㉡ 보정방향(Compensation direction)
마스터캠에서 선택한 체인요소를 중앙에 놓고 해당 공구가 보정되는 방향이 왼쪽이면 체인 왼쪽면에 공구가 놓이고 보정되는 방향이 오른쪽이면 체인 오른쪽면에 공구가 놓입니다.
보정 형태가 안 함이면 체인 기준으로 공구 축이 놓이며 원쪽/오른쪽 보정방향이 적용되지 않습니다.
* 다만 보정 안함으로 적용 시 해당 가공정의의 가공여유값 적용 시 보정방향에 따라 보정(오프셋)되는 방향이 틀립니다.(적용된다는 의미입니다.)
기본적인 보정 방향은 위와 같지만 보정 형태(컴퓨터/컨트롤/중복보정/안 함)에 따라 출력되는 가공 데이터(G코드)는 다음과 같습니다.
컴퓨터 보정 형태
* 출력되는 가공경로 좌표는 마스터캠 내에서 연산처리(보정되어 절대좌표값으로 출력되는)하여 절댓값으로 출력됩니다.
컨트롤 보정 형태
* 출력되는 가공경로 좌표는 마스터캠내에서 체인 선택된 도형요소의 절대좌표값으로 출력되며 해당 보정 방향에 따라서 G41/G42 보정방식이 적용되며 둘의(왼쪽/오른쪽) 가공경로 좌표는 동일(진입/복귀 제외)합니다.
중복 보정 형태(역 중복 보정 형태 포함)
* 출력되는 가공경로 좌표는 컴퓨터 보정 형태와 동일하나 해당 보정 방향에 따라서 G41/G42 보정방식이 적용되어 출력되며 가공여유값이 적용 가능합니다.
안 함
* 출력되는 가공경로 좌표는 컨트롤 보정 형태처럼 체인 된 도형요소를 따라가며 해당 보정방향이 적용되지 않지만 가공여유값 적용 시 적용 보정 방향에 따라 경로 오프셋은 가능합니다.
㉢ 날끝 보정(Tip compensation)
이것은 마스터캠에서 생성하는 가공경로의 Z값의 기준점을 해당 공구의 날밑바닥(날끝)을 기준으로 하는가 와 해당 공구의 형태가 볼엔드밀(날형태가 중심점이 존재하는 공구형태만 해당(볼엔드밀, 롤리팝 공구 등)) 경우 가공경로의 중심점이 해당 공구 날형태의 중심에 있는 경우 해당 중심점을 기준하는 방식을 의미합니다.
* 롤리팝 공구의 한 종류입니다.
* 주로 볼엔드밀 또는 롤리팝 공구 같이 공구 날형태가 정원 형태이라 공구 가공접점이 날바닥면이 아닌 날전체에 적용해서 가공해야 하는 경우 적용되는 방식으로 거의 롤리팝 같은 경우에만 적용됩니다.
날끝 적용 보정
* 위 이미지처럼 날끝 보정(날 끝적용)을 적용하면 생성된 가공경로는 해당 공구 날끝(날밑바닥 접점)에 기준하여 좌표값이 적용됩니다.
(일반적인 형태로서 흔히 적용하는 공구 길이 보정방식(길이 기준이 날 끝기준)의 경우에는 무리 없는 보정 방식입니다.)
* 위 이미지처럼 날끝 보정(중심적용)을 적용하면 생성된 가공경로는 해당 공구 날중심점(공구날 형태 중심점)에 기준하여 좌표값이 적용됩니다.
(특이한 형태 공구(롤리팝) 경우 공구 발끝점이 아니고 해당 날형태 전체 적용을 하기 위하여 날의 중심점을 공구 보정위치로 사용합니다.)
* 이러한 날끝 중심 보정사용 시 생성된 가공경로의 Z값보다 공구반경만큼 실제 공구 가공범위가 낮으므로 경로확인이나 다른 검증 프로그램 시 출력되는 Z값에 주의하셔야 합니다.
컨트롤러 공구보정 최적화
이 항목은 보정형태를 컨트롤 보정으로 설정 시 에만 활성화 됩니다.
기본적으로는 컨트롤 보정 시 해당 체인 요소를 그대로 따라가는 것이 원칙이라 경로의 변동이 있어서는 안 되는데 이후 설명할 "모서리 절삭형태"와 "전체경로 찾기" 기능을 활성화(적용) 하도록 합니다.
