안녕하십니까..
정삭
이제 정삭을 들어가야 합니다.
이제 까지 는 황삭 , 중삭 과정이라 크게 문제 될 소지 가 없지만 최종 마감 가공이니 고민 좀 해봐야 합니다.
우선 고려 해야 할 것 이 가공 공구는 무엇을 쓸 것 인가? , 표면 마감을 어느 정도에서 마감 질 것 인가 (가공 후 사상 작업을 하기 때문 에..) , 캠 작업 요소 (이놈의 캠 연산 속도...)을 고려해야 합니다.
먼저 사용 공구
후보 는 3, 4, 6 파이 볼 엔드밀 , 해당 규격 볼 노즈 R1 가 이 있습니다.
* 볼노우즈 을 사용하냐 볼 엔드밀을 사용하냐 는 필히 고민하셔야 합니다.
우선 맨 처음에 모델링 확인 과정에서 안쪽 포켓 내부 알 값이 R2.0 인 것 을 확인하였습니다.
그럼 최소 알 단위 가 R2.0이라는 애기입니다.
그리고 형태 자체가 급경사의 형태 라 공구 측면 이 닿을 가능성을 생각하여야 합니다.
(리브 형태 나 제작 공구 적용..)
또한 볼 엔드밀 , 볼 노즈 사용에 따라 가공방법(가공 경로 방식)을 고려해야 합니다.
그래서 3가지로 분류해봅니다.
1. 6파이 볼엔드 밀로 등고선 정삭
바닥면(평면) 4파이 볼 노즈 R1 엔드밀로 포켓 정삭
3파이 볼노우즈 R1 엔드밀 로 등고선 잔삭 가공 (포켓 내부 바닥 알 , 그 외 미절삭 되는 모서리 알 부분) 하는 방법
먼저 중삭까지 완료된 형상입니다.
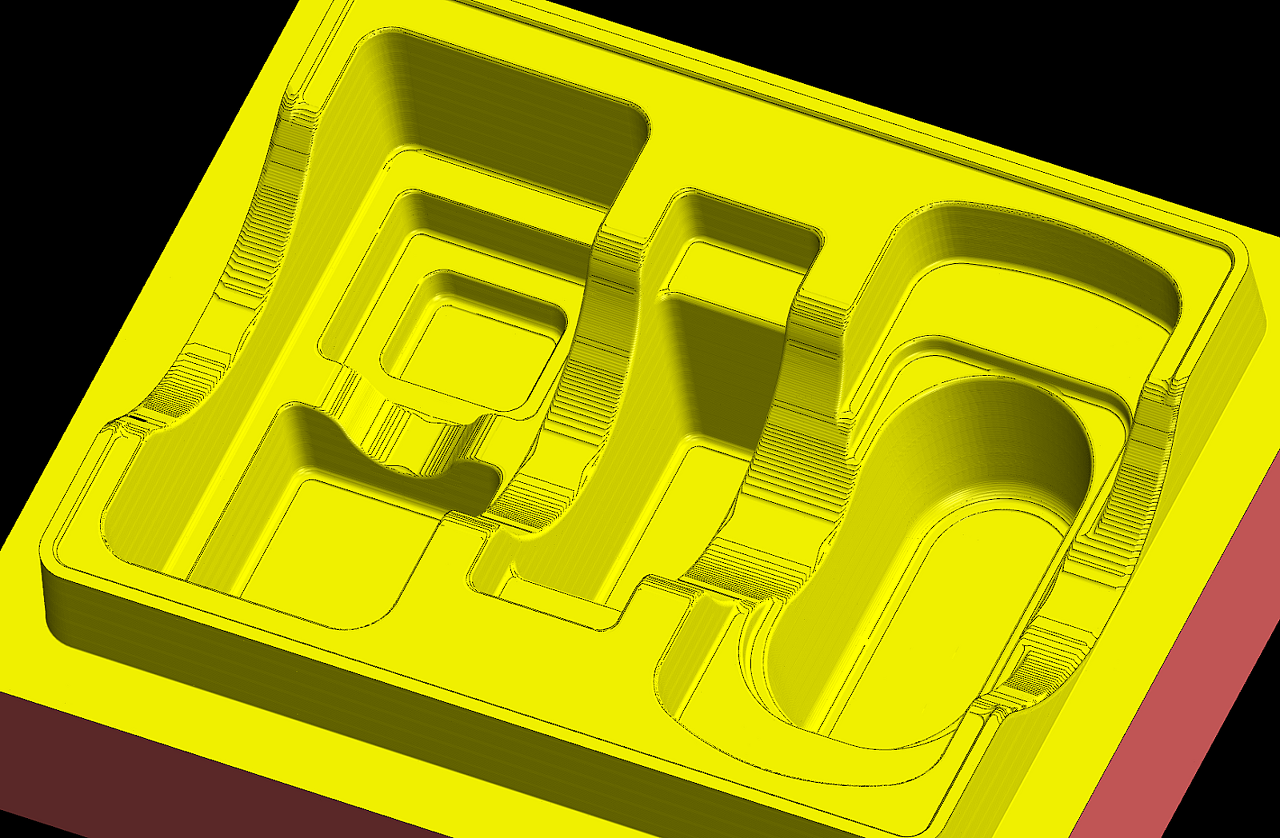
주요 포인트 가 포켓 바닥 부분 미 절삭(정삭 해야 할) 부분과 완만한 경사 가 이어지는 반원 형태 라운딩 부분 계단 형태 미절삭 부분에 대한 정삭입니다.
먼저 등고선 가공으로 포켓 측벽 등 을 정삭 하기 위한 툴패스 을 생성합니다.
먼저 곡면 등고선 가공으로 3 파이 볼 노즈 R0.5로 전체 곡면 (외각 쪽은 공구 중심 영역 설정으로 분리해 놓았습니다.)을 가공 곡면으로 선택하고 특별한 설정 (가공 평면 자동 지정이나 평면 지정을 하지 않고) 하지 않고 가공 간격을 0.15 (가공 깊이 간격)으로 설정하여 툴패스 을 생성해 보았습니다.
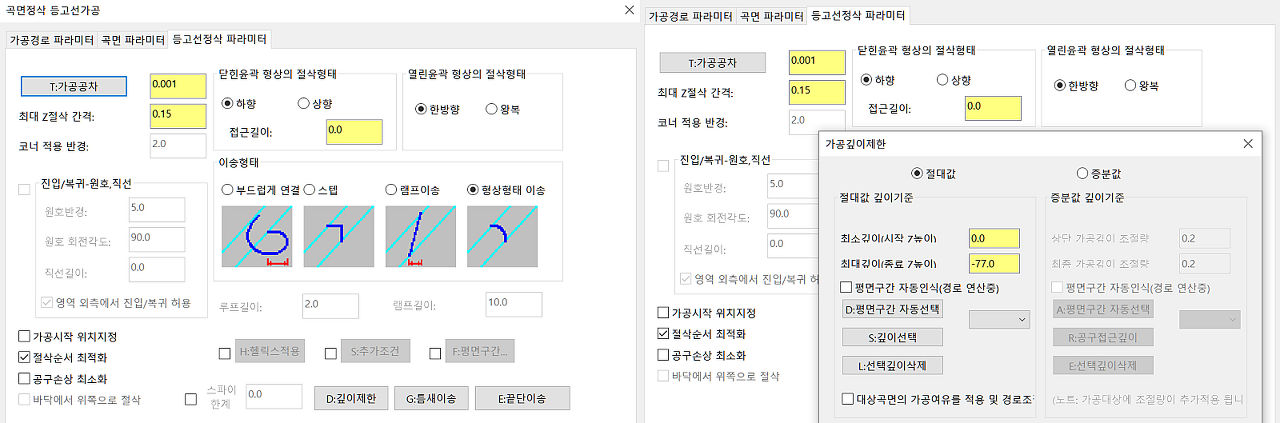
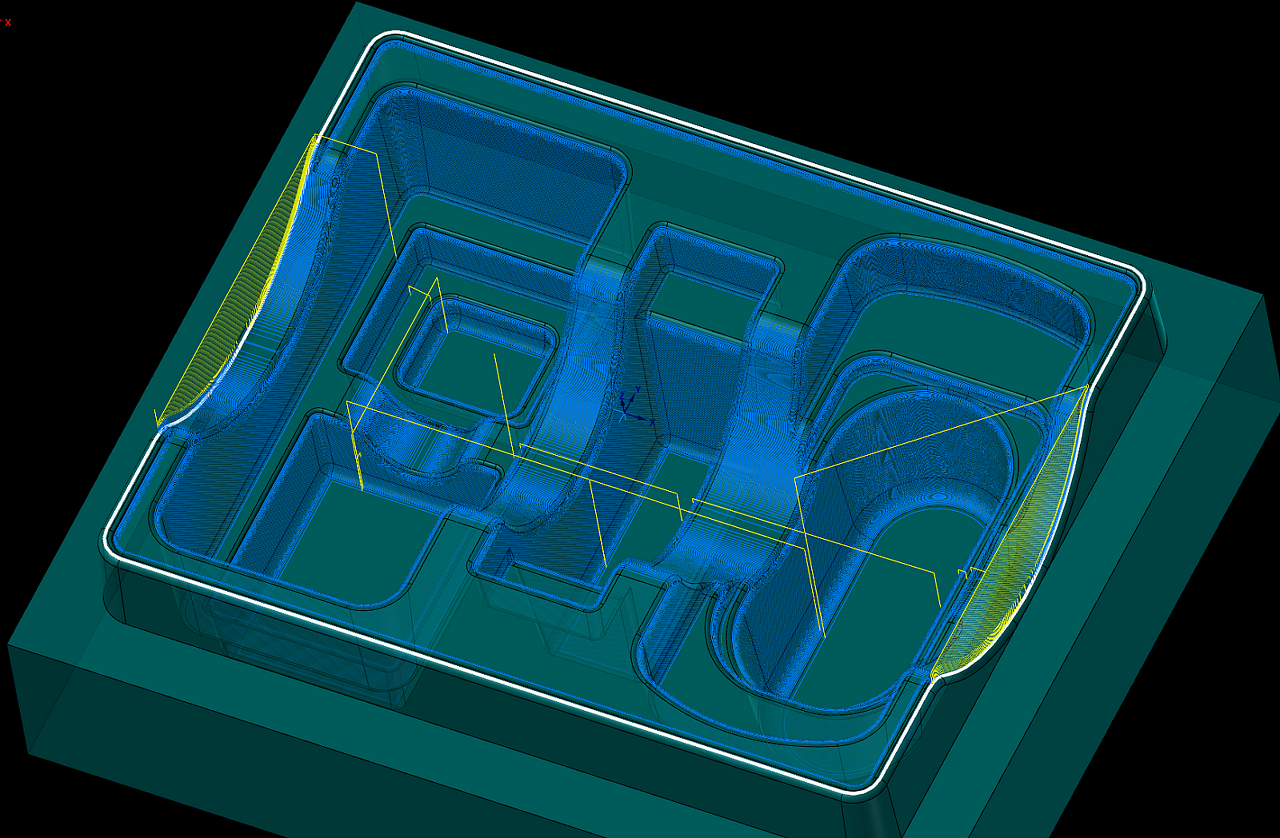
우선 다음과 같이 나옵니다.
자세히 살펴보면 포켓 바닥 면과 반원 형태의 라운딩 부분 의 원호 바닥 (완만한 경사) 부분이 툴패스 가 출력되지 않았습니다.
저 부분 은 별도로 툴패스 (평면 2D 포켓 가공)을 내기 위하여 정삭 툴패스에서 제외한 것입니다.
이유는 저 부분을 등고선 가공 시 같이 툴패스 을 내면 (다수의 평면 존재 시) 에러 가 발생됩니다.
물론 툴패스 을 가공 깊이 별로 따로 (복수의 높이 가 아닌) 하면 가능한데.... 좀 복잡해져서.. 간단하게 해 보겠습니다.
방법 은 우선 해당 평면을 커브 기능으로 해당 평면 외곽선을 생성 시킨후 필요에 따라 공구 을 외곽 으로 오버 가공 하도록 커브 선 을 이동 하여 살짝 키웁니다.
