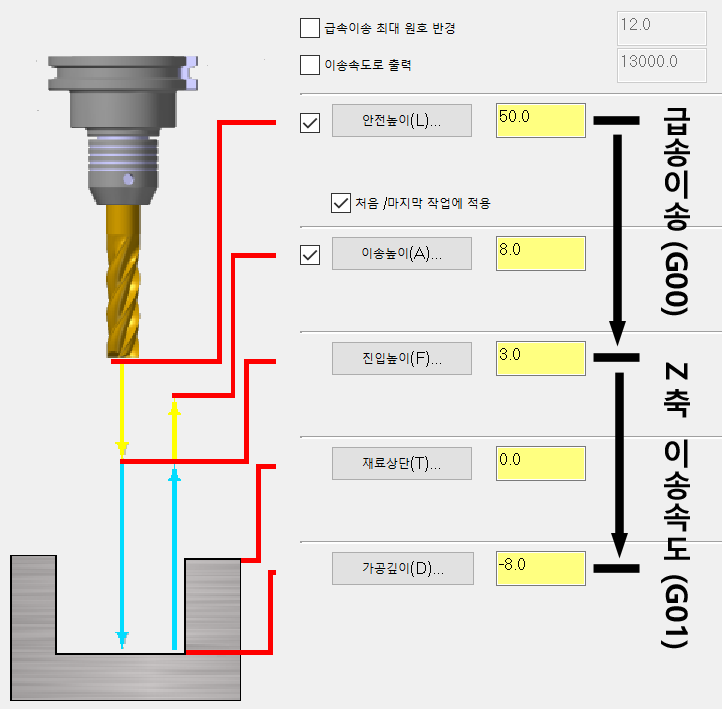
* 기본적으로 링크파라미터 기준 안전거리 또는 이송높이 까지는 해당 장비 급속이송(G00)으로 해당 장비 급속이송 속도로 이송되며 진입높이부터 가공깊이까지 지정된 절삭 이송속도(G01)로 이송됩니다.
* 위 이송속도와는 같은 절삭이송이지만 별도로 지정됩니다.
* 간단히 표현하면 소재 높이에 근접하여 빠르게 가공시작 깊이로 진입하는 Z 축 방향 이송속도 입력칸이라 할 수 있습니다.
복귀 속도 : (가공 종료 후 공구 Z 축 방향 복귀속도)
해당 가공정의가 종료되면 보통의 경우 Z 축 원점복귀 높이 또는 안전높이까지 급속이송(G00)을 하게 됩니다.
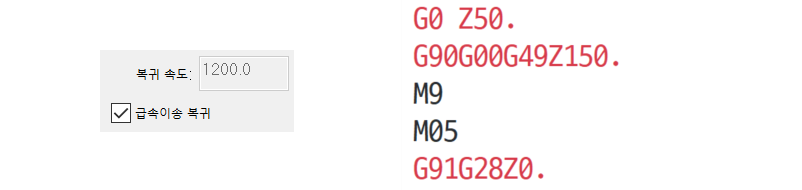
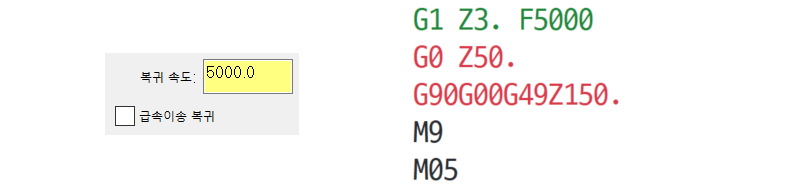
이때 적용되는 급속이송(G00)의 속도가 해당 장비의 급속이송 속도로 복귀이송 하는데 경우에 따라 급속 이송 복귀 선택칸을 체크해제(비활성화) 하면 이때는 진입높이(Z 축 이송속도 적용높이)까지 지정된 이송속도로 절삭이송 하고 이후 다시 급속이송 속도로 복귀 이송 합니다.
* 즉 앞서 Z축 이송속도 지정과 같은 방법으로 Z축 반대방향으로 진행할 수 있습니다.