* 원칙은 그러하나 컨트롤 보정 방식의 단점(?)중 하나인 내부 포켓부 진입여부 문제 때문에 사용 시 해당 장비에서 알람 발생을 막고자 하는 의미가 있습니다.
예로서 아래 이미지를 보면 상단부에 공구규격과 일치하는 포켓이 존재하는 체인요소를 컨트롤 보정으로 경로를 생성 시 포켓진입 문제로 장비에서 알람이 발생할 수 있습니다.
(실직적으로 저상부 포켓 부분이 가공공구보다 작은 경우 진입하지 못해야 정상입니다.)
그런데 컨트롤 보정 방법을 그대로 적용하며 공구 진입여부와 관계없이 경로를 따라갑니다.
그러므로 만일의 경우 해당 위험성이 있는 경로는 사전에 차단하여 진입을 막아야 할 필요가 있습니다.
* 다만 컨트롤 방식은 공구 구경(반경) 값을 해당 장비에서 입력하므로 실제 진입 불가인지는 그때 상황에 따라 틀릿수 있습니다.
* 다만 마스터캠은 해당 장비의 공구 반경값을 알 수 업으로 마스터캠 가공경로상에 입력된 공구경을 기준으로 경로를 생성합니다.
* 위 이미지처럼 만일 해당 경로를 컨트롤 공구보정 최적화를 비활성화하면 해당 공구 구경에 관계없이 체인요소를 따라갑니다.
그렇지만 컨트롤 공구 보정 최적화를 활성화하면 모서리 절삭형태(샤프, 전체) 또는 전체경로 찾기 기능을 활용하여 현재 적용된 가공정의 공구경에 따라 경로를 바꾸기도 합니다.
* 다만 이러한 경로에 대한 조치가 실제로 해당 장비의 여러 사항과 대치되지 않은 경우가 있어 사용에 주의가 필요합니다.
* 이러한 이유로 근래(오래전부터?) 컨트롤 보정을 사용하는 경우가 드물어서 그냥 상식선에서 알고 계시면 될 것 같습니다.
㉣ 모서리 절삭 형태
이 기능은 가공정의에 설정된 공구경이 보정되는 보정형태(컴퓨터, 중복보정)에서 사용됩니다.
* 사실상 안 함 보정형태에서만 비활성화됩니다.
역할은 체인 선택된 도형요소의 모서리(코너부) 가공경로 생성 시 그 모서리 부분의 각을 살리기 위하여 (코너 가감속과 일맥상통한 애기입니다.) 원호 가공을 추가하느냐 안 하느냐의 선택 설정입니다.
안 함 : 선택된 체인 도형요소의 모서리 부분에 대한 가공경로를 바로 방향전환 하는 경로(G1 절삭이송 : G2, G3 원호 절삭을 이송하지 않는 경로)를 생성합니다.
샤프 : 선택된 체인 도형요소의 예리한 모서리(모서리 각도 135도 이하) 부분에만 원호 절삭이송(G2, G3)을 적용하고 모서리 각도 135도를 초과하는 부분은 직선 절삭이송(G1)으로 이송하는 경로를 생성합니다.
전체 : 선택된 체인 도형요소의 모든 모서리 부분(각도에 제한되지 않는)에 원호 절삭이송(G2, G3)을 적용합니다.
* 이러한 선택은 코너부의 절삭 시(주로 90도 이내의 뽀쪽한 형태) 도형요소 형태에 따른 절삭이송(G1)만으로 이루어질 경우 절삭이송 특성상(가감속등) 이유로 코너부의 정확한 절삭이 안 되는 경우가 있습니다.
이러한 문제를 해결하기 위하여 일정 각도(135도 이하) 또는 전체 모서리 부분 절삭이송 시 원호 절삭이송을 추가하여 좀 더 부드러우면서 정확한 형태의 모서리부 절삭이송이 이루어지도록 유도합니다.
* 결과적으로 샤프, 전체 옵션이 현재 모서리를 좀 더 날까롭게 절삭한다기보다 좀 더 정확하고 부드러운 절삭이송이 이루어지도록 유도하는 옵션이라고 할 수 있습니다.