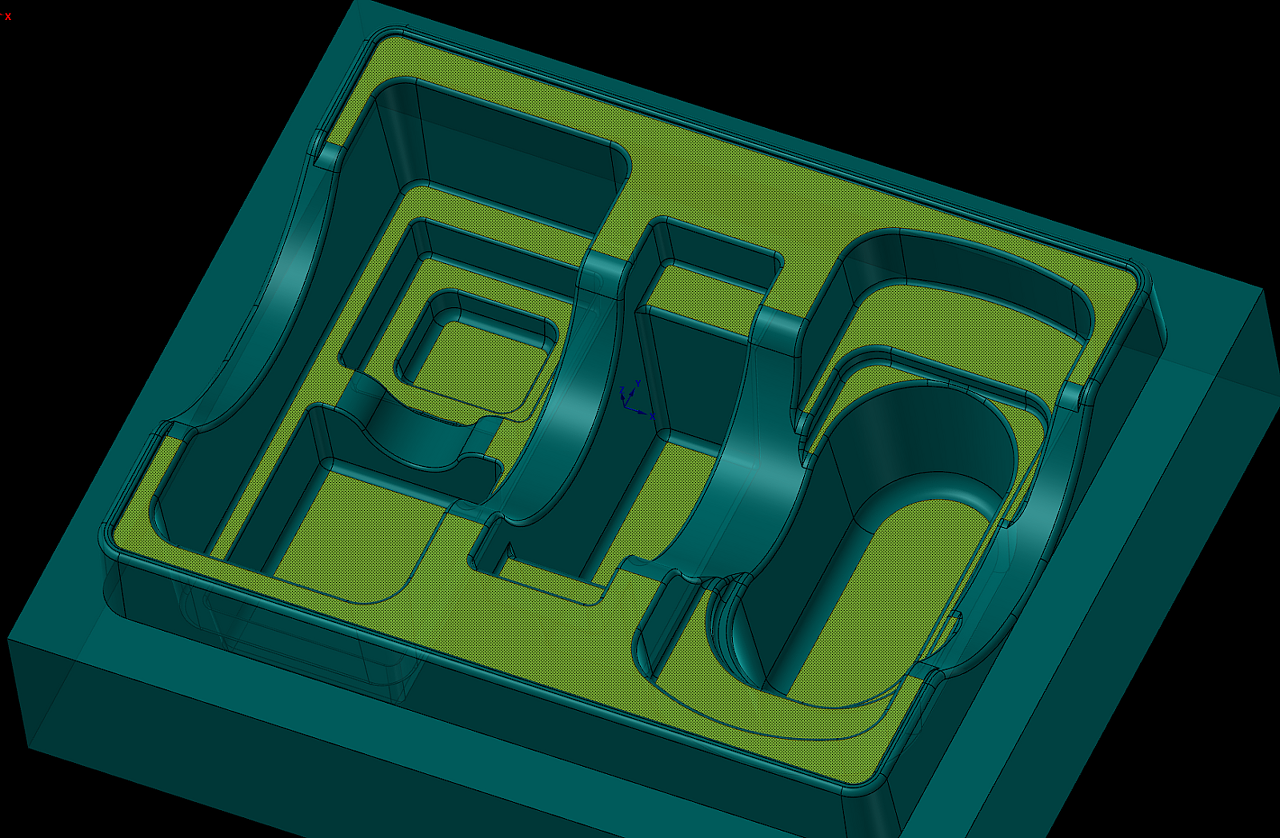
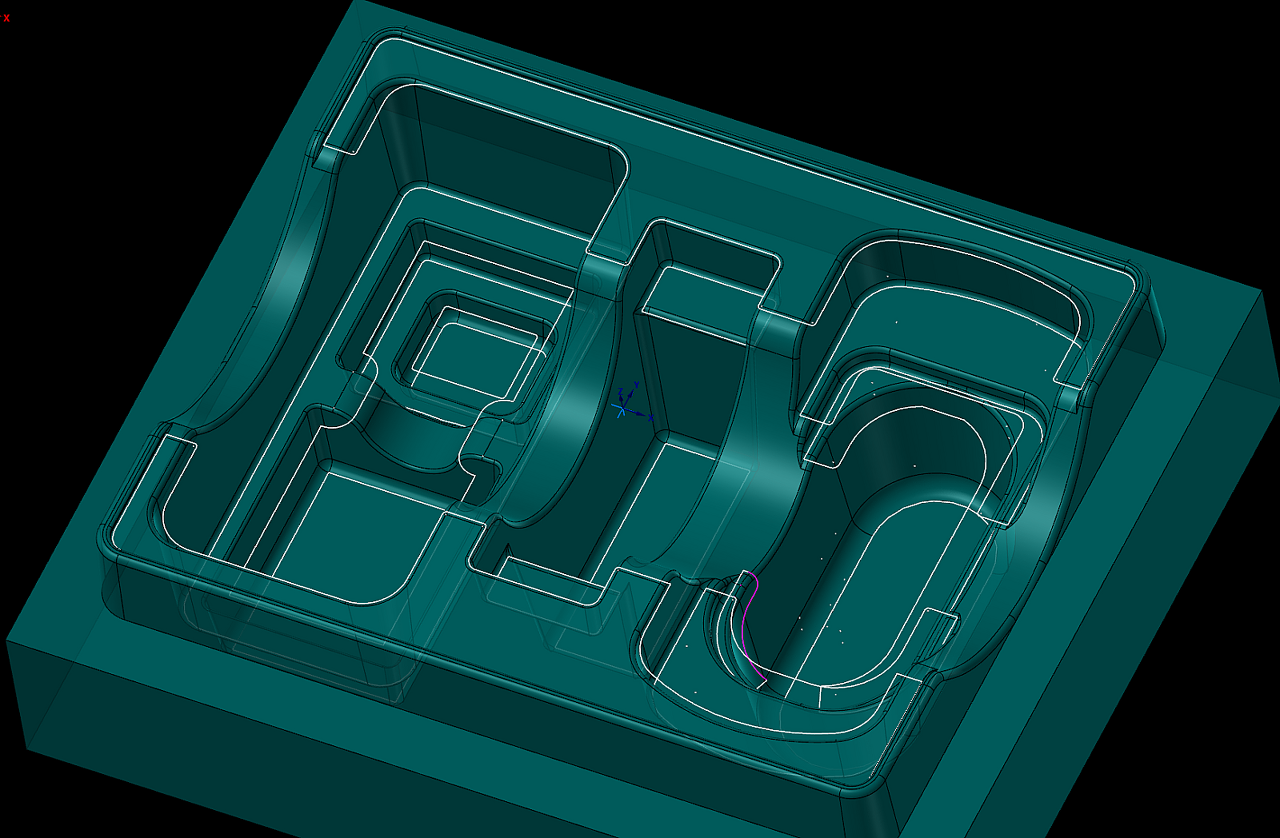
그리고 이 커브 선 을 기준(체인) 하여 포켓 가공을 생성해 줍니다.
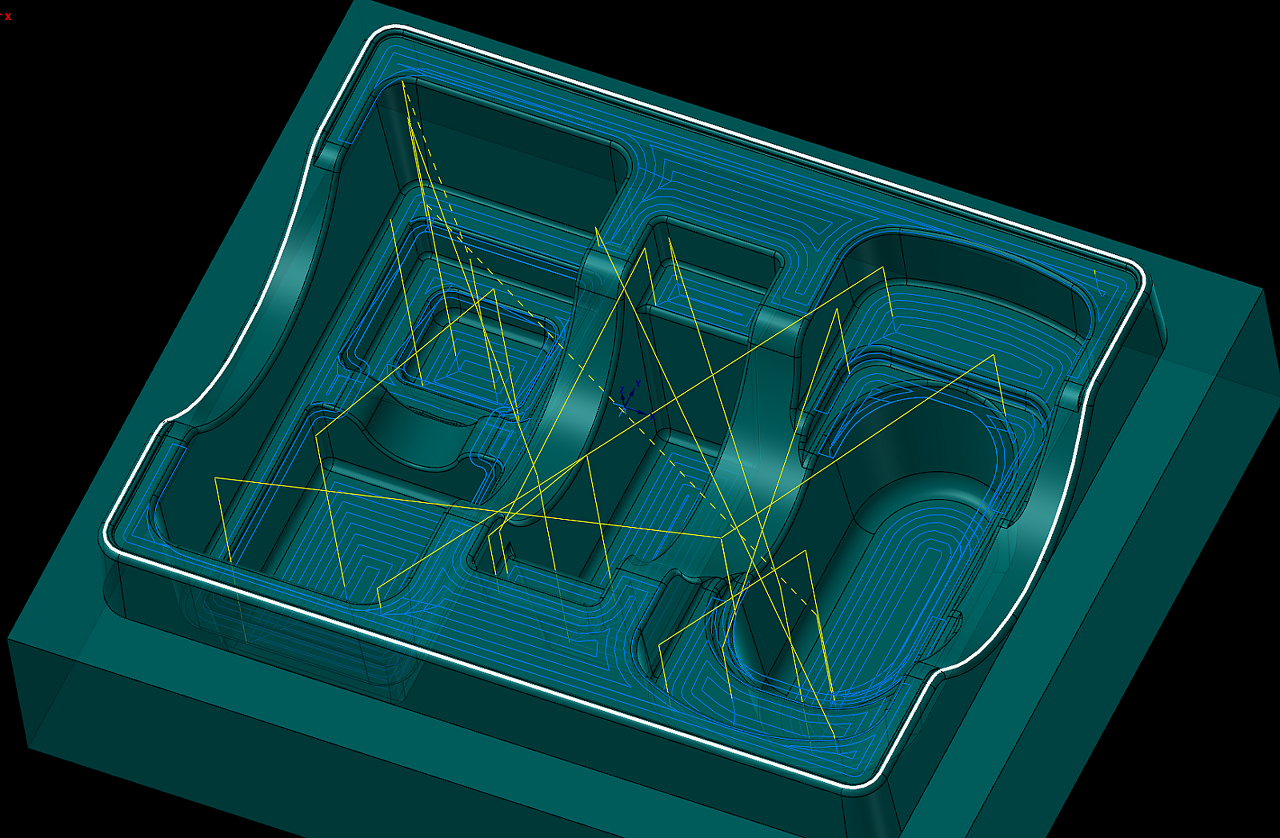
여기까지 생성된 툴패스 을 기초하여 모의 가공을 해봅니다.
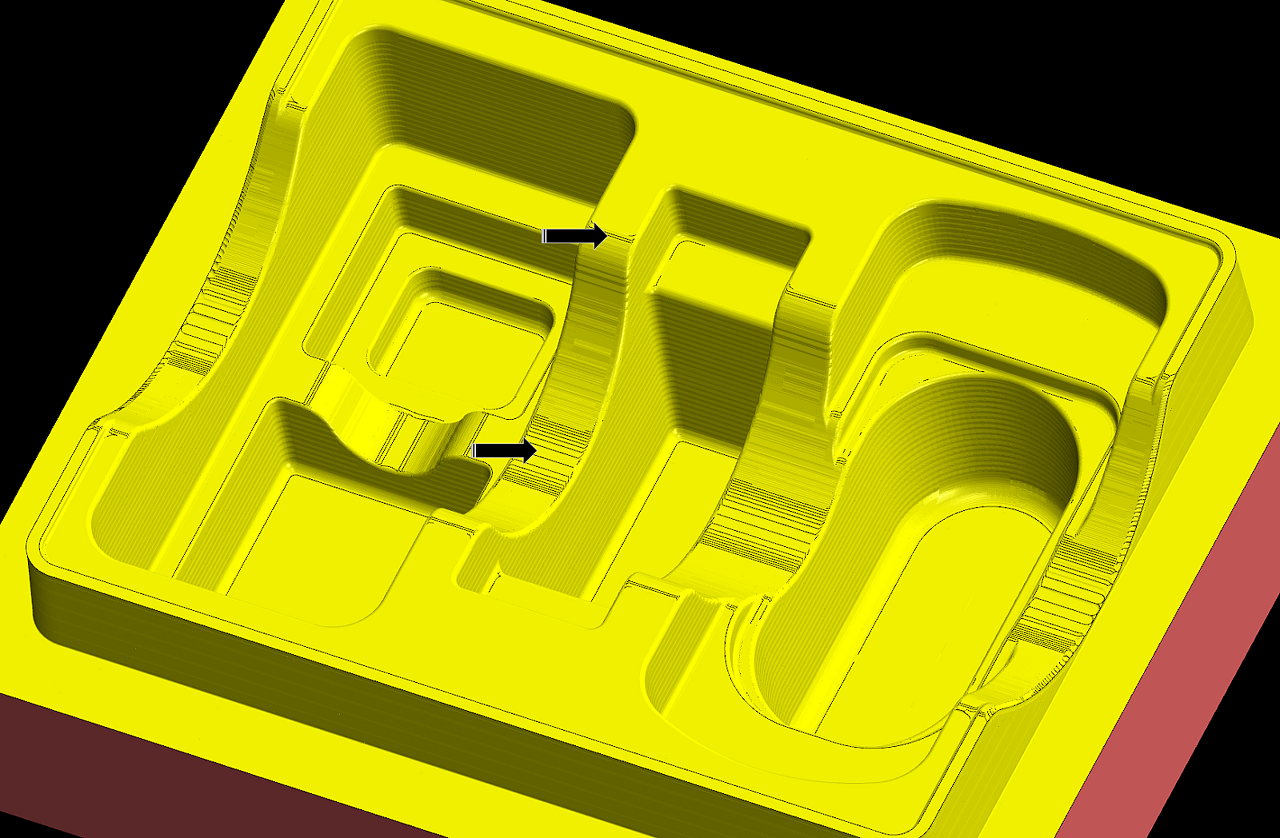
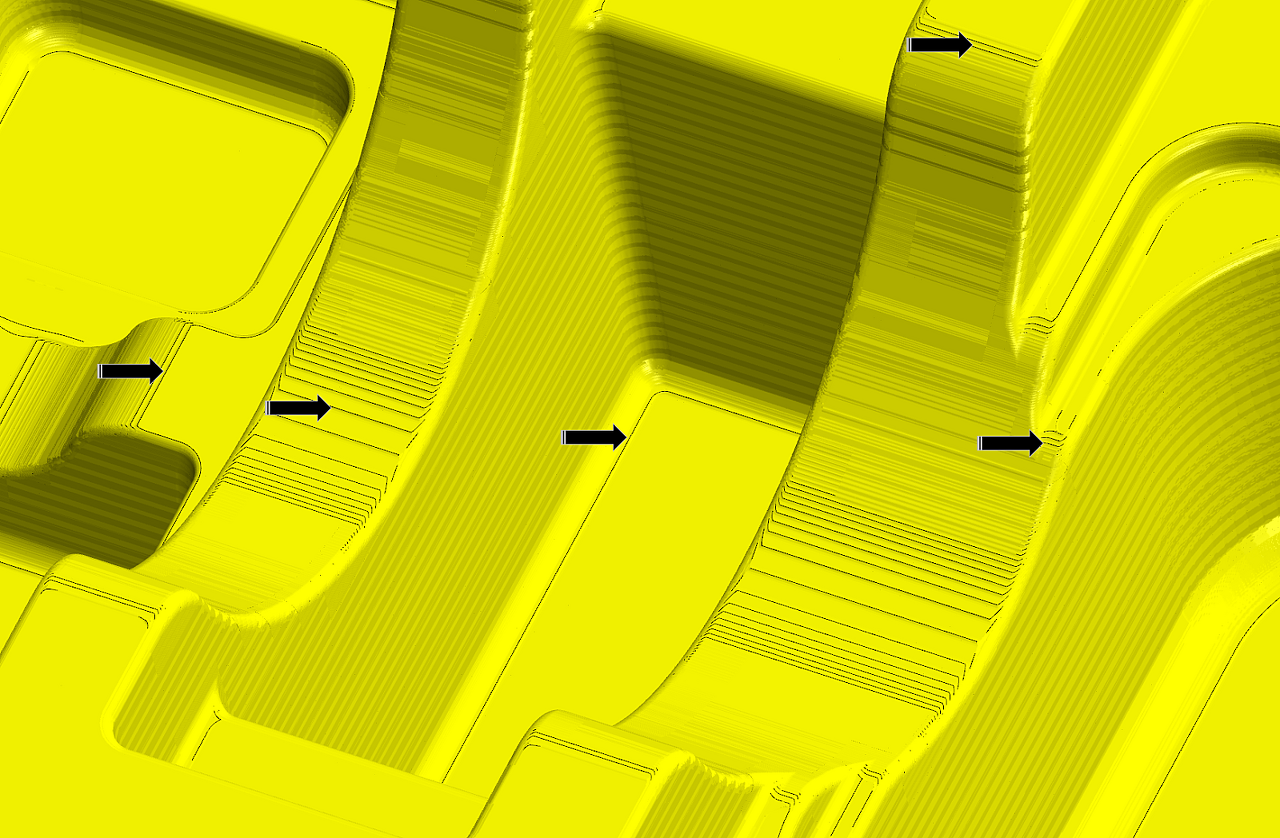
자세히 보면 일부 라운딩 부분 모서리 부분 의 역 알 가공(포켓 쪽) 또는 원형 라운딩 바닥 부분 이 등고선 가공 과정에서 완만한 경사로 인하여 가공 이 덜 된 부분 이 있습니다.
그래서 그러한 부분만 등고선 잔삭 기능 (전 가공 경로 중 등고선 가공 완료된 부분 기초하여 재가공)을 진행합니다.
역시 같은 방법으로 전체 곡면 선택 후 공구 중심 역영 선택하여 재가공을 하였습니다.
