안녕하십니까?
저번에 이어 금형 형태 가공 중삭에 대하여 마무리하겠습니다.
저번 황삭 가공 관련 설명 중 한 가지 누락된 것 이 있어 잠깐 설명하고 진행하겠습니다.
황삭 포켓 가공 시 가공 깊이 (가공 여유 적용 여부 & 정삭 가능 깊이 까지 가공 여부)에 대한 애기인데 황삭 포켓 가공 시 가공 여유 (가공 곡면 대상 : 여기서는 0.15mm)을 지정했는데 실제 가공 경로 생성 시 바닥면 (평면) 이 미절삭 되는 현상에 대한 애기입니다. (중삭 가공의 필요성 제시 을 위한)
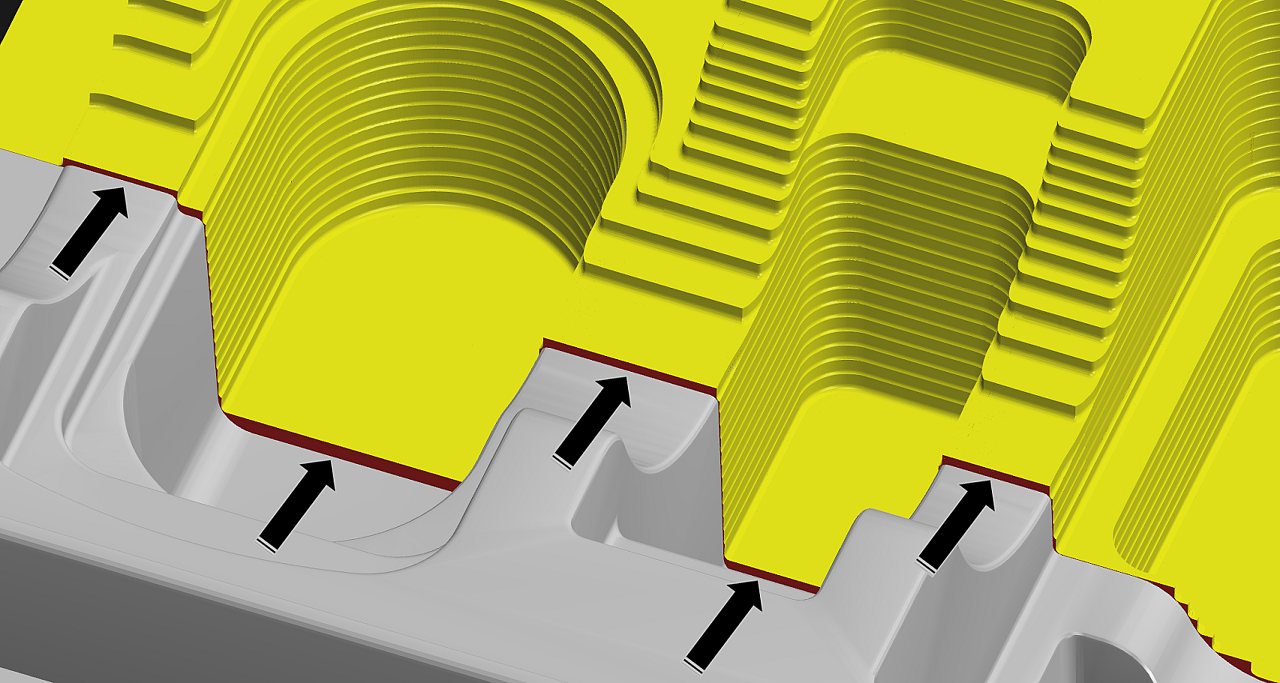
화살표 표시와 같이 바닥 면에 많은 양의 미절삭 부분 이 남습니다.
그런데 아마도 이러한 글을 보시고 "어 나는 그렇게 안되고 가공 여유 부분까지 가공 툴패스 가 잘 나오는데.." 하시는 분 들 이 있을 것 같아 잠시 설명합니다.
우선 아래와 같은 두 가지 포켓 가공 형태 가 있습니다.
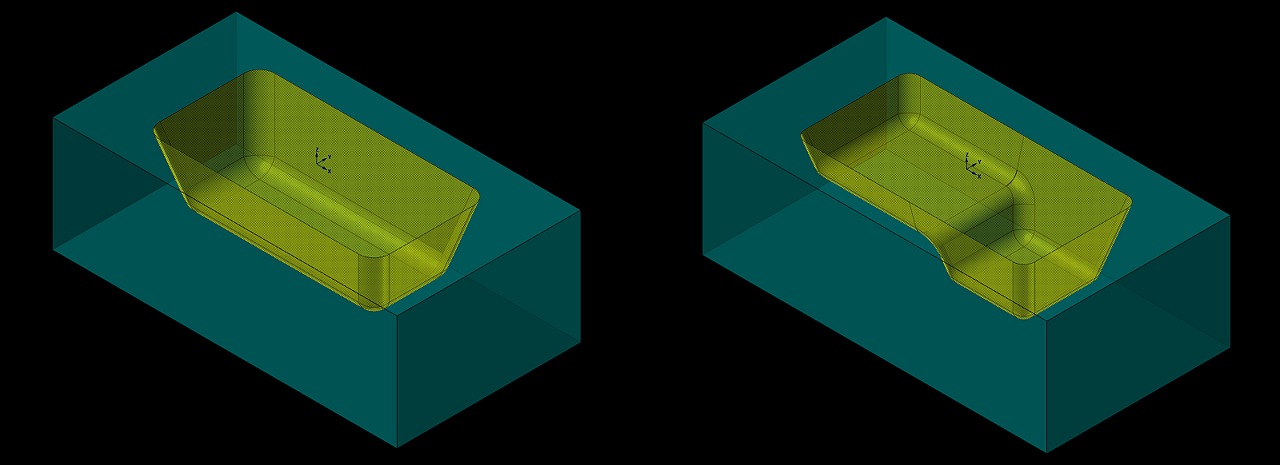
크게 구분하여 포켓 바닥면 이 한 개인 경우와 다수인 경우로 구분합니다.
(단 바닥면 이 평면 이 아닌 경우는 별도입니다.)
우선 포켓 바닥면 이 하나인 경우 을 알 아보겠습니다.
왼쪽의 한 개 바닥면 포켓을 황삭 곡면 포켓 을 실행해 보았습니다.
우선 공구는 8파이 R1 볼 노즈 엔드밀 사용이며 가공 간격 (Z : 3.0mm)이며 포켓 깊이 는 Z -30.0mm입니다.
1안 : 가공 깊이 을 제한하지 않고 포켓 가공
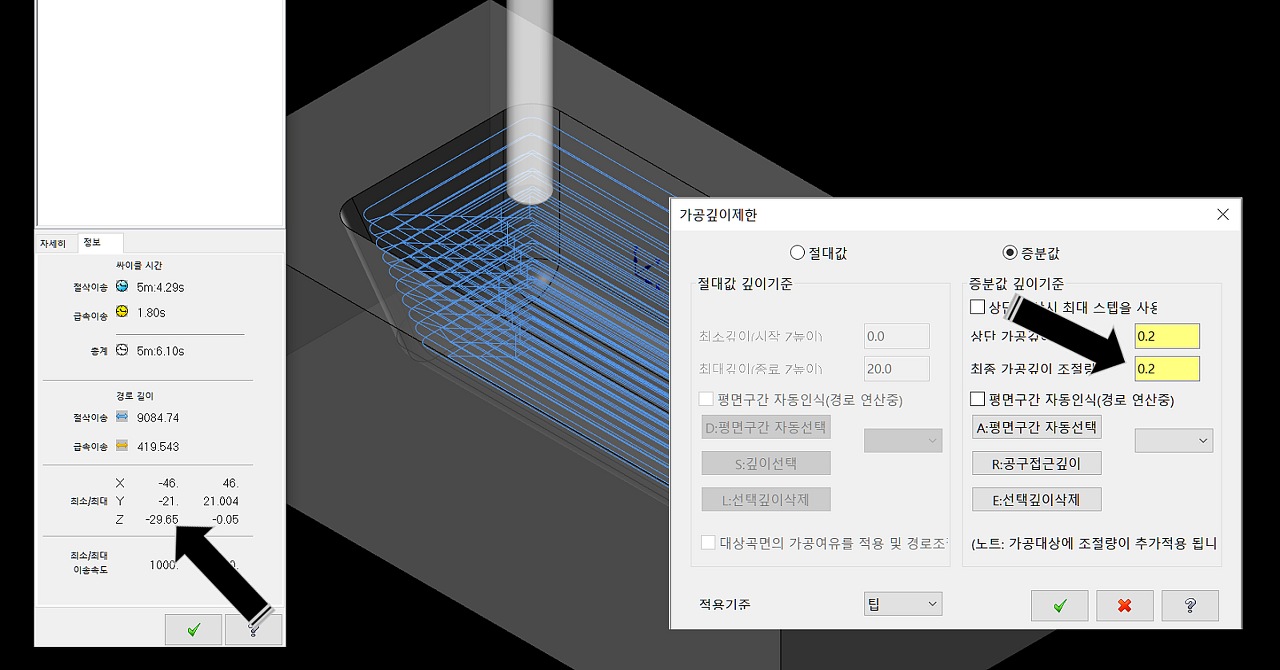
* 다른 툴패스 와 달리 황삭 포켓 가공 은 가공 깊이 제한 기능 이 별도의 적용 체크 란 이 없어 항상 사용된다고 봐야 하나 위 증분 값 적용이 항시 (특별한 지정 없는 경우) 적용되는 항목이라 제한하지 않는 다고 표시합니다.
위 와 같은 설정에서 황삭 포켓 가공을 실시 하자 최대 가공 깊이 가 29.65mm로 되어 있습니다.
(포켓 깊이 30.0 , 가공 여유 0.15)
그럼 포켓 바닥 면에 0.35mm 미절삭 부분 이 남는다는 것인데 가공 깊이 계산 은 다음과 같이 이루어집니다.
가공 포켓 깊이 30.0 - (가공 여유 0.15 + 가공 깊이 제한 증분 값 0.2) = 30.0 - 0.35 = 29.65mm입니다.
2안 : 가공 깊이 제한 설정을 절댓값으로 지정 (평면 구간 자동 인식 미 체크)
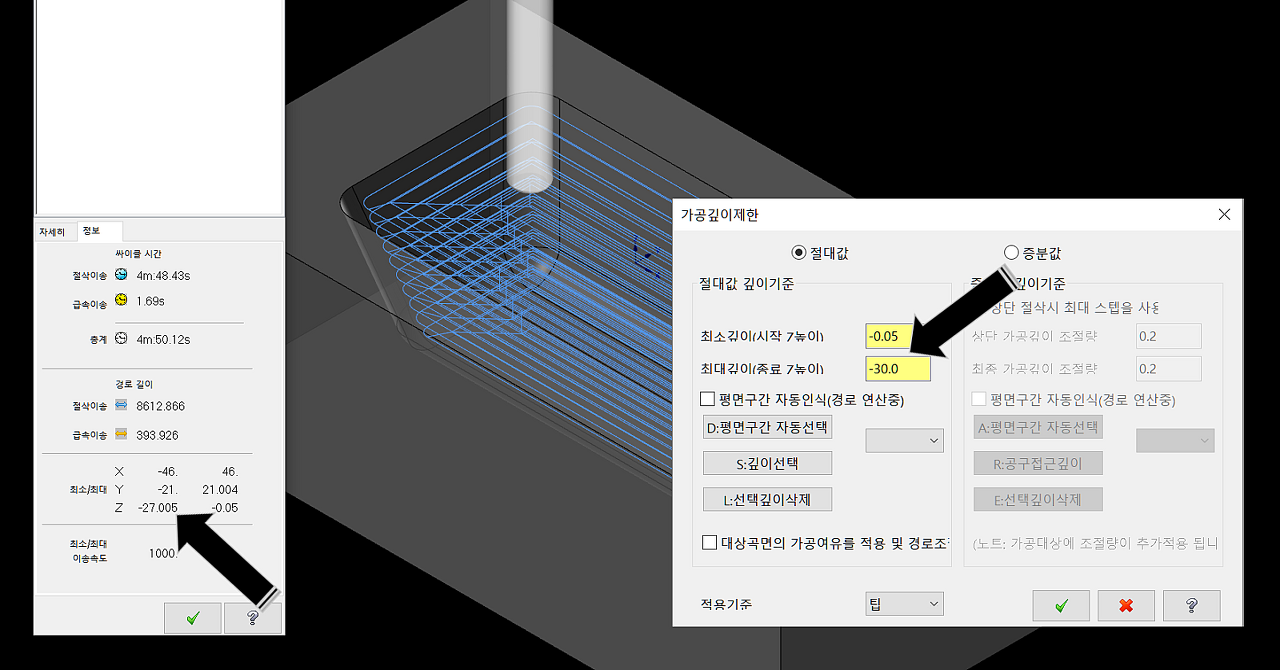
위 와 같은 설정 시 가공 깊이 을 절대 값으로 -30.0이라고 제한 (지정) 하였으므로 포켓 가공 경로 생성 시 단순하게 최소 깊이 시작 (-0.05)에서 최대 깊이 종료 (-30.0)을 가공 깊이 간격 (3.0)으로 나눘어 버립니다.