* 또한 측벽 모서리부의 버 발생이 줄어든다는 이유도 있고(샤프, 전체 옵션의 경우) 대신 안 함(오리지널 가공경로라고 칭 할 경우)보다 다소 가공시간이 늘어날 수 있다는 점과 가공데이터 용량(원호가공이 추가되므로)이 늘어난다는 점등이 있습니다.
* 기본적으로 사용하시는 것을 권장하며 만일의 경우 단순한 가공(또는 황삭 가공 같이 정밀 비중이 떨어지는)에 경우 빠른 가공시간을 위하여 안 함을 선택하는 경우도 있습니다.
전체 경로 찾기
이 기능은 해당 체인요소의 경로를 미리 추정하여 체인형태와 달리 경로상 공구가 들어갈수 없는 구간이 있는 경우 그 구간의 경로는 생성하지 않도록(활성화 시) 합니다.
* 이기능은 기본적으로 안 함 보정형태에서는 비활성화되며 컨트롤 보정형태에서도 사용에 주의가 필요합니다. (가공경로 생성에 오류 발생)
* 기본적으로 컴퓨터 보정형태에서 사용을 권장하며 주로 안이 넓은 포켓형태(입구가 좁은)는 별도 가공경로 적용 시 유용하며 기본적으로 사용을 기본값으로 합니다.
내부㉤/외부㉥ 코너 라운딩 처리반경
이 기능은 내외부 코너(모서리) 부분의 지정된 값을 라운딩 절삭 처리하는 경우입니다.
* 모서리 부분이 각져 있는 경우입니다.
외부 코너 라운딩 처리반경
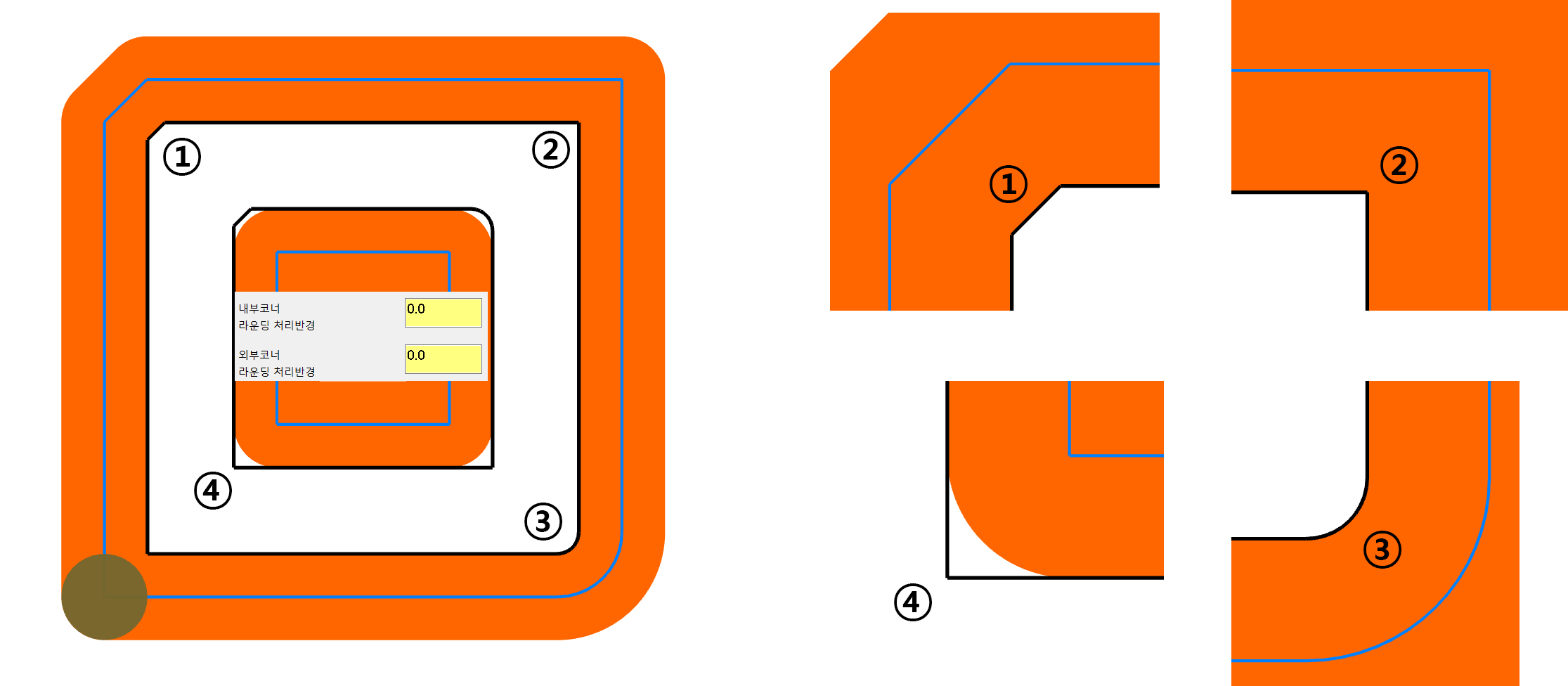
* 위와 같이 외부 코너 라운딩처리 반경값을 0.0 으로 하면 각 체인된 도형요소의 모서리 형태를 그대로 따라 가는 가공경로가 생성 됩니다.