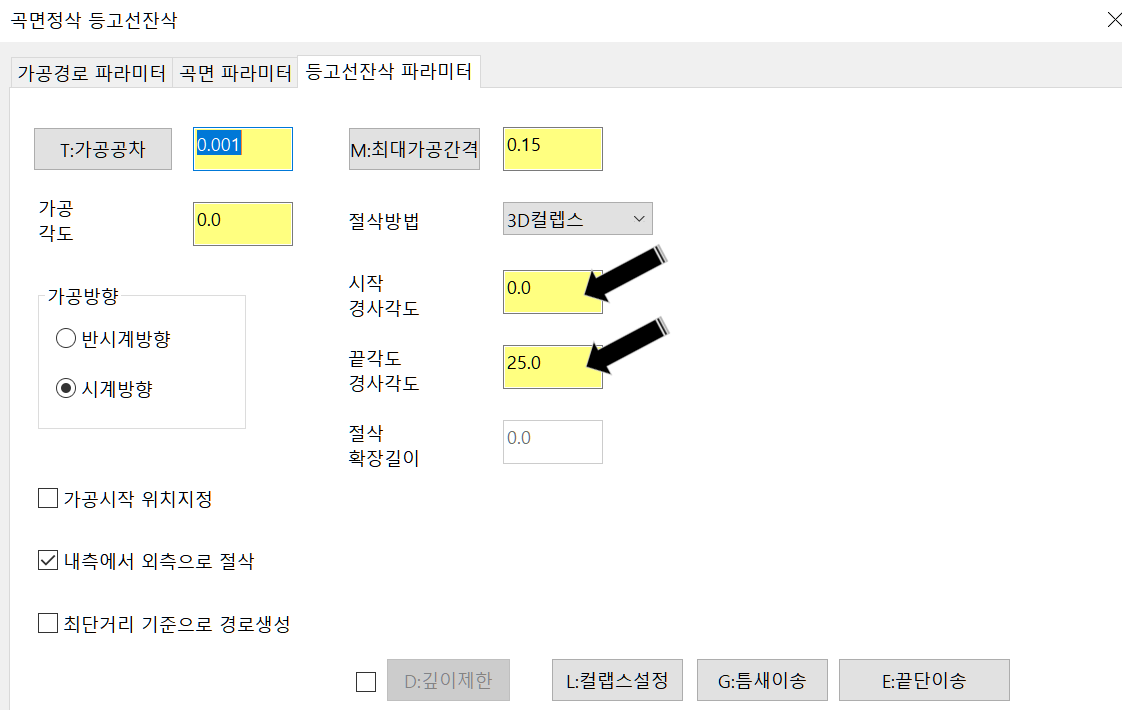
위 절삭 파라미터 중 중요한 것 이 가공 시작 경사 각도와 끝 각도 경사 각도 설정입니다.
이것 은 등고선 가공 중 완만 한 부분 (경사 각도 가 작은)을 중점으로 퉁 패스 산출하라는 의미로 가공 형태 을 고려하여 입력하시면 됩니다.
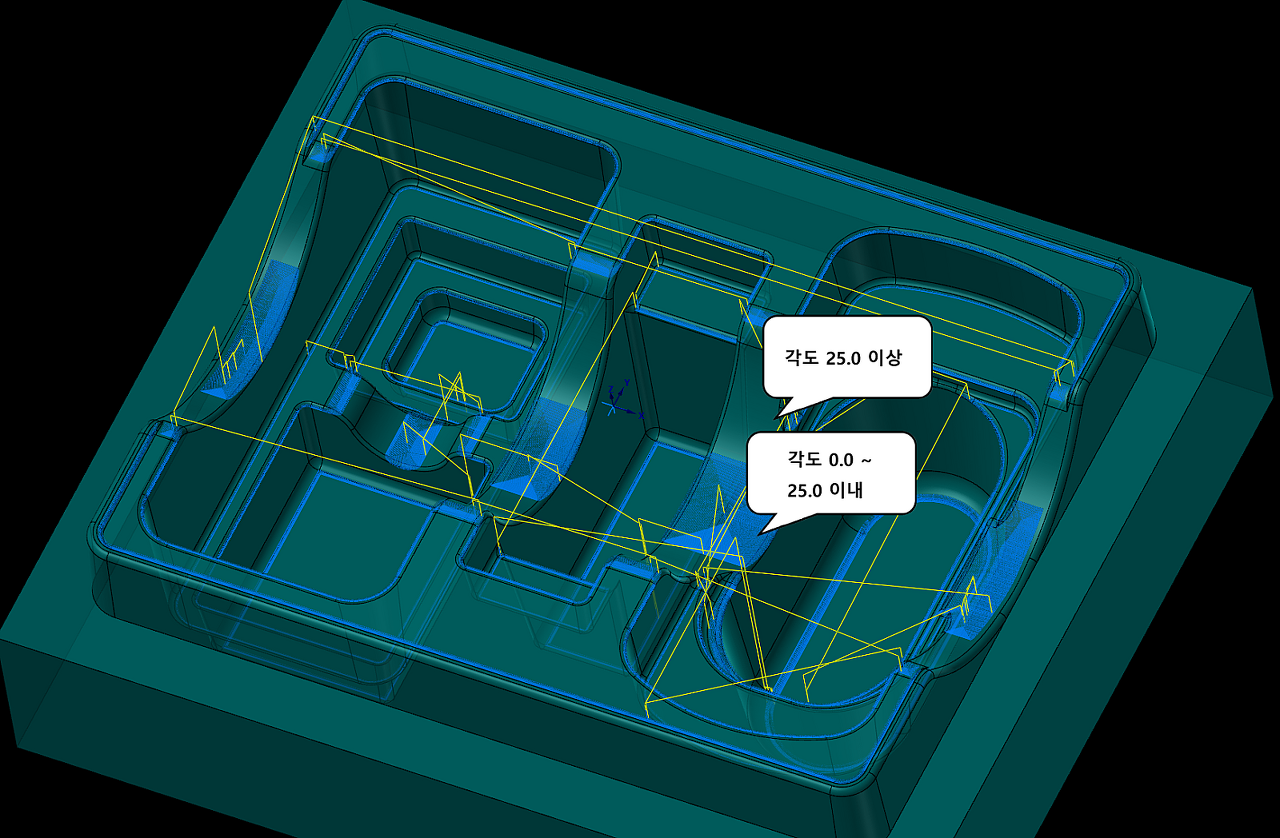
등고선 잔삭 툴패스
그리고 외곽 쪽 의 돌출된 부분 은 스켈롭 가공으로 정삭 툴패스 생성하여 보았습니다.
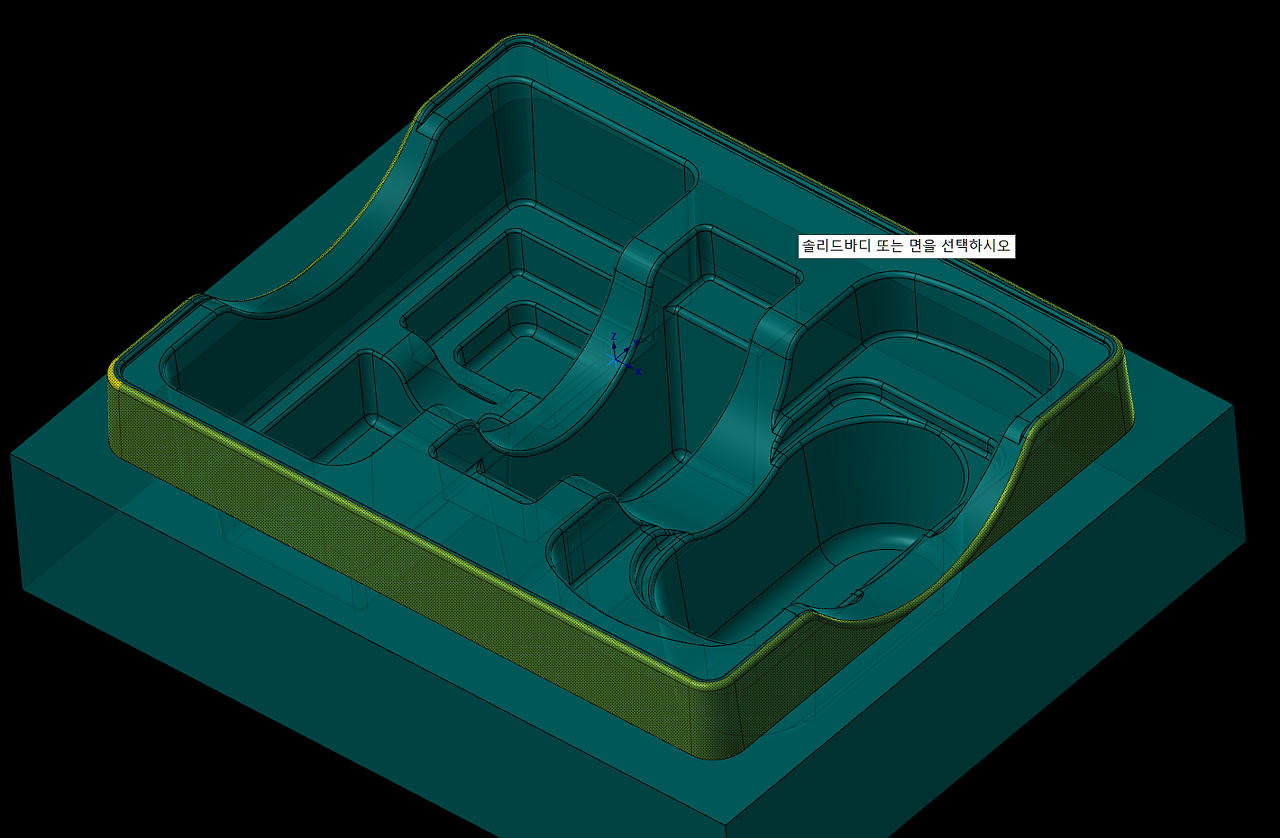
해당 부분 곡면 만 가공 곡면 지정하고 나머지 부분 은 체크 곡면 지정하였습니다.
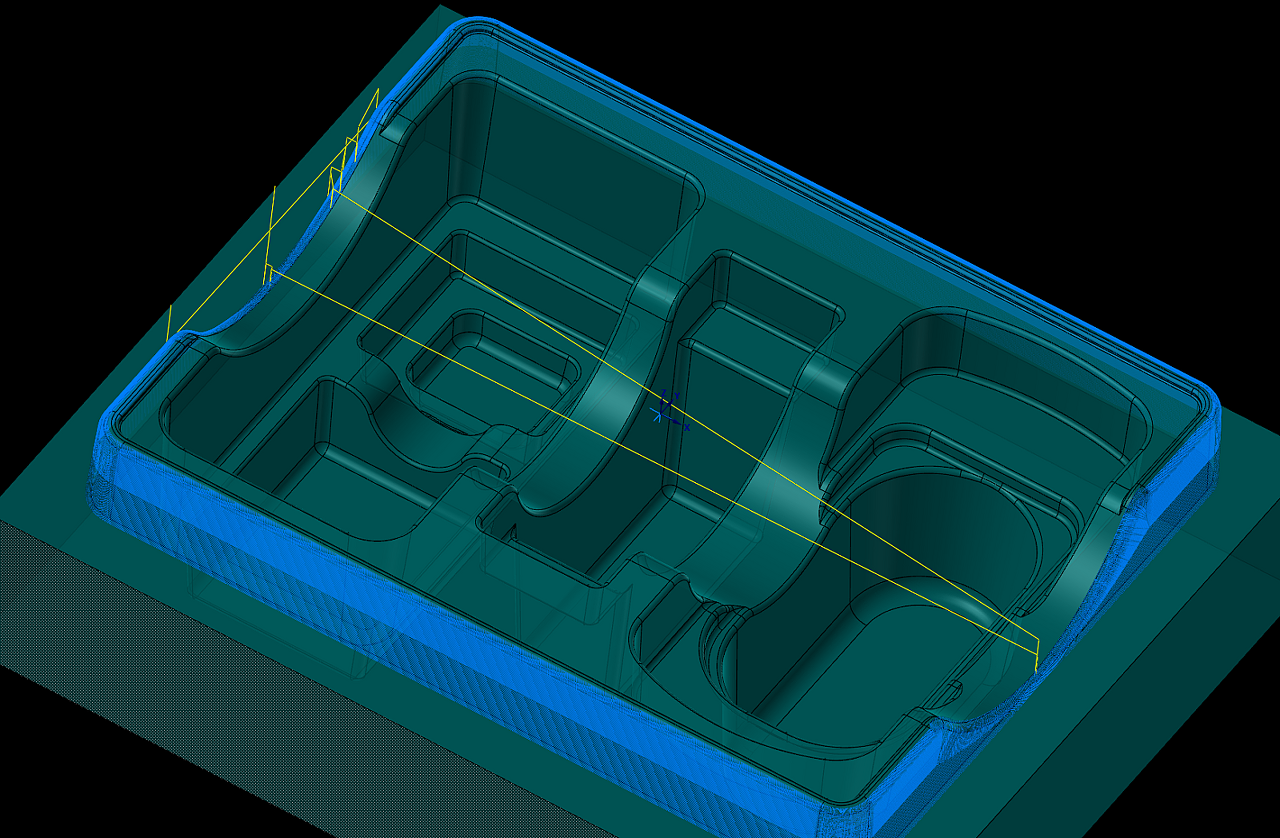
생성된 툴패스
그리고 최종적으로 모의 가공을 돌려 봅니다.