그래서 단순히 -0.05에서 -30.0 = 29.95 / 가공 깊이 간격(3.0)을 하면 마지막 단계 값이 30.05 가 나오므로 최대 깊이 값을 오버 (과절삭) 하므로 이 을 피하기 위하여 여기서 다시 가공 깊이 간격 (3.0) 을 뺀 -27.0 이나 와야 합니다.
* 그런데 왜 27.005로 출력되는지 는 좀 더 공부합니다.
그러므로 이경우 포켓 바닥면 이 기공 깊이 간격 (3.0) 만큼 미절삭 부분 이 남는 것입니다.
*즉 이렇게 가공 깊이 값을 제한하면 가공 여유 값이 무시됩니다. (포켓 바닥 평면에 한하여입니다.)
사실 무시라고 보다 여기서 가공 여유 값을 적용하면 계산 이 어려워지므로 제외한 듯합니다.
사실 황삭인데 30.0 / 3.0 하면 바로 마감 깊이 가 되므로 마지막 한 단계 을 생략한 것입니다.
가공 포켓 깊이 30.0 / 가공 깊이 간격 (등분) 3.0) = 30.0 / 3.0 등분 - 마지막 마감 깊이 제외 = 27.0mm입니다.
3안 : 가공 깊이 제한을 설정할 때 가공 여유 (0.15)을 감안하여 가공 깊이 제한함 (평면 구간 자동 인식 적용)
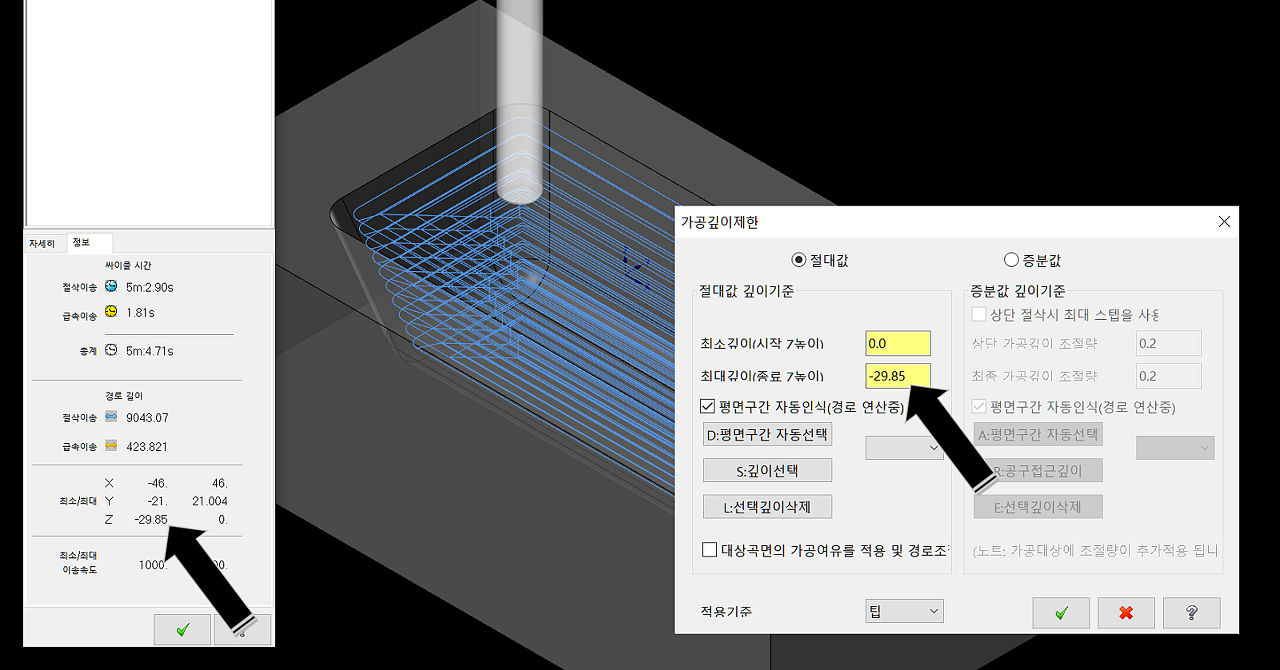
위 와 같은 경우는 가공 여유 지정과 관계없이 가공 깊이 제한 설정 시 최대 가공 깊이 종료 값을 가공 포켓 최대 깊이 에서 가공 여유 을 뺀 값 을 입력 (30.0 - 0.15 = 29.85) & 평면 구간 자동 인식을 체크합니다.
여기서 평면 구간 자동 인식을 체크한 이유는 포켓 바닥 면 깊이 을 인식시키기 위한 설정입니다.
그러므로 가공 툴패스는 가공 깊이 0.0 ~ 29.85을 가공 깊이 간격 (3.0)으로 등분하여 툴패스 을 생성합니다.
가공 포켓 깊이 30.0 & 최대 깊이 종료 제한 (29.85) / 가공 깊이 간격 (등분) 3.0) = 30.0(29.85) / 3.0 등분 = 최대 가공 깊이 29.85mm입니다.
4안 : 가공 깊이 제한을 설정할 때 대상 곡면 가공 여유 을 적용 및 경로 조절을 체크하여 가공 여유 (0.15)을 적용하게 함 (최대 가공 깊이 는 30.0 적용)
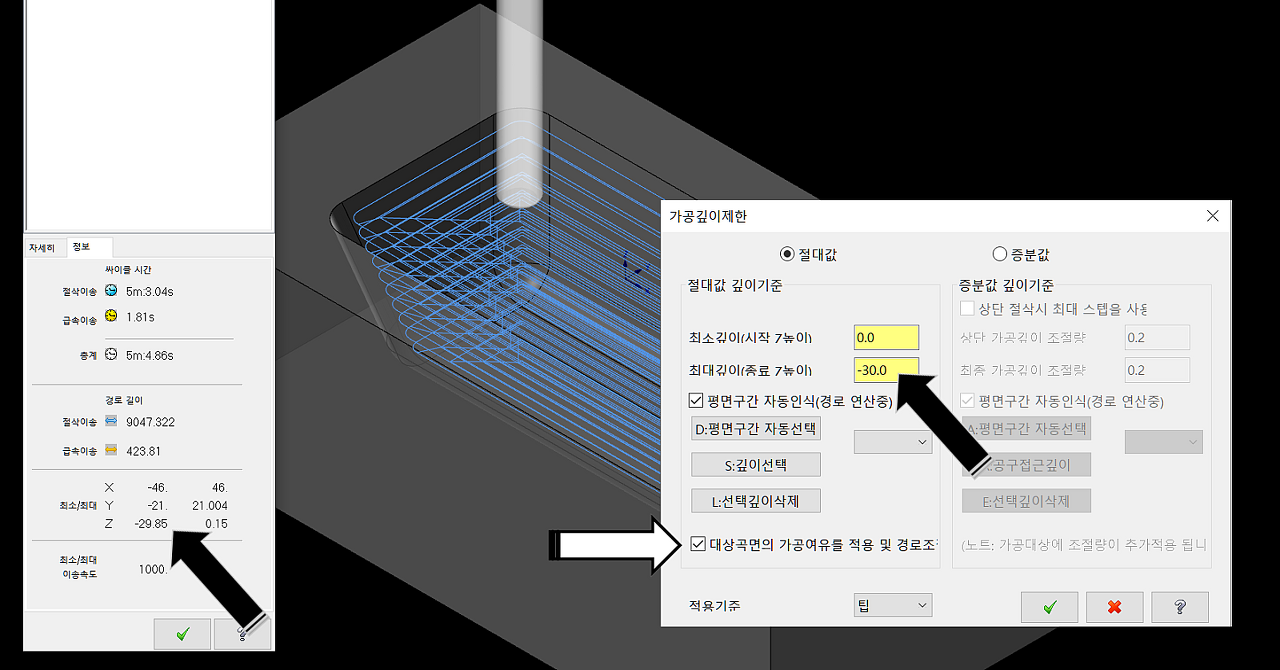
최종 보스
가공 깊이 제한 작용 시 최대 깊이 종료 값 은 실 포켓 마감 깊이 (30.0) 적용 , 평면 구간 인식 적용 , 대상 곡면의 가공용 여유 을 적용 및 경로 조절 적용.
알고 보면 쉬운 정답 : 그럼 가공 여유 을 적용 되게 툴패스 연산하면 되잖아...
설명 생략하겠습니다. 제목이 정답이라.....ㅠㅠ
가공 포켓 깊이 30.0 & 가공 여유 0.15 적용 / 30.0 - 0.15 = 29.85 / 가공 간격 3.0(등분) = 최대 가공 깊이 29.85mm입니다.
이렇게 포켓 내 한 개 의 바닥 (평면) 이 있는 경우 말고 여러 개 의 (각각 포켓 바닥 높이 가 다른) 포켓 바닥 이 있는 경우 도 동일하게 생각하시면 됩니다.
두 가지 예 을 보여 드리면.
우선
1안 : 가공 깊이 제한을 설정할 때 가공 여유 (0.15)을 감안하여 가공 깊이 제한함 (평면 구간 자동 인식 적용)
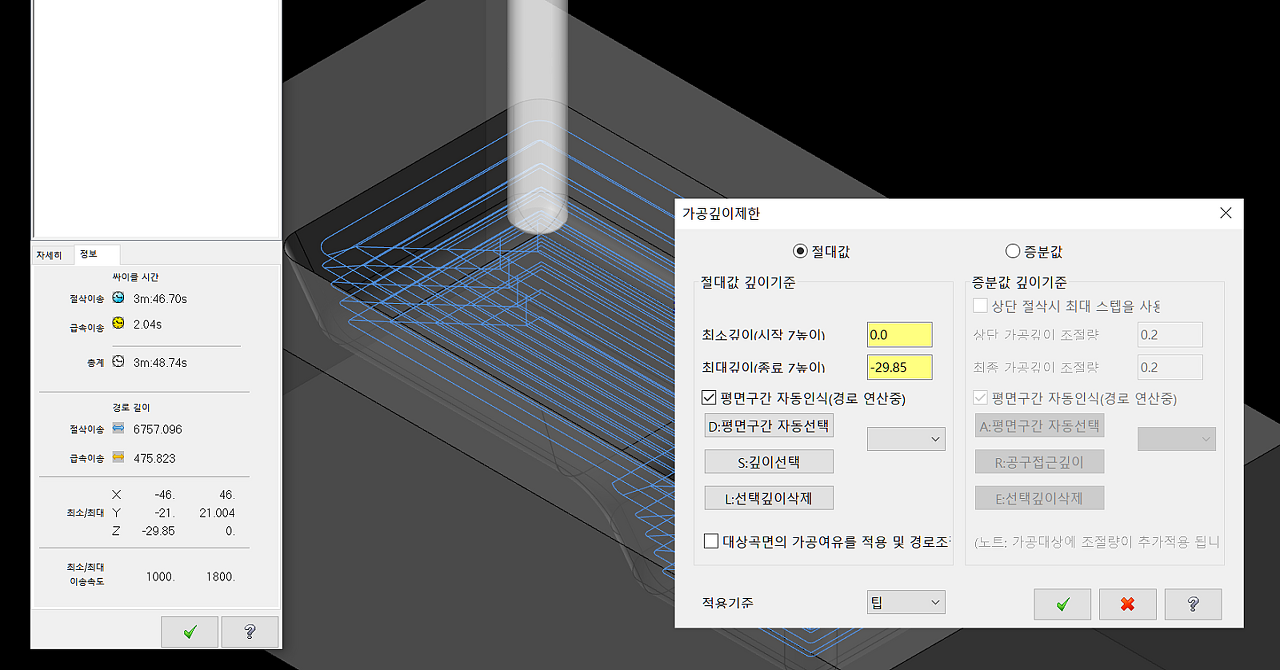
위와 같이 가공 여유 을 감안해서 최대 가공 깊이 (-29.85)을 설정하고 평면 구간 자동 인식을 체크하면 최대 가공 깊이 가 -29.85mm가 됩니다만....