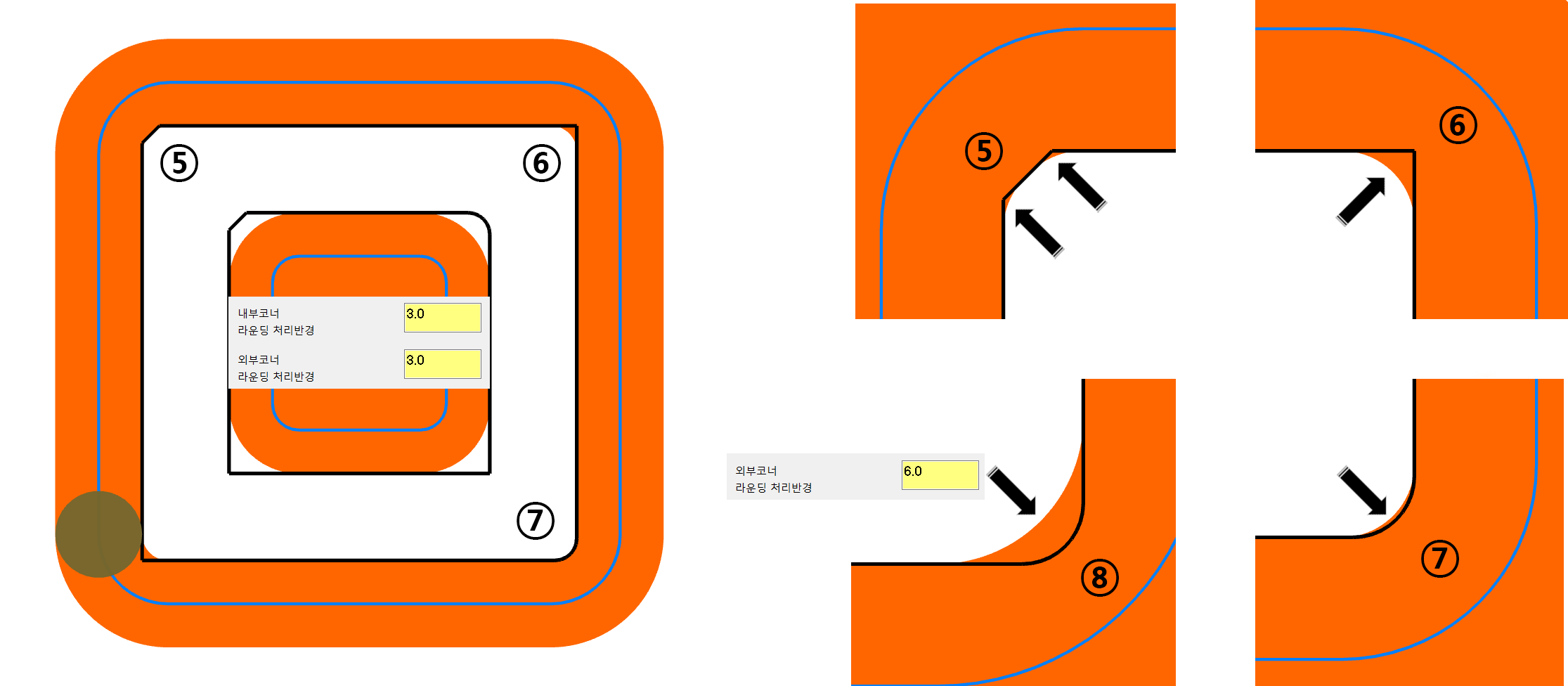
* 위와 같이 외부 코너 라운딩처리 반경값을 3.0 으로 하면 각 체인된 도형요소의 모서리 형태를 넘어서는 필렛 형태의 가공경로가 생성됩니다.