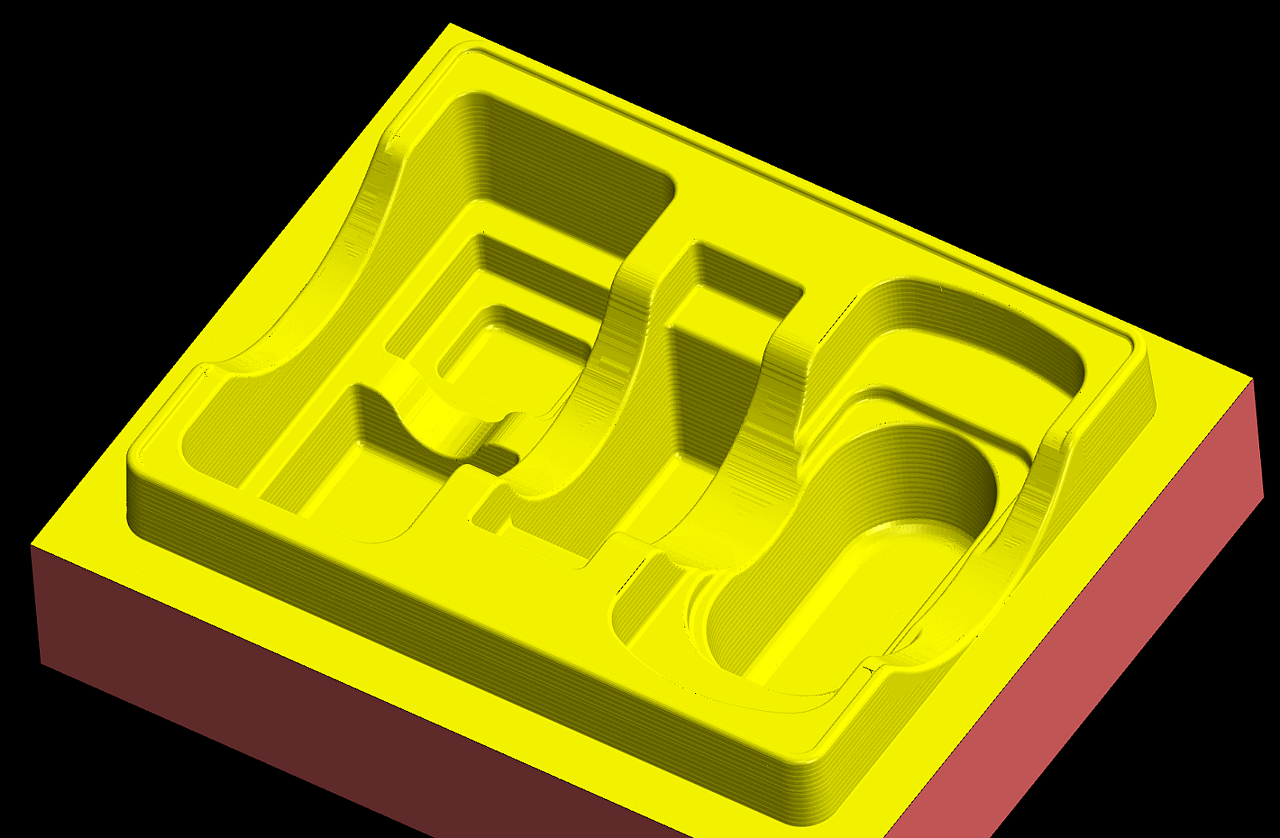
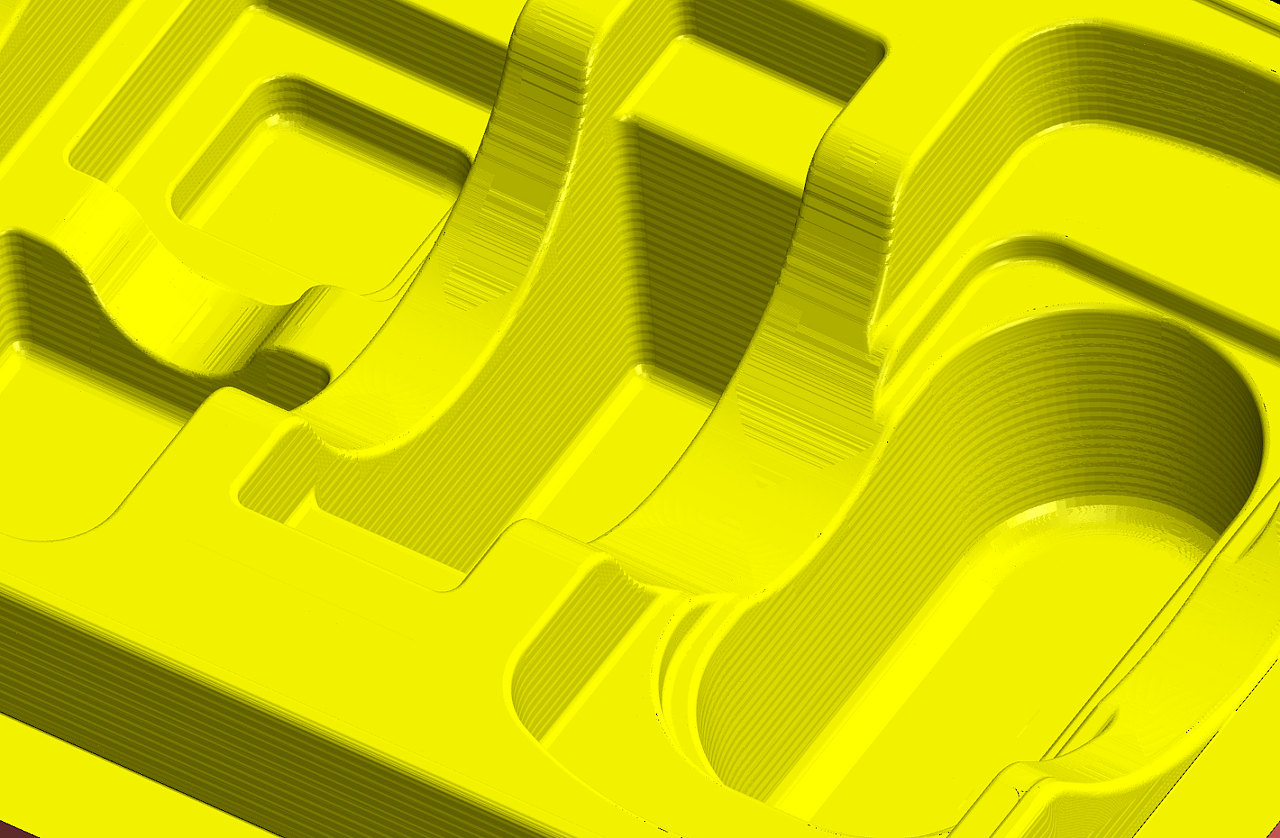
그리고 모델링과 비교 을 해보았습니다. (0.05mm 오차 범위 내)
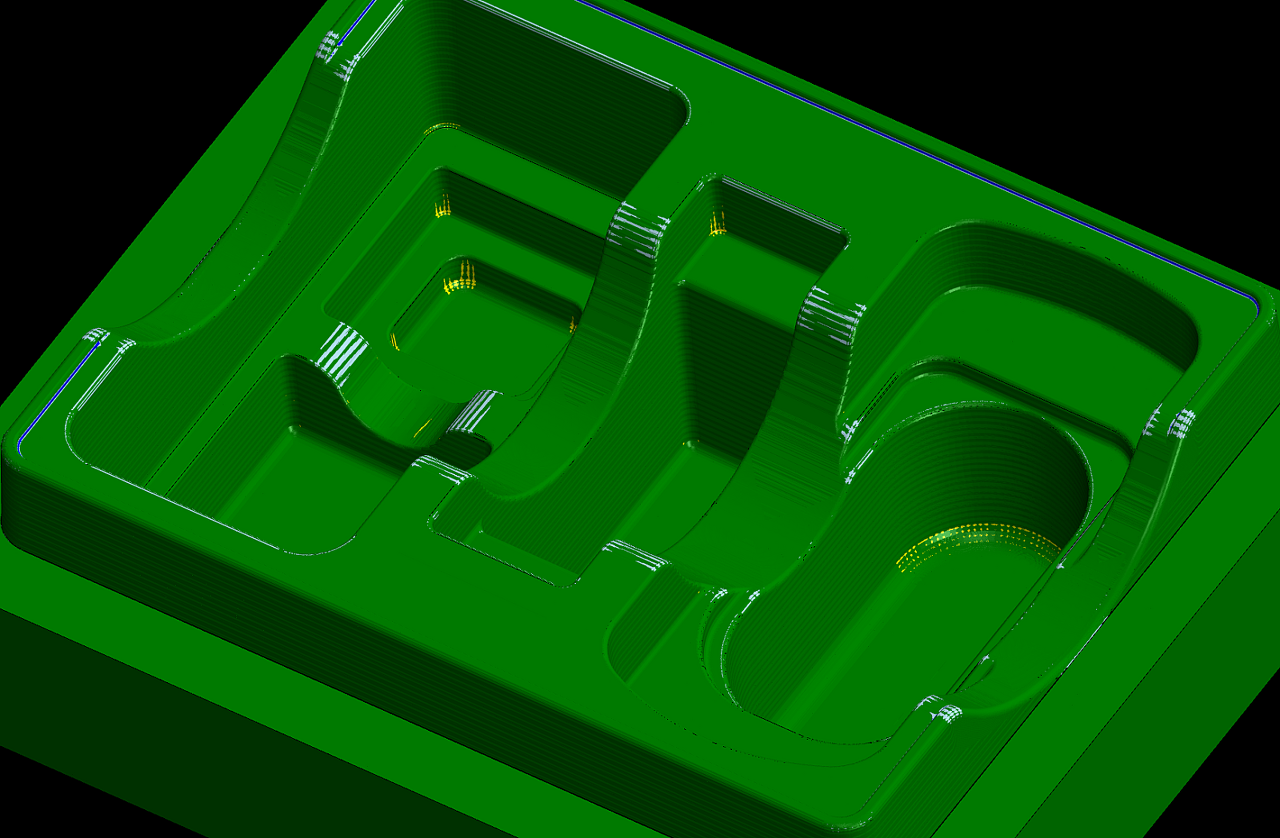
이렇게 해보니 문제 점 이 툴패스 연산 시간 이 너무 깁니다. (통상 한 가공 경로 단 거의 10 ~ 15분 이상)
이러다 보니 정삭 한번 잡고 수정하고 잔삭 한번 잡고 수정 하고 4 ~ 6번 연산 처리시키면 거의 연산 돌아가는 시간 만 1 ~ 2 시간 소요됩니다... (모의 가공 시간 은 좀 짧으니 제외합니다.)
그래서.....
2. 1번 방식과 유사 하지만 좀 빠른 가공 경로 (잔삭 가공을 지향하고 좀 절감(연산 시간) 할 수 있는 다만 곡면 지정 작업 이 복잡한) 생성하는 방법입니다.
일단 중삭 까지 는 동일하게 처리합니다.
정삭 은 똑같이 곡면 등고선 가공으로 하는데 쉘로우 가공을 추가합니다.
먼저 포켓 측벽만 먼저 가공할 것이므로 포켓의 측벽 만 먼저 선택하여 가공 곡면으로 하고 나머지는 전부 체크 곡면으로 설정합니다.
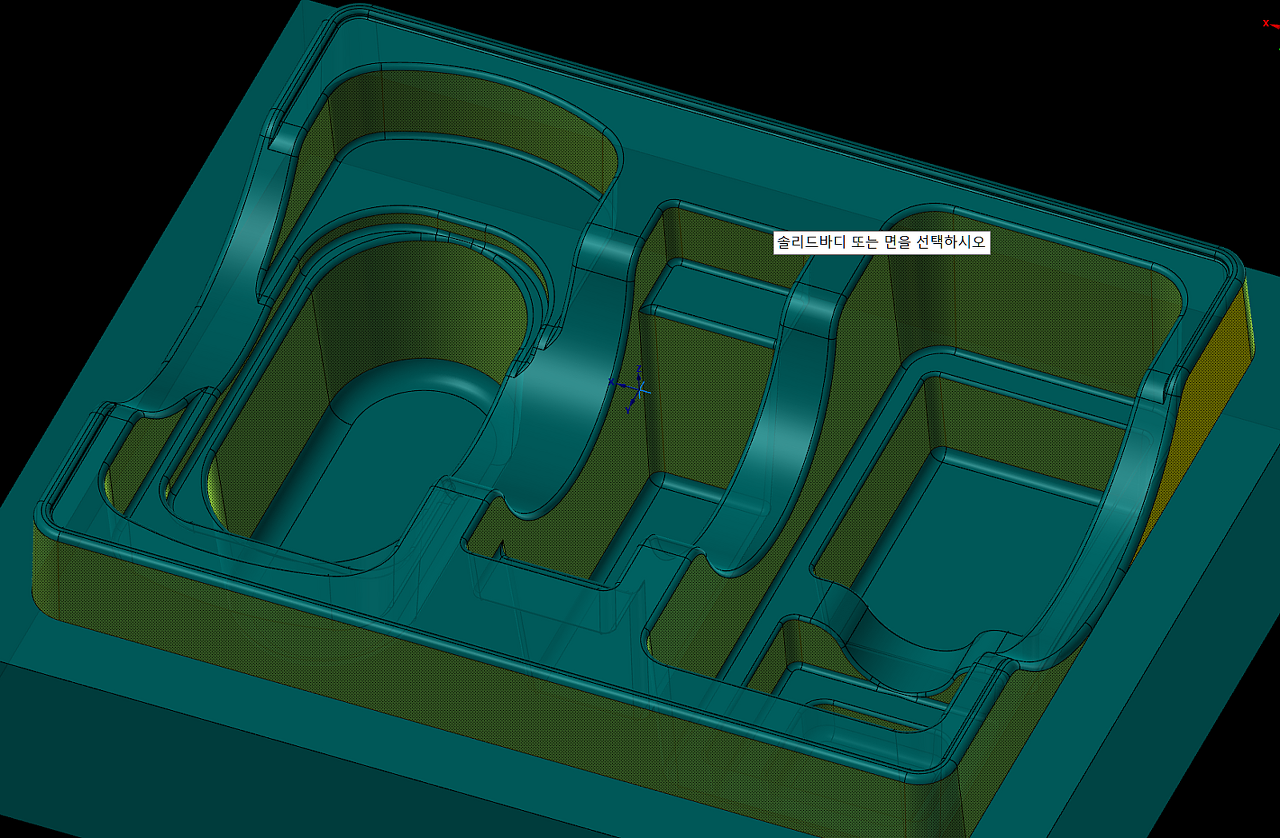
그리고 등고선 가공 툴패스 을 생성해 줍니다.
가공 파라미터는 평범하게 설정해줍니다.
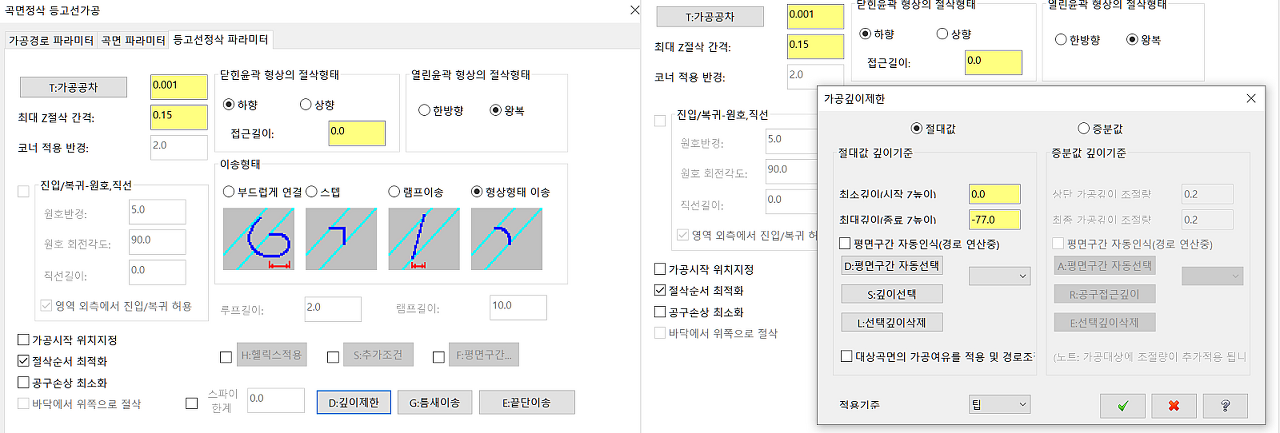
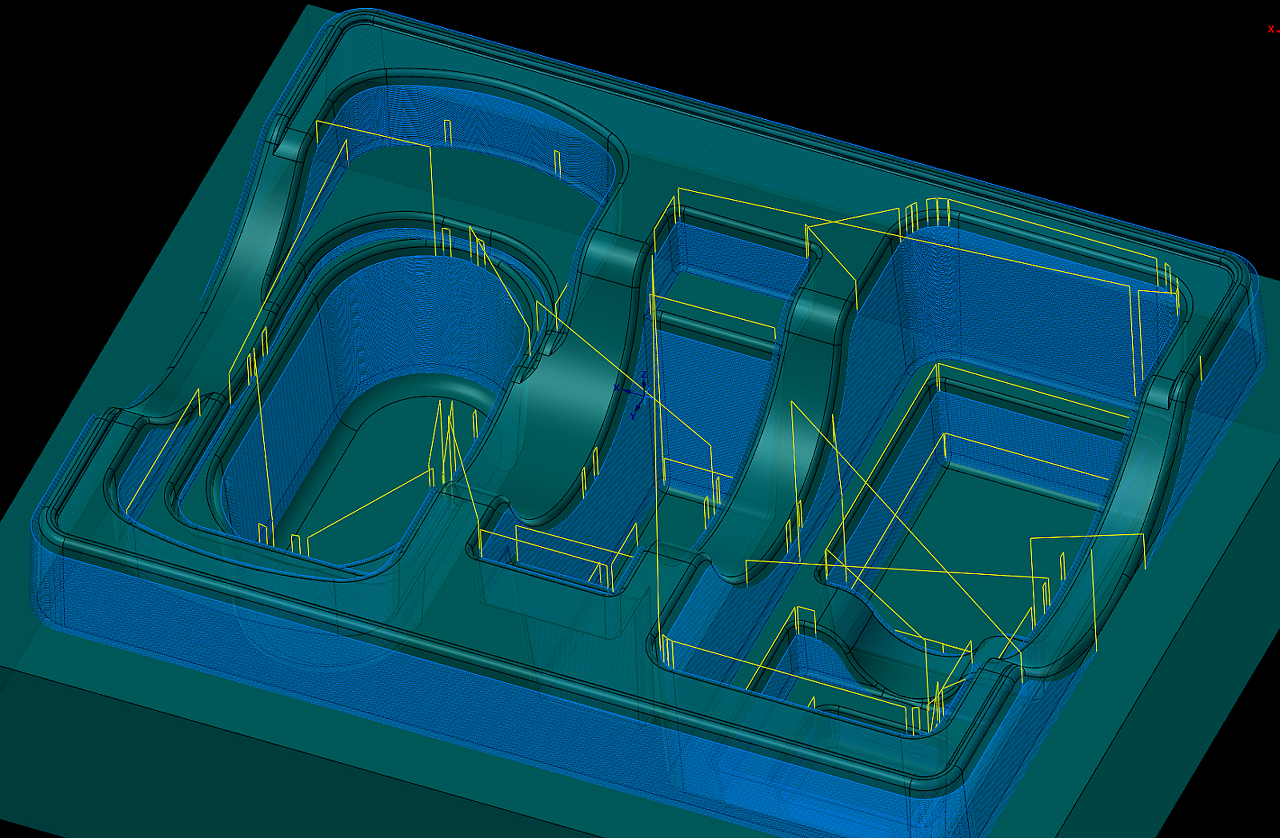
이후 모의 가공으로 가공 형태 을 확인합니다.