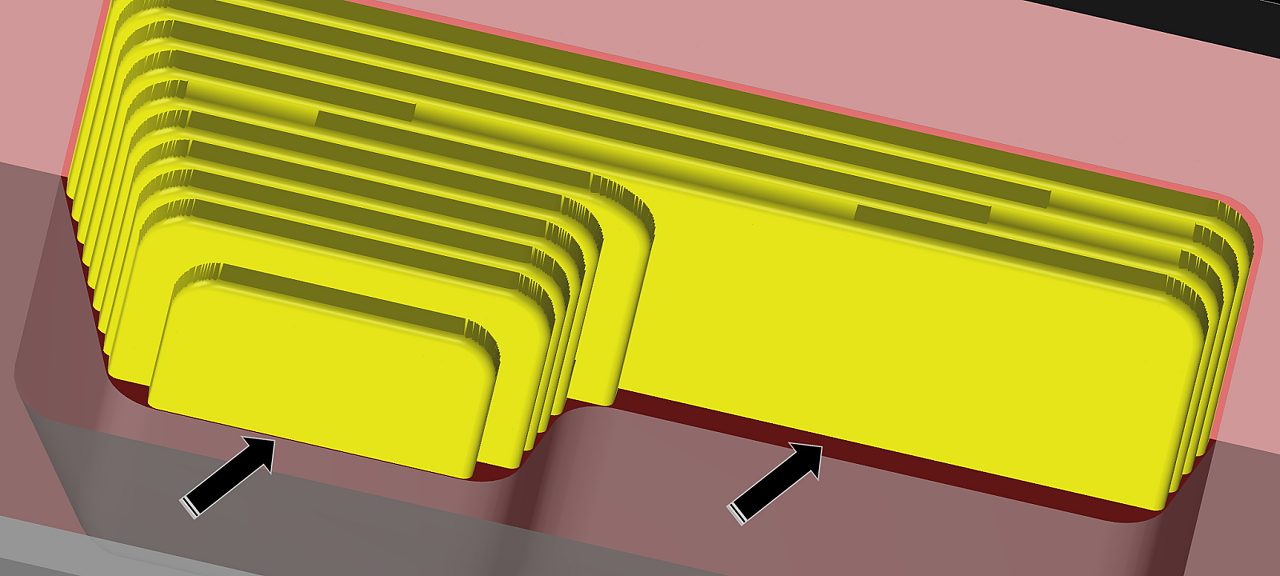
모의 가공을 해보면 최하단 포켓 바닥 은 제대로 가공 여유 가 남는 깊이(-29.85)까지 가공되나 중간의 포켓 바닥 (-14.0) 은 가공 깊이 간격에 따른 등분된 간격으로 미절삭 됩니다.
그러니깐 그냥 좋다는 것 은 다 집어넣은 위 4안으로 작업합니다.
2안 : 가공 깊이 제한을 설정할 때 대상 곡면 가공 여유 을 적용 및 경로 조절을 체크하여 가공 여유 (0.15)을 적용하게 함 (최대 가공 깊이 는 30.0 적용)
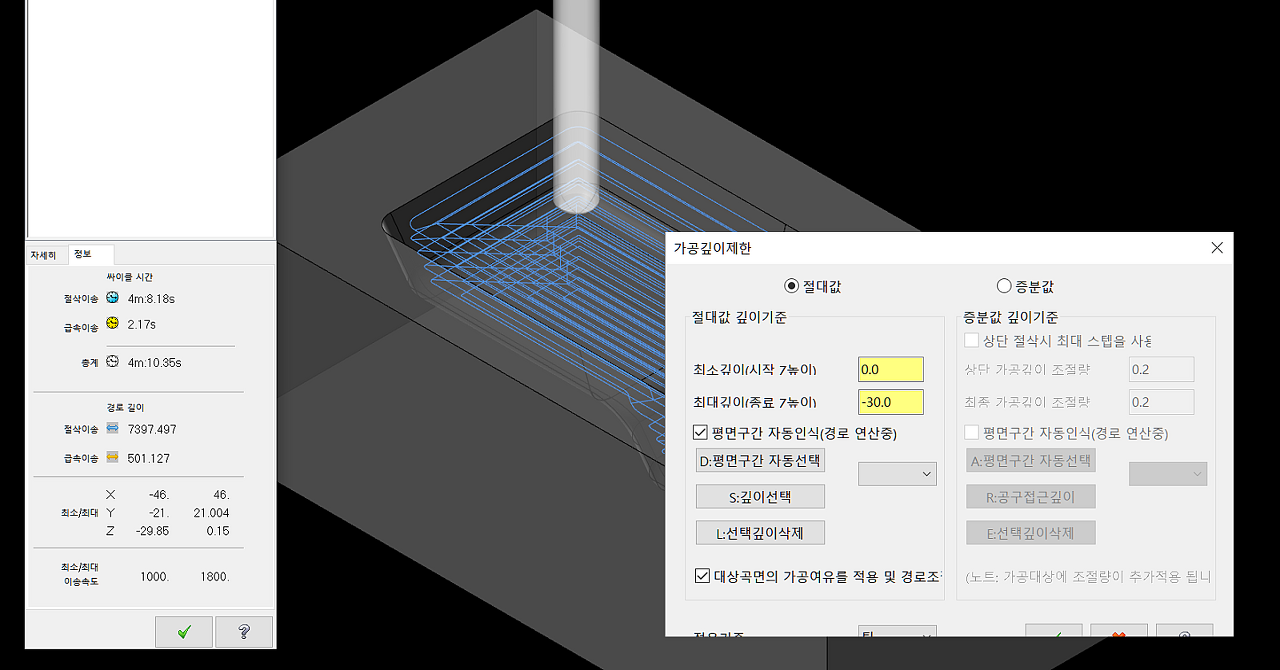
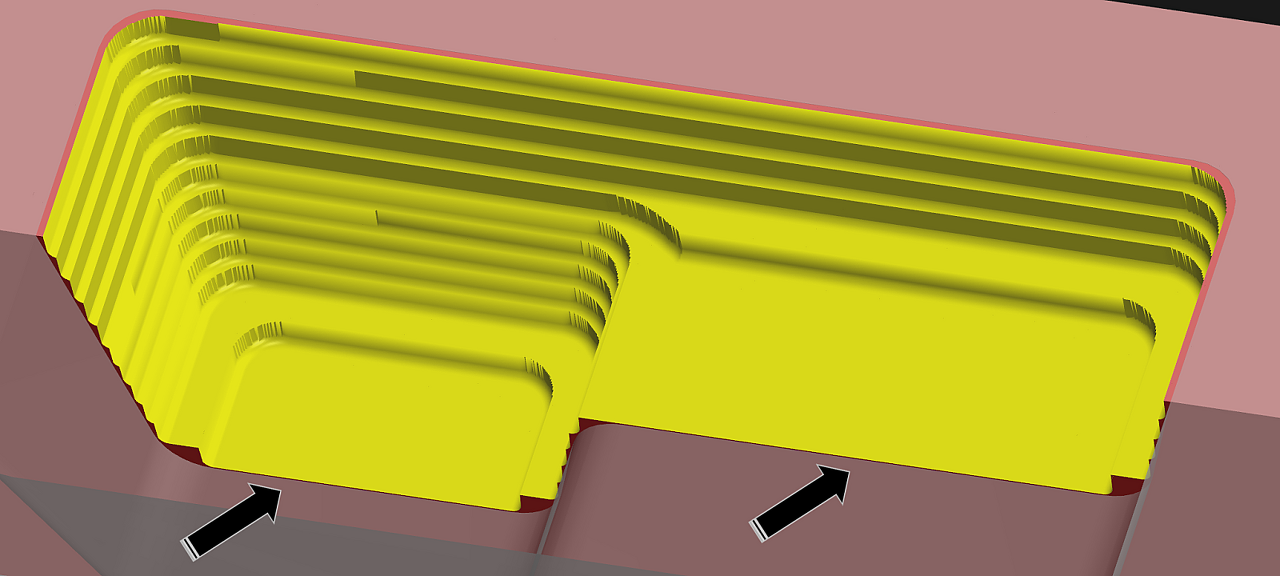
모의 가공 내용 은 상하단 포켓 부분 모두 가공 여유 을 유지 한 깊이 까지 가공됩니다.
* 다만 이는 황삭 공구 을 사용 한 황삭 가공 과정 이므로 너무 타이트 한 가공 여유 (작은 값)을 적용 시 황삭 공구의 공구 규격의 미비함 (특히 커터 공구 경우) 이 있으므로 적용하는 것 을 지향하며 경우에 따라 이러한 점 이 있으므로 그때 가공 환경에 맞추어 작업하시기 바랍니다.
* 다시 말씀드리지만 어디까지 나 참고 사항입니다.
그럼 이제 중삭을 들어가겠습니다.
중삭의 의미는 중간 컷 이라는 의미 인데... (실제 영어 도 중간 컷(Mid Cut) 이라고 구글 변역 이라고 나오지만 해당 캠 에서는 RestMill (잔여분 가공 : 다 가공 못 한 부분 가공) 으로 나오며 중삭 이라는 의미 는 없습니다.
심지어 잔삭 은 Leftover(나머지 가공 : 다 가공 완료했지만 남아 있는 부분 가공)으로 표현되네요.
실제 Mid Cut로 검색하시면 그냥 헤어(머리카락) 중간 컷으로 나옵니다.
뭐 어찌 되었던 우리 들 이 알고 있는 중삭의 의미는 황삭 후 정삭을 들어가기 전에 정삭 하기 용이하게 (정삭에 적절한 가공 여유 남기기) 가능한 일정하게 정삭 할 여유 을 남기게 하는 가공을 의미합니다.
(상세하게는 여러 가지 상황 이 있습니다.)
우선 모의 가공을 통 하여 원하고 자 하는 중삭 과정을 먼저 보겠습니다.
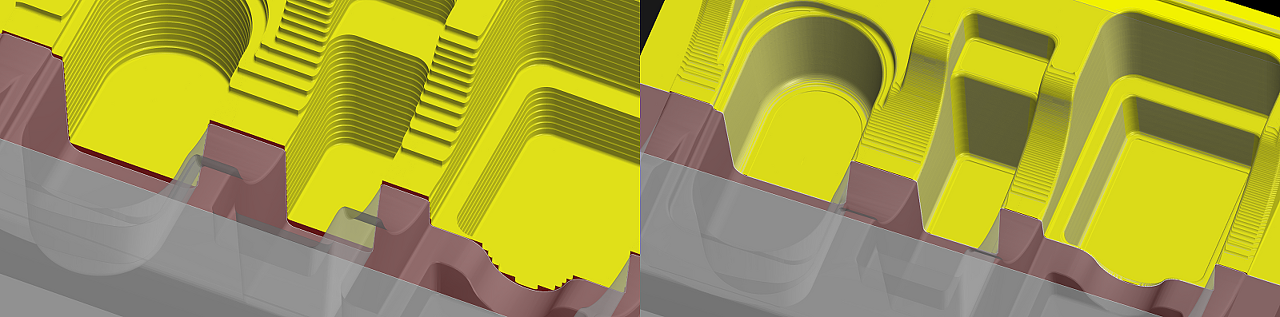
왼쪽이 황삭 가공 과정이고 오른쪽 이 중삭 가공 과정 모의 가공 결과입니다. 위 와 같이 황삭 가공으로 빠르고 많이 불필요 한 부분을 최대한 많이 깎아 내어 다음 정삭 시 해당 공구 가 부담 없이 해당 공차 을 유지하며 가공하는 과정입니다.
우선 저는 안쪽 포켓 부분을 가공 하고 외부 테두리 부분 을 가공하는 방법을 진행하겠습니다.
먼저 가공 방법 은 곡면 등고선 가공과 2D 포켓 가공을 겸하여 작업하겠습니다.