(급속이송 복귀 체크칸 체크 해제 시)
* 보통의 경우 가공정의 완료 후 그 자리에서 수직복귀 하므로 해당 장비의 급속이송 속도 그대로 적용하는 것이 보통이라 급속이송 복귀 체크칸을 체크(활성화/이송속도 미지정)하여 사용합니다.
공구교환 코드 강제 출력 : (동일공구 사용 시 다른 가공정의로 전환 시 해당 공구교환지령(M6) 출력)
다수의 가공정의 생성 중 동일한 공구를 다음 후공정 가공정의에서도 사용하는 경우 이에 대한 공구교환 지령을 강제적으로 지령(실제 작용은 포스팅 과정에서)하냐를 설정합니다.
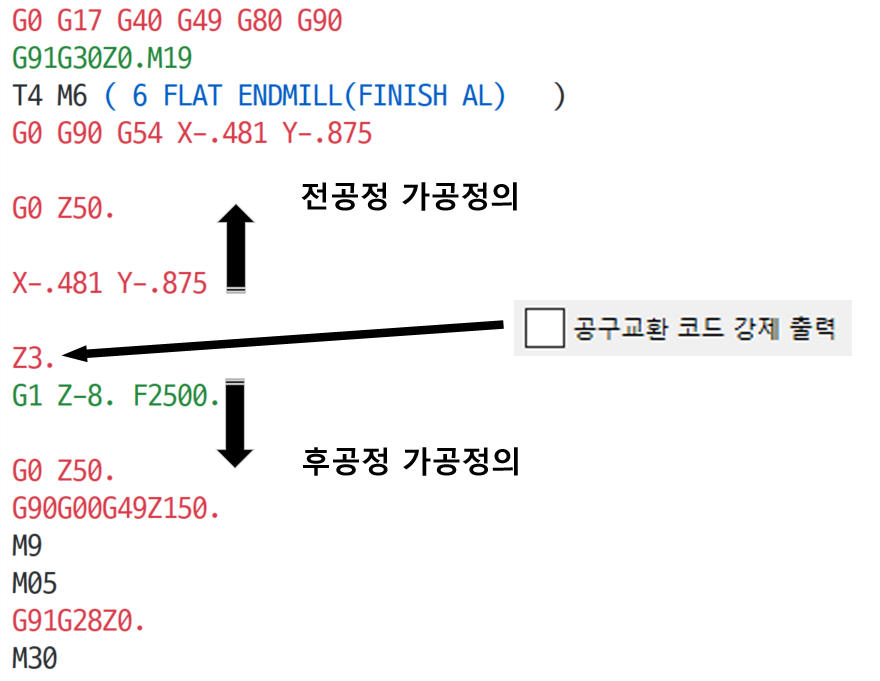
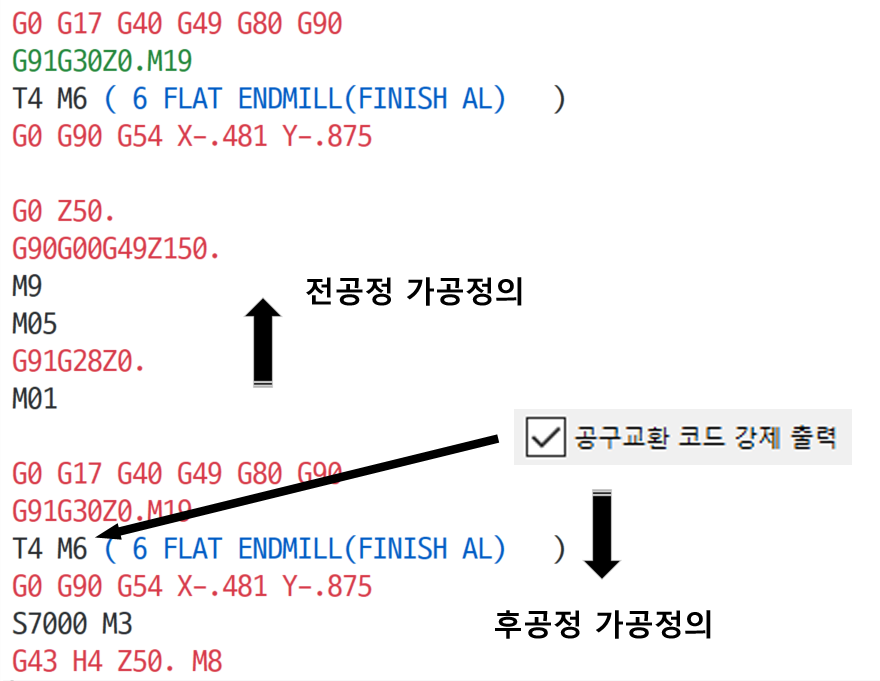
* 즉 다수의 가공정의가 동일 공구를 사용한다면 하나의 가공정의가 실행될 시 공구교환 지령이 발생하느냐 아니냐 을 결정합니다.