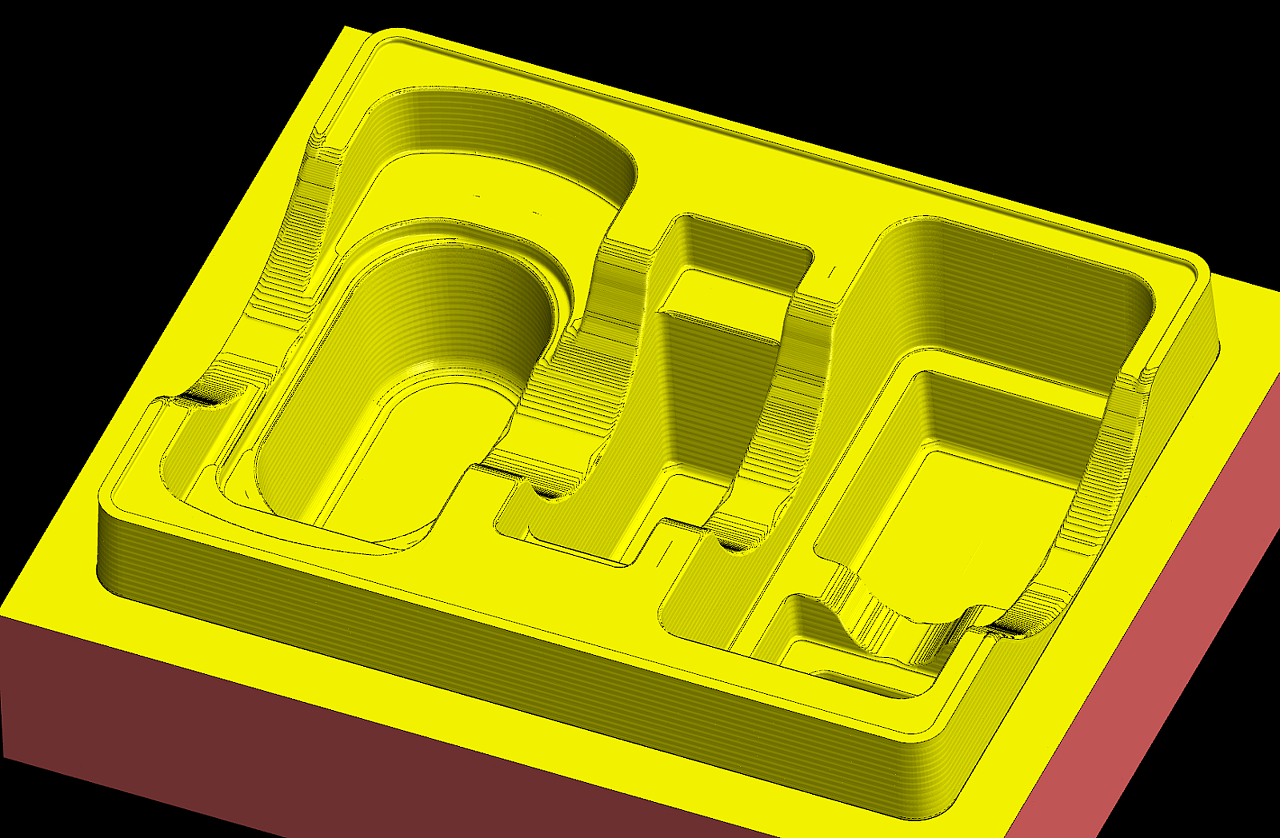
중삭 이후 포켓 측벽면 만 정삭 완료되었습니다.
이후 같은 요령으로 포켓 평면을 스켈롭 가공으로 정삭 해줍니다.
먼저 포켓 바닥 면 만 선택하여 가공 곡면 지정하고 나머지는 체크 곡면 지정 (공구 이송 시 충돌 방지용 / 또는 모든 가공 포켓면 가공 후 공구 이송 높이로 이동 후 이송 처리)을 합니다.
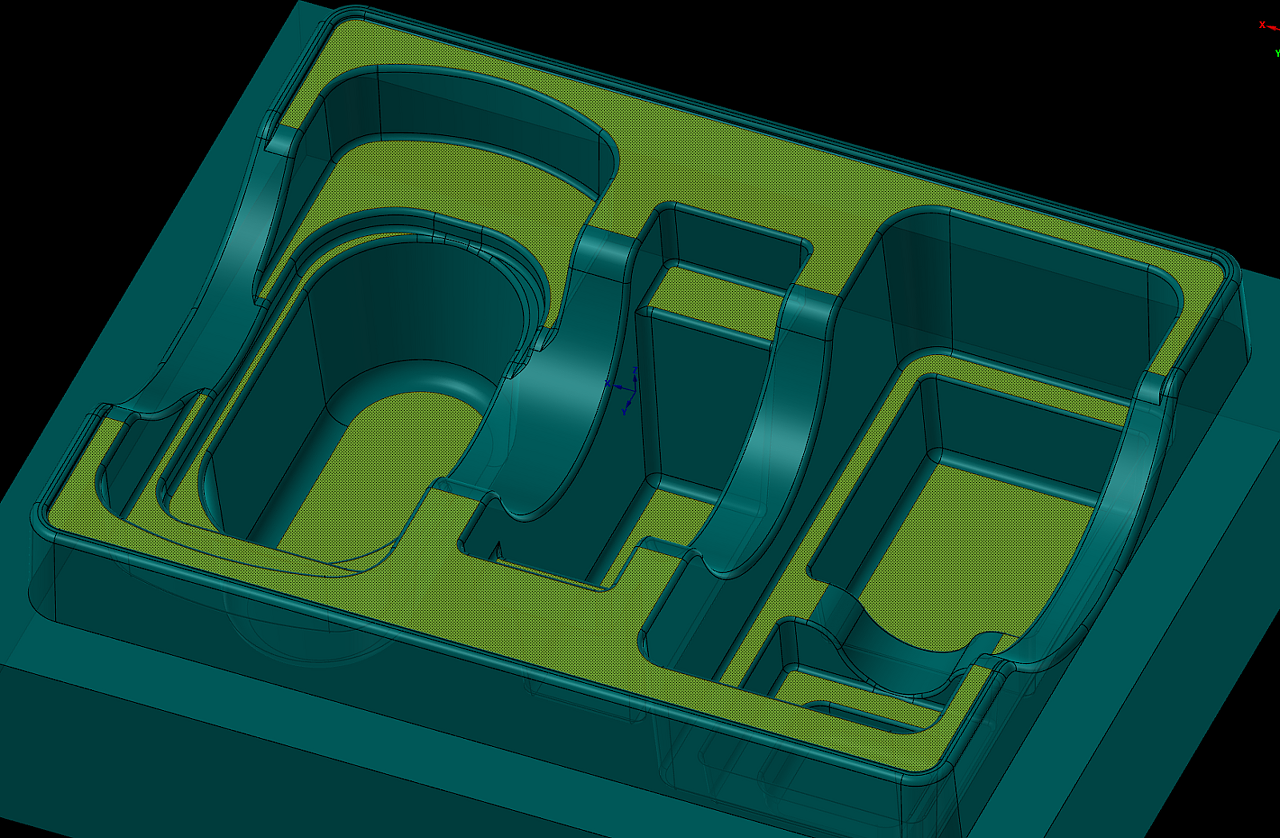
스켈롭 가공 파라미터 설정 은 그냥 무난하게 설정합니다.
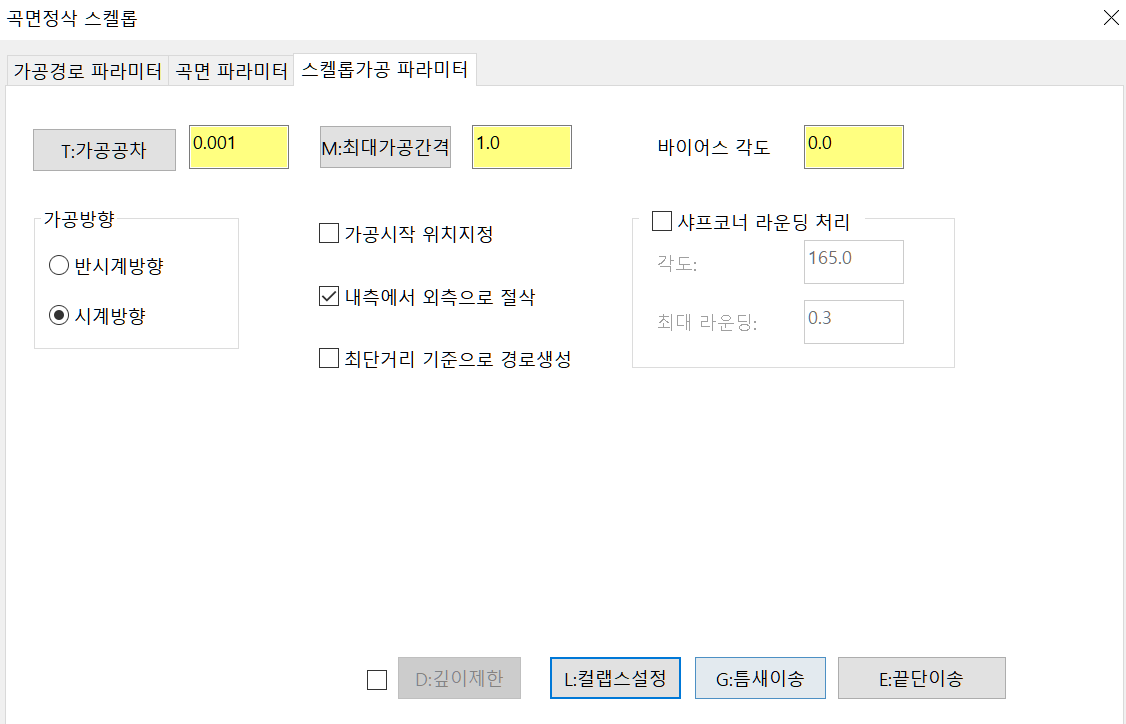
다만 스켈롭 절삭 파라미터 중 공구 중심 영역 설정을 다음과 같이 합니다.
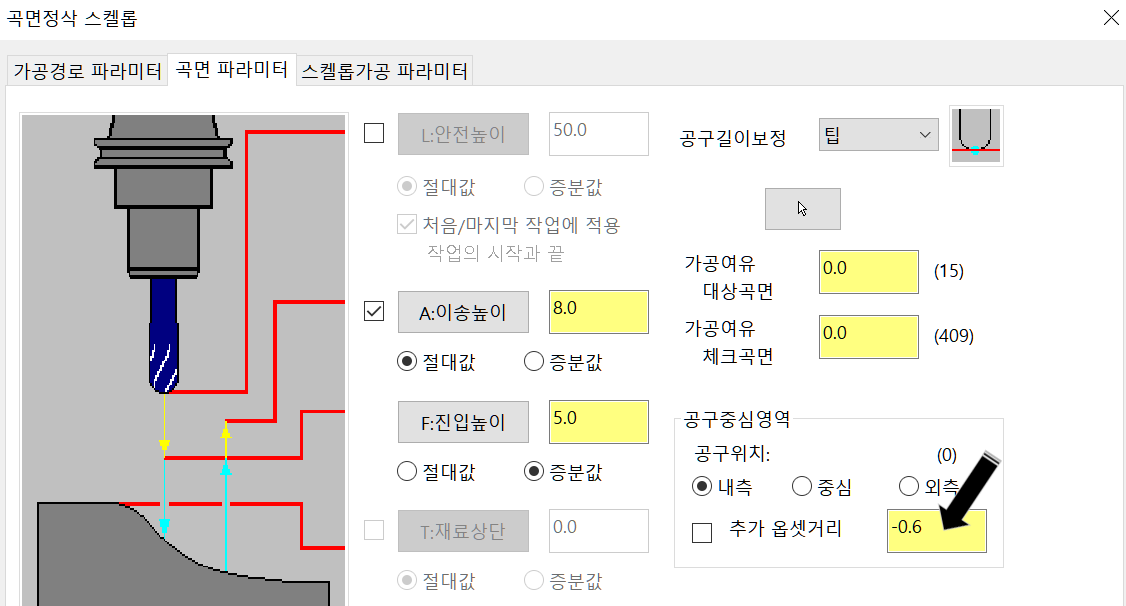
공구 중심 영역 공구 위치 을 내측으로 하고 옵셋 -0.6mm (외측으로) 한 이유는 포켓 측벽과 포켓 바닥 이 만나는 지점을 0.1mm 겹치게 (공구 가공 선 이 발생하지 않게) 절삭하도록 하기 위함입니다.
(이때 이렇게 겹쳐서 가공되어도 이상 없는 형태의 가공 인지 필히 확인하고 또 한 공구 도 평 엔드밀 은 적용 안되며 볼 엔드밀 또는 볼 노즈 (추천) 엔드밀로 하셔야 합니다.)