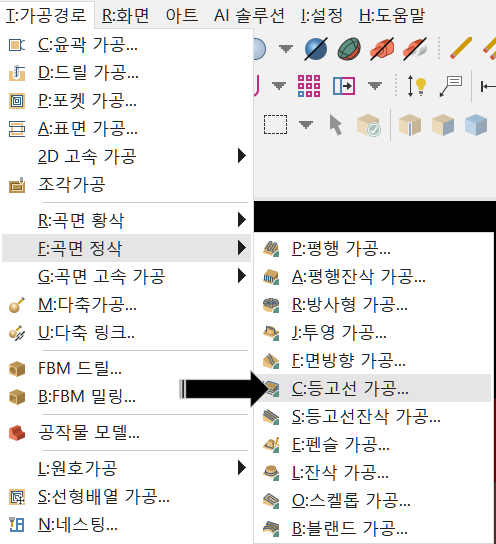
우선 등고선 가공으로 중삭 툴패스 을 생성해 보겠습니다.
가공 방식을 선택 후 해당 모델링 (곡면)을 선택하라고 메시지 가 출력됩니다.
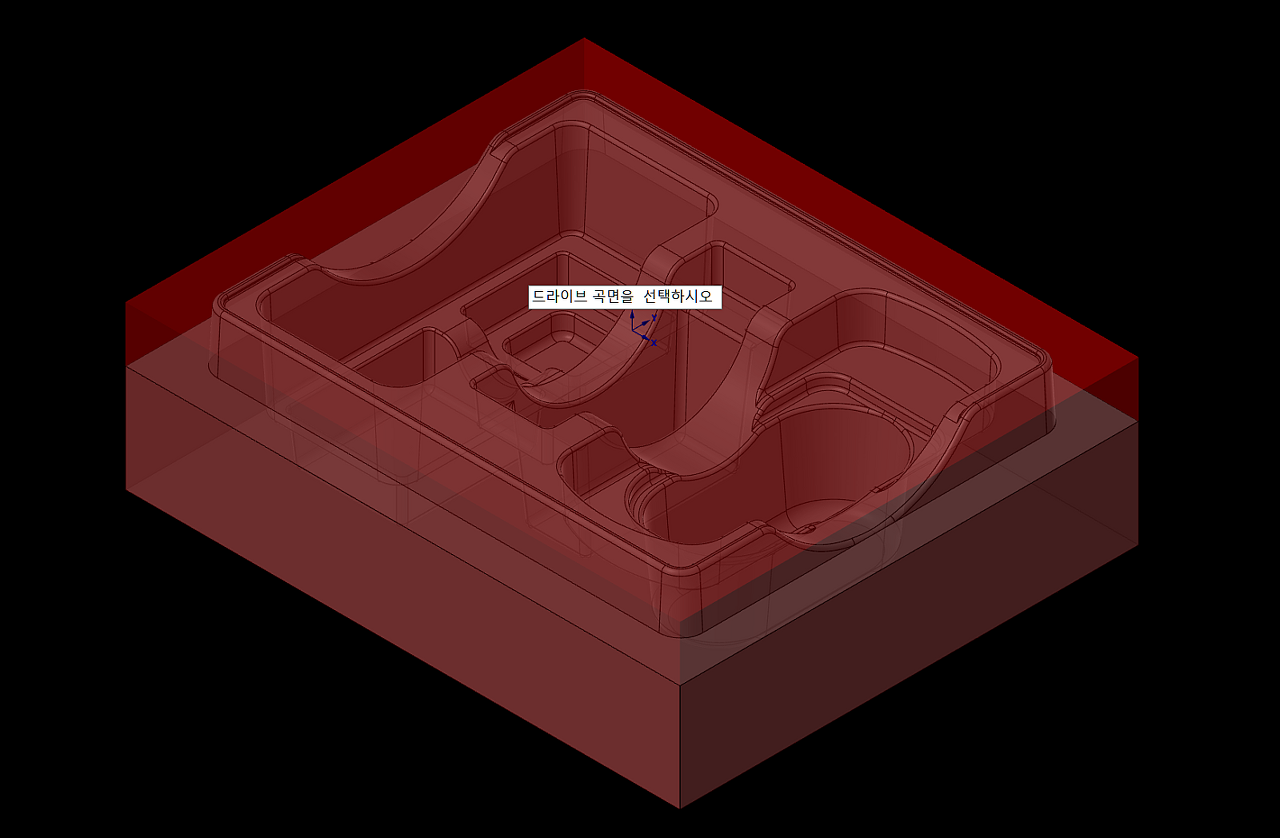
먼저 전체 모델링 (솔리드)을 선택합니다.
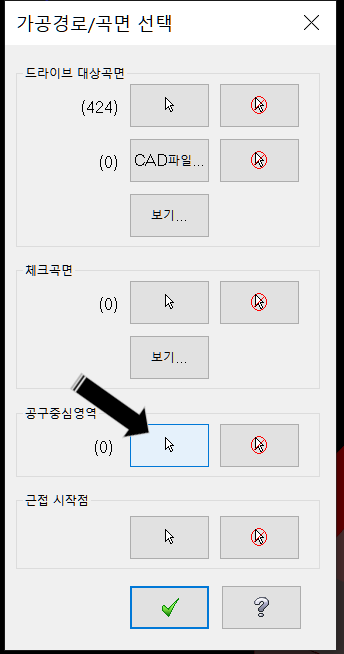
곡면 선택 후 공구 중심 영역을 선택하여 체인 선택 방법을 솔리드 체인으로 변경 후 선택 체인을 루프로 하여 테두리 외곽부 을 선택합니다.
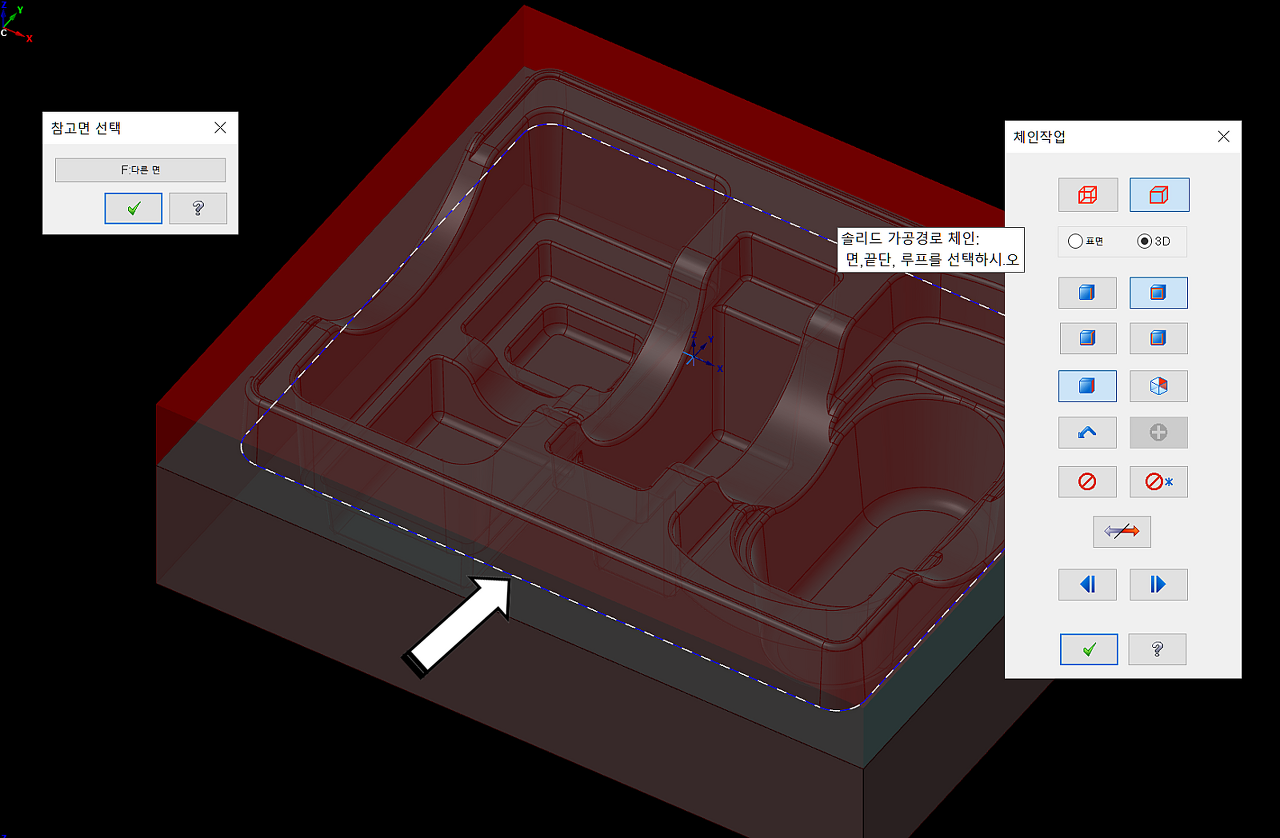
이후 절삭 파라미터에서 곡면 파라미터 설정을 다음과 같이 합니다.
설정 내용
이송 높이 는 증분 값으로 하여 불필요한 점프 을 줄입니다. (안전 높이 절댓값으로 필수 지정)(중요!!)
공구 중심 영역 은 공구 위치 내측 설정 (공구 가 공구 중심 영역 외측으로 생성될 필요 가 없으므로)
다만 양쪽 라운드 부분 뚷린 부분 때문에 공구 위치 을 내측으로 하면서 외측으로 6.0mm 넘어가도록 설정합니다.
황삭 가공 시 적용되는 것 과 동일합니다.
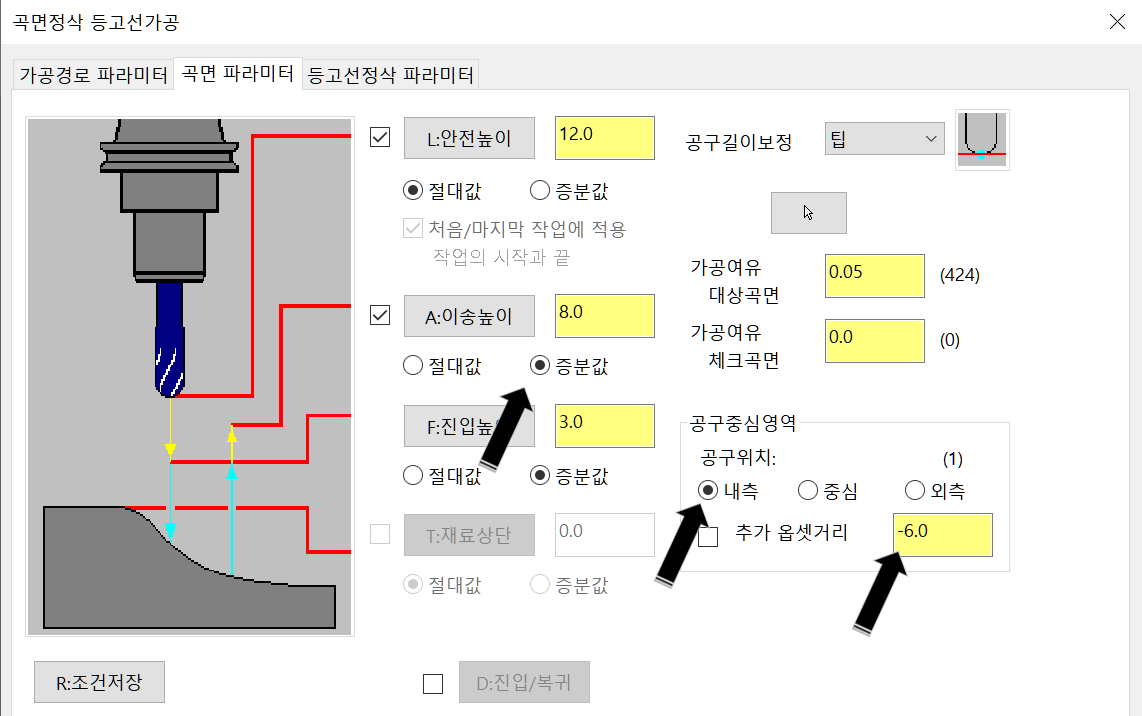
등고선 정삭 파라미터 설정
최대 Z절삭 간격 은 0.5mm로 설정하고 깊이 제한 설정을 걸어 줍니다.