* 주로 황삭 같이 같은 공구로 큰 부하(공구 파손여부) 우려 시 공구 파손 또는 마모를 확인하기 위하여 또는 공정마다 공구를 확인하여야 한다든가 (공구 마모/ 측정등) 아니면 가공종료 후 다음 가공영역 이동시 충돌 위험 때문에 일단 가공종료후 Z 축 원점복귀 하고 다시 가공진입하길 원한다든가 하는 작업상 상황에 따라 선택합니다.
* 기본적으로 공구교환 코드 강제 출력 시 불필요하게(?) 공구 Z 축 원점복귀를 반복하는 경우가 있어 해당 항목을 체크 해제 한 상태로 사용합니다.
㉧ 배치 적용 : (가공정의 연산 생성 배치 작업 적용)
이 기능은 해당 가공정의가 오랜 연산시간을 요하는 경우 이러한 경로연산 시간이 장시간 걸린 예상 가공정의들을 배치(선택)하여 차후 배치작업 적용 기능으로 가공경로 연산을 몰아서 진행하는 기능입니다.
* 즉 장시간 연산이 필요한 가공정의 생성 시 그 즉시 연산에 들어가지 않고 배치적용 체크를 하면(해당 가공정의 경로용량칸에 노란 시계표시됨 : 가공경로 연산 하기 전 상태) 차후 이것을 몰아서 (야간이라던가 휴식시간 이라던가...) 배치작업 적용으로 한꺼번에 연산 작업에 들어갑니다.
(배치작업 연산이 끝나면 해당 가공정의 재생성 한 것과 동일한 상태를 유지합니다.)
㉨ 주석문 : (해당 가공정의에 대한 주석문(알림 / 경고 / 특이사항 등 가공데이터와 관계없는 주석문으로 출력)
해당 가공정의 가공데이터 생성 시 해당 주석문이 G코드상 주석문으로 가공정의 최선두 위치에 출력됩니다.
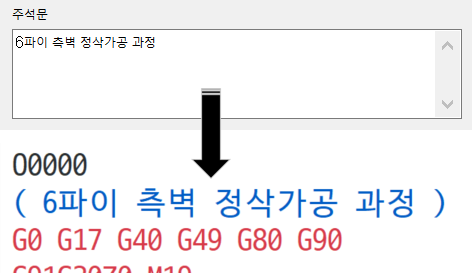
'마스터캠 2021 기능 교육 자료(초안) > 2D 가공 경로 관련' 카테고리의 다른 글
마스터캠 2021를 활용한 2D가공경로에 대하여 -9(윤곽가공 절삭 파라미터) (0) | 2024.03.30 |
---|---|
마스터캠 2021를 활용한 2D가공경로에 대하여 -8(홀더(HOLDER)관련) (2) | 2024.03.24 |
마스터캠 2021를 활용한 2D가공경로에 대하여 -6(윤곽가공경로-1) (0) | 2024.01.21 |
마스터캠 2021를 활용한 2D가공경로에 대하여 -5(체인 옵션) (2) | 2023.12.06 |
마스터캠 2021를 활용한 2D가공경로에 대하여 -4(솔리드 체인작업-1) (4) | 2023.11.26 |