여기서는 3파이 R=0.5mm짜리 볼 노즈 사용을 전제로 합니다.
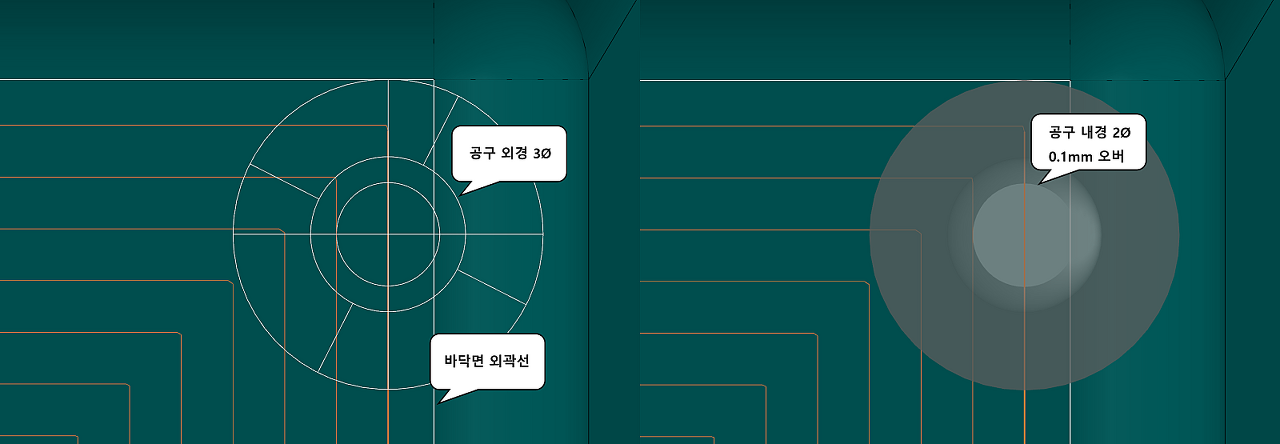
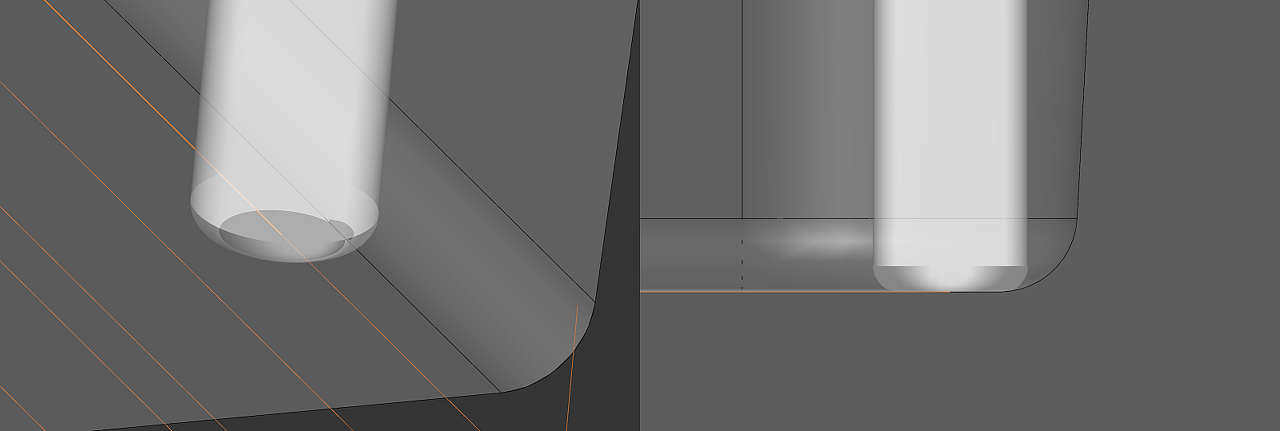
이렇게 하여 포켓 바닥면을 정삭을 마치면 다시 한번 모의 가공을 합니다.
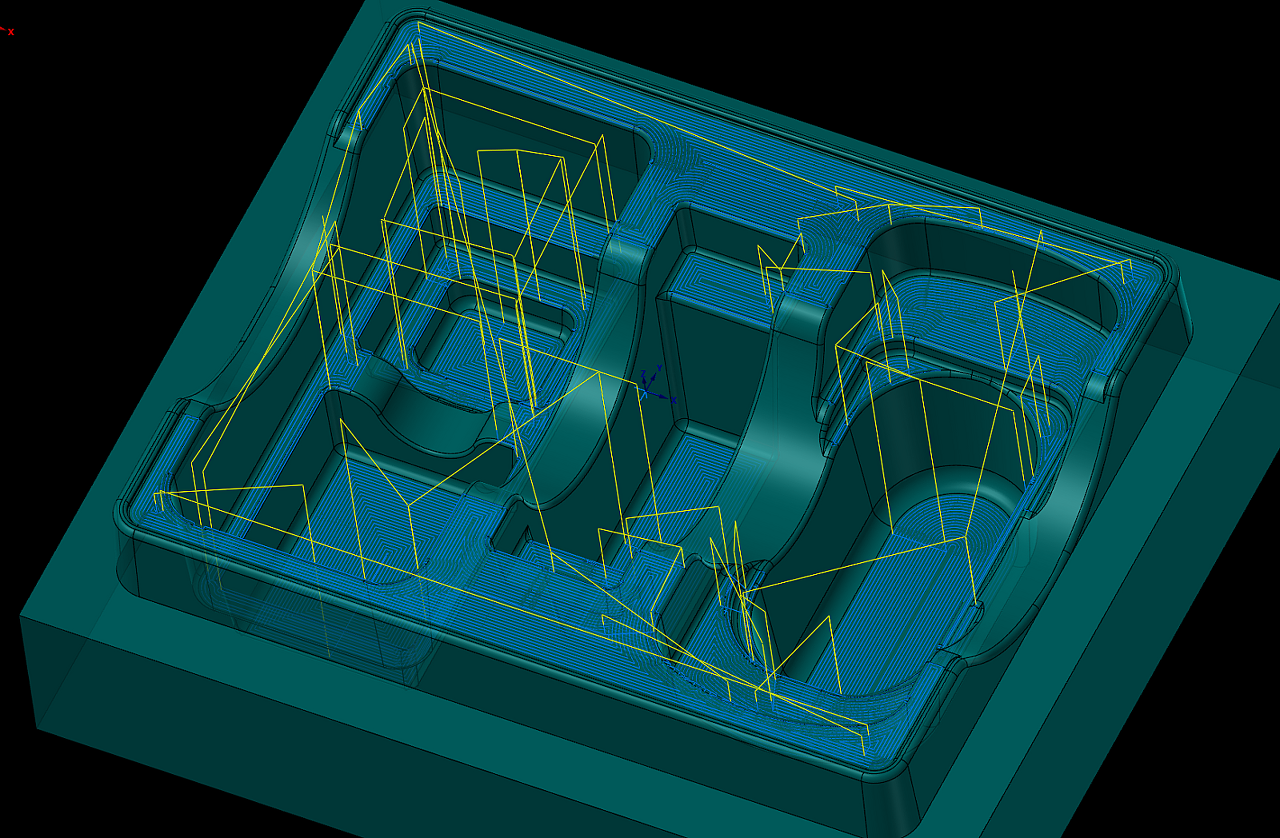
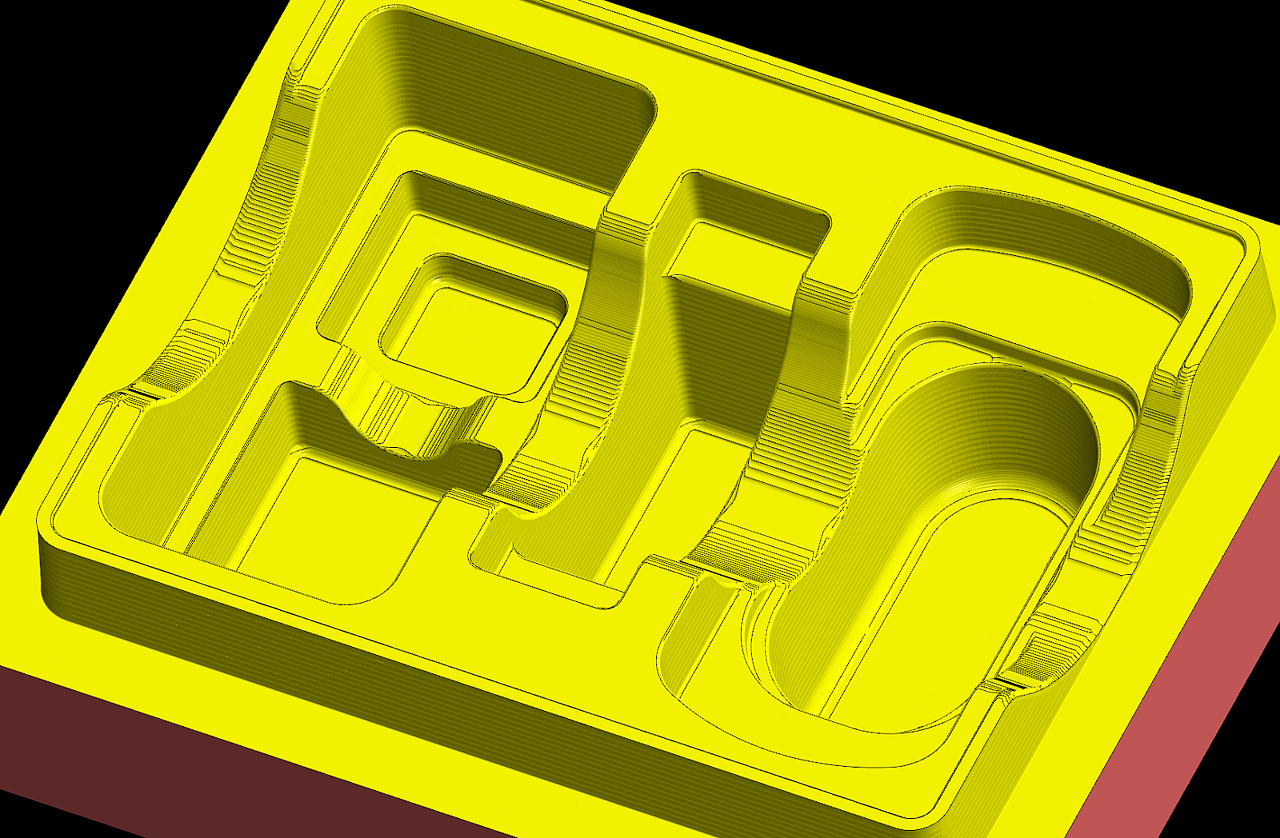
이제 저 모서리 역 알 또는 바닥면 알 그리고 4군데 크게 라운딩 된 부분만 선택하여 가공 곡면 , 나머지는 체크 곡면.. 생략...
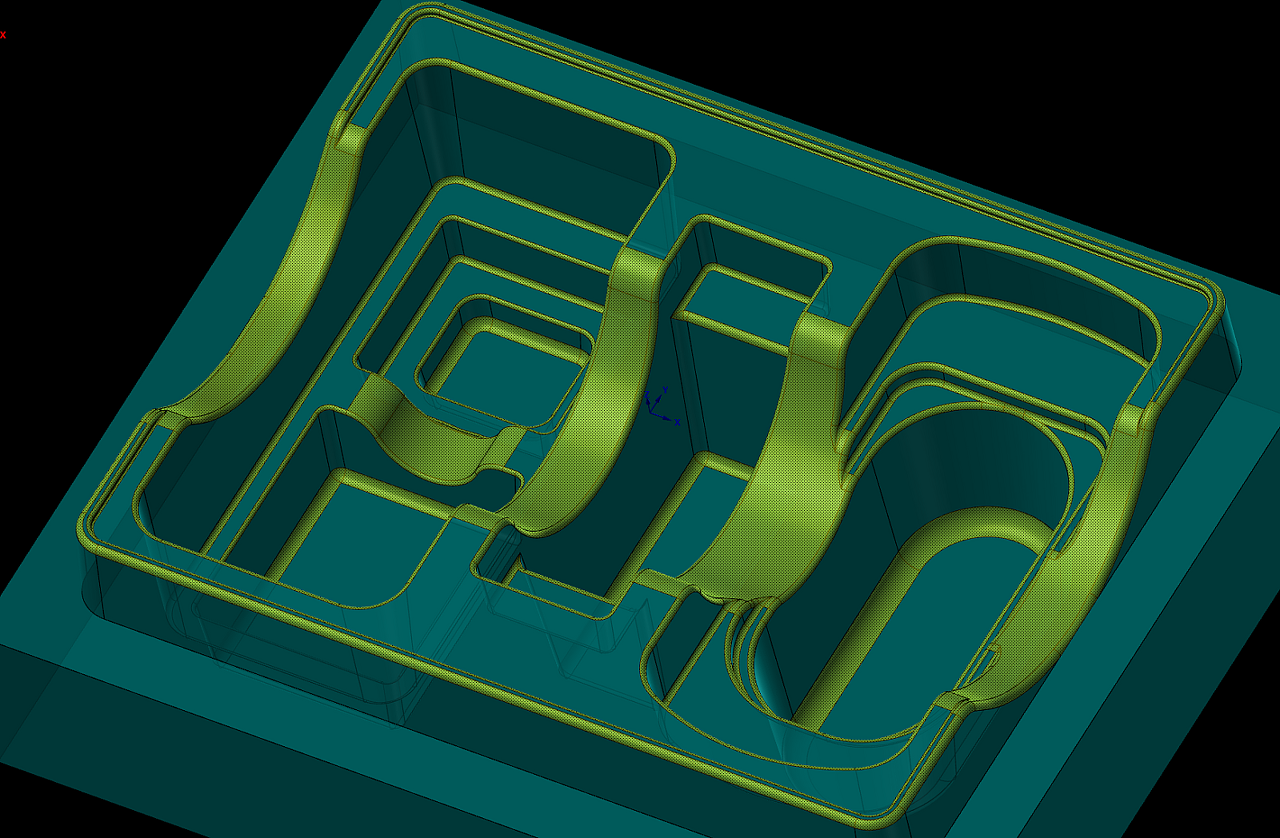

그리고 대망의 마지막 모의 가공을 합니다.