(나머지 사항 은 대충대충....)
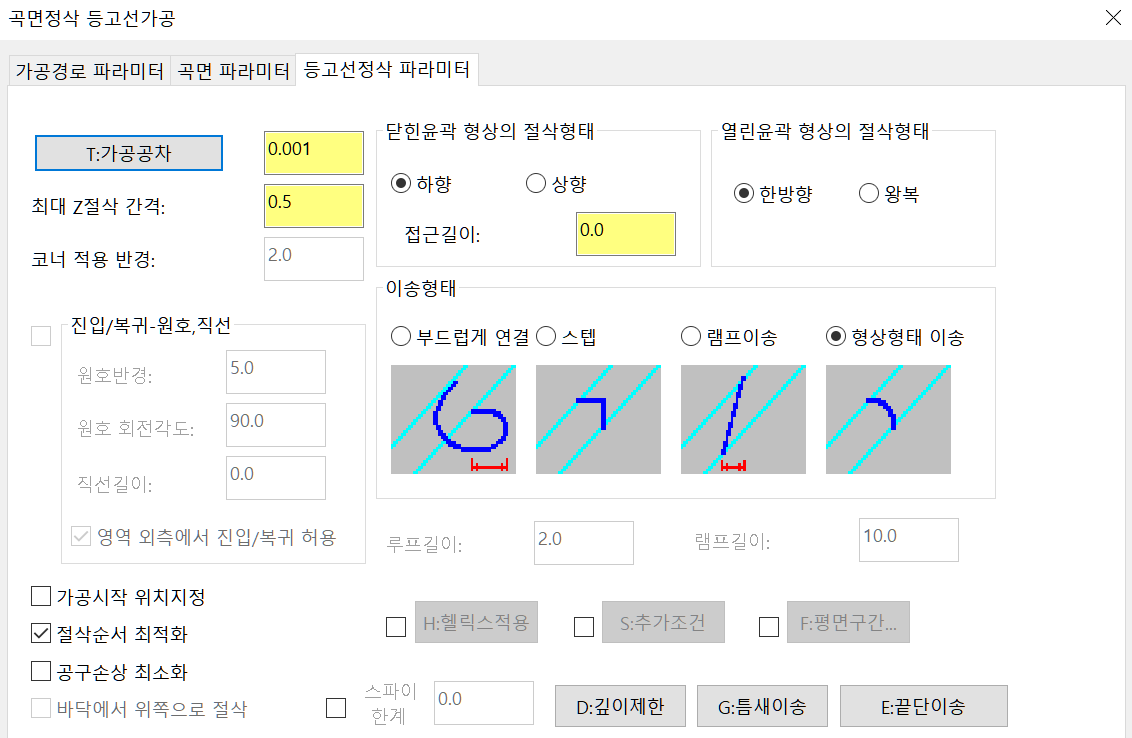
가공 깊이 제한 은 아랴 와 같이 최대 가공 깊이 는 -77.0으로 설정하였습니다.
* 실제 가공 시 최소 깊이 는 0.0으로 하지 마시고 한 단계 가공 깊이 간격만큼 설정하세요.
0.0으로 설정하시면 소재 상단 0.0에서 한번 포켓 가공하고 실제 가공으로 들어갑니다.
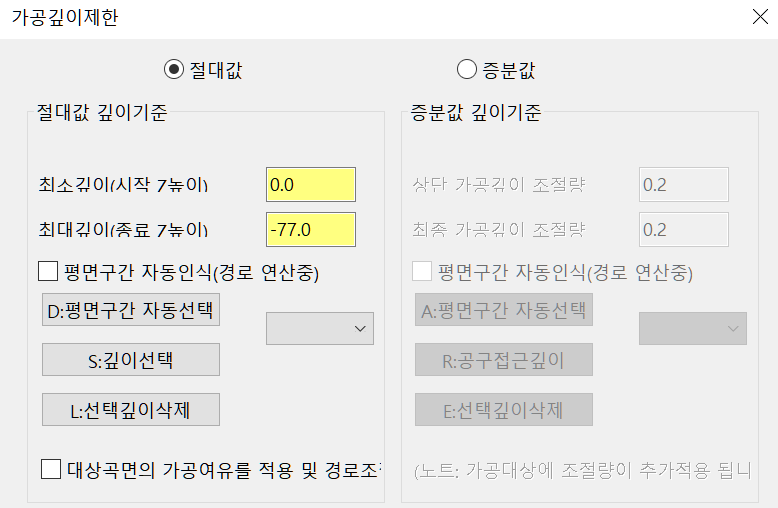
위 설정 특이 사항 이 앞에서 설명한 평면 구간 자동 인식 & 대상 곡면의 가공 여유 을 적용 이 체크 해제되어 있다는 것을 상기해 주세요.
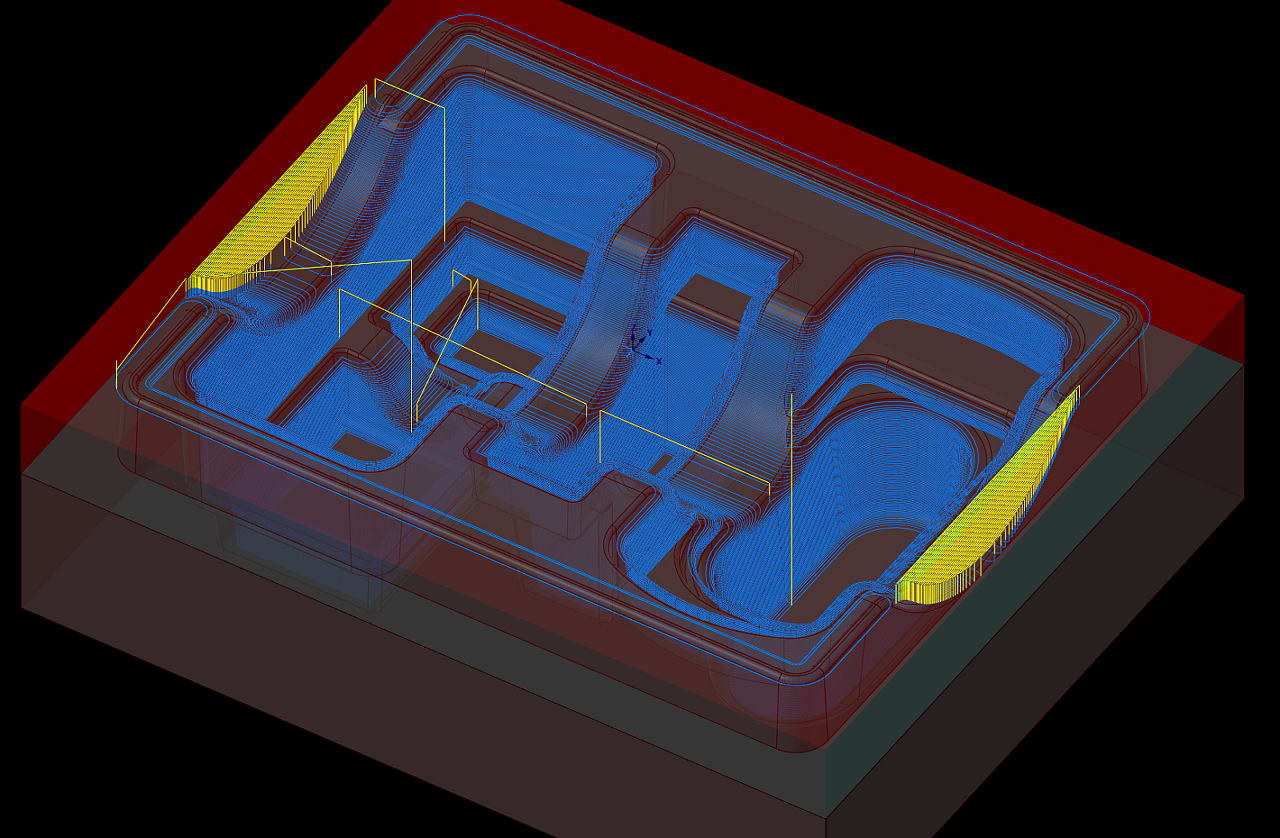
일단 툴패스 을 출력해 보자 평면 부분의 가공 툴패스 가 출력되지 않습니다. (정상입니다.)
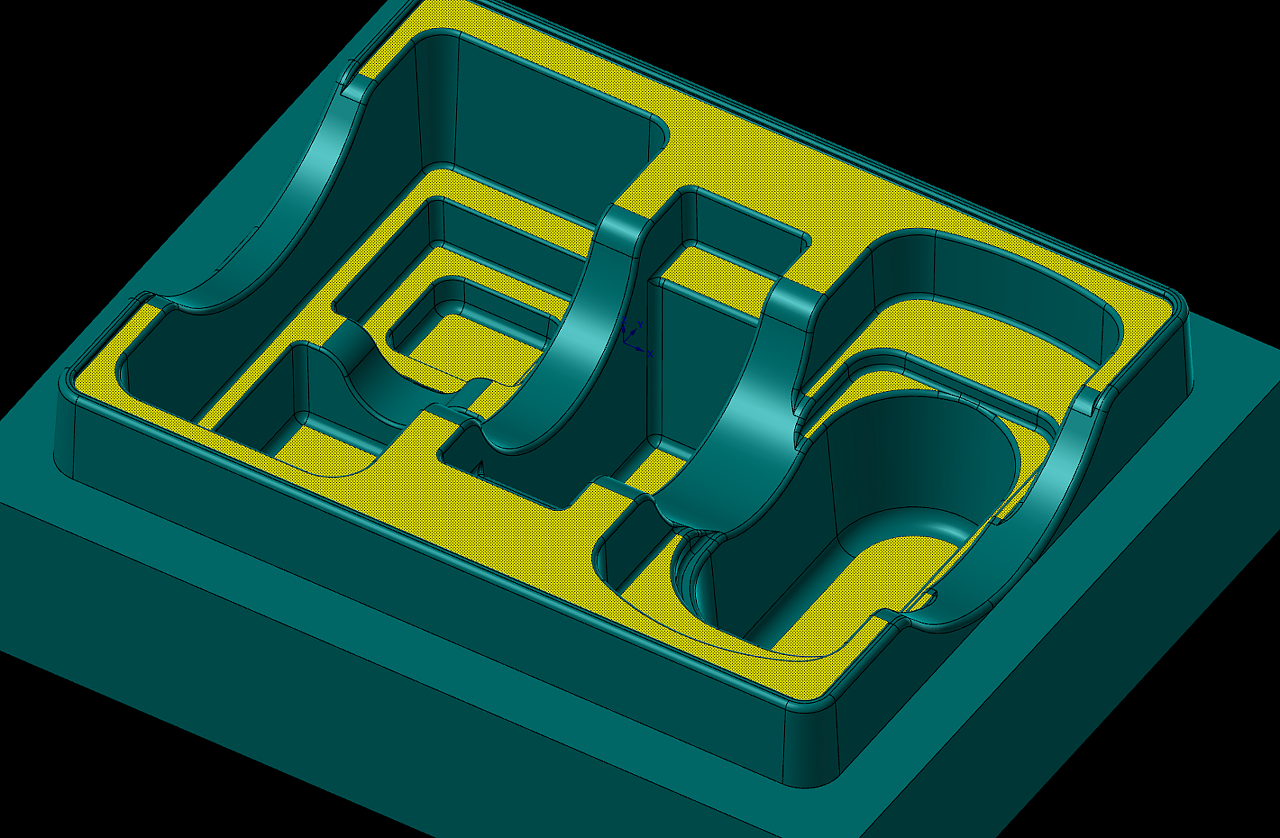
즉 위 모델링의 평면 부분 도 미절삭(황삭) 부분 이 있는데 이 부분 평면 바닥 부분 이 툴패스 가 출력되지 않습니다.
이상태에서 모의 가공을 해보면 다음과 같습니다.