* 정확히는 모서리 부분을 해당 값으로 필렛 했다기보다 해당 각진 가공경로 자체에 경로 라운딩(필렛)이 추가 된것으로 보셔야 합니다.

이것은 해당 윤곽 체인 도형요소가 3D(각 도형요소의 Z값이 틀린경우)좌표값을 가진 경우(3D 윤곽경로)에만 활성화 됩니다.
의미는 정확한의도는 저도 잘 파악이 안되지만 요점은 각각 Z값이 틀린 도형요소 연결점이 Z값 변화폭이 크면 도형요소간 연결경로가 연결되기가(부드럽게) 쉬어지는데 이는 해당 체인요소와의 경로 일치감이 떨어지는 경향이 있습니다.
즉 도형요소간 연경점에 대한 경로생성이 해당 깊이 변화값이 크면 좀더 자유롭게 이루워질수 있으나 변화값이 크다는것(변화폭)은 그만큼 도형요소와의 경로 이탈이 발생할수 있다는것 입니다.
즉 변화 가능값 만큼 경로에서 이탈(Z값만)할 수 있다는 의미가 됩니다.
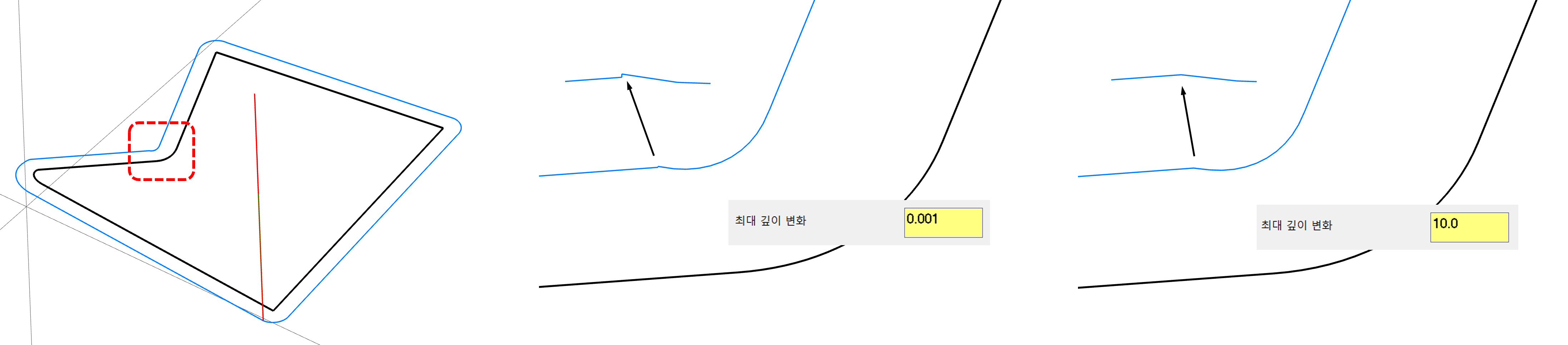
'마스터캠 2021 기능 교육 자료(초안) > 2D 가공 경로 관련' 카테고리의 다른 글
마스터캠 2021를 활용한 2D가공경로에 대하여 -12(윤곽가공 절삭 파라미터-4) (0) | 2024.04.14 |
---|---|
마스터캠 2021를 활용한 2D가공경로에 대하여 -11(윤곽가공 절삭 파라미터-3) (0) | 2024.04.07 |
마스터캠 2021를 활용한 2D가공경로에 대하여 -9(윤곽가공 절삭 파라미터) (0) | 2024.03.30 |
마스터캠 2021를 활용한 2D가공경로에 대하여 -8(홀더(HOLDER)관련) (2) | 2024.03.24 |
마스터캠 2021를 활용한 2D가공경로에 대하여 -7(윤곽가공경로-2) (1) | 2024.03.23 |