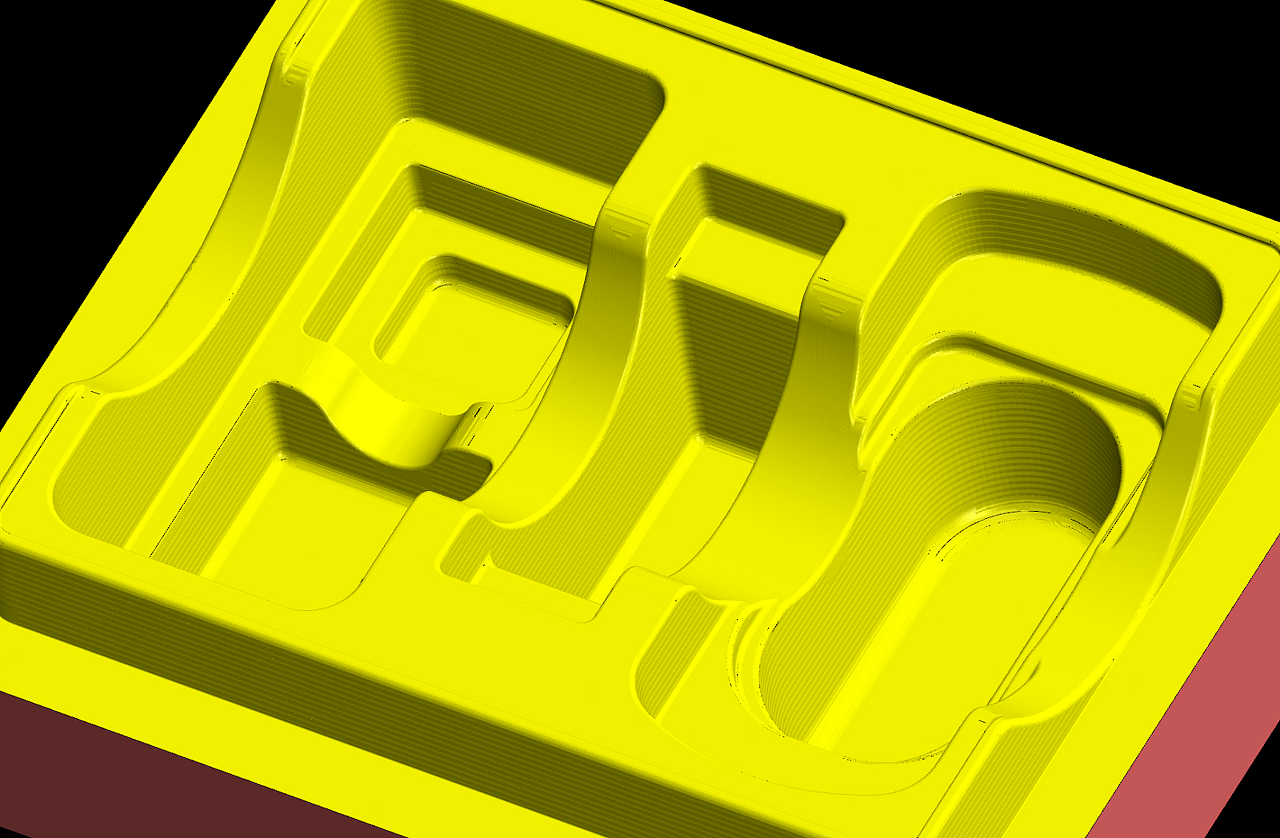
역시 마지막 에는 모델링과 비교 과정을 해봅니다. 비교 오차는 0.05mm
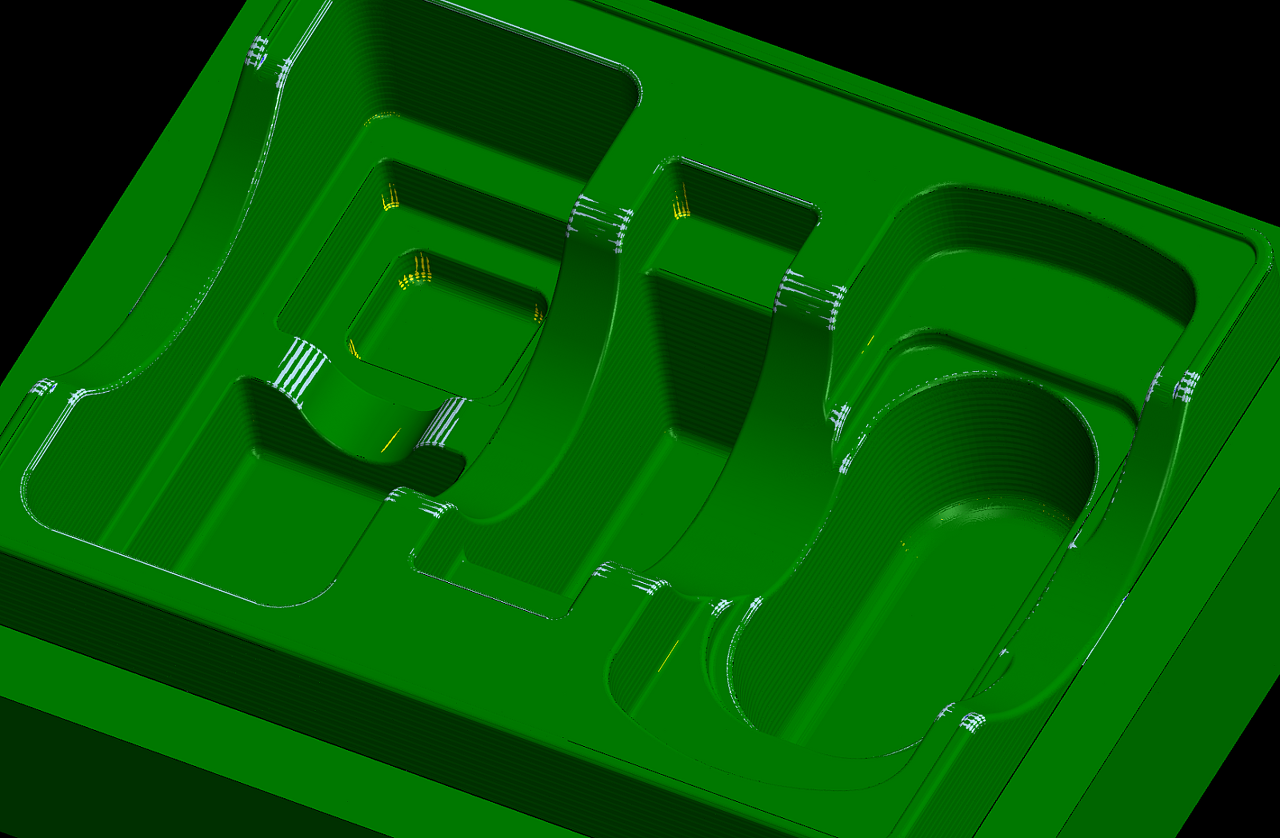
이렇게 마무리하였는데. 1번 안 보다 좀 빠르기는 하지만 해당 캠 연산속도 가 정말 느립니다.... 가공 경로 하나 당 10분 은 보통.... 가공 공차 줄이면 기쁨 두배.... 가 아니고 커피 두 잔 이 됩니다.
3. 4파이 볼 노즈 엔드밀로 전부 스컬롭 가공 처리하는 방법
가공 전체면 을 스켈롭 가공으로 처리 (연산 이 무척 느리다는 단점 이 있음)
뭐 어차피 연산 시간 오래 걸리니 작업자 힘들게 하지 말고 그냥 전체 모델링 잡고 정삭 걸어 줍니다.
짧은 것 여러 개 보다 긴 것 하나로 퉁치자는... 바람직한.... 방식
일단 중삭 까지 는 동일하고 중삭 후 모든 면을 가공 곡면으로 하여 스켈롭 가공으로 마무리합니다.
가공 간격은 0.15mm로 하겠습니다.
(다만 중삭에서 바로 정삭으로 넘어가므로 중삭 시 가능한 가공 여유 을 작게 남겨 놓으셔야 합니다.
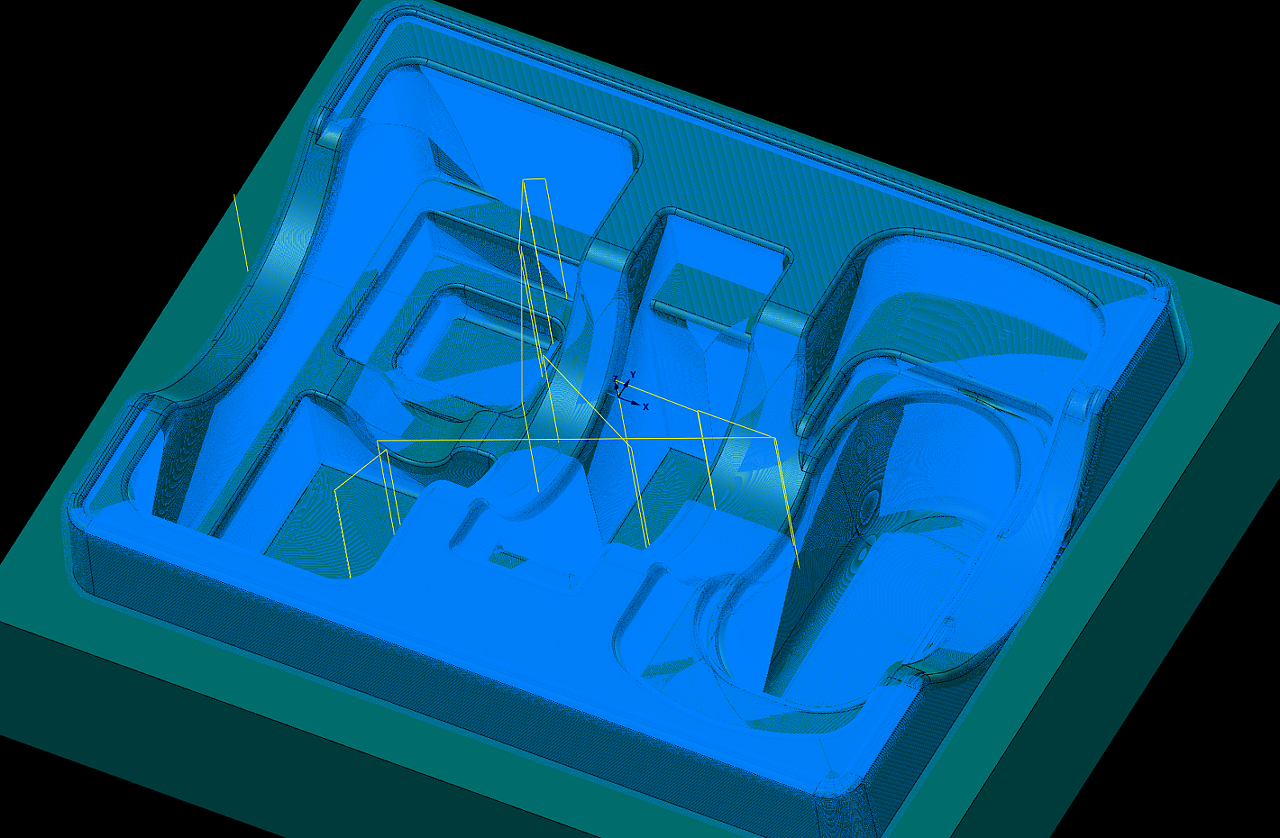
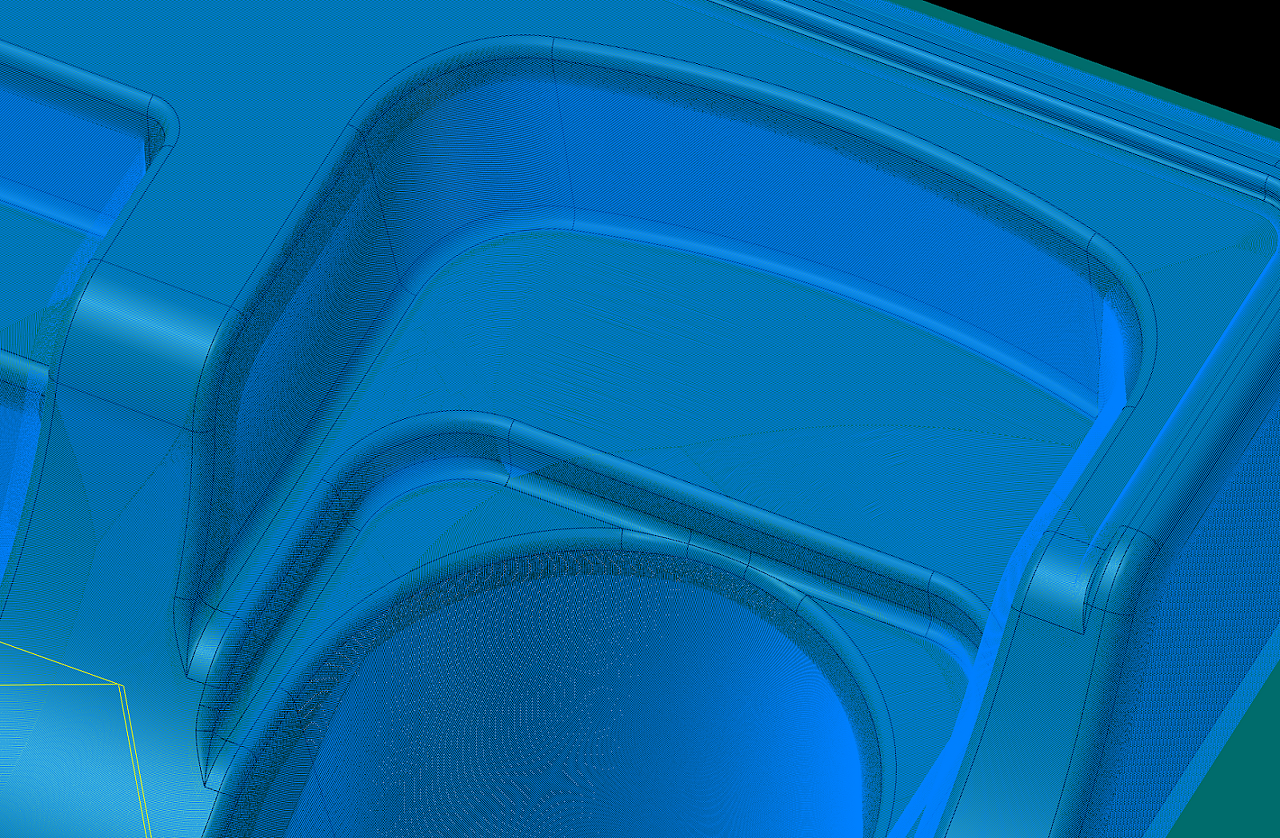
장점 이라 하면 일단 툴패스 작업 시간 이 짧으면서(?) 긴 시간 휴식이 가능하고 사용 공구 종류 을 줄일 수 있고 간혹 가다 같은 정삭 공구인데 서로 가공 영역 겹치는 부분이 살짝 선 이 생기는 문제 을 해결할 수 있습니다.
거기에 저런 포켓 바닥 도 측벽과 같은 가공 간격으로 가공하다 보니 약간 의 툴패스 낭비 요소 가 보이는 단점 이 있어 보입니다.
간혹 가공 시간 이 크게 문제 되지 않는 (어차피 오늘 밤새 무인으로 돌아가니....) 경우 빨리 가공에 들어갈 수 있는 장점 이 있을 수 있습니다.
가공 형태에 좌우되는 방법이라 할 수 있습니다.
단점 은.... 정말 연산 시간 이 길어집니다. 정말 깁니다... 연산 시간 동안 식사 도 가능할 것 같습니다...
이러한 방법 도 있다는 것 을 알아서 선택하시면 됩니다...
그럼 이제 잔삭 하고 마무리하겠습니다.
잔삭 은 그냥 간단하게 해당 곡면 선택하고 나머지는 체크 곡면 지정하여 등고선 가공으로 진행하였습니다.