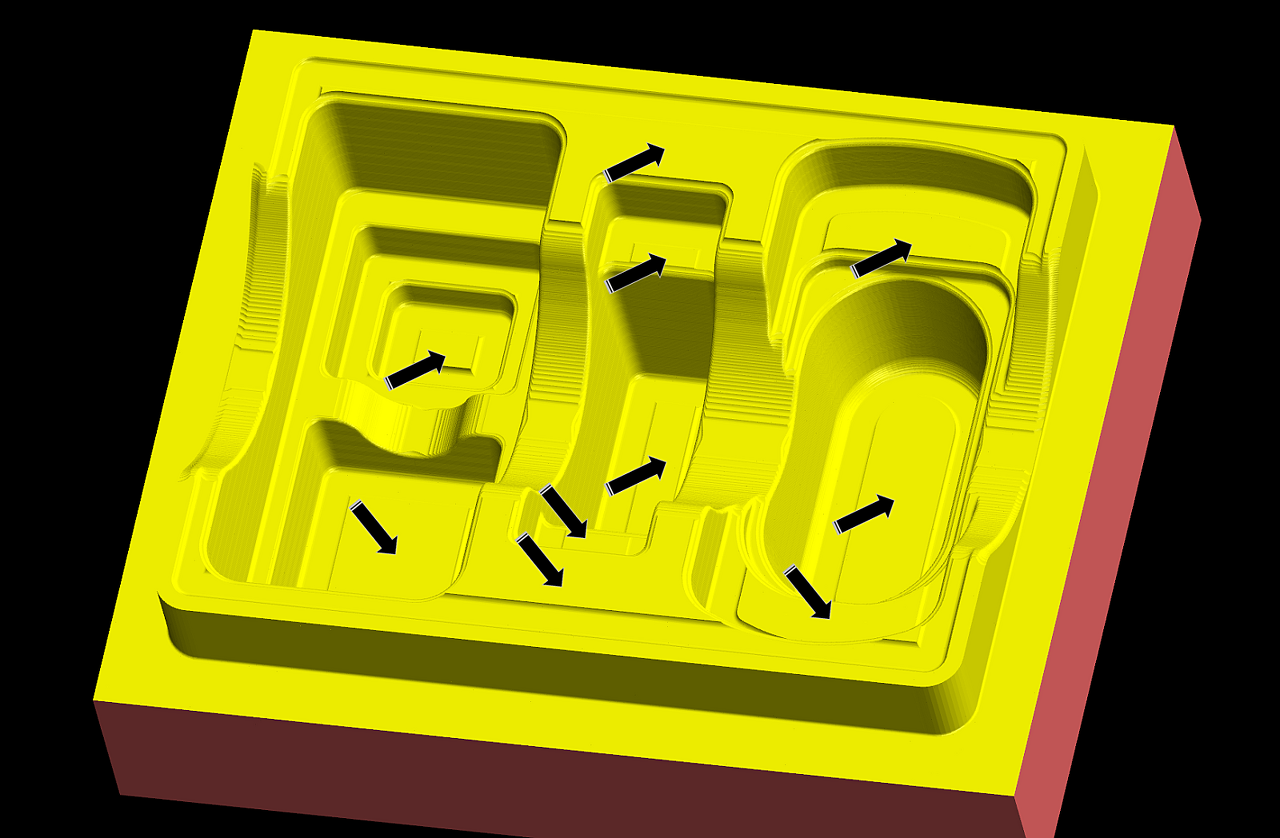
위 와 같이 주로 바닥면 부분에 미절삭 된 부분 이 많이 크게 남습니다.
그러면 중삭의 의미 (정삭 이 가능하게 부하 없는 가공 여유만큼 가공)가 없어집니다.
그러면 위에 설명한 것과 같이 가공 깊이 제한에서 평면 구간 자동 인식이나 대상 곡면 가공여유을 적용 등 의 옵션을 적용하면 안 되나요? (실제로 등고선 가공 은 별도의 평면 구간 설정 값에 따라갑니다.)
그래서 위 사항을 체크해 보고 다시 등고선 툴패스 을 생성해 보았습니다.
(중요한 것 은 평면 구간 설정 체크입니다.)
오랜 연산 시간 뒤 툴패스는 출력되지 않고 에러 메시지만 출력됩니다.
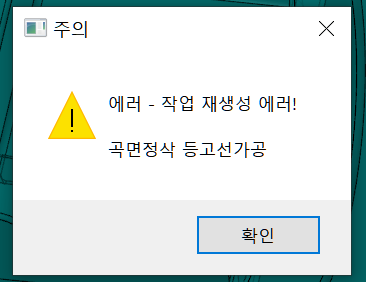
이후 여러 가지 샘플을 돌려 보자
처음 설명한 것처럼 포켓 이 하나의 평면 바닥을 가진 경우 적용 되나 다수 의 평면 바닥 을 가진 경우 에는 한 군데 의 평면만 적용되거나 역시 에러 가 출력되는 등 제대로 원하는 툴패스 가 출력되지 않습니다.
(다만 등고선 가공 후 등고선 잔삭 등 툴패스 을 출력하면 해당 평면 바닥 부 툴패스가 출력되나 불필요한 부분 도 같이 출력되거나 또한 문제없다 해도 툴패스 연산 시간 이 너무 길어 실무에 적응하기 어렵습니다.)
그래서 여기서는 일단 한 번에 중삭 툴패스 을 출력하는 것 을 포기하고 별도의 평면 바닥 툴패스 을 생성하기로 합니다.
(굳이 이렇게 불편하게 (작업자가...) 하는 이유는 이쪽이 연산 시간 단축이나 포켓 툴패스 (가공 깊이 간격 이 있는)을 내야 하기에 선택한 것입니다.)
우선 해당 모델링에서 가공되어야 할 평면 바닥 부분을 포켓 가공하여야 하므로 커브 기능으로 포켓 체인 (바닥 외곽선)을 생성해 보겠습니다.
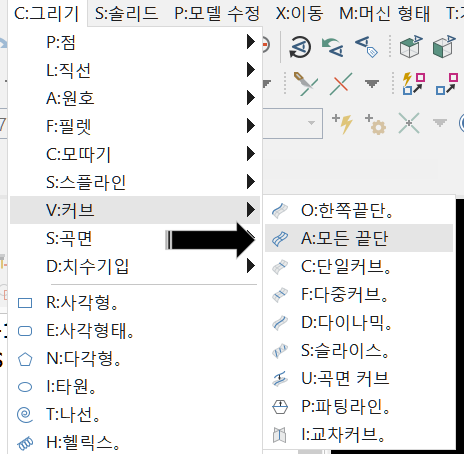
그리기 - 커브 - 모든 끝단을 선택하여 해당 평면 부 면을 선택합니다.
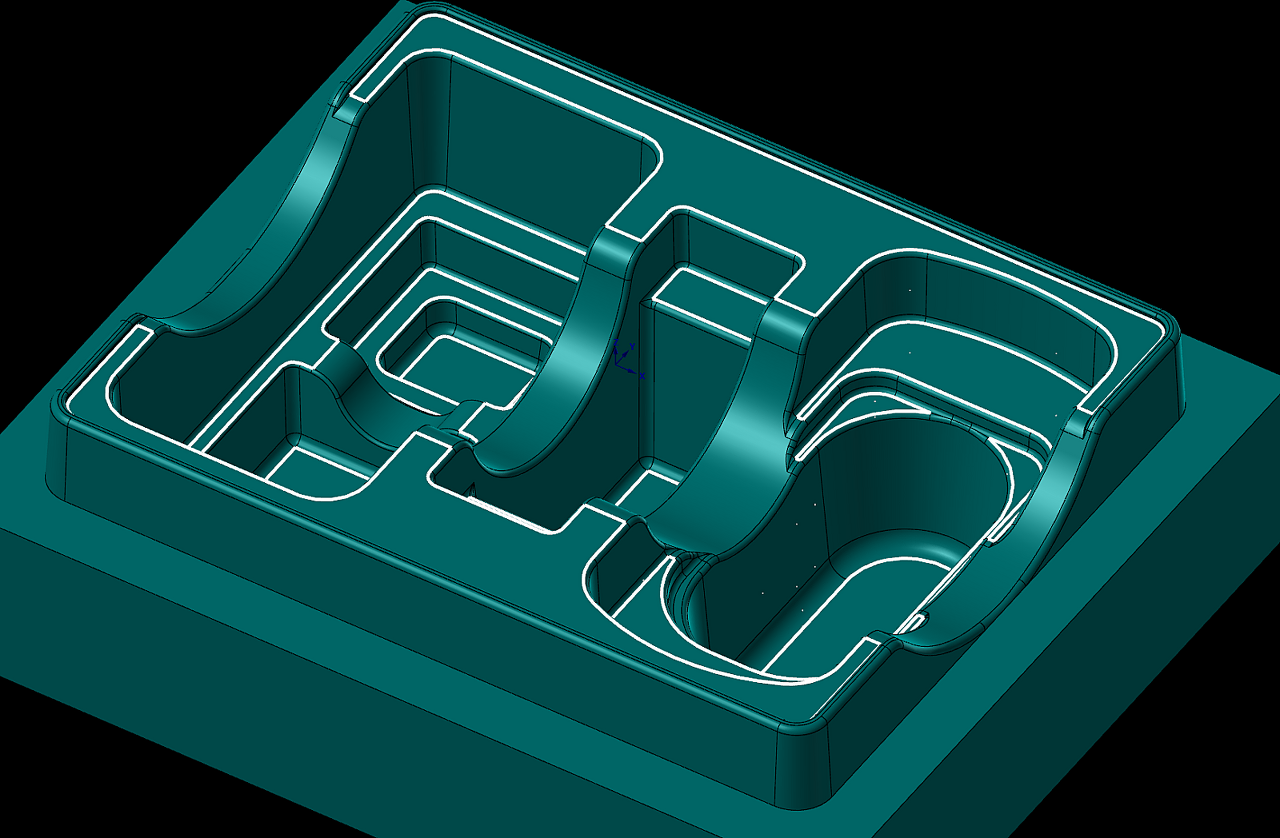
그러면 해당 평면의 외곽선 이 생성됩니다. (따로 레벨을 설정하여 생성하세요 구분 가능하게..)
그리고 2D 포켓 가공 기능으로 저 선 들을 체인 잡아 포켓을 생성합니다.
여기서 주의 사항 이 저 생성된 외곽선을 전부 체인 잡으시고 포켓 가공의 절삭 깊이 파라미터 을 다음과 같이 설정하셔야 합니다.
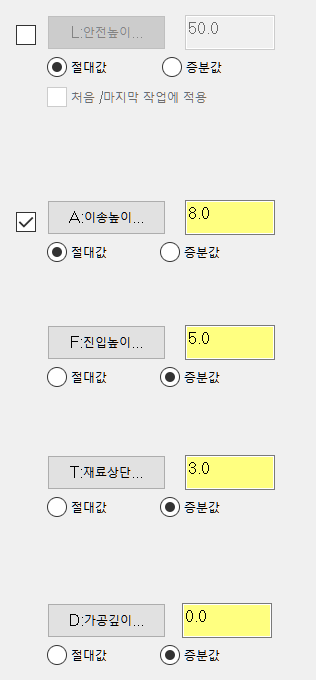
위 와 같이 (포켓 체인 이 각자 가공된 높이에 위치한 경우 다수의 체인) 높이 파라미터 을 설정하면 각 체인 놓인 위치 (깊이)에 따라 가공 깊이 가 설정되며 (즉 체인 이 있는 높이 값에 증분 값 "0.0"을 적용하면 바로 그 체인 높이 각 가공 깊이 0.0 이 됩니다.) 아까 황삭 가공 시 바닥 부에 남은 미절삭 부분 이 대부분 3.0mm 정도 남을 것 을 확인하였으니 그 높이만큼 재료 상단 높이 을 적용하며 이는 가공 깊이 간격 (1.5)을 적용하여 포켓 툴패스 가 1.5 간격으로 2개 생성됩니다.
(물론 정삭을 하여야 하므로 절삭 파라미터에서 가공 여유 0.05를 주어여 합니다.)..... 헉헉..
그래서 툴패스 을 출력해보았습니다.