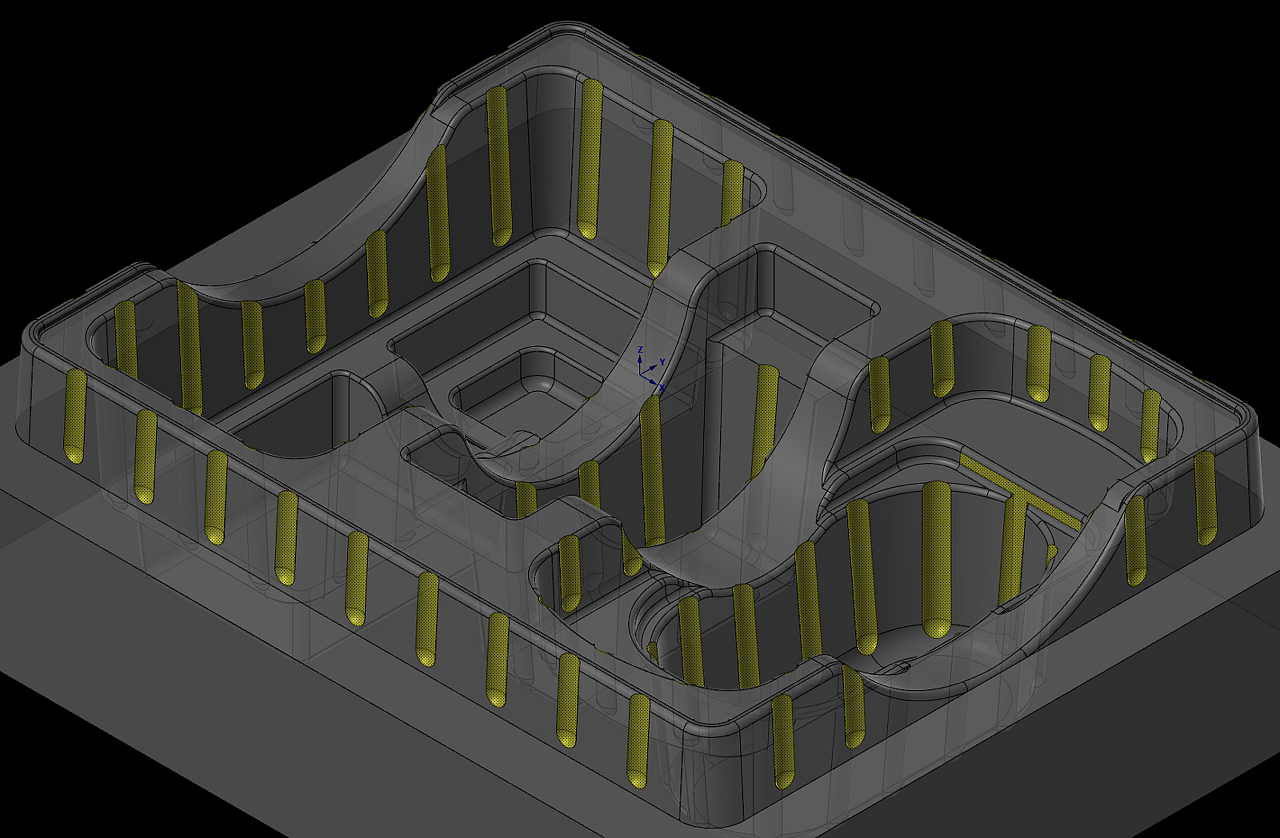
그리고 곡면 등고선으로 툴패스 생성해 보았습니다.
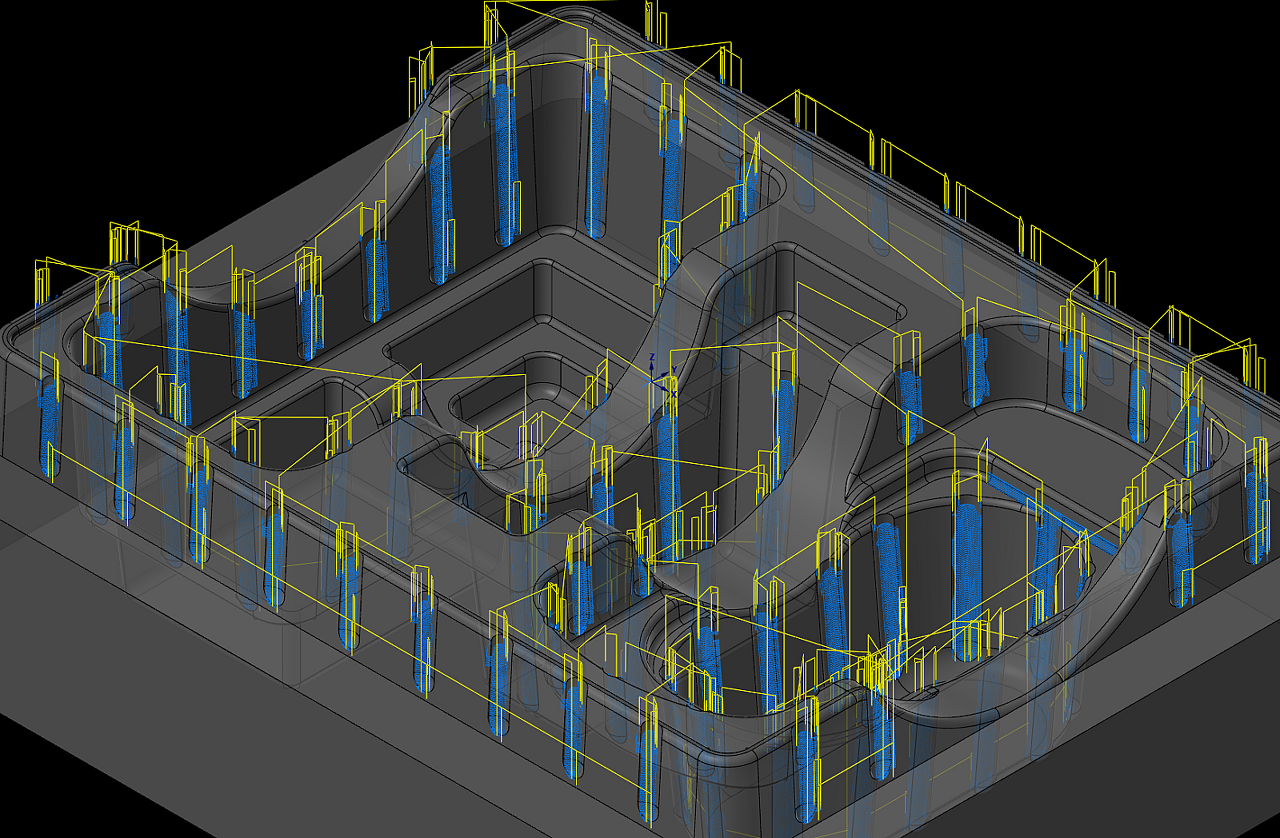
그리고 모의 가공....
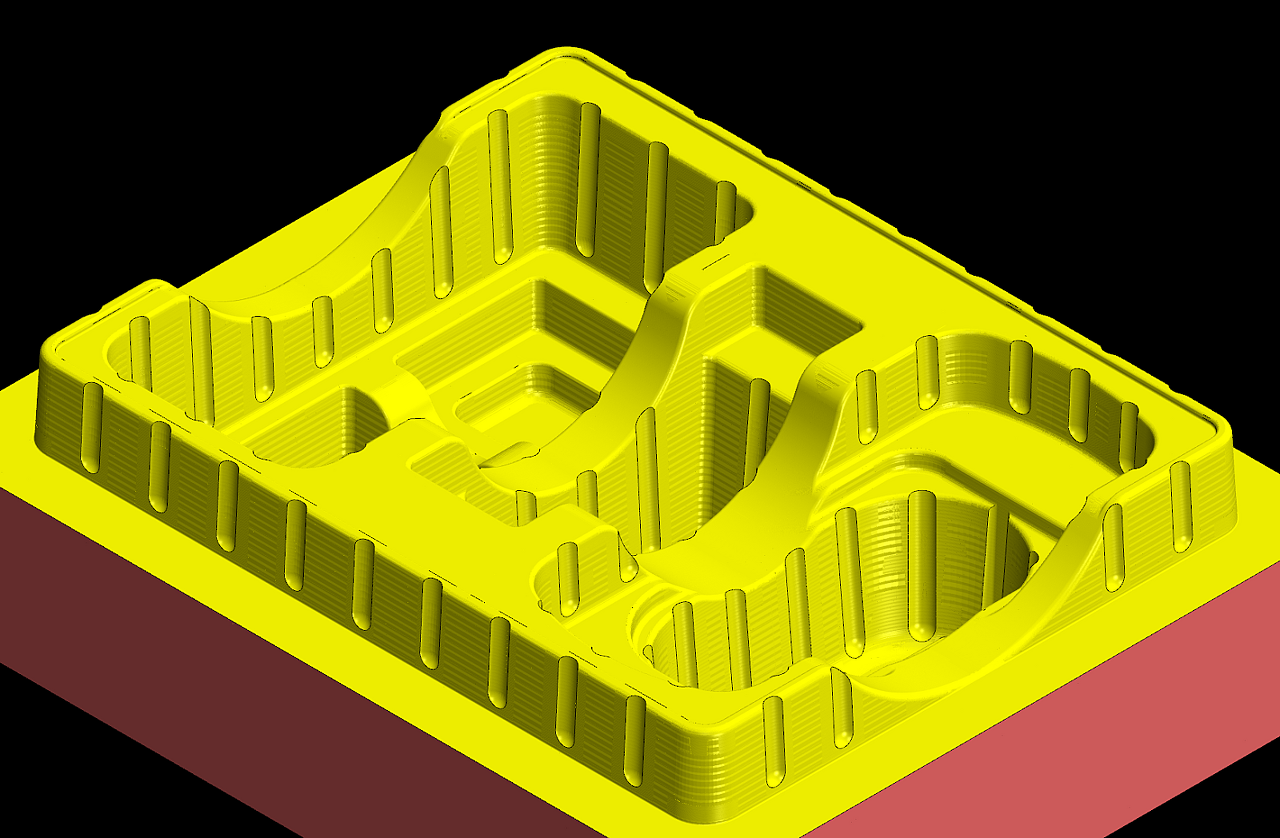
이렇게 해서 우선 간단하게 진공 성형 형태 금형 툴패스 생성을 알아보았습니다.
원래 목적이 등고선 툴패스 내는 팁 이 었는데..... 계속 자료 찾고 대응해 보니깐 처음 의도와 안 맞아서 졸작으로 우선 종료합니다.
그래도 하나 얻은 것은.... 해당 캠 연산 속도 가 너무 한다 생각 드네요.... 위 툴패스 을 전부 재생성하면 30분 에서 거의 한 시간 연산합니다. (세잔 5800H ram 16g 시스템)
그래서 여러 가지 시도해보려다가 연산 시간 때문에 포기하였습니다.
그리고 일단 이 글을 마지막으로 당분간 눈팅자로 활동하겠습니다.,
원래 해야 할 머시닝 기초 관련 책(출판물 아닙니다.) 진도 가 너무 안 나가서 그나마 남는 시간에 여러 가지 해 보아야 하는 데 못 하고 있어 이제 이쪽에 전념하고 싶습니다..
그래서 그동안 감사하였습니다.
해당 캠이 제 컴퓨터 괴롭히는 현장....
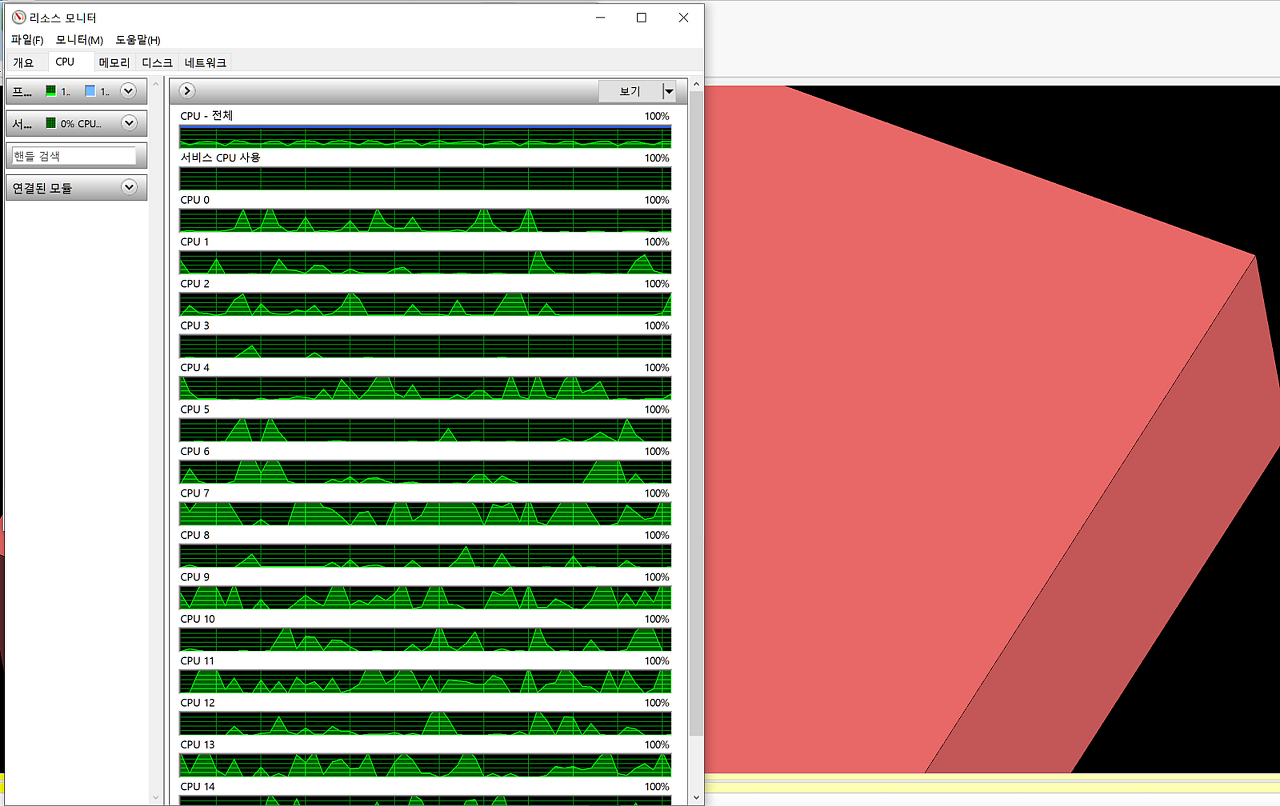
'마스터캠 관련 한 여러 이야기' 카테고리의 다른 글
마스터캠 모의가공시 좀더 실가공 에 가깝게 연습하기-(2D 바이스작업) (0) | 2022.05.22 |
---|---|
바이스 스톱퍼 가공과정 설명기 (재료설정 교육자료용) (0) | 2022.05.22 |
3D 가공 과정 에 대한 짧은 글 입니다. (금형 형태 가공) -3 (0) | 2022.05.21 |
3D 가공 과정 에 대한 짧은 글 입니다. (금형 형태 가공) -2 (0) | 2022.05.21 |
3D 가공 과정 에 대한 짧은 글 입니다. (금형 형태 가공) -1 (0) | 2022.05.21 |