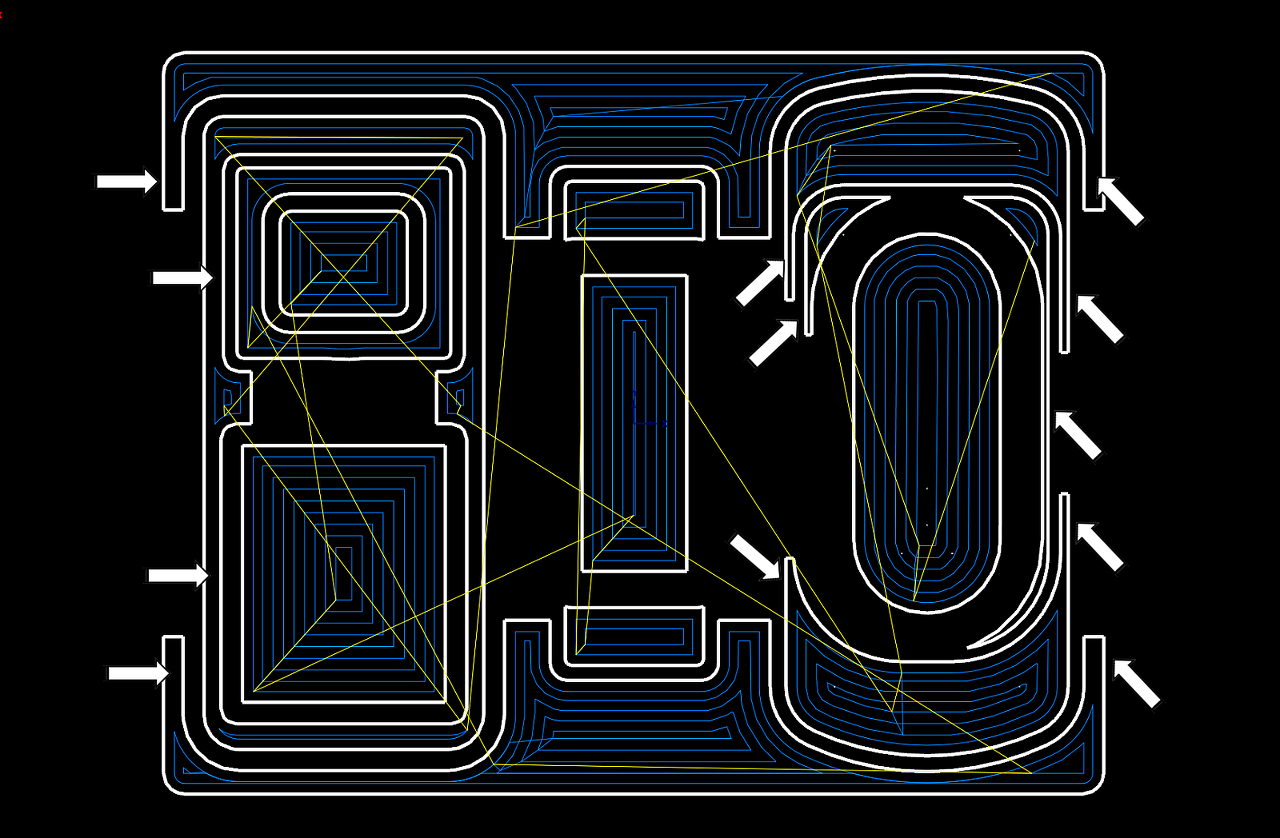
그런데 저기 포켓 부분 얇은 부분까지 툴패스 가 생성되지 않습니다. (당연한 것 인가...)
그러므로 스트레치 기능으로 해당 부분을 늘려주어 공구 가 진입할 수 있도록 수정합니다.
(이 툴패스 체인 는 다시 정삭 시 사용하니 작업 낭비는 아닙니다.)
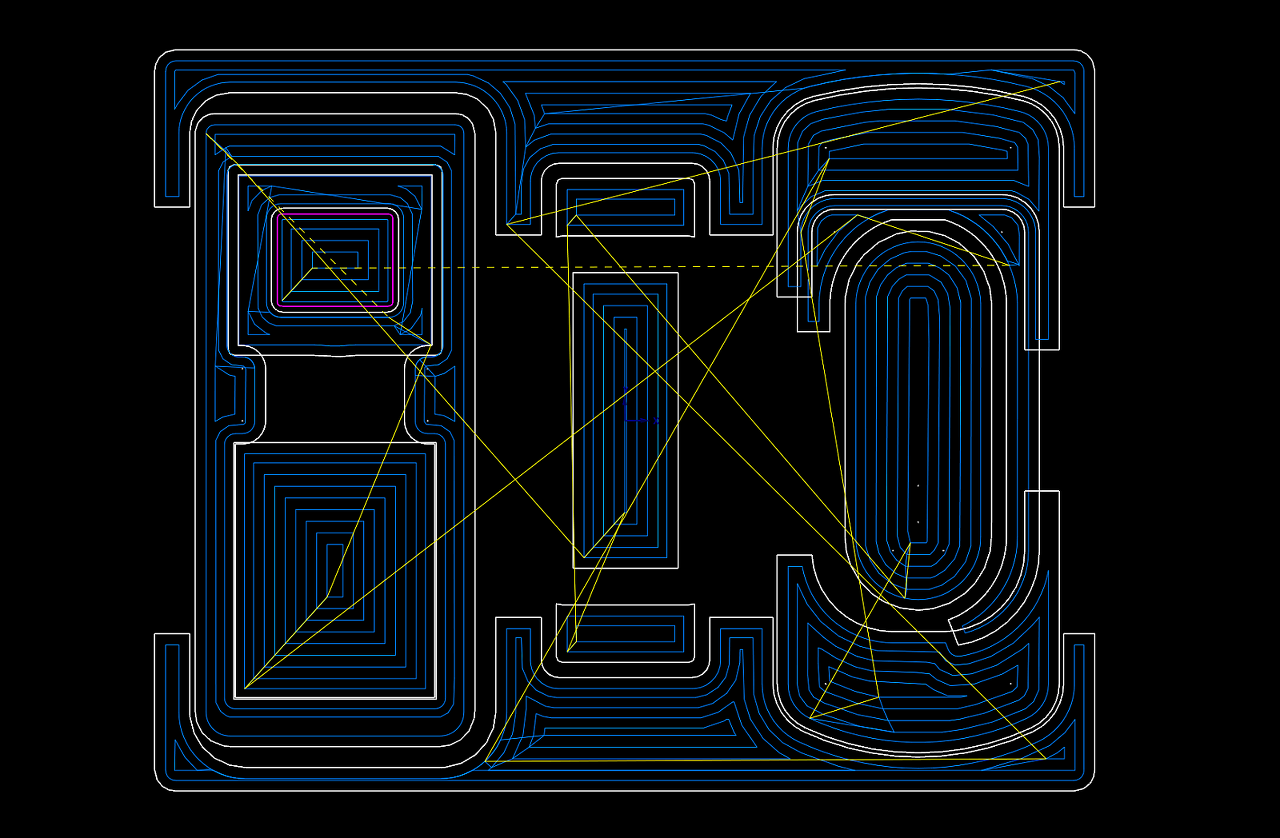
수정하여 다음과 같이 공구 가 진입 가능하게 합니다.
그리고 이 툴패스는 포켓 기능으로 가공 깊이 간격 조절로 2번 단계별 가공하게 하였습니다.
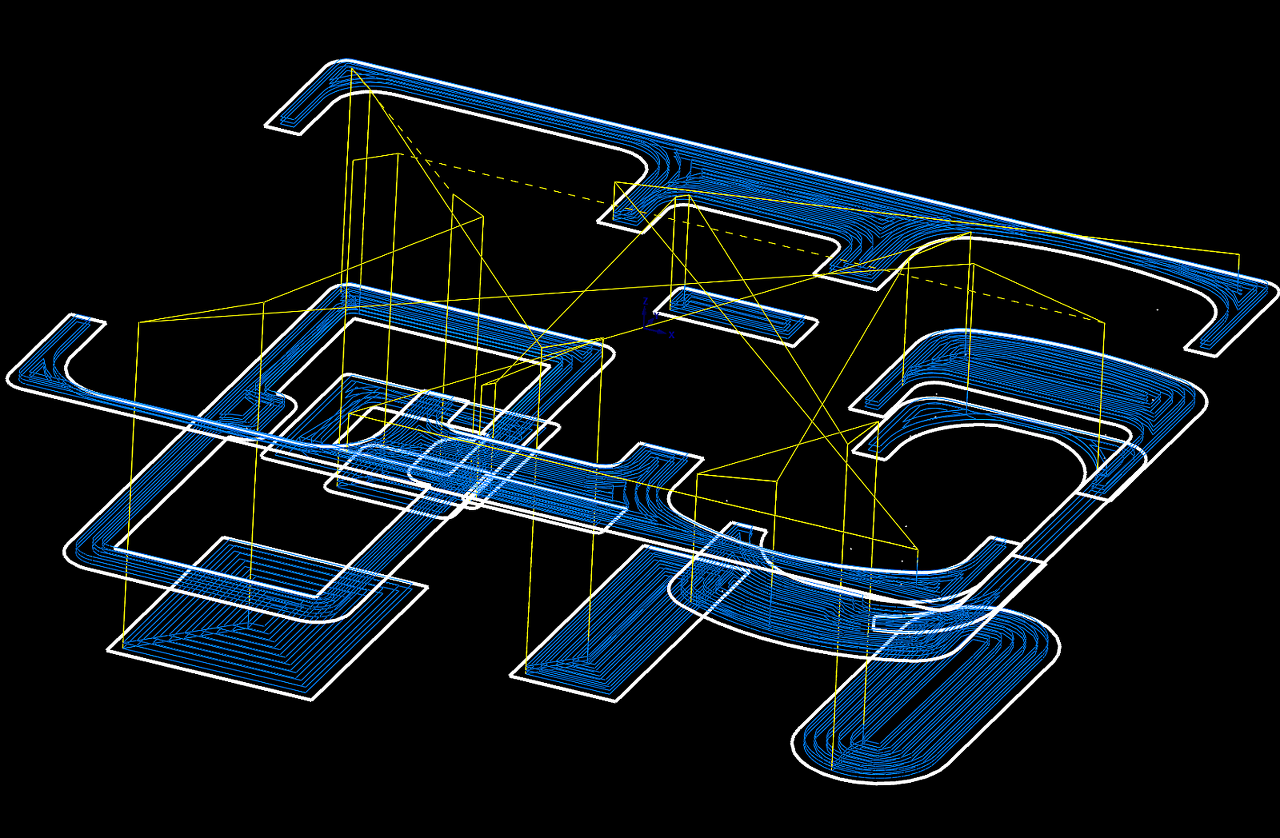
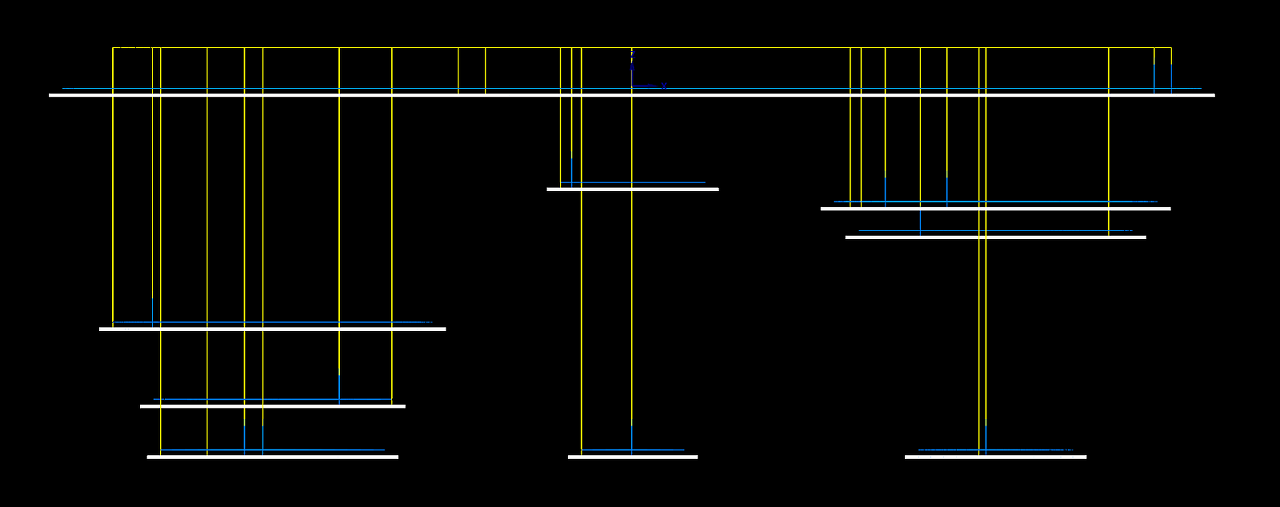
만일 이러한 작업 이 불편하시거나 왜 작업자 가 힘들게 만드냐 하시는 분 은 그냥 해당 평면 면 만 선택하고 나머지 면들 은 체크 곡면으로 지정하여 스켈 룹 가공으로 하셔도 크게 문제는 없습니다. (다만 연산 시간 이......)
한번 곡면 스켈룹 가공 으로 툴패스 을 생성해 보았습니다.
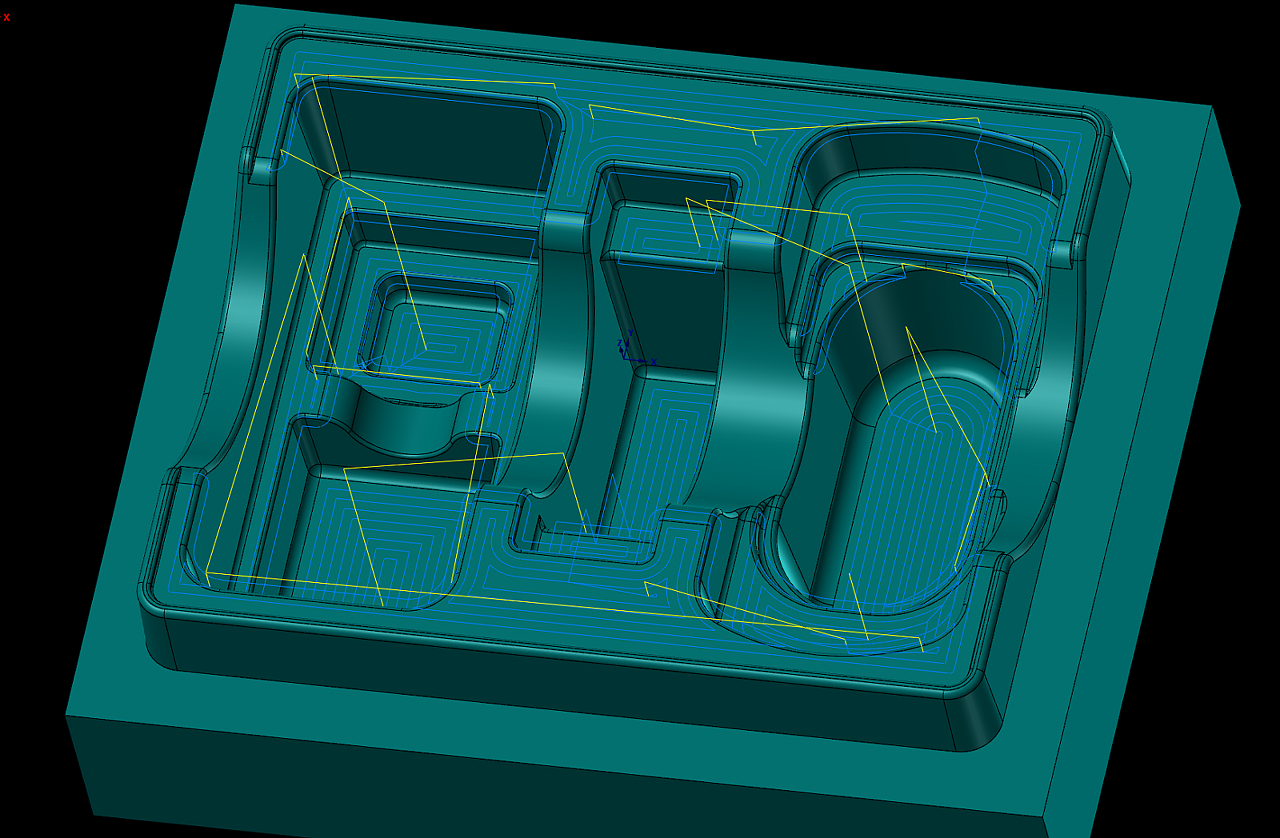
뭐 큰 문제는 없습니다.
다만 포켓 가공 (가공 깊이 간격) 이 적용되지 않으므로 별도로 툴패스 생성 (여기서는 1.5mm 간격으로 두 개) 따로 만들어 주셔야 합니다.
가능하다면 황삭 시 절삭 파라미터 을 잘 조절하여 중삭 시 한번 에 가공할 정도 가공 여유 을 만들면 선택해 볼 툴패스입니다.
어디까지 나 이것이 정석이다 가 아니고 작업자에 따라 선택하셔야 합니다.
그럼 이제 중삭까지 모의 가공을 해보겠습니다.
외측 중삭 이 있는데 이것은 역시 같은 방법으로 외측 경사면 만 가공 선택하고 나머지 면 들 은 체크 곡면 처리하고 공구 중심 영역 은 적용하지 않고 등고선 가공했으며 외측 바닥만 별도 엔드밀로 윤곽 가공하였습니다.
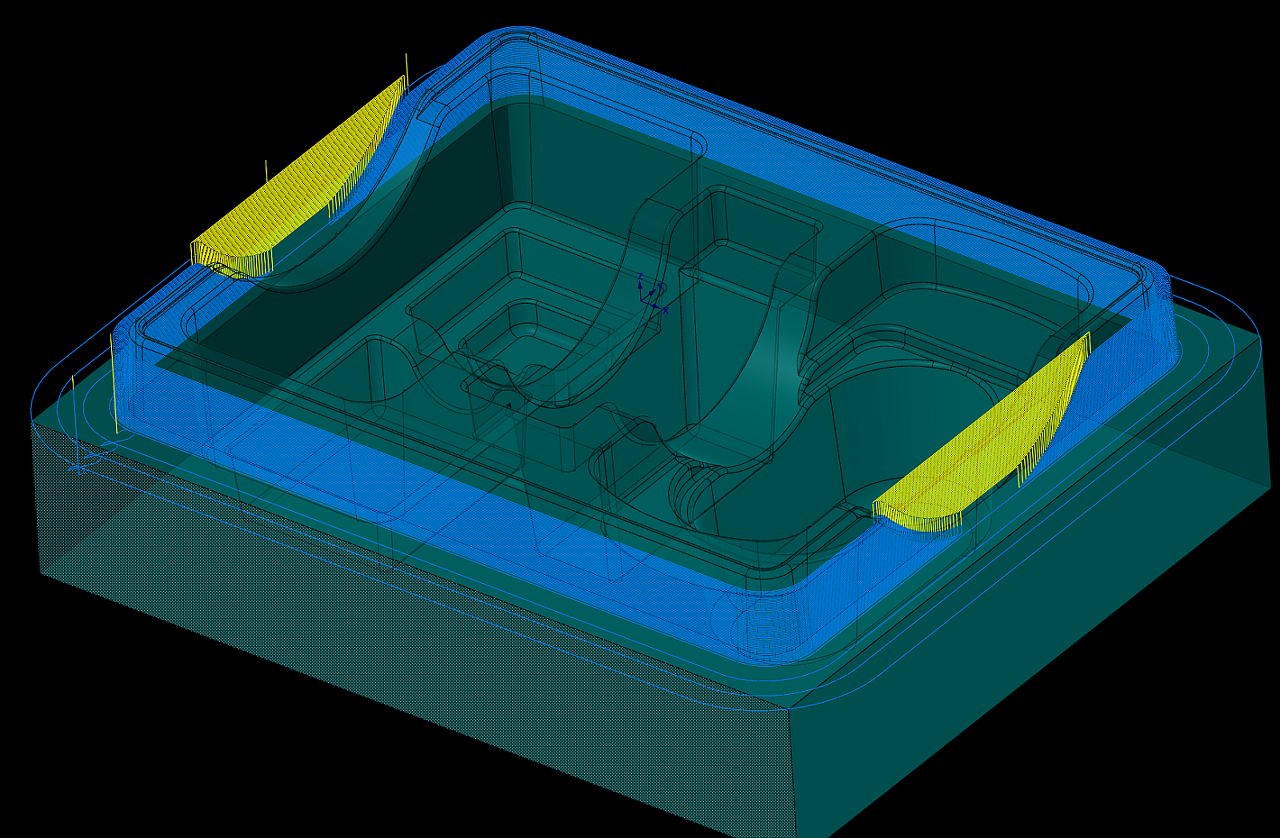
이제 모의 가공해 봅니다.
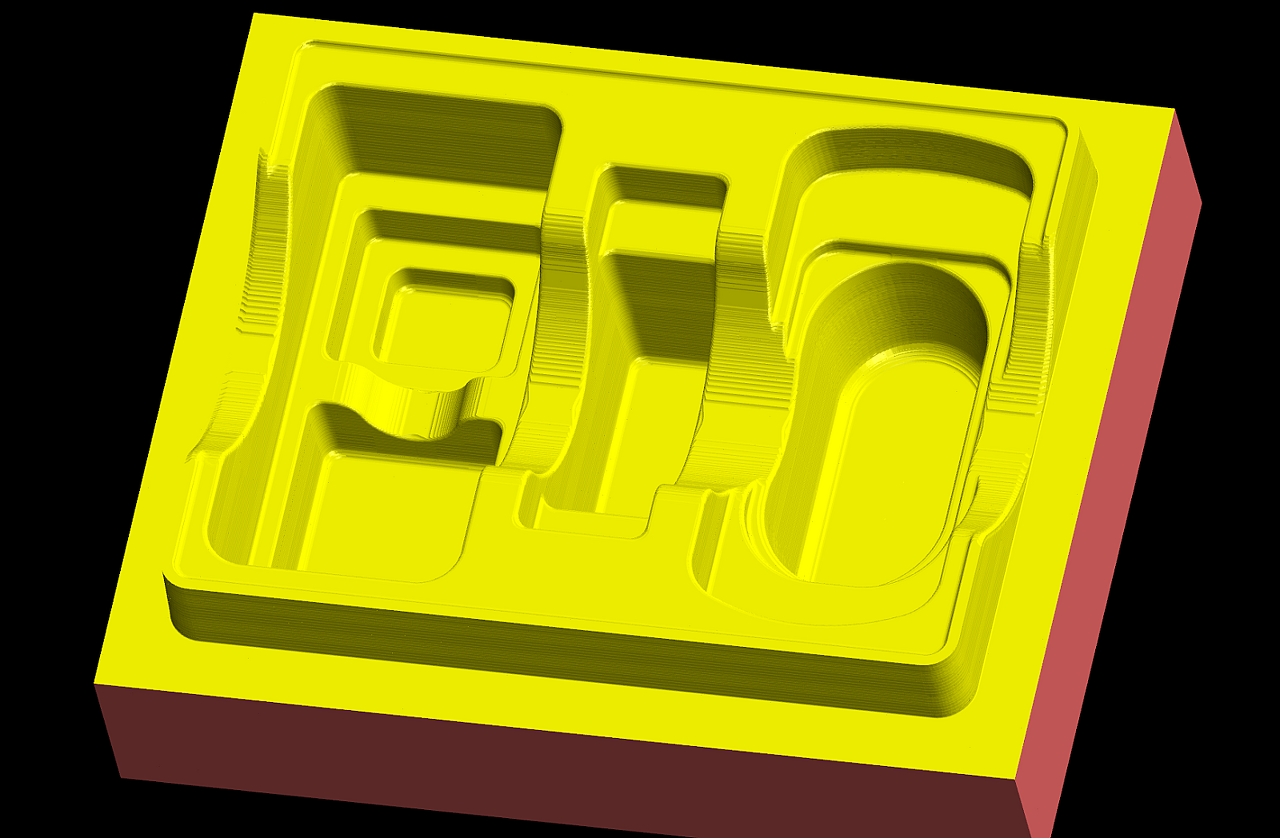
음 정삭 은 다음으로 넘기 겠습니다. ㅠㅠ
'마스터캠 관련 한 여러 이야기' 카테고리의 다른 글
바이스 스톱퍼 가공과정 설명기 (재료설정 교육자료용) (0) | 2022.05.22 |
---|---|
3D 가공 과정 에 대한 짧은 글 입니다. (금형 형태 가공) -4 (2) | 2022.05.21 |
3D 가공 과정 에 대한 짧은 글 입니다. (금형 형태 가공) -2 (0) | 2022.05.21 |
3D 가공 과정 에 대한 짧은 글 입니다. (금형 형태 가공) -1 (0) | 2022.05.21 |
마스터캠 와이어프레임 가공 (쿤스 가공) 에 대하여 알아보겠습니다.-3 (0) | 2022.05.21 |